
Новик_Технология серной кислоты
.pdfЛекция 6 КАТАЛИТИЧЕСКОЕ ОКИСЛЕНИЕ
SO2 Â SO3
Процесс окисления SO2 в SO3 описывается реакцией
SO2 + 1/ 2O2 ↔ SO3, H < 0
Эта реакция гомогенная, обратимая, экзотермическая. Q = 10 142 – 9,26T; T, K (t = 400–700°С).
На равновесие влияют Т, Р, С.
Влияние давления. Поскольку реакция протекает с уменьшением объема, то процесс необходимо проводить при повышенном давлении. Однако процесс окисления в настоящее время осуществляют под атмосферным давлением по следующим причинам:
1)при проведении процесса под повышенным давлением значительно усложняется аппаратурное оформление процесса;
2)на контактирование подается газ, содержащий 7,6–8,0% SO2, около 11% О2 и около 78% N2. Если повысить давление, то 4/5 энергии будет тратиться на сжатие балластного газа N2, а это экономически невыгодно. Применение повышенного давления становится оправданным лишь в том случае, если на стадии обжига и на стадии окисления
SO2 применять кислород или воздух, обогащенный кислородом. Однако это дорого.
Влияние температуры. Для определения зависимости Х* от Kр реакции необходимо установить их взаимосвязь.
|
* |
|
P |
|
|
|
P* |
|
|
||
X |
= |
|
|
SO2 |
|
; |
K р = |
SO3 |
|||
|
|
|
|
|
|
|
. |
||||
|
PSO |
|
+ PO |
|
|
||||||
|
3 |
2 |
P* 1/ 2 |
P |
|||||||
|
|
|
|
|
|
|
O 2 |
SO 2 |
Если возьмем 1 моль смеси, обозначим 2/3а – мольную долю SO2 в исходной смеси, b – мольную долю а в исходной смеси, тогда можно определить равновесные / – / давления:
P* |
= P |
а х* |
|
; |
P |
= P |
a − а х* |
; |
|
1− 1/ 2а х* |
1− 1/ 2а х* |
||||||||
SO3 |
общ |
|
SO2 |
общ |
|
||||
|
|
P* |
= P |
b − 1/ 2а х* ; |
|
|
|||
|
|
O2 |
|
общ |
1− 1/ 2а х* |
|
|
|
31
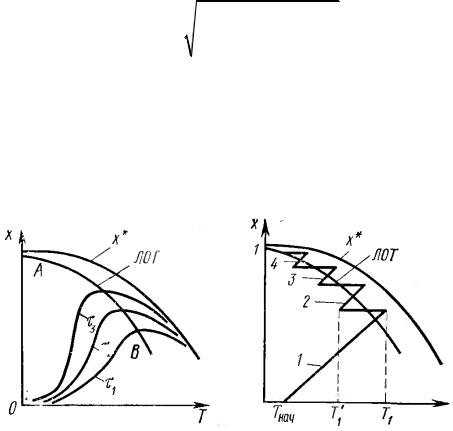
|
PSO* |
|
|
|
|
Pобщ |
|
|
а х* |
|
|
|
|
|
|
K р = |
3 |
= |
|
|
1 − 1 / 2а х* |
|
|
|
|
; |
|||||
PO*1/2 |
2 PSO2 |
|
|
b − 1 / 2а х* 1/2 |
a − а х* |
|
|||||||||
|
|
|
|
|
|
||||||||||
|
|
|
|
|
|
Pобщ |
|
|
* |
Pобщ |
|
|
|
|
|
|
|
|
|
1 − 1 / 2а х |
1 − 1 / 2 |
а х |
* |
|
|
||||||
|
|
|
|
|
|
|
|
|
|
|
|
x* = |
|
|
K p |
|
|
. |
|
K p + |
|
1−1/ 2a x* |
|
||||
|
|
|
|
||||
|
Р |
|
(b |
−1/ 2a x*) |
|
|
|
|
|
общ |
|
|
|
|
Константу равновесия можно рассчитать по эмпирическому урав-
нению (t = 390–650°С):
lg K р0 = |
4907,5 |
− 7,1552 Па−0,5. |
|
T |
|
Зависимость степени превращения от температуры (рис. 8).
|
|
|
|
|
|
|
|
|
|
|
|
|
|
|
|
|
|
|
|
|
|
|
|
|
|
|
|
|
|
|
|
|
|
|
|
|
|
||
|
|
|
|
|
|
|
|
|
|
|
|
|
|
|
|
|
|
|
x |
|
|
|
|
|
|
|
|
||||||||||||
|
|
|
|
|
|
|
|
|
|
|
|
|
|
|
|
|
|
|
|
|
|
|
|
|
|
|
|
|
|
|
|
|
|
|
|
|
|||
|
x |
|
|
|
|
|
|
|
|
|
|
|
|
|
|
|
|
|
|
|
|
|
|
|
|
|
|||||||||||||
|
|
|
|
|
|
|
|
|
x* |
|
|
|
|
|
|
|
|
|
|
|
|
|
|
|
|
|
|
|
|
|
|
x* |
|
|
|
|
|||
|
|
|
|
|
|
|
|
|
|
|
|
|
|
|
|
|
|
|
|
|
|
|
|
|
|||||||||||||||
|
|
|
|
|
|
|
|
|
|
|
|
|
|
1 |
|
|
|
|
|
|
|
|
|
|
|
|
|
|
|
|
|
|
|
||||||
|
|
|
|
|
|
|
|
|
|
|
|
|
|
|
|
|
|
|
|
|
|
|
|
|
|
|
|
|
|
|
|
|
|
|
|
|
|
||
|
|
|
|
|
|
|
|
|
|
|
|
|
|
|
|
|
|
|
|
|
|
|
|
|
|
|
|
|
|
|
|
|
|
|
ЛОТ |
||||
|
|
|
|
|
|
|
|
|
|
|
|
|
ЛОТ |
|
|
|
|
|
|
|
|
|
|
|
|
|
|
|
|
|
|
|
|
||||||
|
|
|
|
|
|
|
|
|
|
|
|
|
|
|
|
|
|
|
|
|
|
|
|
|
|
|
|
|
|
|
|
||||||||
|
|
|
|
|
|
|
|
|
|
|
|
|
|
|
|
|
|
|
4 |
|
|
|
|
|
|
|
|
|
|
|
|
||||||||
|
|
|
|
|
|
|
|
|
|
|
|
|
|
|
|
|
|
|
|
|
|
|
|
|
|
|
|
||||||||||||
|
|
|
|
A |
|
|
|
|
|
|
|
|
|
|
|
|
|
|
|
|
|
|
|
|
|
|
|
|
|
|
|
|
|||||||
|
|
|
|
|
|
|
|
|
|
|
|
|
|
|
|
|
|
|
|
|
|
|
|
|
|
|
|
|
|
|
|
|
|
|
|
||||
|
|
|
|
|
|
|
|
|
|
|
|
|
|
|
|
|
|
|
|
|
|
|
|
|
|
|
|
|
|
|
|
|
|
|
|
||||
|
|
|
|
|
|
|
|
|
|
|
|
|
|
|
|
|
|
|
|
|
|
|
|
|
3 |
|
|
|
|
|
|
|
|
|
|
|
|
||
|
|
|
|
|
|
|
|
|
|
|
|
|
|
|
|
|
|
|
|
|
|
|
|
|
|
|
|
|
|
|
|
|
|
|
|
|
|||
|
|
|
|
|
|
|
|
|
|
|
|
|
|
|
|
|
|
|
|
|
|
|
|
|
|
|
|
|
|
|
|
|
|||||||
|
|
|
|
|
|
|
|
|
|
|
|
|
|
|
|
|
|
|
|
|
|
|
|
|
|
|
|
|
|
|
|
|
|
||||||
|
|
|
|
|
|
|
|
|
|
|
|
|
|
|
|
|
2 |
|
|
|
|
|
|
|
|
||||||||||||||
|
|
|
|
|
|
|
|
|
|
|
|
|
|
|
|
|
|
|
|
|
|
|
|
|
|
|
|
|
|
|
|
|
|
|
|
|
|
|
|
|
|
|
|
|
|
τ3 |
|
|
|
|
|
|
|
|
|
|
|
|
|
|
|
|
|
|
|
|
|
|
|
|
|
|
|
|
|
|
|
||
|
|
|
|
|
|
|
|
|
|
|
|
|
|
|
|
|
|
|
|
|
|
|
|
|
|
|
|
|
|
|
|
|
|
|
|
|
|
|
|
|
|
|
|
|
|
|
τ2 |
|
|
|
|
|
|
|
|
|
|
|
|
|
|
|
|
|
|
|
|
|
|
|
|
|
|
|
|
|
|
||
|
|
|
|
|
|
|
|
|
|
|
B |
|
|
|
|
|
|
|
|
|
|
|
|
|
|
|
|
|
|
|
|
|
|
|
|
|
|
||
|
|
|
|
|
|
|
|
|
|
|
|
|
|
|
|
|
|
|
|
|
|
1 |
|
|
|
|
|
|
|
|
|
||||||||
|
|
|
|
|
|
|
|
|
|
|
|
|
|
|
|
|
|
|
|
|
|
|
|
|
|
|
|
||||||||||||
|
|
|
|
|
|
|
|
|
|
|
|
|
|
|
|
|
|
|
|
|
|
|
|
|
|||||||||||||||
|
|
|
|
|
|
|
|
|
|
|
|
|
|
|
|
|
|
|
|
|
|
|
|
|
|
|
|
|
|
|
|
|
|
||||||
|
|
|
|
|
|
|
|
τ1 |
|
|
|
|
|
|
|
|
|
|
|
|
|
|
|
|
|
|
|
|
|
|
|
||||||||
|
|
|
|
|
|
|
|
|
|
|
|
|
|
|
|
|
|
|
|
|
|
|
|
|
|
|
|
|
|
|
|
|
|
|
|
|
|
|
|
0 |
|
|
|
|
|
|
|
|
|
|
|
|
|
|
|
|
|
|
|
|
|
|
|
|
|
|
|
|
|
|
|
|
|
|
|
|
|
||
|
|
|
|
|
|
|
|
|
|
|
|
|
|
Tнач |
|||||||||||||||||||||||||
|
|
|
|
|
|
|
|
|
|
|
|
|
|
|
|
|
|
|
|
|
|
|
|
|
|
|
T'1 |
|
|
T1 |
|||||||||
|
|
|
|
|
|
|
T |
||||||||||||||||||||||||||||||||
|
|
|
|
|
|
|
|
|
|
|
|
|
|
|
|
|
|
|
|
|
|
|
|
|
Рис. 8. Зависимость степени превращения от температуры
Для достижения высокой степени превращения процесс окисления необходимо проводить при низкой температуре, однако при этом следует продлять время контактирования.
Влияние концентрации SO2. Для увеличения х, т. е. смещения равновесия вправо, необходимо увеличивать концентрацию исходных реагентов или уменьшать концентрацию продуктов в реакции, т. е. производить отвод продуктов реакции из зоны реакции.
Концентрацию SO2 в реальных аппаратах уменьшают по следующим причинам. Процесс окисления в промышленности протекает в адиабатических условиях, т. е. без обмена тепла с окружающей средой. При этом чем выше концентрация, тем больше температура на
32
выходе из слоя катализатора, а при t > 650°С начинает спекаться катализатор, и это ведет к уменьшению его активности. Поэтому в промышленных условиях в фильтрующем слое катализатора процесс окисления ведут при концентрации SO2 7–9% об. В кипящем слое, где процесс может протекать в изотермических условиях, концентрация SO2 может достигать 20%.
Кинетика процесса окисления. Скорость окисления SO2 харак-
теризуется константой скорости
k = k0 e− E/RT .
Энергия активации реакции окисления SO2 в SO3 очень велика, поэтому без катализатора реакция гомогенного окисления практически не идет, даже при высоких температурах.
Вприсутствии катализатора энергия активации понижается, что ведет к увеличению скорости гетерогенной каталитической реакции.
Впоследнее время в качестве катализатора используются ванадийсодержащие контактные массы.
Внастоящее время скорость реакции окисления SO2 в SO3 на ванадиевом катализаторе рекомендуется вычислять по следующей эмпирической формуле:
|
dx |
|
P k |
|
|
|
|
|
|
x |
|
2 |
1− 1 / 2a x |
|
|
|
|
|
b − 1 / 2a x |
|
|
|
|
||||||||
σ = |
|
= |
|
|
|
|
1 |
− |
|
|
|
|
|
|
, |
dτ |
a |
1 |
− 1 / 2a x |
318,3 |
|
b − 1 / 2a x |
|||||||||
|
|
|
|
|
K0 (1− x) |
|
|
|
|||||||
|
|
|
|
|
|
|
|
|
|
|
|
|
|
|
|
где х – достигаемая степень превращения, у. е; τ – время контакта, с; Р – общее давление, Па; a, b – начальные концентрации SO2 и O2 в газовой смеси, у. е; k – константа скорости, Па/с; K0 – константа скорости, Па–0,5.
Для реакции окисления нет одной оптимальной температуры, это интервал температур. И для каждой х существует своя оптимальная температура. Поэтому для высокой интенсивности процесс необходимо начинать при высокой температуре, когда скорость велика, и заканчивать при низкой температуре. При этом достигается высокая степень превращения.
Катализаторы для окисления SO2. Самым активным катализа-
тором для этой реакции является Pt, но она отравляется в 5000 раз сильнее, чем ванадиевый катализатор. По отношению к этой реакции каталитическую активность проявляют ванадийсодержащие вещества.
В настоящее время для данной реакции в качестве катализаторов применяют ванадийсодержащие контактные массы (БАВ, СВД, ИК, ОС, ЛТИ), а также контактные массы фирмы «Монсанто» (ЦП-110, ЛП-120).
33
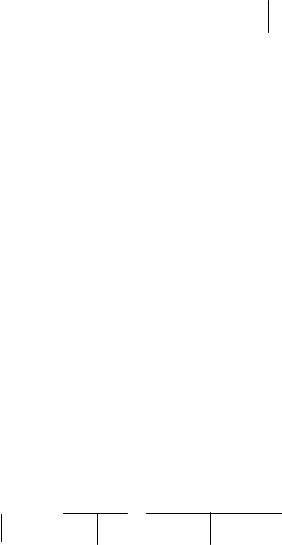
Рассмотрим катализаторы и способы их получения.
БАВ – барий-алюмо-ванадиевый. Это осажденный катализатор. Активный компонент V2O5, содержится 7–8%. Брутто-состав
V2O5 · 12SiO2 · 0,5Al2O3 · 2K2O · 3BaO · 2KCl.
V2O5 + K2SO4 + BaSO4 + Al(SO4)3 + SiO2 (кремнезем)
|
|
|
|
|
|
|
|
|
|
|
|
|
Кт |
активатор |
|
|
|
носитель |
|||||
Функциональная схема: |
|
|
|
|
|
|
|||||
1 |
2 |
2 |
1 |
|
|
|
|
||||
|
|
|
|
O2 → O2 → Кт←SO2 |
←SO2 |
|
|
||||
|
|
|
|
|
|
↓ 3 |
4 |
|
|
1 |
|
|
|
|
|
|
|
|
|
|
|
||
|
|
|
|
|
|
O Кт SO2 →SO3 |
→SO3 |
где 1 – диффузия; 2 – сорбция; 3 – образование комплекса; 4 – десорбция.
Этот катализатор после приготовления и прокалки требует насыщения SO2. Процесс насыщения осуществляется непосредственно в контактном аппарате. После загрузки катализатора в контактный аппарат подается газ с содержанием SO2 0,1% и постепенно в течение 7– 8 суток концентрация SO2 увеличивается до 7,0–7,5%. При насыщении в газовую фазу выделяется хлор, что приводит к загрязнению окружающей среды.
Температура зажигания катализатора 420°С.
СВД – сульфо-ванадиево-диатомовая контактная масса. Катализатор получают сухим способом. Содержание V2O5 7%.
Брутто-состав CВД: V2O5 · 2,7K2O · 0,6SO3 · 0,75CaO · 25SiO2. V2O5 (7%) + K2S2O7 + диатомит + гипс
Кт активатор носитель
Катализатор получают смешением всех активных компонентов. Для этого инфузорную землю (SiO2) смешивают с V2O5, гипсом и пиросульфатом калия. После смешения в полученную массу добавляют воду, пасту отфильтровывают и подают на формовку. Полученная контактная масса, в отличие от БАВ, не требует насыщения SO2. Температура зажигания СВД и БАВ 420–440°С.
Катализаторы ИК (ИК-4, ИК-6) – институт катализа. Их получают смешением гидратированного SiO2, V2O5. В этот катализатор вводят
34
соединения калия в виде пиросульфата калия. Его достоинство – низкая температура зажигания, равная 380°С.
Катализатор ТС – термостабильный. Его готовят по технологии, аналогичной получению СВД, но в процессе осаждения вводят переходные металлы, в частности цирконий, что приводит к увеличению термической стабильности. Температура спекания составляет 780°С.
Катализатор ТС и катализаторы с низкой температурой зажигания целесообразно применять на первом слое катализатора в качестве запалов.
Катализаторы ЛТИ. Этот катализатор применяется для контактных аппаратов с кипящим слоем катализатора. Его получают пропиткой шарикового силикагеля растворами солей ванадия с последующей сушкой и термообработкой.
Температура зажигания контактной массы зависит как от качества катализатора, так и от состава газовой смеси. Температура зажигания возрастает с уменьшением содержания кислорода в смеси.
В промышленных аппаратах активность ванадиевой контактной массы со временем снижается, поэтому катализатор полностью или частично заменяют каждые 3–5 лет.
Первый и последний слои катализатора в контактных аппаратах должны состоять из свежей контактной массы, при этом понижается температура зажигания первого слоя. Наличие же свежей контактной массы на последнем слое обеспечивает высокую общую степень превращения.
Контактные аппараты для окисления SO2. Требования к контактным аппаратам:
–в контактном аппарате должен обеспечиваться оптимальный технологический режим;
–степень превращения должна быть не ниже 89%;
–аппарат должен иметь низкое гидравлическое сопротивление;
–контактные аппараты должны работать в автотермичном режиме (т. е. тепло химической реакции используется для нагрева исходных реагентов до температуры зажигания катализатора, и подвод тепла извне не осуществляется);
–устойчивость в работе;
–простота конструкции и простота регулировки температурного режима;
–легкость загрузки и разгрузки катализатора;
–высокая тепловая инерция (аппарат должен долгое время сохранять тепло, т. е. должна быть хорошая теплоизоляция).
35
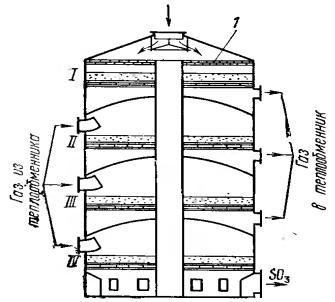
Аппараты одинарного контактирования бывают:
1)со встроенными промежуточными теплообменниками;
2)с выносными промежуточными теплообменниками;
3)с поддувом холодной реакционной газовой смеси и воздуха после нескольких слоев катализатора;
4)с кипящим слоем катализатора;
5)аппараты ОТС (отвод тепла серой).
1. Контактный аппарат с промежуточным охлаждением газов в теплообменниках (рис. 9).
SO2
|
|
|
Газ в теплообменник |
|||
Газ из теплообменника |
|
|||||
|
|
|
|
|
|
|
|
|
|
|
|
|
|
|
|
|
|
|
|
|
|
|
|
|
|
|
|
|
|
SO3 |
Рис. 9. Контактный аппарат с промежуточным охлаждением газов в теплообменниках
В полочном контактном аппарате с промежуточным теплообменником степень превращения достигает 98%. Дальнейшее увеличение количества слоев нецелесообразно, так как увеличение степени превращения будет незначительное, но резко увеличится гидравлическое сопротивление, расход катализатора и размеры аппарата. Эти контактные аппараты бывают как с внутренними (встроенными), так и с внешними (выносными) теплообменниками.
Недостатки аппарата со встроенным теплообменником:
–громоздкость;
–высокое гидравлическое сопротивление.
Для уменьшения гидравлического сопротивления аппарата охлаждение осуществляется в выносных теплообменниках. Для этого между слоями поставлены глухие перегородки.
36
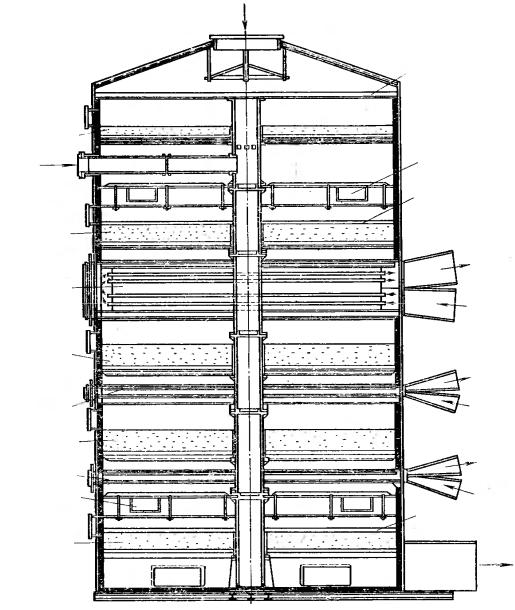
2. Пятислойный контактный аппарат с поддувом холодной реакционной смеси после 1-го слоя катализатора (рис. 10).
Охлаждение газа осуществляется не в теплообменнике, а путем подвода в газовую смесь на выходе из первого слоя холодной газовой смеси.
I
Холодный
SO2
II
1
III
2
IV
3
4
V
SO2
5
4
5
SO2
SO2
SO2
SO2
SO2
5 SO2
SO3
Рис. 10. Пятислойный контактный аппарат с поддувом холодной реакционной смеси после 1-го слоя катализатора
Достоинства: простота конструкции.
Недостатки: уменьшается х за счет ввода холодной реакционной смеси.
37
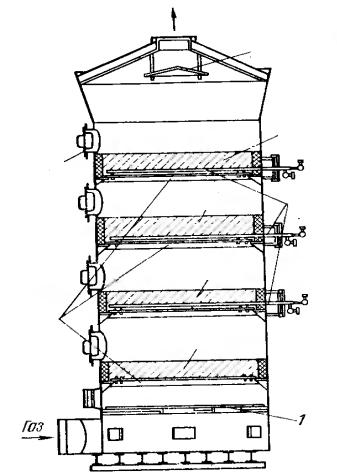
3. Контактный аппарат с кипящим слоем катализатора (рис. 11).
Ваппаратах с плотным (фильтрующим) слоем катализатора нельзя произвести замену катализатора без его полной остановки, в этих аппаратах применяются крупные зерна катализатора (диаметром 5–6 мм), и поэтому процесс лимитируется внутренней диффузией.
Впроцессе работы катализатор слеживается и спекается. Всех этих недостатков лишены аппараты с кипящим слоем катализатора. В ап-
паратах с фильтрующим слоем катализатора концентрация SO2 менее 8,5–9,0%. В аппараты с кипящим слоем можно подавать газ с концен-
трацией SO2 менее 20%. Эти аппараты работают в изотермическом режиме, поэтому перегрев катализатора не происходит.
Газ
5
I
4
II 3
III
2
IV
|
|
1 |
|
Газ |
|||
|
Рис. 11. Контактный аппарат
скипящим слоем катализатора
Ваппараты с кипящим слоем можно подавать газ с температурой
Т0, которая на 50–80°С ниже температуры зажигания катализатора. При прохождении кипящего слоя за счет высокого коэффициента теп-
38
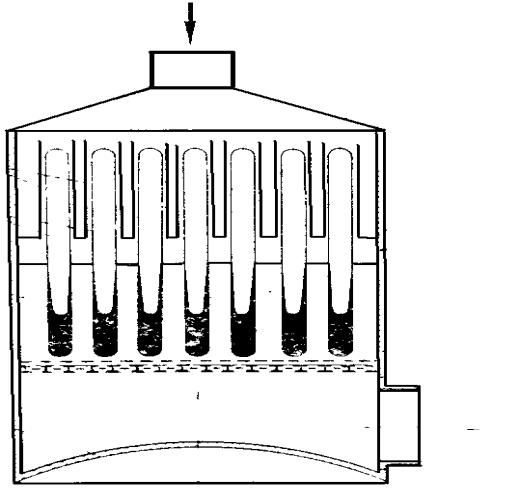
лопередачи температура газа резко повышается от температуры Т0 до Т1, и процесс окисления протекает в изотермических условиях, при этом не происходит перегрева катализатора.
Недостатки аппарата:
–высокая истираемость катализатора;
–срок службы катализатора не превышает 2–3 мес.;
–повышенный расход энергии;
–за счет высокой истираемости катализатора газ загрязняется каталитической пылью.
4. Аппарат ОТС (рис. 12).
Рис. 12. Аппарат ОТС (отвод тепла серой)
В аппаратах ОТС в катализатор помещаются запаянные трубки, внутри которых находится сера. Обжиговый газ поступает в контактный аппарат и проходит в кольцевой зазор между запаянными трубками и гильзами, при этом газ в кольцевом зазоре нагревается за
39
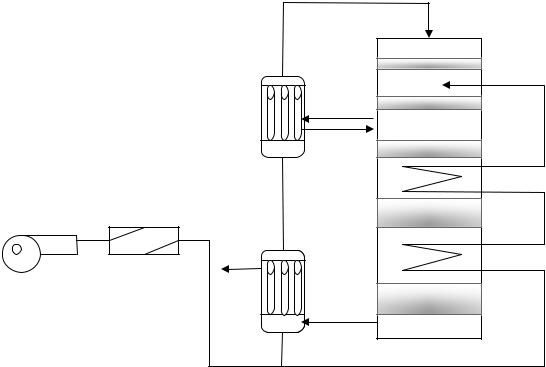
счет набора тепла от парообразной серы, сера при этом конденсируется и по трубам стекает вниз (Ткип серы 445°С), отвод тепла из катализатора происходит за счет кипения и испарения расплавленной серы. Расход металла в этих аппаратах меньше, чем в аппаратах с фильтрующим слоем.
Технологическая схема контактного отделения представлена на рис. 13.
Рис. 13. Технологическая схема контактного отделения
Газ из сушильного отделения турбогазодувкой подается в контактное отделение. Все аппараты до контактного отделения работают под разряжением, после – под давлением.
После газодувки газ проходит фильтр, где очищается от капель масла и кислоты, и разделяется на два потока: 70% газа проходит теплообменник после V слоя и выносной теплообменник после II слоя, в котором нагревается до температуры 420–440оС, и поступает на I слой контактного аппарата, концентрация SO2 в газе составляет 7,5–8,0%. На I слой необходимо загружать катализатор с низкой температурой зажигания и высокой температурой спекания. Это позволяет увеличить концентрацию SO2 в обжиговом газе, что приводит к увеличению степени превращения и скорости процесса. Степень превращения после I слоя составляет 70%, температура газа 600°С. Чем выше концен-
40