
3894
.pdf
13
Примечание: значения коэффициентов: в числителе для задних, средних мостов и для мостов о одинарной главной передачей; в знаменателе с двойной главной передачей; для рулевых управлений в числителе без гидроусилителя, в знаменателе с гидроусилителем.
В зависимости от классов производственного участка дальнейшие расчеты будут отличатся.
|
|
Таблица 3 |
|
Классы производственных рабочих |
|
|
|
|
|
|
|
|
|
Единица измерения про- |
|
Класс |
Наименование участка |
изводственной программы |
|
|
|
|
|
1 |
Разборочный, сборочный, слесарно-механический, |
Изделие, шт. |
|
|
кузовной, испытательная станция, рамный. |
|
|
|
|
|
|
2 |
Моечно-очистительный, кузнечно-рессорный, тер- |
Масса обрабатываемых де- |
|
|
мический. |
талей, кг. |
|
3 |
Гальванический, окрасочный, полимерный. |
Площадь покрытия, м2 или |
|
|
|
дм2 |
|
4.2.2 Режим работы и годовой фонд времени Режимы работы предприятия определяются количеством рабочих дней в
году, количеством смен работы в сутки, длительностью смены и рабочей недели в часах. Годовой режим для авторемонтных заводов с учетом 5-ти дневной рабочей недели принят 250 рабочих дней. [12, 17, 21]
Суточные режим для АРП как правило, составляет 2 смены, но сменность отдельных подразделение может изменяться в. зависимости от условий производства и программы, а также исходя из экономической целесообразности полного использования технологического оборудования.
Сменность работе проектируемого цеха или участка устанавливается заданием или принимается дипломником с соответствующим обоснованием принимаемого решения.
Годовой фонд времени работающего (количество рабочих часов в году) определяется в зависимости от их специальности и характера выполняемой работ в соответствии с действующим законодательством.
Годовой фонд времена рабочего с учетом потерь времени на очередные отпуска, болезни и т.д. называется действительным или расчетным – Фдр, (табл. 4), без учета этих потерь – номинальным – Фнр.
Годовой фонд времени рабочего места определяется по формуле:
14
Фрм = Фнр ∙ Усм(3)
где Усм. – число смен работы.
Таблица 4
Действительные фонды времени рабочих для авторемонтных предприятий
|
Продолжи- |
Годовой фонд време- |
||
|
ни рабочего, час |
|||
Профессии рабочих |
тельность рабо- |
|||
|
|
|||
|
чей смены |
Фнр. |
Флр |
|
|
|
|
|
|
Маляры-пульверизаторщики |
7,2 |
1830 |
1610 |
|
|
|
|
|
|
Кузнецы, газоэлектросварщики, медники, испыта- |
8,2 |
2070 |
1820 |
|
тели ДВС |
|
|
|
|
|
|
|
|
|
Аккумуляторщики, карбюраторщики, слесари- |
8,2 |
2070 |
1840 |
|
авторемонтники, мойщики, шиномонтажники, вул- |
|
|
|
|
канизаторщики, гальваники, регулировщики |
|
|
|
|
|
|
|
|
|
Прочие |
8,2 |
2070 |
1860 |
4.2.3 Производственный процесс цеха (участка)
Производственный процесс составляется на основании технологических процессов разборки, сборки и ремонта деталей автомобилей и их узлов, разработанных проектно-технологическими организациями или принятых на действующих предприятиях. Поэтому производственный процесс является совокупностью всех технологических процессов, связанных с ремонтом автомобиля (разборки, контроля, восстановления, оснастки, окраски, транспортировки и т.п.) и составленным в определенной последовательности в соответствии с планом расположения технологического оборудования.
В проекте производственный процесс в сжатой форме представляется кратким его описанием. В том и другом случаях указываются способы доставки ремфонда или обрабатываемых деталей на участок, последовательность прохождения по рабочем местам, методы ремонта, применяемые материалы, способы окраски и хранения готовой продукции и другие операции, т.е. законченный цикл производства в заданном объеме. Здесь же необходимо подчеркнуть какие новые методы ремонта или оборудования применяются автором данного проекта.

15
4.2.4 Расчет годового объема работ, определение количества и состава работающих
Трудоемкость ремонта автомобилей как трудозатраты, необходимые для выполнения всех видов работ и операций, согласно технологическому процессу на его выполнение, является вторым основанием в исходных данных после производственной программы для проведения технологических расчетов при проектировании АРП. Трудозатраты, указанные в технологических картах, не учитывают масштабов и специфики проектируемого производства, измеряются в нормочасах и служат для расчетов норм времени при начислении заработной платы исполнителям. Суммарное выражение нормативной трудоемкости Тн можно привести к фактической трудоемкости Тф, измеряемой в чел-ч. через коэффициент переработки норм времени Кn, который принимается по отчетным данным действующего предприятия или планируется в пределах 1,35-1,50:
. |
(4) |
Во всех дальнейших расчетах фигурирует только фактическая трудоемкость, которая принимается по укрупненным нормам в зависимости от масштабов производства и структуры производственной программы. Ниже приводятся значения трудоемкости ремонта базовых моделей автомобилей и агрегатов, соответствующие определенной программе предприятия по данным Гипроавтотранса (табл. 5).
Таблица 5
Трудоемкость капитального ремонта базовых моделей ремонтируемых объектов при эталонных условиях
|
Эталонная годовая |
Трудоемкость ТЭ, |
|
Объект ремонта и специализация предприятия |
программа, тыс. кап. |
||
чел. ч |
|||
|
рем. |
||
|
|
||
|
|
|
|
Силовой агрегат ГАЗ-ЗВ09 |
10,0 |
35,0 |
|
|
|
|
|
Силовой агрегат МАЗ-500 |
10,0 |
65,0 |
|
|
|
|
|
Комплект прочих основных агрегатов грузовых |
10,0 |
17,5 |
|
автомобилей и автобусов с карбюраторными дви- |
|
|
|
гателями |
|
|
|
|
|
|
|
Полнокомплектный автомобиль ГАЭ-3309 |
2,0 |
175,0 |
|
|
|
|
|
Полнокомплектный автомобиль МАЗ-500 |
2,0 |
315,0 |
|
|
|
|
|
Автомобиль FA3-3309 на базе готовых силовых |
2,0 |
133,0 |
|
агрегатов |
|
|
|
|
|
|
16
Автомобиль МАЗ-500 на базе готовых силовых |
2,0 |
235,0 |
агрегатов |
|
|
|
|
|
Автобус ЛАЗ-695Нна базе готовых агрегатов |
1,0 |
380,0 |
|
|
|
Примечание 1 Для определения трудоемкости других марок автомобилей необходимо эталонное значение трудоемкости умножить на коэффициенты, учитывающие модель автомобиля – К1 (табл. 6). 2 При определении трудоемкости для предприятий, у которых данные отличаются от эталонной программы, значения трудоемкости необходимо, кроме того, умножить на коэффициент, учитывающий мощность предприятия – К2 (табл. 7).
При расчетах трудоемкости импортных автомобилей необходимо применять коэффициент сложности ремонта до значения Ксл=1,25 (по данным Гипроавтотранса).
Табличные значения трудоемкости, приведенные в «Нормативных характеристиках к проектированию авторемонтных предприятий» следует принимать только в процентном распределении по видам работ, т.к. эти данные не учитывают предприятия малой мощности.
|
|
|
|
|
|
Таблица 6 |
|
Коэффициенты, учитывающие модели автомобиля (агрегата) – К1 |
|
|
|||||
|
|
|
|
|
|
|
|
|
Заводы по |
Заводы по |
|
Заводы по |
|
|
|
|
ремонту си- |
ремонту |
Заводы по |
ремонту гру- |
Заводы по |
Заводы по ре- |
|
Марка авто- |
ловых агре- |
прочих ос- |
ремонту |
зовых авто- |
ремонту ав- |
монту агрегатов |
|
гатов грузо- |
новных аг- |
полноком- |
мобилей па |
легковых авто- |
|||
мобиля (аг- |
вых автомо- |
регатовгру- |
плектных |
базе готовых |
тобусов не |
мобилей (пол- |
|
базе готовых |
|||||||
регата) |
билей и ав- |
зовых авто- |
грузовых |
силовых аг- |
нокомплектный |
||
|
агрегатов |
||||||
|
тобусов |
мобилей и |
автомобилей |
регатов |
ремонт) |
||
|
|
||||||
|
|
автобусов |
|
|
|
|
|
|
|
|
|
|
|
|
|
ГА3-3309 |
1,0 |
1,0 |
1,0 |
1,0 |
|
|
|
ЗИЛ-5301 |
1,13 |
1,17 |
1,13 |
1,13 |
|
|
|
ЗИЛ-ММЗ- |
1,13 |
1,43 |
1,24 |
1,28 |
|
|
|
555 |
|
|
|
|
|
|
|
МАЗ-500 |
1/1,9 |
|
1/1,8 |
1/1,75 |
|
|
|
МАЗ-503 |
1/1,9 |
|
1,1/2,0 |
1,13/1,97 |
|
|
|
КрАЗ-64431 |
1,2/2,3 |
|
1,37/2,52 |
1,44/2,53 |
|
|
|
|
|
|
|
|
|
|
|
КрАЗ-6510 |
1,2/2,3 |
|
1,25/2,25 |
1,28/2,25 |
|
|
|
КамАЗ-5320 |
1,4 |
|
1,3/2,22 |
1,44/2,53 |
|
|
|
БелАЗ-75131 |
|
|
2,22/50 |
|
|
|
|
БелАЗ-7550 |
|
|
2,95 |
|
|
|
|
ЛA3-695I1 |
1,15 |
|
|
|
1,0 |
|
|
ЛИA3-5256 |
1,13 |
|
|
|
1,2 |
|
|
Москвпч- |
|
|
|
|
|
0,73 |
|
2141 |
|
|
|
|
|
|
|
ГАЗ-3110 |
|
|
|
|
|
1,0(1,0/1,5) |
|
ЯМ 3-236 |
1,0/1,9 |
|
|
|
|
|
|
|
|
|
|
|
|
|
|
ЯМЗ-231 |
1,2/2,3 |
|
|
|
|
|
|
|
|
17 |
|
|
|
|
|
|
|
|
|
|
Газ-2705 |
|
1,23 |
1,1 |
1,13 |
|
|
|
|
|
|
|
|
|
ЗМЗ-402 |
0,92/1,75 |
|
|
|
|
|
|
|
|
|
|
|
|
ЗМЗ-406 |
1,01/1,93 |
|
|
|
|
|
|
|
|
|
|
|
|
Д-240 |
0,98/1,75 |
|
|
|
|
|
|
|
|
|
|
|
|
Коэффициент К2 для других значений программ определяется методом интерполяции или путем построения графика зависимости величины этого ко-
эффициента от мощности предприятия. Таким образом, трудоемкость капи-
тального ремонта автомобиля или агрегата будет выражаться:
|
|
Та = Т6 ∙ К1 ∙ К2, |
|
|
(5) |
|||
|
|
|
|
|
|
|
Таблица 7 |
|
Коэффициенты, учитывающие мощность предприятия, К2 |
|
|
|
|
||||
|
|
|
|
|
|
|
|
|
|
Заводы по |
Заводы по |
Заводы по |
Заводы по |
Заводы по |
|
|
|
|
ремонту |
|
|
|
||||
Годовая про- |
цен- |
ремонту си- |
ремонту |
ремонту |
Заводы по |
|
Заводы по |
|
полно- |
|
|||||||
грамма в тыс |
трализован- |
ловых агре- |
прочие ос- |
полно- |
ремонту ав- |
|
ремонту аг- |
|
комплект- |
|
|||||||
капремонтов |
ному вос- |
гатов гру- |
новных аг- |
комплект- |
тобусов на |
|
регатов лег- |
|
ных автомо- |
|
|||||||
|
станов- |
зовых авто- |
регатов гру- |
ных автомо- |
билей на |
базе готовых |
|
ковых авто- |
|
лению дета- |
мобилей и |
зовых авто- |
билей |
агрегатов |
|
мобилей |
|
|
базе сило- |
|
||||||
|
лей |
автобусов |
мобилей |
|
|
|
|
|
|
|
вых агрега- |
|
|
|
|||
|
|
|
|
|
|
|
|
|
|
|
|
|
|
тов |
|
|
|
0,5 |
|
|
|
|
|
1,07 |
|
|
|
|
|
|
|
|
|
|
|
1,0 |
|
|
|
1,08 |
1,06 |
'1,0 |
|
|
|
|
|
|
|
|
|
|
|
1,5 |
|
|
|
1,04 |
1,03 |
0,96 |
|
|
|
|
|
|
|
|
|
|
|
2,0 |
|
|
|
1,0 |
1,0 |
0,92 |
|
|
|
|
|
|
|
|
|
|
|
3,0 |
|
|
|
0,95 |
0,95 |
|
|
|
|
|
|
|
|
|
|
|
|
4,0 |
|
|
|
0,9 |
0,9 |
|
|
|
|
|
|
|
|
|
|
|
|
5,0 |
1,0 |
1,09 |
|
0,84 |
0,84 |
|
|
|
|
|
|
|
|
|
|
|
|
7,0 |
0,98 |
1,04 |
|
0,77 |
0,77 |
|
|
|
|
|
|
|
|
|
|
|
|
10,0 |
0,96 |
1,0 |
1,0 |
0,75 |
0,75 |
|
1,0 |
|
|
|
|
|
|
|
|
|
|
15,0 |
0,93 |
0,93 |
0,93 |
|
|
|
0,94 |
|
|
|
|
|
|
|
|
|
|
20,0 |
0,90 |
0,89 |
0,89 |
|
|
|
0,89 |
|
|
|
|
|
|
|
|
|
|
30,0 |
|
0,85 |
0,85 |
|
|
|
0,85 |
|
|
|
|
|
|
|
|
|
|
40.0 |
|
0,81 |
0,81 |
|
|
|
0,81 |
|
|
|
|
|
|
|
|
|
|
50,0 |
|
0,8 |
0,8 |
|
|
|
0,8 |
|
|
|
|
|
|
|
|
|
|
60,0 |
|
0.8 |
0,8 |
|
|
|
|
0,8 |
|
|
|
|
|
|
|
|
|
Для ремонтных предприятий малого типа с годовой производственной программой 500 кап. ремонтов и ниже K2 рекомендуется принимать равным 1,1
18
... 1,5. Трудоемкость работ на годовую программу или годовой объем работ Тг определяется перемножением величины трудоемкости ремонта каждого представителя в производственной программе на количество ремонтов в соответствии с заданием на проектирование.
Tr= |
a∙ n(6) |
где n – количество ремонтов в годовой программе для каждого представителя; m– количество представителей в годовой программе.
4.2.5 Расчет годового объема работ и количества производственных рабочих Трудоемкость ремонта может быть определена по документам технологического процесса или по укрупненным нормам времени (4.5) и (6). За-
траты труда определяют в чел. ч.
Результаты расчетов удобно приводить в табличном виде по форме приведенной в таблице 8.
Для этого весь объем работ разбивают по видам согласно технологическому процессу и с учетом профессии исполнителя. Итоговые величины подсчитываются после каждого вида работ и в целом по цеху или заводу.
Количество производственных рабочих по профессиям рассчитывается для каждого цеха или участка в зависимости от годового фонда времени рабочего по формуле:
|
|
|
|
|
|
|
. |
|
Таблица 8 |
|
|
|
|
|
|
|
|
||||
|
|
|
|
|
|
|
|
|
||
Расчет годового объема работ и количества производственных рабочих |
|
|||||||||
|
|
|
|
|
|
|
|
|
||
№ |
Наимено- |
Трудоемкость по объектам ремонта, |
Общая |
Количество ра- |
||||||
пп |
вание работ |
|
чел. ч. |
|
|
|
трудоем- |
бочих, чел |
||
|
|
|
|
|
|
|
|
кость |
|
|
|
|
|
|
|
|
|
|
|
||
|
|
Автомо- |
Силовой |
Задний |
Другие |
|
Расчет- |
Приня- |
||
|
|
биль |
агрегат |
мост |
|
виды |
|
ное |
тое j |
|
|
|
|
|
|
|
работ |
|
|
|
|
|
Итого: |
|
|
|
|
|
|
|
|
|
|
|
|
|
|
|
|
|
|
|
|
4.2.6 Определение состава работающих

19
Состав основных производственных рабочих устанавливают на основании предыдущего расчета, назначают разряда исполнителей и сменность их работы в зависимости от выбранного производственного процесса, а также группы производственного процесса в соответствии с профессией исполнителя и санитарной характеристикой производственного процесса.
Определяется средний разряд по участку (отделению) или заводу:
, |
(8) |
где R1, R2и т.п. – разряди рабочих; n1,n2, и т.п. – количество рабочих в каждом разряде.
Для участков авторемзавода средние разряды рабочих имеют примерно следующие значения: разборочно-моечный – 2,0; сборки автомобилей – 2,7; регулировочный – 3,2; ремонта рам, кабин и кузовов – 2,9; ремонта и сборки агрегатов – 3,2; медницко-радиаторный – 2,5; окрасочный – 2,6; ОГМ – 2,9; инструментальный – 3,2; слесарно-механический – 2,8; кузнечно-рессорный – 2,7; термический – 3,1; сварочно-наплавочный – 3,0; гальванический – 3,2; ремонта электрооборудования – 3,0; ремонта топливной аппаратуры – 3,1; полимерный
– 2,7; обойный, шиномонтажный, аккумуляторный, деревообрабатывающий – 2,6; комплектовочный, дефектовочный – 3,5.
Средний разряд вспомогательных рабочих составляет 2,5 … 2,8, а в целом по заводу для производственных и вспомогательных рабочих он колеблется от
2,7 до 3,5.
Количество производственных рабочих вспомогательного производства и их состав принимается по нормам проектирования соответствующих служб (ОГМ, инструментальных цехов, ОГЭ. компрессорных станций, котельных и т.д.) в зависимости от состава обслуживаемого оборудования основного производства. Прочий штат работающих авторемонтного завода принимается в зависимости от количества производственных рабочих (табл. 9).
Общая численность вспомогательных рабочих по предприятию (в т.ч. производственных рабочих вспомогательного производства) должна составлять не более 45 % от производственных рабочих.
Таблица 9
Количество вспомогательных рабочих
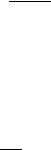
|
|
20 |
|
|
|
|
|
Категория |
Отношение к числу |
|
|
производственных |
Примечание |
||
работающих |
|||
рабочих в процентах |
|
||
|
|
||
|
|
|
|
Вспомогательные ра- |
12 … 15 |
В их число входят: наладчики, смазчики обору- |
|
бочие |
|
дования, распределители работ, кладовщики, |
|
|
|
крановщики, стропальщики, водители наполь- |
|
|
|
ного транспорта, грузчики и другие подсобные |
|
|
|
рабочие. |
|
|
|
|
|
Инженерно-тех- |
13 … 15 |
50 % ИТР заняты на производстве,остальные - |
|
нические работники |
|
в заводоуправлении. |
|
(ИГР) |
|
|
|
Счетно-конторский |
12 … 14 |
1/3 СКП заняты на производстве, остальные - в |
|
персонал |
|
заводоуправлении. |
|
|
|
|
|
Младший обслу- |
2 … 3 |
К МОП относятся: уборщики, курьеры, теле- |
|
живающий персонал |
|
фонистки и т.п. |
|
(МОП) |
|
|
4.2.7 Расчет количества оборудования а) по трудоемкости и количеству оборудования, когда требуется постоян-
ное участие рабочих (металлорежущие старки, разборочно-сборочные стенды и т.п.), шт
(9)
где Тс – годовой объем работ по данной операции в станко-часах. При этом
, |
(10) |
где Кмс. – коэффициент многостаночности, который назначается в зависимости от типа оборудования, чел. ч.; Тг – трудоемкость в чел. ч.; Кз – нормативный коэффициент загрузки оборудования; ФД.О – годовой действительный фонд оборудования в часах.
Дня определения коэффициента загрузки по участку или цеху необходимо суммировать объем работ и количество оборудования. Ориентировочно общий коэффициент загрузки оборудования по авторемонтному заводу составля-
ет К3=0,70 ... 0,85.
б) по производительности оборудования, для которого продолжительность операции не зависит от рабочего (механизированные термические печи, конвейерные моечные машины и т.п.):
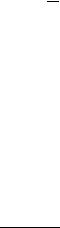
21
, |
(11) |
где N – часовая программа; В – часовая производительность машины по паспорту.
в) по продолжительности технологической операции, которая не требует постоянного присутствия человека в выполнении процесса (испытательные стенды, гальванические ванны и т.п.)
, |
(12) |
где ТМ– машинное время на выполнение одной операции в мин.;Тр– трудоемкость на одну операцию в чел-минутах;Q– годовая производственная программа, шт.;Фдо– действительный годовой фонд оборудования в часах.
Прочее оборудование назначается по производственной необходимости согласно технологическому процессу.
Количество рабочих постов для производства основных видов работ с применением средств механизации определяется по формуле:
|
, |
(13) |
|
где Т– трудоемкость операции в чел. ч.;Фр м– действительный годовой фонд рабочего моста в час; nр– количество рабочих, работающих одновременно на посту, которое зависит от характера работы и объекта и составляет для различных работ следующие величины:наружная мойка, разборка и сборка мелких агрегатов и узлов контроль и комплектовка деталей, устранение дефектов – 1 чел.; разборка и сборка мостов, ремонт кабин и оперения и окраска – 1 … 2 чел.; разборка автомобиля на агрегаты, разборка и сборка двигателей, ремонт рам, сборка автомобиля – 2 … 3 чел.
4.2.8 Расчет производственно-складских помещений Для укрупненных расчетов при решении компоновочных планов цехов и
участков производственно-складские площади можно определить по отдель-
22
ным показателям на I приведенный капитальный ремонт (т.е. на единицу продукции).
Площадь под вспомогательное производство составляет 15 … 18% от основного производства, площадь под закрытые склады соответственно 12 … 15, площадь под магистральные проезды – 8 … 12% и непроизводственные площади (санузлы, тепловые пункты, трансформаторные подстанции и т.п.) – 2 … 3%.
Очень приближенно можно определять площади производственных участков по удельным площадям на единицу оборудования или на одно рабочее место по аналогичному действующему или проектируемому производству. При уточненном определении границ площади производственных подразделений, подсчитываются площади, занятые оборудованием, и по переходному коэффициенту, учитывающему рабочие места, необходимые расстояния между оборудованием, места складирования заготовок и готовой продукции, проходы и проезды (кроме магистральных).
Площади уточняются при рассмотрении грузопотоков в проектируемом подразделении графо-аналитическим методом. В этом случае в заданном масштабе вырезаются из бумаги габаритные модели оборудования (длина, ширина), которые расставляются в производственном подразделении на плане расстановки оборудования с учетом технологического процесса (маршрутная карта) ремонта.
Расчет производственных площадей участков выполняется по форме, приведенной в таблице 10.
|
|
|
|
|
|
Таблица 10 |
Расчет площади |
|
|
|
|
|
|
№ |
Наименование |
Марка, |
Количе- |
Габариты единицы |
Площадь зан. |
Площадь общая, |
|
|
|
2 |
ед. оборудова- |
2 |
|
|
оборудования |
модель |
ство, шт. |
оборудования, м |
ния., м2 |
см. Кпл,м |
|
|
|
|
|
|
|
Итого по участку |
|
|
|
|
|
|
|
|
|
|
|
|
|
Итоговая площадь подсчитывается по каждому участку и перемножается на соответствующий коэффициент Кпл (табл. 11). Площади под площадки складирования принимаются дополнительно без коэффициента. Площади складов рассчитываются по нагрузке, допустимой на пол, с учетом переходов между стеллажами. После окончательного решения планировки цеха составляется ведомость расчетных и принятых площадей.
Таблица 11