
Свариваемость материалов
..pdfДиаметр проволок сплошного сечения при сварке в углекис лом газе и смесях газов выбирают в зависимости от толщины свариваемого металла и пространственного положения шва. Проволоками диаметром 1,0—1,4 мм сваривают соединения толщиной 3—8 мм, швы в различных пространственных поло жениях, а также корневые слои многослойных соединений.
Востальных случаях используют проволоку диаметром 1,6 мм. Рекомендуемые режимы полуавтоматической сварки про
волокой сплошного |
сечения |
приведены |
в |
табл. |
10.14. |
|
|
||||||||||
С варку |
в |
см еся х |
на |
основе |
аргона |
вы полняют |
проволокой |
||||||||||
марки С в-08Х Н 2ГМ Ю , при |
этом |
|
практически |
отсутствует р а з |
|||||||||||||
бры згивание, |
швы |
имею т |
хорош ий |
внеш ний |
|
вид. Реж им ы |
|||||||||||
сварки плавящ имся |
электродом |
|
в см еси |
78,0 % |
Аг + 22 |
% С 0 2 |
|||||||||||
приведены |
в табл . 10.15. |
|
|
|
|
|
|
|
|
|
|
|
|
||||
|
|
|
|
|
|
|
|
|
|
|
|
|
|
|
ТАБЛИЦА |
10.14 |
|
РЕЖИМЫ МЕХАНИЗИРОВАННОЙ СВАРКИ В УГЛЕКИСЛОМ |
|
|
|||||||||||||||
ГАЗЕ ПРОВОЛОКОЙ СПЛОШНОГО СЕЧЕНИЯ (РАСХОД ГАЗА |
|
|
|||||||||||||||
|
|
|
|
|
|
8 -1 2 Л/МИН) |
|
|
|
|
|
|
|
|
|||
|
|
|
|
|
|
Пространственное положение |
|
|
|
|
|||||||
Диаметр |
|
|
нижнее |
|
вертикальное |
|
|
потолочное |
|
||||||||
сварочной |
|
|
|
|
|
|
|||||||||||
проволоки, |
|
|
|
|
|
|
|
|
|
|
|
|
|
|
|
|
|
мм |
|
/, А |
|
и, |
В |
I, |
А |
|
и, |
В |
|
I, |
А |
и, |
В |
||
|
|
|
|
|
|||||||||||||
1.0 |
150— |
190 |
|
22— |
23 |
150— |
200 |
21— |
22 |
145— |
165 |
21— |
23 |
||||
1.2 |
150— |
200 |
|
22— |
24 |
150— |
200 |
22— |
24 |
150— |
170 |
22— |
23 |
||||
1.6 |
200— 350 |
|
26— 30 |
200— 240 |
26— 28 |
|
— |
— |
|||||||||
|
|
|
|
|
|
|
|
|
|
|
|
|
|
|
ТАБЛИЦА |
10.15 |
|
РЕЖИМЫ СВАРКИ ВЫСОКОПРОЧНЫХ СТАЛЕЙ В СМЕСИ |
|
|
|||||||||||||||
|
|
|
|
|
78,0 % |
Аг + |
22 % СО, |
|
|
|
|
|
|
|
|||
Диаметр сварочной |
|
/, |
А |
|
и, в |
Вылет |
|
|
Расход газа, |
|
|||||||
проволоки, |
|
|
|
электрода, |
|
|
л/м |
|
|
||||||||
мм |
|
|
|
|
|
|
|
|
|
|
мм |
|
|
|
|
|
|
1,0 |
|
|
150— |
200 |
|
24— |
26 |
10— |
13 |
|
|
12— |
15 |
|
|||
1,2 |
|
|
180— |
280 |
|
25— |
27 |
12— |
15 |
|
|
14— |
16 |
|
|||
1,4 |
|
|
220— |
350 |
|
25— |
28 |
15— |
18 |
|
|
15— |
18 |
|
|||
1,6 |
|
|
280— 400 |
|
2 6 - 2 9 |
18— |
20 |
|
|
16— 20 |
|
Сварку под флюсом марок АН-17М или АН-43 выполняют на постоянном токе обратной полярности. Сила сварочного тока не превышает 800 А, напряжение дуги до 40 В, скорость сварки изменяют в диапазоне 13—30 м/ч. Одностороннюю однопроход ную сварку применяют для соединений толщиной до 8 мм и выполняют на остающейся стальной подкладке или флюсовой подушке. Подкладные планки изготавливают из малоуглеро дистой стали толщиной 3—6 мм и шириной 40—50 мм.
Максимальная толщина соединений без разделки кромок, свариваемых двусторонними швами, не должна превышать 20 мм. Для стыковых соединений без скоса кромок (односто ронних и двусторонних) используют проволоку марки Св-08ХН2М (ГОСТ 2246—70). Применять более легированные проволоки для таких соединений нецелесообразно, поскольку в этом случае механические свойства швов имеют излишне вы сокую прочность.
Наиболее часто стыковые соединения подготавливают со скосом кромок. Сварку корневых швов стыковых соединений высокопрочных сталей с V- или Х-образной разделкой кромок обычно выполняют проволоками марок Св-08ГА или Св-10Г2 (ГОСТ 2246—70). Заполнение разделок кромок осуществля ется проволоками марок Св-08ХН2ГМЮ или Св-08ХН2ГСМЮ (ГОСТ 2246—70) последовательным наложением слоев. Первые два-три слоя выполняют по оси разделки, а все последующие — со смещениями последовательно то к одной, то к другой сто роне разделки.
10.3.5. Электрошлаковая сварка
При электрошлаковой сварке низкоуглеродистых легированных сталей применяют технологические приемы, позволяющие по высить скорость охлаждения сварного соединения, например сопутствующее дополнительное охлаждение зоны сварки. При этом ниже ползуна устанавливается специальное душирующее устройство — спреер, которое, перемещаясь со скоростью сварки, охлаждает водой шов и зону термического влияния. Скорость охлаждения металла околошовного участка зоны термического влияния удается повысить до шв/5 = 3,5-т-4,0 °С/с, что обеспечивает получение требуемых структуры и показате лей механических свойств этого участка сварного соединения [12] (табл. 10.16).
Сварные |
соединения, |
выполненные |
с дополнительны м о х |
лаж дением , |
о бл адаю т |
достаточной |
хладостойкостью (табл . |
10.17).
МЕХАНИЧЕСКИЕ СВОЙСТВА МЕТАЛЛА ШВОВ ПРИ ТАБЛИЦА 10.16 ЭЛЕКТРОШЛАКОВОЙ СВАРКЕ
Сварочная проволока |
*0,2. МПа |
oBt МПа |
*6. * |
% |
Cff-IOHMA |
771 |
852 |
16,0 |
58,3 |
Св-10ХГ2СМА |
825 |
929 |
19,3 |
65,1 |
|
|
|
ТАБЛИЦА 10.17 |
||
УДАРНАЯ ВЯЗКОСТЬ KCU СВАРНОГО СОЕДИНЕНИЯ СТАЛИ |
|||||
12ГН2МФАЮ ТОЛЩИНОЙ 40 ММ (Дж/см*). |
|
||||
|
|
|
Т, °С |
|
|
Место вырезки образцов |
+20 |
-40 |
-70 |
||
|
|
||||
Шов |
|
86— 109 |
55—85 |
34—87 |
|
ЗТВ: |
|
94 |
69 |
69 |
|
|
|
|
|
||
надрез на границе |
сплавления; |
82—93 |
55—77 |
20—47 |
|
88 |
66 |
31 |
|||
|
|
||||
на расстоянии 1 мм |
от границы |
95—126 |
6 5 -7 7 |
27—50 |
|
сплавления, |
|
107 |
72 |
35 |
|
2,5 мм |
|
90— 105 |
50—80 |
47—67 |
|
|
100 |
68 |
59 |
||
|
|
||||
5 мм |
|
95—103 |
98—107 |
72—85 |
|
|
100 |
100 |
76 |
||
|
|
||||
10 мм |
|
100—100 |
95—110 |
98—110 |
|
|
103 |
100 |
100 |
||
|
|
||||
Основной металл |
|
90—120 |
103— 115 |
77—82 |
|
|
109 |
107 |
80 |
||
|
|
Г л а в а 11. СРЕДНЕЛЕГИРОВАННЫЕ
МАРТЕНСИТНО-БЕЙНИТНЫЕ СТАЛИ (Мусияченко В. Ф., Саржевский В.' А.)
11.1. Состав и свойства сталей
Среднелегированные мартенситно-бейнитные стали содержат С в количе стве до 0,4 % и более. Они легированы Ni, Сг, W, Mo, V. Оптимальное сочетание прочности, пластичности и вязкости стали получают после за
калки и низкого отпуска.
Указанные стали с целью повышения пластичности и вязкости выплав ляют из чистых шихтовых материалов, а также тщательно очищают в про-
цессе производства of газов и неметаллических включений, в ряде случаев подвигая № вакуумно-дуговому, электрошлаковому переплавам, рафинирований в к00Ше жидкими синтетическими шлаками. Термомехани ческая обработка rfM °) позволяет достичь на среднеуглеродистых сталях хорошего сочетания ррочности>пластичности и вязкости.
Типичными поедст*вителями сРеднеУглеР°Дистых мартенситно-бейнитных
сталей, |
широк0 приМеНЯемыми ПРИ изготовлении |
ответственных |
сварных |
||
, |
— r |
|
|
|
|
конструкций, |
явля1°гСЯ стали |
42Х2ГСНМА у |
979—6 3 ) . |
||
|
|
|
|
ЦНИЧМ |
\ |
40ХГСНЗМА |
(ЧМТУ 5309-57), |
30Х2ГСНВМА |
/ ЧМТУ |
||
979—63^ |
а также 30XTQHA, 3ОХГСА, 25ХГСА, 12Х2НЧА (все ГОСТ 4543 71) и не которые другие, имек>“1Ие пРедел прочности 1050—2000 МПа (табл. 11.1).
11.2.Свариваемости сталей
Вряде случаев среднеуглеродистые мартенситно-бейнитные стали применяют в конструкциях в термически упрочненном со стоянии. В этом случае необходимо получить искомый комп лекс свойств без термообработки сварных соединений.
Аустенитизация является ведущим процессом в формирова нии свойств участков зоны термического влияния в широком
диапазоне температурПоэтому целесообразно разделить зону термического влияния по принципу полноты и характера аусте нитизации на три температурные области. Температурный ин тервал этих областей зависит от многих факторов и определя ется особенностями как технологического процесса сварки, так и свойствами основного металла.
Условно первукз из них можно определить как область пере гретого аустенита, характеризующуюся наличием крупного зерна и высокотемпературной химической микронеоднородно сти (ВХМН), вторую— аустенита с оптимальной величиной зерна и высокими свойствами, третью — неполной аустенитиза ции и высокого отпуска.
11.2.1.Фазовые и структурные превращения при сварке
Висследованиях большое внимание уделяется участкам пере грева и высокого отпуска, так как их свойствами часто оп ределяется работоспособность сварных соединений этих ста лей. Высокотемпературная химическая микронеоднородность (ВХМН) образуется главным образом в результате раннего оплавления отдельных микрообъемов металла околошовной
зоны у линии сплавления, включающих легкоплавкие неметал лические включения сульфидного происхождения и другие сегрегаты. Она формируется при всех способах сварки плавле нием. При этом образуется характерная зернистая структура. Границы подплавленных зерен ориентированы по участкам за-
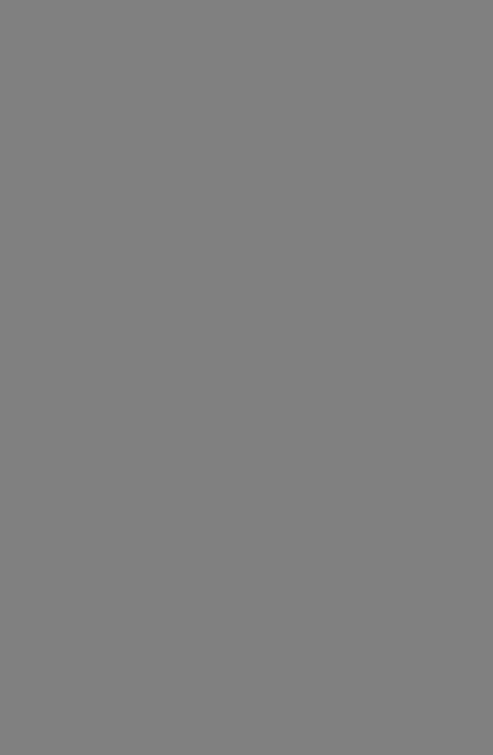
ИССЛЕДУЕМЫХ СРЕДНЕУГЛЕРОДИСТЫХ МАРТЕНСИТО-
ЗАКАЛКИ И НИЗКОГО ОТПУСКА |
|
|
|
|||||
состав, % |
|
|
|
|
|
Механические свойства |
|
|
Мо |
S |
Р |
or |
в |
, МПа |
|
6fi, % |
К С U °С* |
|
|
|
||||||
не более |
|
|
мй& |
О |
Дж/сма |
|||
|
|
|
|
|
||||
0,4—0,6 |
0,010 |
0,02 |
2000±10° |
1700±5° |
6—7 |
50 |
||
0,3—0,4 |
0,025 |
0,025 |
2000*100 |
1500 |
8 |
70 |
||
0,4—0,5 |
0,011 |
0,015 |
1700±10° |
1360 |
7 |
70 |
||
— |
0,015 |
0,025 |
1700 |
1450 |
10 |
70 |
||
__ |
0,030 |
0,03 |
1600 |
1400 |
6 |
50 |
||
— |
0,030 |
0,03 |
1400 |
1300 |
6 |
50 |
||
|
0,030 |
0,03 |
1050 |
820 |
13 |
100 |
неоднородности в имитированных образцах и у линии сплав ления сварных соединений примерно такая же, как и в металле шва аналогичного химического состава.
Микрорентгеноспектральный анализ образцов, нагретых по термическому циклу участка ВХМН, показывает (табл. 11.3), что сегрегация легирующих элементов на первичной границе сохраняется даже после длительных выдержек при 1200 аС. Высокотемпературная химическая микронеоднородность, разви вающаяся в участке подплавления околошовной зоны под воз действием сварочного термодеформационного цикла и сохра няющаяся после термической обработки, изменяет кинетику
ТАБЛИЦА п.2
ВЫСОКОТЕМПЕРАТУРНАЯ ХИМИЧЕСКАЯ МИКРОНЕОДНОРОДНОСТЬ В ОБРАЗЦАХ СРЕДНЕУГЛЕРОДИСТЫХ МАРТЕНСИТО-
БЕЙНИТНЫХ СТАЛЕЙ
|
|
Si |
|
|
Сг |
|
|
Мп |
|
Марка стали |
|
|
|
|
|
|
|
|
|
|
<т |
сз |
V C3 |
<т |
сз |
ег/ез |
<т |
сз |
сг/сз |
42Х2ГСНМА |
0,56 |
0,42 |
1,33 |
2,72 |
2,02 |
1,34 |
1,08 |
0,79 |
1,37 |
40Х2ГСНМ (шов) |
1,03 |
0,70 |
1,47 |
3,0 |
1,96 |
1,53 |
1.41 |
0,95 |
1,49 |
ЗОХГСНА |
1,15 |
0,70 |
1,64 |
2,63 |
1,23 |
2,12 |
1,75 |
1,25 |
1,40 |
40ХЗГСНМФ |
0,75 |
0,7 |
1,07 |
5,0 |
3,82 |
1,30 |
1.1 |
0,85 |
1,29 |
40ХЗГСНМФ (шов) |
0,58 |
0,4 |
1,45 |
4,55 |
3,14 |
1,45 |
1,1 |
0,77 |
1,43 |
30Х2Н2М |
0,66 |
0,45 |
1,46 |
4,20 |
2,50 |
1,68 |
0,53 |
0,49 |
1,08 |
28ХЗСНМВФА (шов) |
1,05 |
0,76 |
1,38 |
2,44 |
1,76 |
1,39 |
1,01 |
0,69 |
1,46 |
28ХЗСНМВФА |
0,93 |
0,73 |
1,27 |
2,40 |
1,85 |
1,30 |
1,01 |
0,84 |
1,20 |
Марка стали |
|
N1 |
|
|
|
Мо |
|
|
|
|
|
|
|
|
|
||
|
|
гг |
*3 |
|
Сг/С3 |
<т |
*3 |
V C3 |
42Х2ГСНМА |
0,58 |
0,46 |
|
1,26 |
0,69 |
0,24 |
2,88 |
|
40Х2ГСНМ (шов) |
М |
0,98 |
|
1,12 |
1,51 |
0,64 |
2,36 |
|
ЗОХГСНА |
1,58 |
1,25 |
|
1,26 |
— |
— |
— |
|
40ХЗГСНМФ* |
0,7 |
0,7 |
|
1,0 |
1,8 |
0,8 |
2,25 |
|
40ХЗГСНМФ (шов) |
0,78 |
0,71 |
|
1,1 |
0,95 |
о;43 |
2,21 |
|
30Х2Н2М |
1,76 |
1,53 |
|
1,16 |
— |
— |
— |
|
28ХЗСНМВФА (шов) |
0,41 |
0,38 |
|
1,08 |
0,96 |
0,52 |
1,85 |
|
28ХЗСНМВФА |
0,39 |
0,37 |
|
1,06 |
0,93 |
0,62 |
1,50 |
|
* Сг = 1,2; С3 = 0,65; |
сг/с3 = |
1,85-W |
|
|
|
|
|
|
П р и м е ч а н и е . |
— концентрация |
на границе, |
вес %; с3 |
— концентрация в |
||||
зерне, % (по массе). |
|
|
|
|
|
|
|
|
|
|
|
|
|
|
|
ТАБЛИЦА 1J.3 |
|
ВЛИЯНИЕ ТЕРМИЧЕСКОЙ ОБРАБОТКИ НА ВЫСОКОТЕМПЕРАТУРНУЮ |
||||||||
ХИМИЧЕСКУЮ МИКРОНЕОДНОРОДНОСТЬ В ОБРАЗЦАХ СТАЛИ |
|
|||||||
|
|
|
30Х2Н2М |
|
|
|
|
|
|
|
|
|
Si |
|
Сг |
|
|
Режим термообработки |
|
|
|
|
|
|
||
|
|
|
*Г |
сз |
сг/сз |
<т |
гз |
сг/сз |
Нагрев по термическому циклу |
0,30 |
0,15 |
2,0 |
4,2 |
2,5 |
1,68 |
||
участка ВХМН |
|
|
0,2 |
|
|
|
|
|
Термообработка по режиму для |
0,34 |
1,7 |
4,1 |
2,2 |
1,86 |
|||
основного металла после на |
|
|
|
|
|
|
||
грева по циклу |
|
|
0,2 |
|
|
|
|
|
Двойная |
термообработка после |
0,35 |
1,75 |
3,7 |
2,26 |
1,63 |
||
нагрева |
по циклу |
|
0,66 |
|
|
|
|
|
Нагрев по термическому циклу |
0,45 |
1,46 |
4,2 |
2,5 |
1,68 |
|||
участка ВХМН |
|
|
|
|
|
2,6 |
|
|
1200 °С, |
6 ч после нагрева по |
0,55 |
0,38 |
1,45 |
4,0 |
1,54 |
||
циклу |
|
|
|
|
|
|
|
|
|
|
|
|
|
Мп |
|
|
Ni |
|
Режим термообработки |
|
|
|
|
|
|
|
||
|
|
|
|
сг |
сз |
V C3 |
сг |
сз |
сг'сз |
Нагрев по термическому циклу |
0,65 |
0,48 |
1,35 |
2,0 |
1,6 |
1,25 |
|||
участка ВХМН |
|
|
|
|
|
|
|
|
|
Термообработка по режиму для |
0,6 |
0,46 |
1,3 |
2.0 |
1,65 |
1,21 |
|||
основного |
металла |
после |
на |
|
|
|
|
|
|
грева по циклу |
|
|
|
|
|
|
|
|
|
Двойная термообработка после |
0,65 |
0,4 |
1,62 |
1,75 |
1,42 |
1,23 |
|||
нагрева по |
циклу |
|
|
|
|
|
|
|
|
Нагрев по термическому циклу |
0,53 |
0,49 |
1,08 |
1,76 |
1,53 |
1,16 |
|||
участка ВХМН |
|
|
|
|
|
|
|
|
|
1200 °С, 6 |
ч после нагрева |
по |
0,5 |
0,5 |
1,0 |
1,67 |
1,34 |
1,25 |
|
циклу |
|
|
|
|
|
|
|
|
|
П р и м е ч а н и е . |
с3 — концентрация |
в зерне |
% (по |
массе); сг — концентрация |
|||||
на границе |
%. |
|
|
|
|
|
|
|
|
ТАБЛИЦА 11.4
КИНЕТИКА ПРЕВРАЩЕНИЯ АУСТЕНИТА ПРИ СВАРОЧНОМ ТЕРМИЧЕСКОМ ЦИКЛЕ*
|
|
Степень превраще |
||||
|
|
|
ния аустенита |
|
||
|
|
(%) в температурных |
||||
|
|
|
интервалах |
|
||
Образец |
О |
|
|
| |
||
°С |
°С |
эжин |
||||
|
|
о |
||||
|
|
300—250 |
250—200 |
ЭоООЗи |
||
|
|
Е |
||||
|
|
чX |
|
|
|
|
|
|
со |
|
|
|
|
С подплавлением, |
62 |
27 |
8 |
3 |
||
^шах ^ |
1430 °С |
75 |
19 |
6 |
0 |
|
Без |
подплавле |
|||||
ния |
|
|
|
|
|
|
Тгпах = |
1280 °С |
|
|
|
|
* Скорость нагрева 150 °С/с, скорость охлаждения в интервале 800—500 °С 8° С/с
ТАБЛИЦА 11.5
СТЕПЕНЬ ПРЕВРАЩЕНИЯ АУСТЕ НИТА ПРИ ПОВТОРНОМ ПЕЧНОМ НАГРЕВЕ И ОХЛАЖДЕНИИ*
|
|
Степень превраще |
|||
|
|
ния аустенита |
|
||
|
|
(96) в температурных |
|||
|
|
|
интервалах |
ниже |
|
|
|
S |
°С |
°С |
|
|
Образец |
и |
|
|
|
|
о |
|
|
|
|
|
|
лX |
400—300 |
300—200 |
200°Си |
|
|
Ьм |
|||
|
|
а |
|
|
|
|
|
В |
|
|
|
С подплавлением |
3 |
45 |
48 |
4 |
|
Без |
подплавле |
8 |
62 |
29 |
1 |
ния |
|
|
|
|
|
* Нагрев до 950 °С выдержка 10 мин, скорость охлаждения в интервале 800— 500 °С 1,5 °С/с.
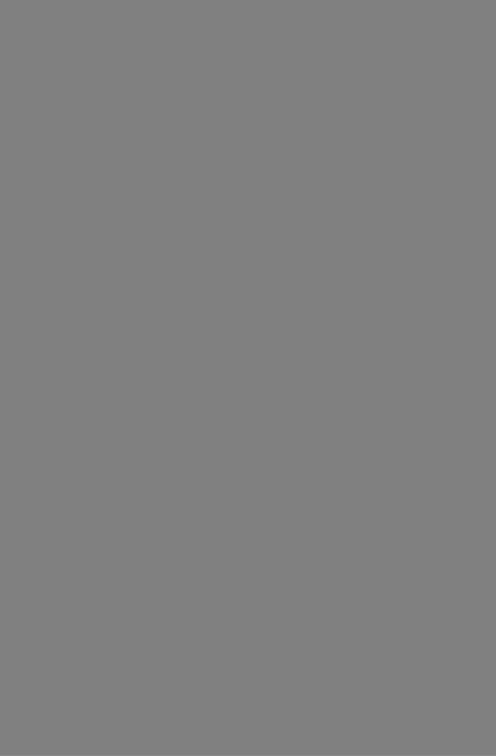
щин — основного дефекта при сварке этих сталей — связыва ется с формированием ВХМН у линии сплавления и последую щим превращением аустенита в околошовной зоне, характером и величиной сварочных напряжений, распределением водорода в процессе сварки [1—3]. Причем значение фактора ВХМН уве личивается с повышением легирования стали и содержания
вней С.
Всварных конструкциях зародыш трещины может образо ваться вследствие отставания пластической деформации от
фронта |
нарастающих |
напряжений. Именно |
в |
участке |
ВХМН |
||||||||
б, МПа |
|
|
|
|
а |
|
|
|
|
|
|
|
|
250 |
|
|
1? |
|
|
|
|
|
|
|
|
||
|
|
|
|
|
|
|
|
|
|
|
|||
150 |
|
/ |
|
|
|
|
|
|
|
|
|
||
|
|
|
|
|
|
|
|
|
|
|
|
||
|
_ |
|
/ |
|
|
|
|
|
|
|
|
|
|
50 |
|
|
----------------------------- — |
|
|
|
|
|
|
|
|||
|
|
|
|
|
|
|
|
|
|
|
|
||
250 |
|
|
|
|
|
|
|
|
|
|
|
|
|
150 |
- t u |
|
|
|
|
|
|
|
|
|
|
||
50 |
|
|
|
|
|
|
|
|
|
|
|||
* |
8 12 |
16 |
20 24 т,ч |
0 |
4 |
8 |
12 |
16 |
20 |
24 Г,ч |
|||
О |
|||||||||||||
Рис. П.2. |
Кривые замедленного |
разрушения |
Рис. |
П.З. Кривые замедленного раз- |
|||||||||
|
соединений сталей: |
|
рушения |
соединений стали |
35X3H3M: |
||||||||
а —30Х2Н2М; б — 42Х2ГСНМА; |
/ — после |
/ — с |
наплавкой кромок; |
2 —без на- |
|||||||||
электрошлакового |
переплава; |
3 — после элек- |
|
|
|
плавки |
|
|
|||||
тронно-лучевого |
переплава,; |
2, |
4 — переплав |
|
|
|
|
|
|
|
|||
|
не |
производился |
|
|
|
|
|
|
|
|
создаются наиболее благоприятные условия для слияния микронесплошностей в дефект критических линейных размеров. Этот дефект затем развивается в надрыв — горячую трещину, способную перерасти в холодную в зависимости от вязкости примыкающего участка околошовной зоны, а также напряжен ного состояния.
Трещины, зародившиеся на первичных границах участка ВХМН околошовной зоны, встречаются в сварных соединениях конструкций из сталей 40ХГСНЗМА и ЗОХГСНА, выполненных электронно-лучевой и многослойной дуговой сваркой под флю сом. При этом они вероятнее в верхней части шва, где участок неоднородности шире и превышает 0,2 мм [4].
Уменьшение содержания S, газов и неметаллических вклю чений в металле при электронно-лучевом и электрошлаковом переплаве сталей 42Х2ГСНМА и 30Х2Н2М приводит к повы шению его пластичности и особенно ударной вязкости. Так как неметаллические включения приводят к локальным оплавле ниям при температуре ниже Тс, то в рафинированном основ ном металле первая стадия подплавления может смещаться
2И