
Промышленные роботы Ч. 2 учебное пособие
.pdf3)приводы перемещения каретки, выдвижения руки и ее вращения, поворота плечевого и локтевого звеньев руки;
4)механизмы качания руки, выдвижения кисти, компенсации угла качания кисти, поворота кисти;
5)кисть с однозахватным механизмом, имеющим возможность поворота на 180° и на 90°, с двухзахватным механизмом, с однозахватным механизмом
иавтоматической стеной захватов.
Важной задачей агрегатного конструирования ПР является разработка модульного принципа построения и унификации схемной и алгоритмической части системы их программного управления.
3.3. Система управления РТК
Роботизированный технологический комплекс представляет собой совокупность промышленных роботов, оборудования, транспортных связей, вычислительных и информационных средств, предназначенную для автоматизированного выполнения операций производственного процесса.
Иерархичность структуры РТК учитывается при проектировании как его самого (рис. П. 1.1 прил. 1), так и системы управления им.
Структура системы управления РТК определяется в первую очередь видом объектов управления, характером происходящих в них процессов и взаимодействиями между ними. Такими объектами в составе РТК прежде всего являются технологическое оборудование и промышленные роботы, объединенные в ячейки, транспортные системы и автоматизированные склады. Все эти объекты находятся в определенной иерархической подчиненности и функционируют в составе единого комплекса. Поэтому и структура системы управления комплексом тоже является иерархической, включающей четыре уровня управления (рис. 3.21).
На нижнем (первом) уровне этой системы находится управление робототехнической ячейкой (РТЯ), которое организуется на основе специальных устройств управления с увязкой по времени начала и конца выполнения отдельных операций или с использованием дополнительной информации о ходе технологического процесса. Этот уровень управления осуществляется в виде программного управления и включает в себя также каналы связи с оборудованием и верхними уровнями управления. Реализация этого уровня в настоящее время производится на основе унифицированных устройств управления ПР и основного технологического оборудования.
71
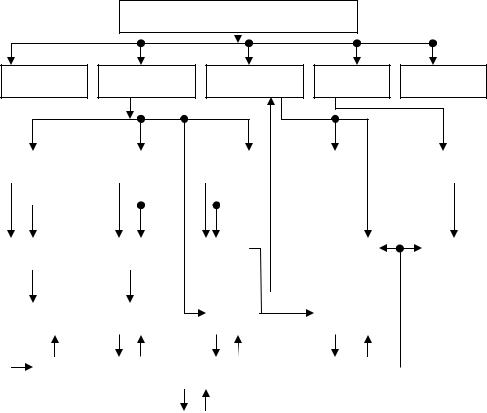
|
Система управления РТК |
|
|
|
1 |
2 |
3 |
4 |
5 |
6 |
|
7 |
|
8 |
|
9 |
|
|
11 |
|
|
|
|
|
|
|
|
|
|
|
|
|
|
|
|
|
|
|
|
|
|
|
12 |
|
|
13 |
|
14 |
|
|
|
15 |
|
|
16 |
|||||
|
|
|
|
|
|
|
|
|
|
|
|
|
|
|
|
|
|
|
|
|
|
|
|
|
|
|
|
|
|
|
|
|
|||
|
|
|
|
|
|
|
|
|
|
|
|
|
|
|
|
|
|
17 |
|
|
18 |
|
19 |
|
|
|
10 |
|
|
|
|
||||
|
|
|
|
|
|
|
|
|
|
|
|
|
|
|
|
||
|
|
|
|
|
|
|
|
|
|
||||||||
|
|
|
Роботы и технологическое оборудование |
|
|
|
|
||||||||||
|
|
|
|
|
|
|
|||||||||||
|
|
|
|
|
|
|
|
|
|
|
|
|
|||||
|
|
|
|
|
|
|
|
|
|
|
|
|
|||||
|
|
|
|
|
Технологический процесс |
|
|
|
|
|
|
||||||
|
|
|
|
|
|
|
|
|
|
|
|
|
|
|
|
|
|
Рис. 3.21. Структурная схема системы управления: 1 – банк данных; 2 – подсистема управления РТК; 3 – подсистема оперативно-календарного планирования; 4 – подсистема контроля качества; 5 – подсистема автоматического контроля и устранения неисправностей; 6, 7 – диспетчер управления оборудованием (ДУО); 8 – диспетчер управления транспортом; 9 – подсистема планирования по объему и номенклатуре; 10 – устройство управления транспорта; 11 – диспетчер управления оборудованием контроля качества; 12, 13 – подсистема выбора программ (ПВП); 14 – подсистема расчета маршрута; 15 – подсистема учета и анализа простоев оборудования; 16 – подсистема учета брака и его статистического анализа; 17, 18, 19 – устройства управления робо-
тов и технологического оборудования (УРТО)
Второй уровень управления обеспечивают системы управления, связывающие отдельные РТЯ в согласованно работающий участок или линию. Аппаратурно этот уровень часто реализуется с помощью мини-ЭВМ. В усовершенствованном варианте на этом уровне может также осуществляться автоматизированный синтез программ функционирования РТЯ. Эффективность применения на данном уровне стандартных мини-ЭВМ обусловлена:
1)возможностью автоматизации технологической подготовки производства, сокращением времени разработки программ и возможностью их быстрой корректировки;
2)повышением надежности передачи информации в результате ликвидации промежуточных программоносителей (магнитные ленты, перфоленты) и устройств считывания с них информации (магнитные головки, фотосчитыватели);
72
3)автоматизацией учета показателей технологического процесса (время обработки, точность и т. д.) и контроля технологических режимов;
4)возможностью автоматизации контроля качества продукции и определения его зависимости от изменения технологических параметров.
Следующим по сложности типом РТК является цех, и, соответственно, система управления цехом образует третий уровень управления, который осуществляет координацию работы участков, автоматизированных складов и внутрицеховых транспортныхсистем. Этот уровень реализуется также с использованием ЭВМ.
Четвертый уровень – уровень оперативно-календарного планирования и контроля. На этом уровне осуществляется составление плана по объему и номенклатуре изделий на смену, сутки, неделю и т. д. Как самостоятельные подсистемы в состав четвертого уровня входят подсистемы диагностики и устранения неисправностей РТК.
3.4.Особенности систем управления роботами
3.4.1.Дистанционные системы управления
Вроботах последних поколений используется дистанционное управление. Внутренняя система управления роботом при дистанционном управлении может быть программной или адаптивной. Чаще всего используются адаптивные системы (рис. П. 2.2. прил. 2). Устройства, воспринимающие информацию
овнешней среде, обрабатывают информацию и выбирают последовательность обхода уже имеющихся в программе робота точек позиционирования.
Основное свойство адаптивных систем – реализация цели управления
вусловиях недетерминированной внешней среды и дрейфа параметров робота – отражается в структуре двумя новыми (по сравнению с программными системами) элементами: информационной системой и устройствами для вычисления координат целевых точек и последовательности их обхода, использующими информацию об изменениях, произошедших во внешней среде и компонентах робота. Функции управления адаптивным роботом выполняет вычислительное устройство, уровень сложности которого определяется уровнем адаптации робота. В простейшем случае это может быть микропроцессор или микроЭВМ (для сложных адаптивных робототехнических систем вычислительное устройство может представлять собой мультимикропроцессорную сеть).
Дополнительно к ним присоединяется дистанционная система управления,
вкомплексе они образуют единую многоканальную систему (рис. 3.22).
73
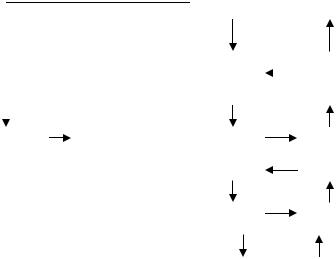
|
|
|
Человек-оператор |
|
|||||
|
|
|
|
|
|
|
|
|
|
|
|
|
|
|
|
|
|
||
|
|
Пульт супервизорного |
|
|
Система отображения |
||||
|
|
управления |
|
|
|
обстановки |
|||
|
|
|
|
|
|
|
|
||
|
|
|
|
|
|
|
|
||
Рукоятка |
|
Управляющая система |
|
|
Система обработки |
||||
|
|
робота с микроЭВМ |
|
|
|
информации |
|||
|
|
|
|
||||||
|
|
|
|
|
|
|
|
||
|
|
|
|
|
|
|
|
||
|
|
Манипулятор робота |
|
|
Система очувствления |
||||
|
|
|
|
|
|
|
|
|
|
|
|
|
|
|
|
|
|||
|
|
|
|
|
Среда |
|
|
||
|
|
|
|
|
|
|
|
|
|
Рис. 3.22. Схема системы управления роботом
Разновидностью дистанционного управления является супервизорное. Оно заключается в следующем (рис. П. 2.3. прил. 2). На пульте управления у человека-оператора установлены дисплейное и другие устройства и приборы отображения обстановки в рабочей зоне робота. Здесь действует канал информационной дистанционной связи робота с человеком. Последний, наблюдая таким образом обстановку и действия робота, принимает решения о подаче тех или иных управляющих команд со своего пульта в зависимости от сложившейся обстановки. ЭВМ робота, получив команду, исполняет ее по соответствующей программе. Набор различных программ придан роботу заранее.
Каждая программа указанного набора соответствует автоматическому выполнению роботом определенной операции, поэтому человеку-оператору отводится функция распознавания обстановки и выдачи ЭВМ робота задания на определенную операцию, которая роботом затем самостоятельно исполняется в автоматическом режиме. В этом состоит смысл супервизорного дистанционного управления действиями робота со стороны человека-оператора.
Выдача человеком команд роботу по дистанционному управляющему каналу может осуществляться различными способами. Например, может подаваться кодовый признак программы (в виде некоторого числа) на выполнение определенной операции, затем он заменяется кодовым признаком другой программы и т.д. В зависимости от возможностей робота отдельные программы могут соответствовать достаточно простым частям операции, которую должен выполнить робот, или же всей сложной операции в целом.
74
В других случаях супервизорная команда образуется на экране в виде целеуказания. Например, световым карандашом на экране телевизора можно указать точку, в которую должен переместиться схват манипулятора робота и взять там заданный предмет, что автоматически роботом и осуществляется.
Оба канала дистанционной связи (информационный и управляющий), как правило, должны быть снабжены микроЭВМ или микропроцессорными устройствами для обработки информации с целью ее наилучшего отображения на пульте оператора и для формирования программ и целеуказательных сигналов управления по командам человека-оператора.
3.4.2. Автоматические и полуавтоматические системы управления
Автоматические системы управления позволяют роботу выполнять тех-
нологический процесс без участия оператора.
Система управления повышенной надежности. В некоторых системах для экстремальных условий с большой неопределенностью целесообразно наряду с автоматическими режимами действия робота ввести их комбинацию с полуавтоматическим управлением через ЭВМ исполнительного уровня, добавив на пульт оператора управляющую рукоятку. Это делается для повышения надежности системы в целом. Предполагается, что в экстремальных условиях человекоператор не может подойти непосредственно к роботу и к его местной стойке управления, чтобы перепрограммировать или обучить новым действиям. Поэтому ручной режим, необходимый для этих целей (как и в обычных промышленных роботах), здесь делается дистанционным с удаленного пульта оператора. Особенно это важно в каких-либо непредвиденных или аварийных ситуациях.
Полуавтоматические системы управления. Полуавтоматическое управ-
ление основано на сечетании ручного и автоматического управления. Полуавтоматическая система управления манипулятором отличается от копирующей другим характером задающего устройства и наличием вычислителя. Здесь в качестве задающего устройства вместо многозвенного механизма, повторяющего кинематику рабочего манипулятора, применяется управляющая рукоятка с несколькими степенями свободы.
Управляющие рукоятки имеют самые разные принципы построения и конфигурации. Число управляющих перемещений в рукоятке должно быть равным числу степеней подвижности рабочего манипулятора, а кинематическая схема может быть произвольной, но должна быть удобной для работы челове-
75
ка-оператора с рукояткой. Конструктивно необходимо обеспечить малость управляющих перемещений с точным съемом соответствующего электрического сигнала пропорционально перемещению.
Существуют управляющие рукоятки без механических перемещений. Они снабжаются тензорезисторными измерителями силы нажатия руки человека. Рукой производятся нажатия вдоль трех осей, а также поворотные нажатия, при этом число сигналов, снимаемое с измерителей, установленных на рукоятке в различных направлениях, должно соответствовать числу степеней подвижности рабочего манипулятора.
Во всех случаях человек-оператор следит визуально за результатом своих действий по изображению фактического движения рабочего манипулятора (на телевизионном экране или непосредственно через стекло) и корректирует это движение дистанционно с помощью той же управляющей рукоятки.
Заметим, что при силовом алгоритме управления человек-оператор ощущает на рукоятке реальные усилия взаимодействия рабочего манипулятора с объектом своей работы (в определенном масштабе). Эта дополнительная информация вместе с упомянутой визуальной значительно увеличивает эффективность проведения работ. Как и в копирующих системах двустороннего действия, это создает эффект присутствия. Но здесь он реализуется значительно проще с участием микропроцессорного вычислительного устройства.
Сигналы от управляющей рукоятки поступают в микропроцессорное вычислительное устройство, где они преобразуются по определенным алгоритмам, в результате чего формируются сигналы управления, подаваемые на все приводы звеньев рабочего манипулятора.
В такой полуавтоматической системе благодаря наличию микропроцессорного вычислительного устройства могут быть реализованы самые разнообразные алгоритмы управления и осуществлены движения в любой системе координат независимо от кинематики манипулятора и конфигурации управляющей рукоятки. Наиболее типичны три вида алгоритмов управления: скоростной, силовой и позиционный. В них предполагается изменение скорости, силы
иосуществление перемещения на рабочем конце манипулятора пропорционально величине нажатия руки человека на управляющую рукоятку (по модулю
инаправлению).
При скоростном алгоритме управления величина смещения рукоятки по каждой степени подвижности преобразуется в электрический сигнал, про-
76
порциональный величине смещения. Эти сигналы посылаются в микропроцессорный вычислитель. Там, во-первых, происходит преобразование координат управляющей рукоятки в координаты рабочего манипулятора и, во-вторых, формирование сигналов управления приводами по каждой степени подвижности манипулятора таким образом, чтобы конец манипулятора (схват или инструмент) получил скорость движения в том же направлении, в каком человек нажал на управляющую рукоятку. По значению эта скорость должна быть пропорциональна величине смещения управляющей рукоятки. При этом, очевидно, общая величина и направление смещения складываются из составляющих в системе координат рукоятки, а общее значение и направление скорости схвата – из составляющих в системе координат рабочего манипулятора. При формировании сигналов управления в микропроцессорном вычислителе для повышения качества процесса управления по правилам теории автоматического регулирования могут добавляться производные и интегралы от основного сигнала, пропорционального величине смещения в управляющей рукоятке. Вместо этого, если в манипуляторе ставятся следящие приводы, требуемое качество процесса управления может достигаться также внутренними обратными связями и дифференцированиями в самой следящей системе каждого привода.
При силовом алгоритме управления аналогично происходит весь процесс снятия сигналов с управляющей рукоятки и преобразования их в микропроцессорном вычислителе с последующим формированием сигналов управления приводами рабочего манипулятора. Но существенное отличие состоит в том, что пропорционально общему смещению управляющей рукоятки создается сила, как бы тянущая за конец манипулятора, чем и определяется его движение. Непосредственно эта сила реализуется при соприкосновении схвата или инструмента с каким-либо внешним предметом. Эта сила по величине и направлению соответствует общему смещению рукоятки (сила и смещение складываются из составляющих в своих системах координат). Смещение управляющей рукоятки пропорционально силе нажатия руки человека за счет того, что управляющая рукоятка подпружинена на каждой степени подвижности. Следовательно, можно сказать, что сила, образующаяся на конце рабочего манипулятора, пропорциональна по величине и одинаково направлена с силой нажатия человека на рукоятку. Кроме того, пружины в рукоятке нужны, чтобы рукоятка возвращалась в нулевое положение, когда человек перестает на нее нажимать.
77
При позиционном алгоритме управления происходит аналогичная процедура преобразования и формирования сигналов, но разница состоит в том, что в результате получаются величина и направление смещения конца рабочего манипулятора, пропорциональные величине и направлению смещения управляющей рукоятки от руки человека-оператора.
Существуют полуавтоматические системы, в которых заложены все три основных вида алгоритмов дистанционного полуавтоматического управления, при этом человек-оператор может включать попеременно любой из них. Например, для транспортного перемещения манипулятора в зоне его действия целесообразно скоростное управление. Вблизи объектов действия, где нужно соблюсти величины смещений в малой окрестности, необходимо позиционное управление. При рабочем контакте с объектом требуется силовое управление, позволяющее человеку-оператору осуществлять в процессе работы определенное силовое воздействие на объект. Средство переключения алгоритмов управления выводится на пульт управления человека-оператора, однако в конкретных случаях проведения определенных манипуляционных работ удается организовать в системе автоматическое переключение алгоритмов управления по соответствующим сигналам датчиков.
3.5. Алгоритмы управления манипуляционными промышленными роботами 3.5.1. Анализ существующих методов управления ПР
Планирование траектории движения манипулятора промышленного робота осуществляется с помощью алгоритмов управления планированием. Эти алгоритмы управления рассматриваются как нелинейные алгоритмы разделения командного движения по степеням подвижности манипулятора. Их реализация связана с решением нелинейных уравнений, характеризующих конфигурацию механизма при заданном положении рабочих органов промышленных роботов. Для решения таких нелинейных задач прибегают либо к помощи ЭВМ, либо к имитационному моделированию с использованием реальных моделей манипуляционных систем.
Для линеаризации уравнений, описывающих поведение манипуляционной системы при малых изменениях координат элементов механизма, обычно прибегают к дифференцированию по времени координат положения звеньев в сложном механизме, связанном нелинейными зависимостями, либо к компенсации нелинейностей при помощи регуляторов и обратной связи.
78
Задачей управления является выработка алгоритма требуемого функционирования приводов манипулятора. При этом используется несколько методов управленияпланированиемтраекториидвиженияманипуляторапромышленногоробота.
Метод управления по вектору скорости. Скорость движения рабочих ор-
ганов манипуляционной системы задается в виде шестимерного вектора, представляющего проекции векторов угловой скорости рабочего органа и скорости его некоторой точки в какой-либо системе координат, которая предусматривается алгоритмами управления таким образом, чтобы полностью определить скорость рабочего органа в текущей точке траектории.
Непосредственное использование этого метода для целей управления ограничивается возникновением в процессе управления вырожденных конфигураций механизма, которые должны учитываться алгоритмом управления. Такой метод управления является эффективным, если необходим быстрый перевод рабочего органа из одного положения в другое и не требуется высокой точности позиционирования. Кроме того, метод обладает достаточной сложностью реализации.
Метод последовательных корректировок положения. Он наиболее широ-
ко применяется в цифровых системах управления. В этом случае алгоритм управления по вектору скорости формируется как приращение координат манипулятора за один цикл вычисления алгоритма.
Недостатком метода является частая выборка узловых точек сложной траектории, чтобы переходы от одной точки к другой при планировании траектории движения не меняли принципиально необходимой картины движения.
Приближенные методы. При синтезе системы управления манипулятором пользуются приближенными решениями, которые вытекают из ограниченности задания значений координат. Обычно берут три значения: два крайних и одно среднее – и для них вычисляют обратную матрицу Якоби, зависящую от конфигурации манипулятора. Для всех других значений координат (в том числе и узловых, характерных точек траектории) обратная матрица вычисляется интерполированием. Во многих случаях, особенно при наличии обратной связи по положению, этого оказывается вполне достаточно для достижения конечной цели управления.
Недостатком метода являются возникающие при интерполяции ошибки, достигающие большого значения, особенно при отсутствии обратной связи по положению.
79
Метод управления по вектору силы. К недостаткам метода управления по вектору скорости следует отнести невозможность обеспечивать формализацию стремления перемещения рабочих органов промышленных роботов в заданном направлении, если на заданной траектории встречаются точки, в которых матрица конфигурации манипулятора является вырожденной.
Тенденция к упрощению процесса управления и обусловленных им вычислений привела к использованию метода управления по вектору силы, в котором имитационно реализуется идея управления по заданному направлению. В действительности к манипулятору не прилагаются никакие силы, но следящие приводы развивают совокупность обобщенных сил, которые динамически эквивалентны заданным силам, имитирующим их приложение к манипулятору. Вычислитель, получив на входе задающие сигналы, определяет обобщенные силы и относит их к координатам, которые непосредственно управляются приводом. В свою очередь, приводы постоянно вырабатывают такие обобщенные силы, которые получаются на выходе вычислителя. В эти обобщенные силы могут автоматически вводиться поправки регуляторами и компенсаторами.
3.5.2.Анализ существующих методов компенсации нелинейностей
иразвязки взаимодействий в ПР
Основной задачей управления промышленными роботами является генерирование внешних моментов u(t) таким образом, чтобы движение робота осуществлялось по выбранной траектории. Движение робота обычно осуществляется двумя различными контролируемыми фазами. Первой из них является контрольная фаза грубого движения, во время которой робот перемещается от изначальной позиции в окрестность места расположения заданной цели вдоль предварительно определенной траектории. Второй контрольной фазой является стадия точного движения, когда рабочий орган робота динамически взаимодействует с объектом, используя при этом информационный канал обратной связи от внешних датчиков для выполнения задачи.
Если в роботах используется традиционная следящая техника, то нелинейности, присутствующие в динамике манипулятора, не могут быть скомпенсированы на стадии грубого движения. С повышением требований к рабочим характеристикам промышленных роботов становится необходимым принимать во внимание динамические эффекты. Поэтому в течение последнего времени было предложено большое число усовершенствований в схемах и алгоритмах непосредственного контроля промышленных роботов.
80