
Строительство на подрабатываемых и карстоопасных территориях
..pdf5.2.8.Экспериментальные исследования работы армирования грунтового основания
При проектировании армирования грунтовых оснований, как показано в предыдущих параграфах, одной из важнейших является такая характеристика армирующего материала, как прочность на разрыв.
Геосинтетические материалы обладают достаточно большим относительным удлинением на разрыв. При этом нужно учитывать, что зависимость относительного удлинения от растягивающего усилия является нелинейной. Как показали исследования, проведенные на кафедре СПГ ПНИПУ, учет этой зависимости позволяет более рационально подбирать геосинтетические материалы для усиления оснований. Методика, разработанная на кафедре, также использует эту зависимость. Кроме того, для расчетов армированных оснований применяются численные методы, например программа PLAXIS, которым требуется знание жесткости на разрыв геосинтетического материала G (также встречается название нормальная жесткость геосинтетического материала и обозначение EA), которая определяется на один погонный метр ширины материала (кН/м).
Значение жесткости G зависит от относительного удлинения при растягивающих усилиях:
G = EA = F/(∆l/l), |
(31) |
где E – модуль упругости геосинтетического материала; A – площадь поперечного сечения геосинтетического материала; F – растягивающее усилие в геосинтетическом материале; ∆l/l – относительное удлинение геосинтетического материала.
Жесткость G может определяться при разрыве геосинтетического материала и при различном удлинении (обычно от 2 до 5 %), в зависимости от типа материала и конкретного его применения. Как показывают проведенные ранее исследования и анализ графиков зависимости относительного удлинения геосинтетического материала от растягивающего усилия (см. рис. 19), при меньших растягивающих усилиях фактическое значение жесткости G больше, чем при разрывных усилиях. Учет этого позволяет более оптимально подбирать геосинтетические материалы для армирования грунтовых оснований.
Построение графиков завимости жесткости от относительного удлинения проводится по результатам испытаний геосинтетических мате-
91
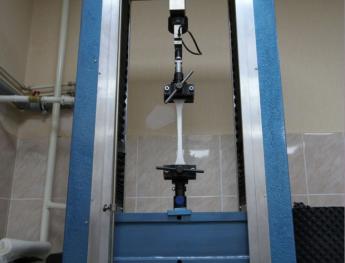
риалов на разрыв в соответствии с ГОСТ 15902.3-79. Испытания проводят на разрывных машинах (рис. 21), обеспечивающих постоянную скорость опускания нижнего зажима, постоянную скорость деформации или постоянную скорость возрастания нагрузки с относительной погрешностью показаний разрывной нагрузки ±1,0 %, абсолютной погрешностью показаний удлинения ±1,0 мм, со средней продолжительностью разрыва, регулируемой от (30±15) до (60±15) с.
На разрывной машине устанавливают расстояние между зажимами
(100 ± 1) мм.
Скорость опускания подвижного зажима разрывной машины устанавливают такой, чтобы средняя продолжительность процесса растяжения элементарной пробы до разрыва соответствовала:
−(30 ±5) с – для нетканых полотен с удлинением менее 100 %;
−(60 ±15) с – для нетканых полотен с удлинением более 100 %. Количество проб испытуемых материалов и их размеры изготавли-
вают в соответствии с нормативными документами.
При разрыве элементарной пробы в зажиме или на расстоянии 5 мм и менее от зажима результат испытания учитывают только в том случае, если его значение не менее минимальной разрывной нагрузки, предусмотренной в нормативно-технической документации на продукцию. В противном случае подвергают разрыву дополнительные элементарные пробы.
Рис. 21. Испытательная разрывная машина МТ-136
92
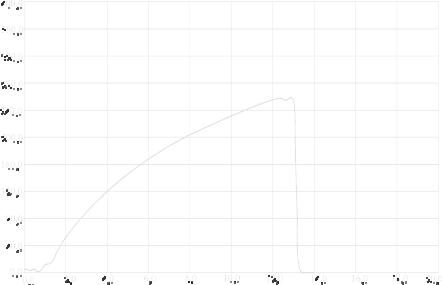
По окончании проведения испытаний снимают кривую «нагрузка – удлинение» (рис. 22), где по оси абсцисс – абсолютное удлинение в мм, по оси ординат – усилие в кгс для полоски материала шириной 50 мм.
После обработки данных испытаний по нескольким образцам (обычно не меньше 10) строится зависимость относительного удлинения геосинтетического материала εп от растягивающего усилия Fa
(см. рис. 19).
Рассмотренные выше методы расчета дают приближенные значения, так как не могут учесть всех особенностей взаимодействия армирующих материалов с грунтами основания. Поэтому для определения применимости методов расчета более достоверно можно судить, только проводя модельные эсперименты, наиболее приближенные к реальным условиям эксплуатации армированного основания, в том числе и при возникновении провалов.
Примером проведения таких модельных экспериментов могут служить исследования, проведенные в Германии с участием российских ученых.
Рис. 22. Диаграмма «нагрузка – удлинение» управляющей программы разрывной машины МТ-136
Задача экспериментов заключалась в моделировании поведения грунтового основания дороги, армированного упрочненным геотекстилем, в случае провала грунтового основания дорожного полотна.
93
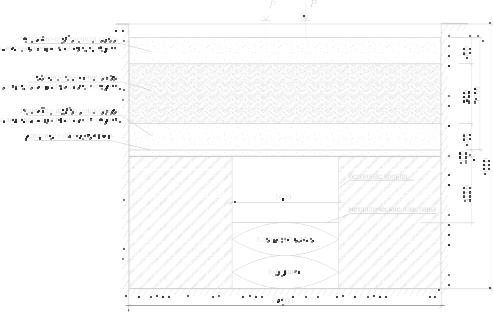
Эксперименты проводились в октябре-ноябре 2004 г. в лаборатории строительного факультета технического университета Анхальт (Hochschule Anhalt) в г. Дессау (Германия) под руководством профессора У. Турчинского (Ulrich Turczynski) и доктора С. Швердта (Sven Schwerdt). В лотке был смоделирован участок дорожного полотна с провалом земли (рис. 23). Исследовалось поведение основания и дорожного полотна автомобильной дороги при однослойном армировании на основе принципа частичной безопасности. Моделировались нагрузка от движения автомобиля со скоростью 60 км/ч и максимальная нагрузка на одно колесо 75 кН. Нагрузки прикладывались до и после образования провала.
Эксперименты проводились в лотке размером 4,7×3×4 (h) м (рис. 24), в котором послойно укладывались три слоя связного грунта (песчано-гравийный и гравийно-щебеночная смесь, оба с включением глинистого грунта) и армирующая прослойка. Геосинтетический материал был уложен в нижнем слое, моделирующем уплотненное основание дорожной одежды, на 0,1 м выше моделируемого провала.
Рис. 23. Принципиальная схема эксперимента
94
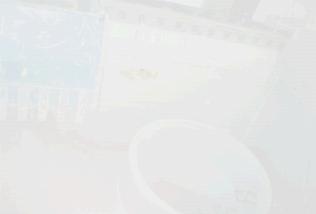
Рис. 24. Вид лотка с установленными бетонными кольцами
Для измерения вертикальных деформаций грунта применялись глубинные марки, установленные на уровне закладки армирующей прослойки. Положение марок до и во время проведения эксперимента фиксировалось с помощью тахеометра относительно базовых точек.
На уровне закладки армирующей прослойки были установлены датчики давления (5 шт.) для определения вертикальных напряжений в грунтовом массиве непосредственно над армирующей прослойкой и тензометры (5 шт.) для определения растягивающих усилий в геотекстиле от действующих нагрузок, моделирующих провал грунта. Показания приборов передавались через специальные блоки на компьютер, где расшифровывались и проходили дальнейшую обработку.
Все использованные датчики, приборы и инструменты предварительно прошли проверку и тарировку в соответствии с действующими немецкими стандартами.
На первом этапе проведения эксперимента прикладывалась статическая нагрузка от двух домкратов (2×75 кН) и фиксировались показания датчиков, приборов и перемещения глубинных марок.
На втором этапе из пневмоподушек стравливался воздух, статическая нагрузка вновь прикладывалась и фиксировались показания приборов. После этого были выполнены эксперименты с нагрузкой от движущегося грузового автомобиля.
Нагрузка от движущегося автомобиля моделировалась с помощью тех же домкратов. Нагрузка прикладывалась домкратами поочередно через промежутки времени, соответствующие прохождению колес автомобиля со скоростью 60 км/ч, максимальная расчетная нагрузка на
95
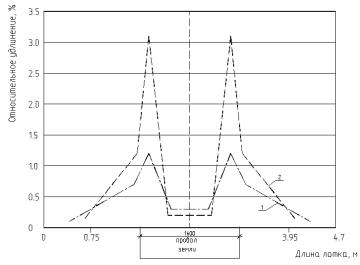
одно колесо 75 кН. Количество циклов динамического нагружения было рассчитано исходя из транспортной нагрузки на автодорогах Германии (федеральных и автобанах). Нагружение проводилось фазами: 10000–20000 циклов, затем перерыв, во время которого к поверхности прикладывалась статическая нагрузка и проводились замеры. Полный цикл экспериментов продолжался почти две недели и был прекращен при достижении осадки поверхности приблизительно 10 см. Всего было проведено около 300 000 циклов нагружения.
После окончания эксперимента были сняты показания приборов и замерено положение глубинных марок. Затем была проведена аккуратная послойная выемка грунта вплоть до армирующего материала.
По результатам проведенных экспериментов были построены графики относительных удлинений (рис. 25) и растягивающих усилий в армирующей прослойке на разных стадиях эксперимента, изменения вертикальных напряжений на контакте геотекстиля и грунта, определены области оседания грунтового массива над армирующей прослойкой и на поверхности.
Рис. 25. Относительные удлинения в геотекстиле после окончания эксперимента: 1 – в продольном направлении; 2 – в поперечном направлении
Проведенный эксперимент был одним из многочисленных, проводимых в Германии и являлся звеном в цепи по накоплению статистики поведения геосинтетических материалов в различных условиях. Это,
96
в свою очередь, позволяет оптимизировать проектирование армированных грунтовых оснований для случаев возникновения провалов под сооружениями на подрабатываемых и карстоопасных территориях.
5.3. Уплотнение грунтовых оснований
При строительстве на подрабатываемых территориях и просадочных грунтах, при наличии в глубине грунтового массива карстовых полостей, в мировой практике часто применяют уплотнение грунтовых оснований.
Методы уплотнения грунтовых оснований подразделяются на поверхностные и глубинные. Поверхностное уплотнение проводят укаткой, трамбованием, вибрационными механизмами, методом вытрамбовывания котлованов, подводными взрывами. Глубинное уплотнение проводят с помощью устройства песчаных и грунтовых свай, глубинного виброуплотнения, уплотнения статической пригрузкой в сочетании
сустройством вертикального дренажа, водопонижением [].
Спрактической точки зрения при наличии в основании здания или сооружения старых горных выработок или карстовых полостей наиболее эффективным является уплотнение грунтового основания тяжелыми трамбовками (динамическое уплотнение). В нашей стране этот метод предложен в 1954 г. Ю.М. Абелевым. За рубежом теоретический подход к динамическому уплотенению разработан в 1971 г. С. Вараксиным. Уплотнение обычно производится свободным сбрасыванием трамбовок весом до 15 т (150 кН) с высоты 5–10 м с помощью крана (рис. 26). В мировой практике использовались трамбовки массой до 900 т, например, при строительстве аэропорта в Ницце (Франция) (рис. 27).
Трамбовка обычно изготавливается из железобетона и имеет в плане обычно форму круга, квадрата или многоугольника. Подошва штампа может быть плоской или конической.
Уплотнение тяжелыми трамбовками производится несколькими ударами по одному следу, пока не наступит отказ, то есть величина осадки при одном ударе одна и та же. Эта величина зависит от вида грунтов. Качественным показателем является достижение грунтом заданной плотности сложения и соответствующих ей характеристик прочности и деформируемости грунта. Эффективность уплотнения грунтов тяжелыми трамбовками определяется размером, весом, высотой сбрасывания трамбовки, степенью плотности, влажностью, структурной прочностью уплотняемых грунтов. Обзор зарубежных публикаций позволяет добавить к оценке эффективности динамического уплот-
97

нения фактор способа сбрасывания трамбовки. Свободное сбрасывание трамбовки (рис. 28) позволяет увеличить эффективноесть ее использования и уменьшает воздействие сбрасывания на подъемное оборудование. За рубежом эту систему называют Free Fall System (FFS).
Рис. 26. Схема поверхностного уплотнения грунта тяжелой трамбовкой: 1 – уплотняемая полоса; 2 – полоса перекрытия; 3 – уплотненная полоса; 4 – место стоянки крана; 5 – ось проходки крана; 6 – трамбовка
Рис. 27. Динамическое уплотнение грунта при строительстве аэропорта в Ницце (Франция)
98
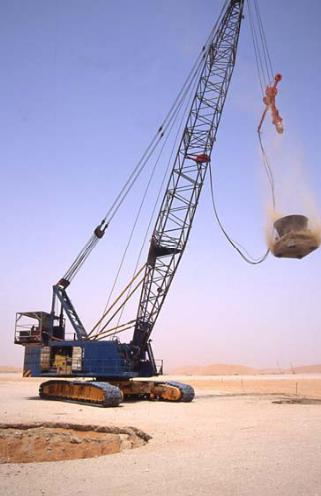
Рис. 28. Свободное сбрасывание трамбовки (FFS)
Более подробно уплотнение грунтов тяжелыми трамбовками слабых грунтов рассматривается в работах М.Ю. Абелева [32] и учебниках по курсу «Основания и фундаменты» [38].
Применение уплотнения грунтового основания тяжелыми трамбовками (динамическое уплотнение) при наличии в грунтовом массиве пустот старых выработок и карстовых полостей связано фактически с разрушением этих пустот и заполнением их грунтом вышележащих слоев.
В качестве примера такого использования динамического уплотнения можно привести работы, проведенные при строительстве автомагистрали (автобана) А71 в Германии. Проведенные перед проектировани-
99
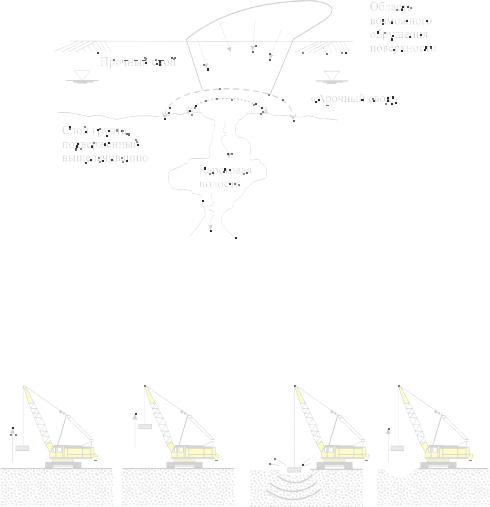
ем дороги изыскания, в том числе с использованием георадара, показали наличие на участке длиной 1,5 км потенциально опасные области возможных провалов, в том числе наличие карстовых пустот (рис. 29).
Рис. 29. Карстовая полость под проектируемой дорогой
В качестве мероприятий по предотвращению провалов поверхности на таких участках дороги заказчиком был выбран метод динамического уплотнения грунта DYNIV®, который практически не отличается от уплотнения грунта тяжелыми трамбовками (рис. 30).
Рис. 30. Динамическое уплотнение грунта DYNIV®
Уплотнение грунта проводилось модифицированным методом DYNIV® с помощью трамбовки массой 35 т, которая свободно сбрасывалась с высоты примерно 30 м (система FFS), так как только при такой технологии проведения работ достигается глубинное уплотнение, приводящее к закрытию карстовых полостей.
100