
673
.pdfВ результате математического моделирования была получена зависимость, позволяющая выявить влияние условий накатывания и способности материала к упрочнению на относительную степень упрочнения ϕ в виде
функции
|
σ |
|
|
|
|
ϕ= f |
|
,β,µ,П |
, |
(1) |
|
σs |
|||||
|
|
|
|
где σ – нормальное к поверхности вала напряжение; µ – коэффициент кон-
тактного трения.
В плоской постановке при нестесненном пластическом деформировании проекция b площади контакта S конического индентора с полупространством (если пренебречь образованием наплыва) всегда пропорциональна глубине внедрения а, т.е.
b =ka, |
|
где k – коэффициент пропорциональности. |
|
С другой стороны, нормальную нагрузку F, |
действующую на индентор, |
можно определить по уравнению |
|
F =qmbz =qm kaz, |
(2) |
где qm – среднее давление в контакте; z – линейный размер, перпендикулярный главной плоскости деформирования, z =1.
Известно [6], что при нестесненном пластическом деформировании qm =Cσs (С – константа, зависящая от трения и геометрии индентора). Предполагая, что независимо от глубины внедрения и нагрузки на площади контакта всегда существует линейный размер l0 , на котором внешняя нагрузка
инициирует постоянную интенсивность влияния (погонную нагрузку), из выражения (2) можно получить
a |
= |
F |
|
|
= |
σ |
, |
|||
l |
Cσ kzl |
σ |
s |
|||||||
|
|
|
|
|||||||
0 |
|
s |
0 |
|
|
|
|
|
||
|
|
a =l |
σ |
. |
|
|
(3) |
|||
|
|
|
|
|
||||||
|
|
0 σ |
|
|
|
|
|
|||
|
|
|
s |
|
|
|
|
|
Из формулы (3) следует важный вывод о том, что при нестесненном пластическом деформировании, имеющем место в процессе накатывания роликом, отношение σ/ σs прямо пропорционально глубине внедрения a. Проведенные оценочные расчеты это полностью подтвердили.
21
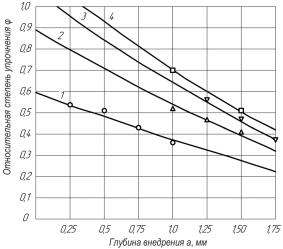
Таким образом, для конкретного материала вала и принятых условий смазывания П и µ – постоянные величины. Поэтому решение уравнения (1),
являясь функцией двух аргументов, в трехкоординатной системе представляет собой некую поверхность ϕ.
Экспериментальное определение одного из значений ϕ при произвольно выбранном сочетании a и β (например, для образца № 1) позволяет устано-
вить величину произведения kC, удовлетворяющую всем точкам поверхности ϕ и, следовательно, всем сочетаниям a и β. Следовательно, на основании
выражения (3) в уравнении (1) величина σ/ σs является пропорциональной глубине внедрения а. Таким образом, при П= const и M =const уравнение
(1) приводится к функции
ϕ= f (a,β).
Экспериментальная оценка достоверности разработанной математической модели проводилась с использованием конических роликов с углами контакта 5, 10, 15 и 20° при величинах натяга 0,25–1,75 мм. С целью сравнительной оценки проводились опыты с тороидальным роликом. Накатывались образцы валов из стали 40Х диаметром 60 мм.
Рис. Зависимость относительной степени упрочнения φ от глубины внедрения а и угла контакта β (сплошные линии – расчет, точки – эксперимент; 1 – β = 5°,
2 – β = 10°, 3 – β = 15°, 4 – β = 20°)
Степень упрочнения накатанных образцов оценивалась по приросту относительной микротвердости поверхности. Микротвердость измерялась с помощью микротвердомера ПМТ-3М по соответствующей методике.
22
Результаты расчета показали близкое соответствие результатам опытов (рисунок), что указывает на достоверность примененного математического моделирования. При этом было установлено, что угол контакта и натяг существенно влияют на параметры упрочнения, а ролик с конической рабочей поверхностью по упрочняющей способности более эффективен, чем тороидаль-
ный (в 1,5–1,6 раза).
Работа выполнялась в рамках хоздоговорной НИР, заказчик «Горьковская железная дорога – филиал ОАО «Российские железные дороги».
Список литературы
1.Смелянский В.М. Механика упрочнения деталей поверхностным пластическим деформированием. – М.: Машиностроение, 2002. – 300 с.
2.Макушок Е.М. Основные направления развития механики трения //
Трение и износ. – 1995. – № 3, Т. 16. – С. 416–427.
3.Школьник Л.М., Шахов В.И. Технология и приспособления для упрочнения и отделки деталей накатыванием. – М.: Машиностроение, 1964. – 184 с.
4.Джонсон У., Меллор П.Б. Теория пластичности для инженеров: пер.
сангл. / пер. А.Г. Овчинникова. – М.: Машиностроение, 1979. – 567 с.
5.Сторожев М.В., Попов Е.А. Теория обработки металлов давлением: учебник для вузов. – 4-е изд., перераб. и доп. – М.: Машиностроение, 1977. – 423 с.
6.Трение, износ и смазка (трибология и триботехника) / А.В. Чичинадзе [и др.]; под общ. ред. А.В. Чичинадзе. – М.: Машиностроение, 2003. – 576 с.
Получено 7.02.2012
23
УДК 621.9.06
А.М. Ханов, А.Е. Кобитянский, А.В. Шафранов
A.M. Khanov, A.E. Kobityansky, A.V. Shafranov
Пермский национальный исследовательский политехнический университет
State National Research Polytechnical University of Perm
ОЦЕНКА ВЛИЯНИЯ ПАРАМЕТРОВ ОПОР КАЧЕНИЯ НА ДИНАМИКУ ШПИНДЕЛЬНОГО УЗЛА
ESTIMATION OF IMPACT ROLLING-CONTACT BEARING PARAMETERS ON THE SPINDLE ASSEMBLY DYNAMICS
Проведено исследование динамики шпиндельного узла на опорах качения. На основе математического моделирования получены оценки влияния параметров опор на динамические характеристики шпиндельного узла. Приведены результаты расчетов.
Ключевые слова: металлорежущие станки, шпиндельные узлы, математическое моделирование, динамика.
Dynamics research dynamic spindle on rolling bearing is conducted. On the basis of mathematical modeling estimations are received and results of influence of parameters of support on dynamic characteristics spindle knot are resulted.
Keywords: metal-cutting machines, spindle assemblies, mathematical modeling, dynamics.
Оценка влияния параметров опор вращения шпиндельных узлов на его динамическую точность является одним из этапов цикла комплексных исследований с помощью имитационного моделирования [1, 2]. В качестве основы моделирования принята соответствующая математическая модель и программное обеспечение SpindelDinamic 6.6020 [3]. Объектом изучения является шпиндельный узел станка 3В642 в процессе плоского шлифования.
Первоначально оценивалось влияние типоразмеров подшипников качения в диапазонах, приведенных ниже. В процессе моделирования варьировались рабочие частоты вращения шпинделя, при фиксированных прочих режимах обработки.
Рассчитывались перемещения шпинделя x1, x2, z1, z2, соответственно
в левой и правой опорах, и перемещения инструмента xинстр, zинстр в вертикальной и поперечной плоскостях, а также их скорости и ускорения.
24
Параметр |
|
Значение |
Типоразмер/количество тел качения |
|
66408/10 |
подшипников |
|
36208/12 |
Типоразмер/количество тел качения |
|
46308/12 |
подшипников |
|
46108/16 |
Рабочая частота |
|
1000 |
|
2000 |
|
вращения шпинделя, об/мин |
|
4000 |
|
|
6000 |
Глубина шлифования, мм |
|
0,01 |
Поперечная подача, мм/ход |
|
10 |
Скорость заготовки, м/мин |
|
3 |
В качестве примера в таблице приведены |
значения кинематических |
и динамических характеристик на подшипниках 36208.
Результаты расчетов максимальных и минимальных значений динамических характеристик
шпиндельного узла на подшипниках 36208
Динамические |
Частота вращения шпинделя, об/мин |
|||
характеристики |
1000 |
2000 |
4000 |
6000 |
x1, мкм |
–1,254–1,049 |
–1,130–1,201 |
–0,765–1,077 |
–0,765–1,077 |
Vx1, мм/с |
–6,399–6,270 |
–6,089–6,221 |
–4,784–4,790 |
–4,784–4,790 |
ax1, м/с2 |
–39,062–41,407 |
–42,324–40,320 |
–32,547–26,183 |
–32,547–26,183 |
z1, мкм |
–1,000–0,608 |
–1,120–0,954 |
–0,878–0,783 |
–0,878–0,783 |
Vz1, мм/с |
–4,900–4,570 |
–5,672–5,941 |
–4,318–4,489 |
–4,318–4,489 |
az1, м/с2 |
–25,168–30,682 |
–36,275–38,014 |
–26,135–27,348 |
–26,135–27,348 |
x2, мкм |
0–3,063 |
–0,065–2,366 |
–0,395–1,909 |
–0,395–1,909 |
Vx2, мм/с |
–7,646–7,852 |
–5,718–5,677 |
–4,323–4,382 |
–4,323–4,382 |
ax2, м/с2 |
–45,923–30,936 |
–31,063–21,194 |
–22,606–15,406 |
–22,606–15,407 |
z2, мкм |
–0,132–1,276 |
–0,509–1,065 |
–0,485–0,763 |
–0,485–0,763 |
Vz2, мм/с |
–3,584–3,637 |
–3,334–3,450 |
–2,474–2,568 |
–2,474–2,568 |
az2, м/с2 |
–21,427–14,085 |
–17,397–13,328 |
–12,088–9,330 |
–12,088–9,330 |
xинстр, мкм |
0–4,177 |
–0,042–3,056 |
–0,065–2,460 |
–0,059–2,460 |
VXинстр, мм/с |
–10,329–10,417 |
–7,096–7,019 |
–5,477–5,574 |
–5,477–5,574 |
aXинстр, м/с2 |
–59,517–45,004 |
–38,141–29,775 |
–26,892–22,635 |
–26,892–22,635 |
zинстр, мкм |
–0,001–1,761 |
–0,589–1,462 |
–0,582–1,033 |
–0,582–1,033 |
VZинстр, мм/с |
–4,328–4,373 |
–4,326–4,353 |
–3,267–3,246 |
–3,268–3,246 |
aZинстр, м/с2 |
–24,774–18,169 |
–21,493–17,170 |
–14,464–12,139 |
–14,464–12,139 |
Фрагменты графических иллюстраций результатов расчета, например для вертикальной плоскости nшп = 2000 об/мин, представлены на рис. 1–3.
25
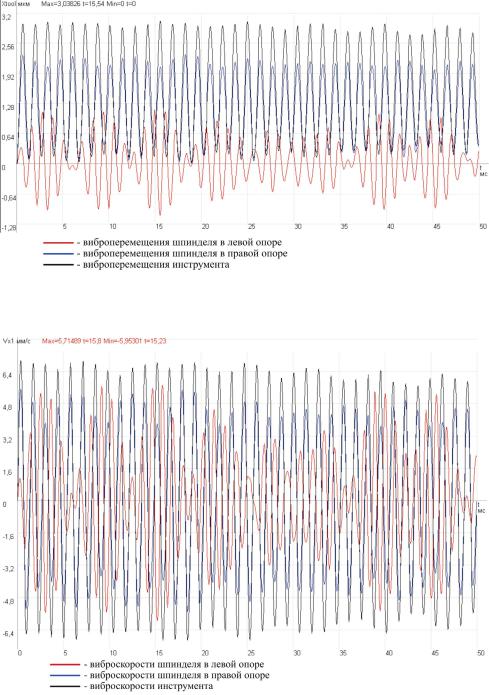
Рис. 1. Виброперемещения инструмента и шпинделя в опорах в вертикальном направлении
Рис. 2. Виброскорости инструмента и шпинделя в опорах в вертикальном направлении
26
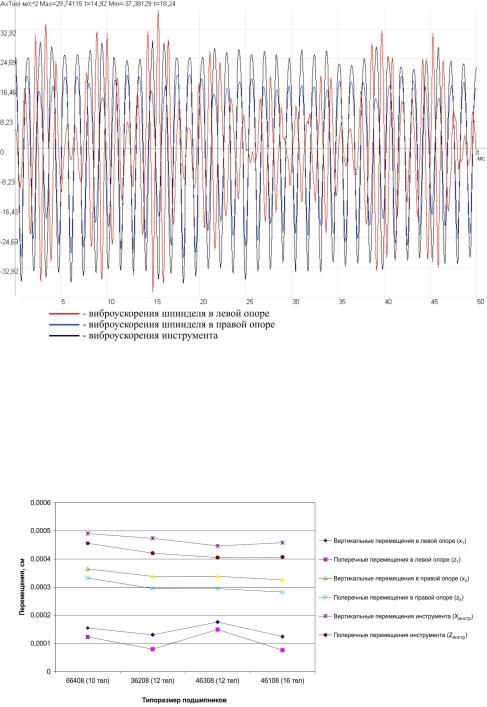
Рис. 3. Виброускорения инструмента и шпинделя в опорах в вертикальном направлении
Установлено, что при увеличении количества тел качения подшипников
с10 для серии 66408 до 16 для серии 46108 при nшп = 2000 об/мин величины виброперемещений инструмента уменьшаются в вертикальном направлении
с4,9 мкм до 4,579 мкм; в поперечном – с 4,559 мкм до 4,071 мкм, что составляет соответственно 6,5 и 10,7 % (рис. 4).
Рис. 4. Диаграммы влияния типоразмера подшипника на виброперемещения инструмента и шпинделя в опорах
27
При оценке влияния погрешностей изготовления деталей подшипников учитываются погрешности желобов колец. Предполагается недеформируемость тел качения и колец подшипников. Тогда можно считать, что перекатывание тел качения происходит по волнистой поверхности беговой дорожки с условно принятым профилем. В соответствии с работой [4] профили дорожек качения колец и их погрешности hi представляются в виде
h |
=− n |
A sin k (ϕ |
с |
+iγ)+α |
|
+ |
n |
B |
sin k (cϕ |
с |
−iγ)+β |
|
, |
|
i |
∑ k |
|
|
k |
|
∑ k |
|
|
k |
|
||||
|
k=1 |
|
|
|
|
|
|
k=1 |
|
|
|
|
|
|
где hi – суммарное отклонение вследствие погрешностей дорожек качения наружного и внутреннего колец в i-м контакте; Ak, Bk – амплитуды k-й гармоники соответственно для контуров наружного и внутреннего колец; αk, βk – сдвиг фазы k-й гармоники для тех же контуров; c – коэффициент, учитывающий разность углов поворота внутреннего кольца (φв) и сепаратора (φс),
с=ωв ωс −1 ; n – количество гармонических составляющих.
Сучетом вертикального и поперечного направлений:
h |
= |
|
− n |
A sin k (ϕ |
с |
+iγ)+α |
|
+ |
n |
B |
sin k (cϕ |
с |
−iγ)+β |
|
cosη , |
||
xi |
|
|
∑ k |
|
|
k |
|
∑ k |
|
|
k |
|
i |
||||
|
|
|
k=1 |
|
|
|
|
|
|
k=1 |
|
|
|
|
|
|
|
h |
= |
|
− n |
A sin k (ϕ |
с |
+iγ)+α |
|
+ |
n |
B |
sin k (cϕ |
с |
−iγ)+β |
|
sin η . |
||
zi |
|
|
∑ k |
|
|
k |
|
∑ k |
|
|
k |
|
i |
||||
|
|
|
k=1 |
|
|
|
|
|
|
k=1 |
|
|
|
|
|
|
|
Функции неровностей вводились в математическую модель [1] в виде дефектов «волнистости» и «гранности» дорожек качения. Численный эксперимент проводился в диапазоне изменения параметров дефектов, установленных из технических условий.
По наружным кольцам: высота волнистости А = 0,5…3,0 мкм; шаг волнистости Нн = 1,5…10 мм; высота гранности В = 0,5…2,5 мкм; шаг гранности
Нн = 6…12 мм;
По внутренним кольцам: высота волнистости А = 0,5…4,8 мкм; шаг волнистости Нн = 1,0…10 мм; высота гранности В = 2,0…6,0 мкм; шаг гранности
Нн = 14…24 мм.
Фрагменты результатов расчетов для этих случаев приведены на рис. 5–6 при условии гранности дорожек качения, а на рис. 7–8 – при учете их волнистости.
Временной сигнал полученных графиков представляется как результат сложения трех гармонических компонент. Первые две компоненты имеют частоты, незначительно отличающиеся друг от друга, приводящие к биениям. Третья компонента, со значительно более низкой частотой, является результатом введения в математическую модель функции погрешностей беговых
28
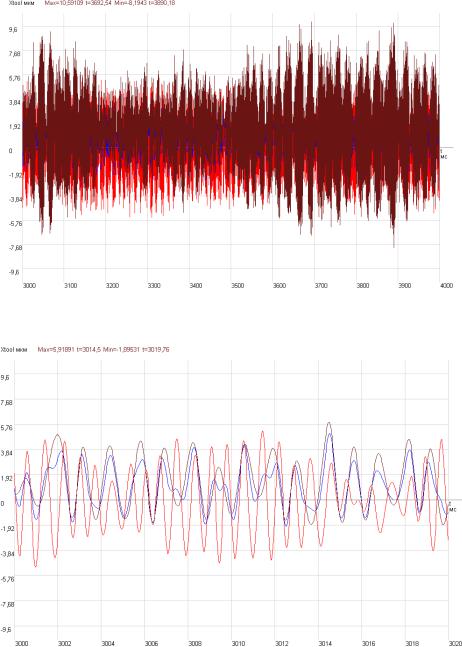
дорожек подшипника качения. Действие третьей компоненты состоит только в том, что она смещает по высоте точки суммарной кривой, т.е появляется длинная волна.
Рис. 5. Виброперемещения в вертикальном направлении при гранности дорожек качения: A = 1 мкм; Hн = 10 мм; В = 2 мкм; Hв = 20 мм (nшп = 2000 об/мин)
Рис. 6. Фрагмент виброперемещений в вертикальном направлении при гранности дорожек качения: A = 1 мкм; Hн = 10 мм; В = 2 мкм; Hв = 20 мм (nшп = 2000 об/мин)
29
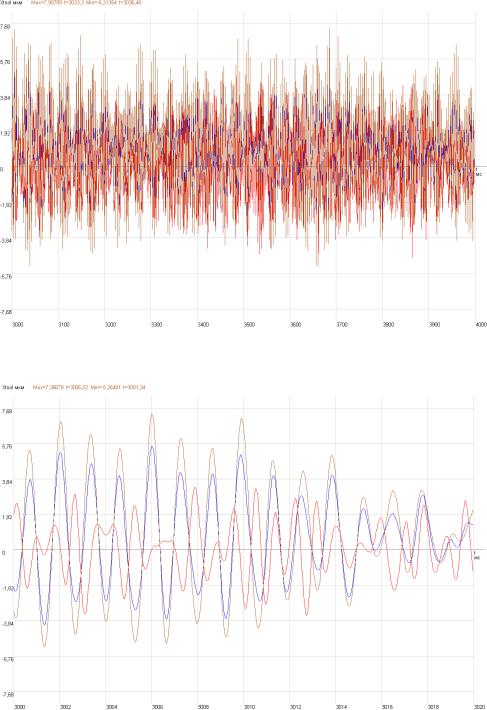
Рис. 7. Виброперемещения в вертикальном направлении при волнистости дорожек качения: A = 1 мкм; Hн = 1 мм; В = 0,8 мкм; Hв = 10 мм (nшп = 4000 об/мин)
Рис. 8. Фрагмент виброперемещений в вертикальном направлении при волнистости дорожек качения: A = 1 мкм; Hн = 1 мм; В = 0,8 мкм; Hв = 10 мм (nшп = 4000 об/мин)
30