
Современные научные исследования в дорожном и строительном производс
..pdfили специалистов, которые предоставляют услуги. Немаловажным является
итот факт, что по аутсорсингу совсем не проработана российская законодательная база.
Из всего вышеизложенного можно сделать вывод: самым рациональным
иэкономически выгодным путем поддержания подвижного состава в рабочем исправном состоянии является путь радикального распределения. Он четко разделяет работы, выполняемые на предприятии и в сторонних организациях; часть работ остается на предприятии, тем самым наблюдается экономия материальных ресурсов. Этот путь является рациональным и выгодным именно для предприятий с небольшим количеством подвижного состава, так как на крупных предприятиях с большим числом подвижного состава целесообразно организовать производство или перевооружить производственно-техническую базу. Аутсорсинг стоит рассматривать как перспективу, так как в Российской Федерации он еще недостаточно развит и качество услуг может не удовлетворить потребности нашего предприятия.
Список литературы
1.Техническая эксплуатация автомобилей:. учебник для вузов / под ред. Е.С. Кузнецова. – 3-е изд., перераб. и доп. – М.: Транспорт, 1991. – 413 с.
2.Бухгалтерский учет, налогообложение, аудит. – URL: http:// www.audit-
it.ru/
3. Напольский Г.М. Технологическое проектирование АТП и СТО.
131
ОРГАНИЗАЦИЯ РЕМОНТА КУЗОВОВ АВТОМОБИЛЕЙ В ДИЛЕРСКОМ ЦЕНТРЕ
А.Д. Некрасов, В.В. Афанасьев
Пермский государственный технический университет, Россия
Организация кузовного ремонта – удовольствие дорогое, но прибыльное. Стоимость кузовных работ в среднем составляет от 5 до 15 тыс. руб. Кузовной ремонт – это универсальный вид работ, спрос на него, безусловно, есть и со временем будет только расти. Кузовной ремонт машины – это исправление внешних и внутренних повреждений кузова транспортного средства с использованием современных технологий и специализированного оборудования.
К некоторому преимуществу центра кузовного ремонта можно отнести то, что для него не имеет особого значения, где он расположен, по той причине, что работы достаточно дорогие и сложные, а с качеством у многих компаний, занимающимися кузовным ремонтом, большие проблемы, поэтому многие клиенты готовы не только на то, чтобы в другой район ездить, парой даже в другую область.
В данной статье речь пойдет об организации кузовного ремонта в дилерском центре, для того, чтоб была понятнее суть статьи да и проблемы в целом, давайте рассмотрим проблему и возможную организацию ремонта кузовов на примере дилерского центра Мазда «Восток Моторс Пермь».
На сегодняшний день в автоцентре «Мазда» кузовной ремонт как таковой отсутствует, ремонт кузовов осуществляют подрядные организации. Но существуют определенные требования, предъявляемые к дилерским центрам, и одним из таких требований является наличие собственного центра ремонта кузовов, иначе в любой момент автоцентр «Мазда» может потерять право на продажу автомобилей, следовательно от сюда «вытекает» первая и самая главная проблема, а именно отсутствие центра кузовного ремонта. К следующей проблеме я бы отнес все вопросы, касающиеся организации ремонта кузовов. Основной задачей является не только проведение работ по ремонту кузовов, окраске, но и то, что центр кузовного ремонта должен приносить некую прибыль для компании; во-первых, необходимо, чтобы центр кузовного ремонта за определенный период окупил себя, во-вторых, необходимо оплачивать зарплату рабочим, задействованным в нем, в-третьих, качество проводимых работ должно соответствовать определенному уровню.
На данный момент существует две основные проблемы, а именно:
1.Отсутствие центра кузовного ремонта.
2.Поиск способа организации с целью получения выгода.
132
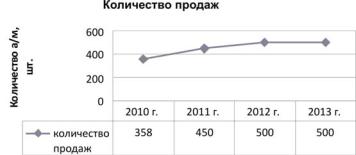
Итак, рассмотрим пути решения данных проблем. Для начала нам необходимо проанализировать, а целесообразно ли нам вообще строить либо арендовать помещение в долгосрочную аренду для собственного центра кузовного ремонта?
Проведем расчеты, для этого нам понадобятся:
1.Количество проданных автомобилей автоцентром за последний год.
2.Прогноз продаж автоцентром на следующие 2–3 года.
3.Парк автомобилей, в данном случае – количество автомобилей марки «Мазда», зарегистрированных в г. Перми.
Продажи за 2010 г. и плановое число продаж представлены на рисунке.
Рис. Количество продаж за 2010 г. и план на следующие три года
Приступим к расчету: парк а/м 4357, из них мы планируем обслуживать 15 %, в 2011 г. плановое число продаж 450 а/м из них порядка 60 % будет обслуживаться у нас, следовательно, в 2011 г. плановое число клиентов центра кузовного ремонта составит: 4357·0,15 + 450·0,6 = 653,5 + 270 = 923 автомобиля в год, это 77 автомобилей в месяц
В 2012 году: 4357·0,15 + 500·0,6 + 67 (15 % от продаж предыдущего года) = 653,5 + 367 = 1020 автомобилей в год, или 85 автомобилей в месяц. Обслуживание 70 с лишним автомобилей в месяц – это вполне «приличный» по площадям центр кузовного ремонта.
Теперь рассмотрим вторую проблему. Очевидно, что основными факторами, влияющими на эффективность работы предприятия, являются правильная организация процесса и наличие необходимого и достаточного количества квалифицированных специалистов для проведения как непосредственно авторемонтных операций, так и вспомогательных. Это необходимые условия, без выполнения которых рентабельность предприятия окажется обязательно ниже ожидаемой. Разумеется, что к числу необходимых условий следует обязательно добавить оснащенность каждого поста обязательным инструментом и оборудованием.
Теперь о менее очевидном, но влияющим на выработку предприятия
вогромной степени. Имеется в виду грамотная планировка рабочих площадей,
впервую очередь той, на которой осуществляется кузовной и малярный ремонт.
133
Специалист сразу же замечает допущенные ошибки в планировочных решениях. Почему-то некоторые владельцы пытаются создать планировочное решение сами, не желая проконсультироваться с теми, кто посвятил этому вопросу долгое годы, знаком со всеми нюансами этой работы и уже оборудовал многие участки. Если при таком подходе преследуется цель сэкономить деньги, то это более чем наивно. Сиюминутная экономия в общем-то небольших средств обязательно обернется большими потерями в процессе работы автосервиса. Правильная планировка центра кузовного ремонта и организация работ в нем способны без дополнительных затрат повысить прибыльность предприятия минимум на 50 %.
Чтобы утверждение не выглядело голословным, приведем практический пример. Рассмотрим финансовые потери на примере подобного предприятия.
Итак, прибывает очередной автомобиль, требующий кузовного ремонта. Мастер-приемщик оформляет все необходимые документы, на станции имеются свободный пост и незагруженный специалист. Казалось бы, машину можно начинать немедленно ремонтировать, а следовательно, и зарабатывать деньги. Но все не так просто, как кажется: автомобиль у ворот, а пост – в дальнем углу станции. А двор и цех уже заставлены другими автомобилями, часто обездвиженными и ожидающими моториста, арматурщика или другого специалиста. Собирается команда из трех-пяти рабочих (некоторые высокой квалификации), и «пострадавшего» пытаются протолкнуть к месту ремонта. Мешающие машины растаскиваются вручную, и проезд освобождается. Затем восстанавливается первоначальная диспозиция – «раскиданные» автомобили возвращаются на свои места. Хорошо, если все обойдется без вмятин и царапин на машинах. И такое случается, что требует дополнительных затрат на незапланированный ремонт.
Попробуем разобраться – сколько денег теряет автосервис из-за такой, организации планировки. Порядка 10–20 мин уходит на подобную доставку машины к месту ремонта.
Что означает такая, казалось бы, не очень значительная потеря времени? Считаем, причем опять по минимуму: отвлекаются на бессмысленную работу три человека, бесцельная потеря времени каждым – 0,25 часа, а сервис принимает в ремонт четыре автомобиля в день. Получается, что каждый день предприятие теряет 3 нормо-часа, что, в свою очередь, сопровождается финансовыми потерями. Сюда же следует прибавить время, потраченное на перемещение автомобилей по территории станции. В среднем, во время ремонта автомобиль приходится перемещать четыре раза (от стапеля в зону подготовки, затем в ОСК и т.д.). Считаем, что на каждое такое перемещение необходимо 15 мин. При четырех автомобилях в день такие «передвижки» займут 12 нормо-часов, учитывая, что их осуществляют те же три сотрудника. Итого 12+3 – получается, что 15 нормо-часов в день тратятся на перемещение автомобилей. Безусловно, 60–70 % этого времени необходимо для ремонта, так как разные виды работ производятся в разных местах, а следовательно, есть объективная необходимость в таких перемещениях. Но вот остальные 30–40 % – это то время, кото-
134
рое затрачено на бесполезное раздвигание и толкание автомобилей, которые мешают продвижению к месту ремонта или во время ремонта по технологической цепочке. 30 % – 15 часов – получается, что 4,5 нормо-часа затрачивается в автосервисе сверх технологически необходимого. И если учесть, что один рабочий цикл окрасочно-сушильной камеры занимает примерно 2,5 ч, то реально автосервис мог бы выпускать из окрасочного цеха дополнительно 1–2 автомобиля ежедневно.
Правильное размещение оборудования в рабочей зоне не менее важно, чем организация движения автомобилей. Например, в одном из автосервисов две окрасочно-сушильные камеры и три зоны подготовки были расположены в одну линию, а два стапеля установлены, наоборот, напротив окрасочных камер. Такое решение нельзя назвать правильным по двум причинам. Во-первых, приходится проводить два сложных криволинейных перемещения: первое – от стапеля к зоне подготовке наискосок и второе – от зоны подготовки в камеру с поворотом на 180º. А если учесть, что очень часто автомобиль сначала маскируется, а потом ставится в окрасочную камеру, то задача по перемещению еще более усложняется, что увеличивает потери времени. Гораздо проще работать, если установить зоны подготовки напротив окрасочных камер. В этом случае автомобиль из зоны подготовки в камеру перемещается по прямой. Во-вторых, зону кузовного ремонта попросту необходимо отделять от зоны окраски, так как кузовной ремонт более «грязный» и включает пожароопасные операции, например сварку или резку металла, а в зоне окраски присутствует легковоспламеняемые материалы.
Также бывает и размещение рабочих постов в технологических проездах. Такая «экономия» площадей недопустима. Сюда же относятся случаи сокращения расстояния между постами, так что для перемещения автомобиля, последний приходится «переносить на руках». Опять бессмысленные потери времени. Чтобы избежать подобных ситуаций, создание планировочного решения необходимо поручать специалистам, которым известны проверенные практикой нормативы.
Помощь специалистов особенно неоценима в случаях размещения маляр- но-кузовных участков в плохо приспособленных для такой деятельности помещениях, к примеру, ширина которых составляет 12–18 м. Тут правильно с технологической точки зрения разместить оборудование и агрегаты очень непросто, но возможно, разработав индивидуальное решение.
И наконец, о редко встречающейся ситуации, когда на предприятии имеется переизбыток ремонтного оборудования. Стремление руководителей обустроить с его помощью дополнительный рабочий пост понятно. Но если такое решение идет вразрез с оптимальным планировочным вариантом, то можно гарантировать отсутствие ощутимых положительных результатов. Скорее следует ожидать отрицательного эффекта.
135
Для того чтобы избежать подобных ситуаций, необходимо консультироваться с поставщиками оборудования, оценивать организацию в подобных предприятиях, тем более что большинство серьезных компаний на сегодняшний день оказывают помощь в размещении оборудования и организации рабочих мест и делают это, как правило, бесплатно. Но если какая-либо компания этого не делает, то есть смысл сменить поставщика, даже если он предлагает оборудование по более привлекательной цене. Ведь неправильная планировка – это причина непрерывной потери средств при последующей работе.
Из всего вышесказанного вывод следует один – для того чтобы организовать эффективную работу центра кузовного ремонта, нужно проделать значительную работу, потратитьвремя на расчеты, а также на литературу.
Список литературы
1.Волгин В.В. Автосервис производство и менеджмент практическое пособие. – 4-е изд., изм. и доп. – М.: Дашков и К°, 2009. – 576 с.
2.Автосервис – это бизнес // Журнал АБС, Сервис. – 2007. – № 10.
136
КОМПЛЕКС ДЛЯ ОСУЩЕСТВЛЕНИЯ НЕПРЕРЫВНОГО МОНИТОРИНГА И ЭКСТРЕННОГО РЕМОНТА МЕТАЛЛИЧЕСКИХ КОНСТРУКЦИЙ
И.А. Осокин, А.С. Пермикин
Уральский государственный университет путей сообщения, г. Екатеринбург, Россия
Непрерывный мониторинг состояния конструкций (НМС) – система наблюдения за условиями работы и поведением конструкции, направленная на
обеспечение |
сохранения его функциональных потребительских свойств |
в заданных |
пределах, осуществляемая на непрерывной, длительной основе |
с использованием измерительной аппаратуры и обеспечивающая предоставление информации о состоянии конструкции в реальном режиме времени.
Традиционно оценка технического состояния конструкции осуществлялась на основе осмотров, обследований (осмотров сооружения, сопровождаемых инструментальными измерениями) или испытаний.
Осмотры, обследования больших сооружений и сложных конструкций являются трудоемкими из-за большого объема обследования и сложности доступа обследователей к узлам конструкции. Испытания конструкций являются дорогостоящими, так как требуют использования испытательной нагрузки или динамических возбудителей.
Важное преимущество НМС мостовой конструкции – накопление экспериментальных данных о нагрузках и воздействиях, об условиях работы конструкции, которые могут быть эффективно использованы для повышения надежности и сроков эксплуатации других сооружений, в том числе при разработке нормативных документов и проектировании.
С развитием информационных технологий, совершенствованием измери-
тельной |
техники |
появляется возможность |
создания систем |
НМС как |
||
на строящихся, так |
и |
на эксплуатируемых |
конструкциях. |
НМС позволяет |
||
в течение |
длительного |
времени получать |
информацию |
о |
напряженно- |
деформированном состоянии, об обращающихся нагрузках, различных воздействиях и других показателях эксплуатации конструкции и принимать эффективные решения по управлению ее эксплуатацией.
При осмотрах выявляются дефекты на той стадии развития, на которой они стали доступны для осмотра. Причины появления дефектов не всегда могут быть выяснены даже опытными специалистами, они определяются предположительно. При такой практике принятие своевременного и надежного решения по устранению и предупреждению дефектов затруднено.
137
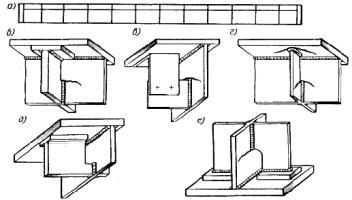
Применение НМС позволяет фиксировать условия работы и поведение конструкции непрерывно. Поэтому внештатные или пиковые воздействия, такие как землетрясения, ураганные порывы ветра, проход сверхнормативной нагрузки и другие, вместе с соответствующими изменениями в условиях работы конструкции будут зарегистрированы.
В эксплуатируемых металлоконструкциях могут происходить необратимые механические изменения, называемые усталостными повреждениями, которые накапливаются и приводят к возникновению микроскопических трещин. Дальнейшее развитие трещин приводит в лучшем случае к усталостной поломке металлоконструкций, а в худшем – к катастрофе. Поэтому задача предупреждения усталостного разрушения является весьма важной и всегда актуальной.
Наиболее характерные типы трещин в сварных балочных пролетных строениях со сплошными стенками различных конструкций представлены на (рис. 1). Наибольшее распространение имеют трещины в стенках у верхних концов сварных швов вертикальных ребер жесткости. Чаще трещины этого типа встречаются около ребер, верхние торцы которых соединяются с верхним поясом через прокладки, приваренные только к ребрам. Главная причина появления и развития этих трещин – высокие циклические напряжения у концов сварных швов, связанные со стесненным изгибом стенки из ее плоскости, вибрацией стенок, наличием больших растягивающих остаточных напряжений [2].
Рис. 1. Характерные типы трещин в сварочных балочных пролетных строениях со сплошными стенками [2]: а – схема главной балки; б – трещина в стенке балки у верхнего конца сварного шва вертикального ребра жесткости (торец ребра приварен к прокладке); в – трещина в стенке балки у верхнего конца сварного шва вертикального ребра (ребро к верхнему поясу прикреплено с помощью уголка на высокопрочных болтах); г – трещины на стенке балки у верхнего конца сварного шва вертикального ребра жесткости, в ребре жесткости и в верхнем поясном листе у сварного шва (торец ребра приварен к поясному листу); д – продольная трещина на поясном шве; е – трещина в стенке балки у нижнего конца сварного шва вертикального
ребра жесткости
138
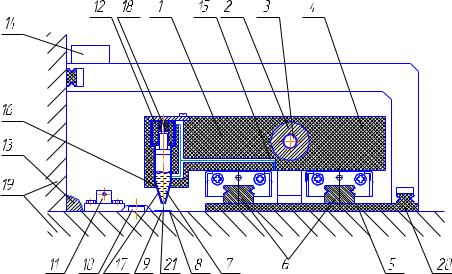
Мы предлагаем устройство для обнаружения трещин и автоматического восстановления сплошности металлоконструкций. Задача предлагаемого устройства – автоматизировать процесс обнаружения и устранения дефектов на поверхности металлоконструкций. Задача решается путем применения датчиков, использования их показаний для управления процессом обнаружения и устранения дефектов, а сварочное устройство выполнено передвижным, управляемым с помощью радиосигнала. Сущность нашего изобретения заключается в том, что выбирается зона возможного возникновения дефектов на открытой поверхности металлоконструкции, на эту зону устанавливаются датчики, сигналы от них с помощью радиоустройства поступают на центральный пост управления, с которого производят «опрос» датчиков согласно разработанному алгоритму, при этом при срабатывании определенного датчика на центральный пост управления приходит конкретная информация о наличии, координатах, типах, размерах и скорости развития дефектов. На основании этих данных определяют прогрессирующий дефект и по радиосигналу от соответствующего датчика включается передвижное сварочное устройство с емкостью для металлотермитной смеси и перемещается к дефекту. Устройство располагается над трещиной, затем по радиосигналу выключается двигатель передвижного сварочного устройства, по этому же сигналу включается работа емкости с экзотермической смесью, осуществляется ее выталкивание и поджиг, а после опорожнения емкости передвижное сварочное устройство также по радиосигналу возвращается в парковочное место, где заменяют пустую емкость на заполненную металлотермитной смесью (заявка № 2010105877 (008325) от 18.02.2010 г.).
Рис. 2. Схема передвижного сварочного устройства
139
На рис. 2 представлена схема передвижного сварочного устройства. Устройство монтируется вдоль сварного шва 13, соединяющего элементы металлоконструкции 19. В непосредственной близости от него расположены датчики: струнный трещиномер 11, полоса тензодатчиков 10, датчик-шлейф 8. Устройство состоит из цельнометаллического корпуса 1, который опирается на две направляющие 6, установленные на основании 5. Устройство перемещается посредством червячной передачи, состоящей из винта 3 и гайки 2. В корпусе выполнен канал для электрических проводов 15, по которым осуществляется питание электромагнита 12 и электрозапала 16 металлотермитной смеси 7, загруженной в сменную емкость 17. Сменная емкость 17 состоит из цилиндрической и конической частей, причем последняя часть обеспечивает подачу металлотермитной смеси 7 точно к дефекту 9, благодаря точному определению координат с помощью контактных щупов 21, а в цилиндрической части сменной емкости расположен поршень 18, приводимый в движение электромагнитом 12, обеспечивающим регулируемую подачу металлотермитной смеси 7 в коническую часть сменной емкости 17. На корпусе 1 сварочного устройства расположено устройство 14 (для подачи радиосигнала на центральный пост управления). Все сварочное устройство закрыто неметаллическим кожухом 4, закрепленным с помощью защелки 20 на основании 5.
Внедрение устройства необходимо для обнаружения мелких трещин, предупреждения их опасного развития и восстановления сплошности металлоконструкций от более крупных трещин. Устройство обладает малыми габаритными размерами и требует незначительных энергозатрат, что существенно облегчает его установку и эксплуатацию. Предлагаемая нами емкость для термитной сварки может входить в состав систем автоматического оповещения и заваривания трещин, что позволяет обойтись без участия человека, таким образом происходит снижение численности обслуживающего персонала. А технология термитной сварки позволяет осуществить всю запитку системы от аккумуляторов.
Устройство для заполнения термитной смесью в трещины строительной конструкции включает емкость и механизм подачи термитной смеси под давлением.
Рассматриваемый мехатронный модуль должен обеспечивать поступательное движение рабочего органа. Выбираем передачу, преобразующую вращательное движение в поступательное (из-за меньшей стоимости).
В данном устройстве выбираем передачу «винт-гайка-скольжения» (ВГС). Передача «винт-гайка-скольжения» предназначена в основном для преобразования вращательного движения в поступательное и лишь в редких случаях – поступательного во вращательное. Конструкции передач просты и технологичны.
140