
Металлорежущие станки
..pdf
Рис. 76. Структура, обеспечивающая ломаный ряд
Сложенные структуры
При больших значениях диапазона регулирования привода станка нередко оказывается невозможным осуществить простую множительную структуру, так как диапазон регулирования последней переборной группы получается больше допустимого. В подобных случаях целесообразно применять сложенную структуру привода.
Сложенной называется структура, состоящая из двух (или более) кинематических цепей, каждая из которых является простой множительной структурой. В этом случае число ступеней скорости привода z равно сумме ступеней скорости всех составляющих его множительных структур:
z = z1 + z2 + z3,
где z1, z2, z3 – числа ступеней скорости составляющих структур. Как правило, составляющие структуры имеют общую часть, число ступеней скорости которой z0. Пусть z1 = z0 и z2 =
= z0· zд , тогда z = z0 (1 + zд).
Общая часть структуры z0 используется для получения всех скоростей и называется основной, структуру zд называют дополнительной. Для объединения составляющих структур в одну сложенную в привод вводят соединительные передачи. Наиболее распространенные схемы соединения двух структур представлены на рис. 77. Верхнюю область регулирования частот вращения шпинделя получают при помощи основной струк-
131
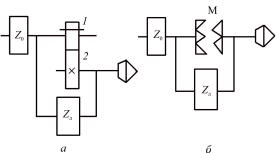
туры z0 и передают движение на шпиндель через зубчатую передачу 1–2 (рис. 77, а) или через муфту М (рис. 77, б). Нижнюю область регулирования обеспечивают последовательным соединением основной z0 и дополнительной zд структур соединительной передачей.
Рис. 77. Схемы соединения структур
На рис. 78 показана кинематическая схема коробки скоростей со сложенной структурой, на рис. 79 – ее структурная сетка и график частот вращения.
Группы колес рa и рb образуют основную структуру z0 = = рa · рb. Они сообщают вращение полому валу III.
Дальнейшая передача движения шпинделю осуществляется либо с помощью муфты, либо через перебор.
Общее число ступеней скорости:
z = рa · рb (1 + рс · рd).
В нашем примере рa = 3; рb = 2, рс =1; рd =1, поэтому z = 3 ·2·(1 + 1 ·1) = 12.
Сложенные структуры обладают рядом достоинств: обеспечивают большое число ступеней скорости при широком диапазоне регулирования; высокие скорости вращения передаются короткими кинематическими цепями, что уменьшает потери мощности и повышает КПД. Количество вариантов сложенных структур может быть очень большим.
132
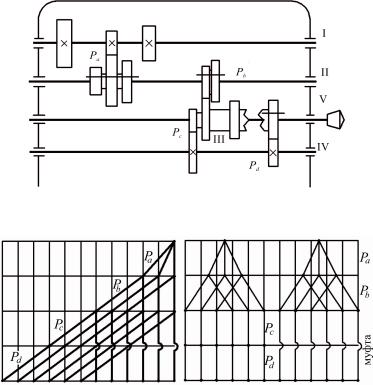
Рис. 78. Кинематическая схема коробки со сложенной структурой
Рис. 79. Структурная сетка и график частот вращения для сложенной коробки скоростей
В общем случае оптимальным является вариант, который при заданном числе ступеней скорости имеет большее число скоростей, получаемых по короткой кинематической цепи; наименьшее количество деталей (зубчатых колес, валов, муфт); меньшие диапазоны регулирования групп передач. Для винторезных станков оптимальным является вариант, при котором большее число скоростей получается по длинной кинематической цепи (через перебор), так как в этом случае расширяются возможности нарезания резьб с увеличенным шагом.
133
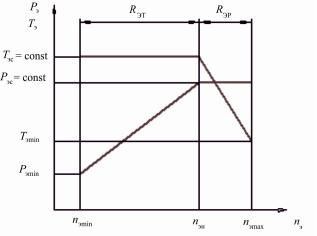
Приводы с бесступенчатым регулированием
Бесступенчатое регулирование в силу ряда преимуществ (повышенная производительность вследствие максимального использования режущей способности инструментов, возможность плавного изменения скорости на ходу станка, удобство дистанционного управления) широко применяется в современных металлорежущих станках, особенно в станках с ЧПУ. Для этой цели применяют регулируемые электродвигатели, иногда фрикционные вариаторы (в станках, еще находящихся в эксплуатации).
В качестве двигателей главного привода применяют электродвигатели постоянного тока с тиристорными системами управления и асинхронные двигатели с преобразователями частоты. Использование преобразователей частоты (инверторов) в настоящее время развивается опережающими темпами. Изменение момента М и мощности N на валу электродвигателя в процессе его регулирования показано на рис. 80.
Рис. 80. Зависимость момента и мощности на валу электродвигателя от частоты его вращения
134
Как видно из графика, при вращении вала регулируемого электродвигателя обеспечиваются два диапазона регулирования: диапазон регулирования с постоянным моментом RМ и диапазон регулирования с постоянной мощностью RN. Первый характеризуется постоянством крутящего момента в диапазоне частот вращения электродвигателя от nmin до nном, второй – постоянст-
вом мощности в диапазоне частот вращения от nном до nmax. Под номинальной частотой вращения электродвигателя nном понима-
ется частота, от которой его можно регулировать без снижения мощности.
Регулирование электродвигателя с постоянным моментом осуществляется в значительном диапазоне, а диапазон регулирования с постоянной мощностью невелик и составляет RN = = 2…12. Такой диапазон не обеспечивает требуемого диапазона частот вращения шпинделя станка R = 100…250. Поэтому применяют комбинированные приводы, в которых вместе с регулируемыми электродвигателями используется простая (переборная) коробка скоростей на 2–4 ступени, которая расширяет диапазон частот вращения шпинделя при постоянной мощности, а также общий диапазон регулирования [2, 4, 6]. При этом изменение частоты вращения шпинделя с постоянным моментом осуществляется на нижней ступени коробки скоростей за счет соответствующего диапазона электродвигателя RМ.
Общий диапазон регулирования привода
R = Rб · Rст = Rб · φz–1,
где z – число скоростей коробки; φ – знаменатель геометрического ряда, обеспечиваемого коробкой скоростей.
Для компенсации скольжения электродвигателя и проскальзывания фрикционной передачи необходимо обеспечить перекрытие частот вращения при переключениях коробки. С этой целью принимают φ = (0,92…0,96)Rб.
При проектировании привода с вариатором возможны два случая:
135
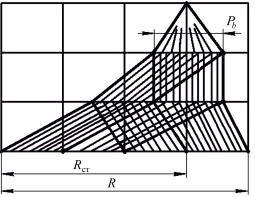
1.Задаются общим диапазоном регулирования привода и диапазоном регулирования бесступенчатого устройства при постоянной мощности и определяют знаменатель ряда частот вращения коробки скоростей и число ее ступеней.
2.При известных общем диапазоне регулирования и числе ступеней скорости определяют диапазон регулирования бесступенчатого устройства и знаменатель ряда частот вращения ведомого вала коробки.
Рис. 81. График частот вращения привода с бесступенчатым регулированием
Кинематический расчет ступенчатой коробки скоростей выполняют так же, как обычной множительной структуры; отличие состоит лишь в том, что знаменатель геометрического ряда частот вращения имеет увеличенное (нестандартное) значение. Пример оформления графика частот вращения при бесступенчатом регулировании показан на рис. 81.
136
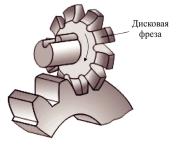
Лекция 11. СТАНКИ СО СЛОЖНОЙ КИНЕМАТИКОЙ
Методы зубонарезания
Метод копирования
Заключается в том, что режущему инструменту придают форму межзубовой впадины нарезаемого колеса и последовательно прорезают все впадины.
В качестве инструмента применяют дисковые модульные фрезы (рис. 82) для мелких и средних модулей и пальцевые фрезы для средних и крупных модулей.
Рис. 82. Фрезерование зубьев цилиндрического колеса дисковой модульной фрезой
Достоинство метода заключается в том, что не требуются специальные станки. Нарезание зубьев можно выполнить на обычных фрезерных станках, применяя делительные головки.
Недостатки метода:
1)низкая производительность, так как после каждой впадины процесс обработки нужно прерывать для выполнения деления;
2)невысокая точность – это связано не с погрешностями наладки и настройки станка, а с конструкцией модульных фрез.
137
Крутизна эвольвенты зависит от диаметра основной окружности колеса d0,
d0 =m z cos(α) ,
где α – угол зацепления.
На практике встречаются разные сочетания названных параметров, а иметь специальную фрезу для каждого случая не представляется возможным.
Для практического применения используют наборы, состоящие из 8 или 15 модульных фрез. Каждая фреза предназначена для нарезания определенного интервала чисел зубьев и имеет профиль, соответствующий наименьшему числу нарезаемых зубьев.
Метод обката
Заключается в том, что помимо главного движения и подачи инструменту и заготовке сообщаются взаимосвязанные движения, имеющие место при работе какой-либо зубчатой передачи. Иначе говоря, на станках, работающих по методу обката, воспроизводится зацепление передачи.
Для этого необходимы специализированные станки, которые достаточно универсальны и применяются в серийном и мелкосерийном производстве. Они отличаются высокой производительностью, так как процесс резания непрерывный, в большинстве случаев объединен с процессом деления. На этих станках достигается высокая точность.
Классификация зубообрабатывающих станков
I. По методам нарезания
1. Станки, работающие по методу копирования, используемые в массовом производстве для нарезания мелкомодульных колес. Они представляют собой многошпиндельные автоматические шпиндельные головки. При этом исключены погрешности профиля, так как применяют специальные модульные фрезы. Другие станки, работающие по этому методу,
138
используют инструмент сложной конструкции (многорезцовые
идолбежные головки).
2.Станки, работающие по методу обката. Они более универсальны, применяются в серийном и мелкосерийном производстве.
II. Станки, работающие по методу обката, различаются в зависимости от применяемого инструмента:
1.Зубодолбежные станки. Инструмент – зуборезный долбяк дискового или чашечного типа. По производительности они уступают зубофрезерным станкам, так как значительная часть времени теряется на холостой ход долбяка. Однако эти станки очень удобны при обработке многовенцовых блоков, так как долбяк требует меньше места для выхода, чем фреза. На этих станках можно нарезать колеса внутреннего зацепления и шевронные.
2.Зубофрезерные станки. На них имитируется червячное зацепление, инструментом является червячная модульная фреза. Они имеют более высокую производительность, чем зубодолбежные станки. На них легче обрабатывать колеса с винтовым зубом, так как одна и та же фреза позволяет нарезать шестерни с разными углами наклона зубьев. На зубодолбежном станке для каждого угла β необходим специальный долбяк и накладные винтовые направляющие для штосселя.
3.Станки для обработки конических колес. На них вос-
производится зацепление конической пары. Инструментом служат зубострогальные резцы при обработке прямозубых колес либо резцовые головки при обработке колес с круговым зубом.
III. Станки для отделочной обработки колес
1.Для обработки колес из сырых материалов применя-
ются:
1) зубообкатные станки (рис. 83). Эталонное колесо прижимают к обрабатываемому, последнее подтормаживается. Обработка заключается в пластичном деформировании тонких по-
139
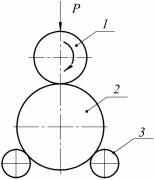
верхностных слоев зубьев. При этом уменьшается шероховатость поверхности и улучшается их износостойкость;
Рис. 83. Схема работы зубообкатного станка:
1 – эталонное колесо (инструмент), которое закалено до высокой твердости и имеет высокую точность; 2 – обрабатываемое колесо; 3 – поддерживающие колеса
2) зубошевинговальные станки. Инструментом служит шевер, представляющий собой закаленное эталонное колесо. На боковых поверхностях зубьев шевера прорезаны канавки для образования режущих кромок. Для прямозубых колес применяют косозубые шеверы, и наоборот. Режущие кромки шевера оказывают скоблящие действия и срезают микронеровности поверхности. Шевер получает вращение и прижимается к заготовке. Они осуществляют осциллирующие движения вдоль своих осей.
2. Для обработки закаленных колес.
Для чистовой обработки закаленных колес служат зубошлифовальные станки для получения более правильной формы зуба и снижения шероховатости его поверхности (рис. 84):
1) станки, работающие по методу копирования. На этих станках обеспечивается высокая производительность благодаря большой линии контакта круга с заготовкой. Однако имеют ме-
140