
- •Т.В. КОСТЫГОВА
- •ТЕХНОЛОГИЯ ПРОИЗВОДСТВА ПРОВОДОВ
- •Костыгова Т.В.
- •1. ПРОИЗВОДСТВО ПРОВОЛОКИ
- •1.1. Металлы, обрабатываемые в кабельной промышленности
- •1.2. Изготовление медной и алюминиевой катанки
- •1.4.3. Прокатные станы
- •1.7. Травление катанки
- •1.8. Скальпирование медной катанки
- •1.10. Оборудование для волочения проволоки
- •1.12. Отжиг медной и алюминиевой проволоки
- •2. ПРОИЗВОДСТВО ОБМОТОЧНЫХ ПРОВОДОВ
- •2.1. Классификация обмоточных проводов
- •3.2.Способы наложения эмалевой изоляции
- •expfciTo)
- •3.3.2. Расчет концентрации растворителя для случая, когда скорость процесса определяется внешним массообменом (Bi < 1)
- •3*5. Условия возникновения газообразных включений на стадии пленкообразования
- •UooJ
- •3.7.1. Агрегаты для эмалирования проволоки диаметром 0,015-0,05 мм
- •3.7.4. Устройство катализаторов
- •3.8. Особенности эмалирования проводов из расплава смол
- •4. ПРОИЗВОДСТВО ОБМОТОЧНЫХ ПРОВОДОВ
- •4.1.1. Обмоточные машины для наложения изоляцни из натуральных и синтетических волокон
- •4.2. Подразделенные и транспонированные обмоточные провода
- •4.4. Обмоточные провода с пластмассовой изоляцией
- •ТЕХНОЛОГИЯ ПРОИЗВОДСТВА ПРОВОДОВ
де случаев используется часть катанки, которая поступает непосредствен но с приемного устройства прокатного стана. Плавильная печь индукцион ного типа имеет производительность 3-10 т/ч (обычно около 6 т/ч), темпе ратура меди в тигле около 1120 °С, содержание кислорода в меди не более 5 10-4 % (бескислородная медь). Исходная заготовка - катанка диаметром 12,7 мм - подвергается предварительному волочению и скальпированию до диаметра 9,6 мм и подается к литейному тиглю. На этой операции за час к литейному тиглю поступает 3 т медной заготовки. На выходе из литейно го тигля, в который заготовка поступает снизу, она имеет диаметр 15,9 мм. После предварительного охлаждения, обеспечивающего снижение темпе ратуры поверхности до 800 °С, медная заготовка подается к прокатному стану. Производительность стана до 9 т/ч. Так как поступающая к прокат ному стану заготовка имеет круглую форму и высокую температуру, то для получения катанки диаметром 12,7 мм достаточно всего пяти прокат ных клетей, калибровка которых выполнена по системе круг - овал. После горячей прокатки температура катанки составляет около 50 °С. Весь про цесс осуществляется в защитной атмосфере, что позволяет получать бес кислородную катанку высокой чистоты с неокисленной высококачествен ной поверхностью.
Процесс получения медной катанки методом «дип-форминг» имеет те же преимущества перед процессом горячей прокатки, что и процесс не прерывного литья и прокатки (НПЛ):
1)в качестве сырья вместо дорогостоящих слитков используются ка тодная медь, отходы производства, медная стружка и т. п.;
2)исключается операция травления катанки;
3)длина получаемой катанки ограничивается только вместимостью приемного устройства;
4)повышенное качество катанки, обеспечиваемое равномерной мел козернистой структурой, проявляющееся в высокой пластичности и по вышенной электропроводности.
Использование катанки, полученной методом «дип-форминг», осо бенно эффективно в производстве круглых и прямоугольных эмалирован ных проводов больших сечений. В отличие от метода НЛП метод «дипформинг» обеспечивает получение бескислородной меди.
1.7. Травление катанки
Горячая прокатка медной заготовки сопровождается интенсивным окислением ее поверхности, в результате чего заготовка покрывается очень твердой и хрупкой окалиной.
При горячей прокатке алюминиевой заготовки окалина не образуется, так как алюминий покрыт тонкой и очень прочной окисной пленкой AI2O3, препятствующей дальнейшему процессу окисления.
Волочение медной катанки с окалиной не производится, так как из ка танки с окалиной получается проволока неудовлетворительного качества по чистоте поверхности и механическим параметрам. Кроме того, повыша ется обрывность проволоки, снижается стойкость волочильного инстру мента и производительность оборудования.
Основным способом удаления окалины с поверхности медной катанки является травление.
Травление медной катанки производится в водном растворе серной кислоты, содержащей 5-15 % H2SO4, при температуре 40-60 °С. Окалина, состоящая из внутреннего слоя закиси меди С112О и наружного слоя окиси меди СиО, быстро растворяется в таком растворе, а медь в этих условиях с серной кислотой не реагирует.
CuO + H2SO4 —►Q 1SO4 + H 2OJ
CU2O + H2SO4 —> CUSO4 + Си + Н2О.
Протравленные бухты катанки промываются холодной водой для удаления остатков кислоты и частиц металла, а затем, с целью полной ней трализации кислоты, раствором щелочи при температуре 55-60 °С в тече ние 2-3 минут (мыльный раствор). Щелочь частично остается на поверх ности катанки и благоприятно влияет на процесс волочения.
Обычно производится травление катанки в бухтах, но можно совме щать травление с прокаткой при непрерывном движении катанки.
Оборудование для травления подразделяется на два основных типа: периодического и непрерывного действия.
Установки периодического действия состоят из ряда ванн и подъем но-транспортных механизмов. В таких установках медь, подлежащая трав лению, последовательно в течение определенного времени проходит опе рации травления, промывки, нейтрализации, сушки.
Установки периодического действия применяются в основном для травления пакетов бухт, шин, коллекторной меди. Пакеты заготовок опус каются краном в бак с травильным раствором, подогретым до 40-60 °С, и остаются там на 30-40 минут до приобретения поверхностью изделий светло-розового или кирпичного цвета. Из травильной ванны катанка кра ном переносится на площадку для промывки, где струей из брандспойта с нее удаляются остатки травильного раствора и медная пыль. Промывка должна быть тщательной. В конце промывки стекающая с бухт вода долж на быть бесцветной. После промывки бухты погружаются в бак нейтрали
зации, где должен находиться раствор мыла или каустической соды в воде, подогретой до температуры 50-70 °С.
Установки непрерывного действия предназначены для травления медной катанки в бухтах. Такие установки имеют транспортеры, при по мощи которых бухты автоматически перемещаются из ванны в ванну.
Во избежание уменьшения концентрации серной кислоты ванны трав ления соединены с установкой для регенерации раствора. Происходит по стоянный обмен порциями раствора между ванной травления и ванной ре генерации, для чего предусмотрено автоматическое регулирование уров ней в обеих ваннах.
При выходе из ванны травления бухты промываются холодной про точной водой под давлением. Затем они поступают в ванну нейтрализации, в которой и происходит подогрев бухт, что ускоряет дальнейшую сушку.
Раствор в ванне нейтрализации постоянно обновляется, т.е. часть рас твора через сливной штуцер уходит в канализацию, а в ванну добавляется холодная водопроводная вода.
После нейтрализации бухты желательно обдуть подогретым воздухом или паром. Сухие протравленные бухты поступают на приемный стол, где их освобождают от подвески. Затем они идут на склад.
Для приготовления травильного раствора применяется техническая серная кислота с содержанием H2SO4 62-67 %. Травильный бак заполняет ся водой до половины объема, после чего в него тонкой струей вливается серная кислота. В полученный раствор снова доливается вода с таким рас четом, чтобы полностью был покрыт протравливаемый металл. Концен трация серной кислоты должна быть равна 8-12 %. Раствор подогревается до температуры 50-60 °С.
Раствор для нейтрализации приготавливается из 40 %-ного хозяйст венного мыла и каустической соды. Разведенное мыло и каустическая сода добавляются в бак для нейтрализации 2-3 раза в смену. Кусковое мыло пе ред загрузкой в бак должно быть растворено в горячей воде.
В процессе травления в растворе накапливаются сернокислые соли меди, которые замедляют реакции растворения окислов и делают раствор непригодным для травления. Его необходимо заменить. На заводах для из влечения меди из растворов используются следующие методы:
1. Электролитический. Извлечение меди ведут путем электролиза тра вильного раствора после перекачки его в специальную ванну. В ванне на ходятся медные и свинцовые пластины, к которым подводится постоянный ток. Медная пластина - катод, свинцовая - анод. На катоде осаждается медь, на аноде - кислород. Одновременно с извлечением меди регенериру ется (восстанавливается) отработанный раствор, который применяется для повторного использования.
2.Выпаривание. Отработанный раствор перекачивают в бак для выпа ривания. Во время нагрева раствор испаряется до насыщения его медным купоросом. Насыщенный раствор перегоняется в баки-кристаллизаторы, в которых при охлаждении выделяется медный купорос. Кристаллизуется купорос на устанавливаемых в баках свинцовых пластинах в течение 3-4 дней.
3.Извлечение меди в виде фольги. Для извлечения меди из растворов применяется барабанный электролизер с нерастворимым анодом. Травиль ный раствор закачивается насосом в напорный бак, откуда он самотеком поступает в ванну электролизера и из нее обратно в травильную ванну. Медь непрерывно осаждается на вращающемся барабане-катоде. Она от деляется от барабана в виде непрерывной ленты; последовательно прохо дит через слой воды, концентрированной серной кислоты и снова через слой воды; обмывается струями чистой воды; просушивается горячим воз духом и наматывается на шпулю. Толщина фольги зависит от силы тока и скорости вращения барабана.
Отработанные травильные растворы и промывочные воды перед сли вом в канализацию обезвреживаются путем пропускания их через слой из
вести.
H 2S 0 4 +Са(ОН)2 ->CaS04 + 2Н20;
CuS04 + Са(ОН)2 —> CaS04 + Cu(OH)2.
Образующиеся нерастворимые соли извлекаются из нейтрализацион ных колодцев, а вода сливается в канализацию.
Наличие на поверхности заготовки после травления темных пятен и полос недопустимо, оно является следствием плохого травления, обуслов ленного следующими причинами:
-не выдержано время травления;
-низка температура травильного раствора;
-травильный раствор содержит много медного купороса.
Смена травильного раствора и чистка ванны производятся по мере выработки травильного раствора, но не реже двух раз в месяц.
Содержание H2SO4 контролируется после изготовления нового тра вильного раствора, а затем периодически в процессе работы. Содержание медного купороса проверяется 1 раз в смену и дополнительно при обнару жении плохого качества травления.
1.8. Скальпирование медной катанки
Травление в ванне с серной кислотой удаляет окалину. При этом на поверхности катанки обнаруживается большое количество мелких трещин,
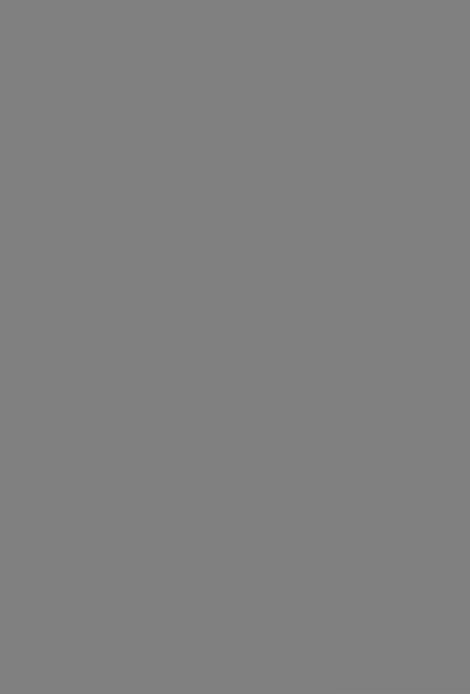
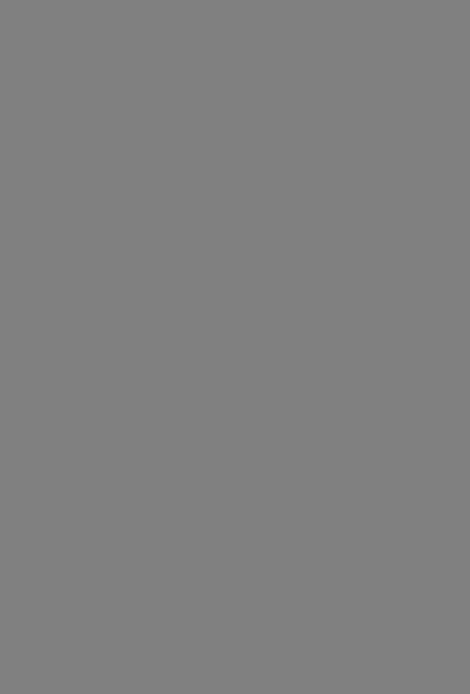
Таблица 1.3
|
|
Показатели деформации металла |
|
|
||||
Показа |
|
Величины показателей, выраженные через |
|
|||||
|
|
|
|
|
|
|
коэф |
|
тели |
диаметр |
|
|
|
|
|
||
|
|
|
|
|
фициент |
|||
деформа |
|
|
|
|
|
|||
круглого |
сечение |
длину |
вытяжку обжатие удлине |
умень |
||||
ции |
профиля do, |
FQ, FK |
Аь IK |
|
8 |
ние X |
шения |
|
металла |
|
|||||||
|
|
dK |
|
|
|
|
|
сечения |
|
|
|
|
|
|
|
е |
|
|
|
|
|
|
|
|
|
|
Вытяж- |
|
do2 |
F0 |
lK |
|
1 |
1 + X |
1 |
ка р |
|
|
FK |
*0 |
|
1 -6 |
8 |
|
|
|
|
|
|||||
Обжа |
do |
~ dx |
Fo~FK |
Iк ~ A> |
H-1 |
8 |
X |
1 - Б |
тие 5 |
|
do |
Fo |
IK |
|
1 + X |
||
|
|
|
|
|||||
Удлине |
О |
1N1 * N> |
Fo~FK |
Ik “ A> |
Ц- 1 |
5 |
X |
1 - Б |
ние X |
|
dK |
FK |
lo |
1 -5 |
8 |
||
|
|
|
||||||
Коэф |
|
dK2 |
FK |
lo |
1 |
1 - 5 |
1 |
8 |
фициент |
|
dB2 |
Fo |
IK |
|
|
1 + X |
|
умень |
|
|
|
|
|
|
|
|
|
0 |
|
|
|
|
|
|
шения
сече ния 8
Вытяжка р показывает, во сколько раз увеличилась длина изделия, а обжатие 6 - на сколько уменьшилось сечение металла (обычно в процен тах).
Так как объем металла при пластической деформации практически не меняется, то можно записать
Fok = FKlK или -^ - = у - = Ц-
FK 10
Вытяжка, которую получают за один проход, называется частной. Величину суммарной вытяжки за п проходов можно записать в виде
Цсум = НтМ 2’****Цл>
где Реум - суммарная вытяжка при волочении через п волок; Pi - вытяжка в первой волоке;
р„ - вытяжка в и-й волоке.
Сила Р, прикладываемая к переднему концу протягиваемой проволо ки, носит название силы волочения. Этой силы должно быть достаточно
для того, чтобы преодолеть сопротивление деформации металла и силу трения металла о стенки волоки. Сила волочения, отнесенная к 1 мм2 пло щади протянутого металла F, называется напряжением волочения oz (кг/мм2).
Р
Для определения <jz существует несколько аналитических формул. Одна из них - формула Гавриленко:
ст2= М р - 1)0 +/ctg а),
где Ст/г - сопротивление деформации протягиваемого металла; / - коэффициент трения;
а- половина угла рабочего конуса;
р- вытяжка в данном проходе.
Так как сила волочения приложена к проволоке со стороны выхода из волоки, то стабильность процесса определяется прочностью проволоки. Это условие может быть записано следующим образом:
|
CTZ< °Ву |
|
где с в - предел прочности протягиваемого металла после выхода из волоки. |
|
|
Разделив ов на |
получим |
|
|
~ > 1; * з = — з |
(М) |
|
Gz |
|
где К3 - коэффициент запаса. С одной стороны, чем коэффициент запаса больше, тем меньше вероятность обрыва проволоки.
С другой стороны, из формулы (1.1) следует, что чем больше р (вы тяжка), тем выше напряжение волочения crz и, соответственно, меньше К3. Поэтому К3 выбирают исходя из имеющегося опыта по условию мини мальной обрывности. Обычно К3находится в пределах 1,5-2,0, причем для меньших диаметров проволоки назначается большее значение К3.
Вкабельной промышленности применяется холодное волочение, т.е. металл перед обработкой не нагревается. Он входит в волочильный канал при комнатной температуре. При холодном волочении с надлежащей смаз кой и качественным инструментом протянутый металл имеет гладкую бле стящую поверхность и достаточно точные размеры поперечного сечения.
Вкабельной промышленности производятся из'делия большой длины, но малых сечений, с отношением ширины к толщине поперечного сечения, не превышающим «12. Такое изделие называется проволокой.