
673
.pdf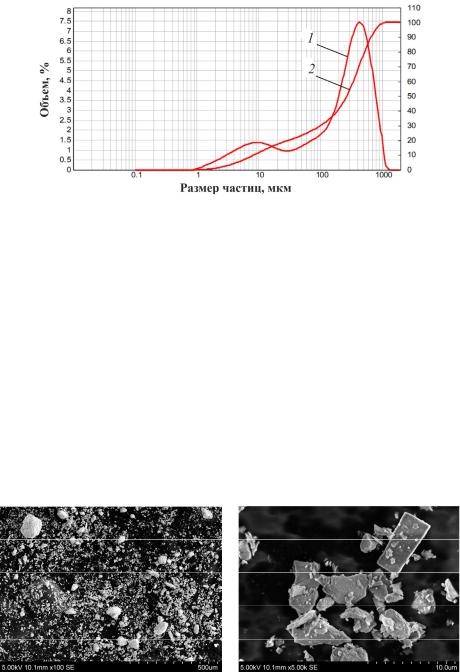
Рис. 3. Гранулометрический состав порошка габбро-диабаза, полученный комплексной системой Mastersizer 2000: 1 – распределение частиц относительно объемафракции; 2 – интегральноераспределение частиц в зависимости от общего объема фракции
Для проведения электронной микроскопии с анализом изображения был использован сканирующий электронный микроскоп Hitachi S-3400N, потребовалось менее 1 г пробы габбро-диабаза, чтобы определить гранулометрический состав и морфологию частиц. Время проведения электронной микроскопии составило 40 мин, обработка полученных результатов заняла 120 мин.
Распределение и морфология частиц анализировалась на основе рис. 4. Видно, что в габбро-диабазе присутствует несколько минеральных фаз, об этом свидетельствует разная форма частиц: например кристаллы, гранулы, осколочные частицы, сложные агломераты, состоящие из различных минеральных фаз частиц, которые по-разному влияют на металлургические процессы при свар-
ке (рис. 4, б).
а |
б |
Рис. 4. Гранулометрический состав и морфология частиц габбро-диабаза Пермского края: а – общий вид, ×100; б – кристаллы и осколочные частицы минеральных фаз в габбро-диабазе, ×5000
81
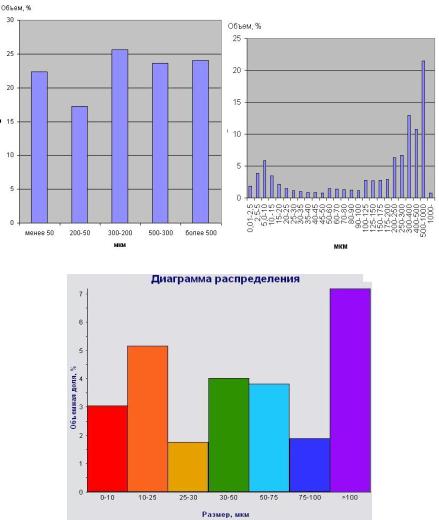
Результаты гранулометрического состава частиц габбро-диабаза представлены на диаграмме, полученной в программе «ВидеоТест – Металл 1.0» (рис. 5, в). Диаграмма показывает процентное соотношение фракций от менее 10 мкм до более 100 мкм по фотографии рис. 4, а. Регистрация более мелких частиц менее 0,1 мкм велась ручным подсчетом в программе «ВидеоТест – Размер 1.0» на снимках с 30000-кратным увеличением.
Преимущества и недостатки метода гранулометрического анализа представлены в табл. 3.
а |
б |
в
Рис. 5. Сравнительный анализ гранулометрического состава частиц габбро-диабаза, полученныйразличнымиметодами: а– ситовым анализом; б– лазерным сканированием; в – электронной микроскопией с анализом изображений в программе «ВидеоТест 1.0»
82
Таблица 2
Сравнительная характеристика различных методов гранулометрического анализа
Характеристика |
Ситовой анализ |
Лазерное |
Электронная |
|
сканирование |
микроскопия |
|||
|
|
|
|
|
Необходимое количество порош- |
25–500 |
2–10 |
0,1–5 |
|
ка для анализа, г |
||||
|
|
|
||
Время проведения анализа, мин |
30–60 |
3–5 |
60–120 |
|
Диапазон улавливаемых разме- |
>50 |
0,2–2000 |
<0,2 |
|
ров, мкм |
||||
|
|
|
||
Возможность отделять частицы |
+ |
– |
– |
|
разного размера |
||||
|
|
|
||
Возможность определить морфо- |
– |
– |
+ |
|
логию частиц |
||||
|
|
|
||
Возможность подсчета удельной |
– |
+ |
– |
|
поверхности |
||||
|
|
|
||
Возможность подсчета среднего |
+ |
+ |
+ |
|
радиуса |
||||
|
|
|
Полученные данные свидетельствуют о том что порошок габбро-диабаза состоит из частиц различной формы, как сферической, так и остроугольной, средний диаметр частиц составляет 300 мкм, средняя удельная поверхность 0,2 м2/г. При обобщении данных, полученных всеми тремя методами, установлено, что 60 % порошка составляют частицы размером 200–300 мкм, 10 % – частицы размером 300 и более мкм, 10 % – частицы 100 и более мкм, 5 % – частицы 50–75 мкм, 5 % – частицы 75–100 мкм, 3,25 % – частицы 10–25 мкм, 2 % – частицы 30–50 мкм, 2 % – частицы 5–10 мкм, 1,5 % – частицы менее
5 мкм, 1,25 % – частицы 20–30 мкм.
Таким образом, рассмотренные методы гранулометрического анализа, а именно ситовой анализ, лазерное сканирование и электронная микроскопия, наиболее эффективны в комплексном применении. Ситовой анализ – единственный способ, позволяющий отделить друг от друга частицы разного размера, электронная микроскопия – единственный метод, позволяющий оценить морфологию частиц, а лазерное сканирование – наиболее быстрый метод, позволяющий получить информацию о распределении частиц в числовом диапазоне, определить удельную поверхность и средний диаметр частиц.
Список литературы
1.ПетровГ.Л. Сварочные материалы. – Л.: Машиностроение, 1972. – 250 с.
2.Технология электрической сварки металлов и сплавов плавлением / под ред. акад. Б.Е. Патона. – М.: Машиностроение, 1974. – 768 с.
83
3.Игнатов М.Н., Ханов А.М. Основы технологии электродного производства: учеб. пособие / Перм. гос. техн. ун-т. – Пермь, 1997. – 109 с.
4.Волков В.А. Коллоидная химия: Поверхностные явления и дисперсные явления: учебник для вузов. – М.: Изд-во МГТУ, 2001. – 640 с.
5.Оценка пригодности и доступности базальтоидных и габброидных комплексов Западного Урала (Пермский край) для производства сварочных материалов / А.М. Игнатова [и др.] // Вестник ПГТУ. Машиностроение, мате-
риаловедение. – Пермь, 2010. – Т. 12, № 4. – С. 104–116.
6.Сканирующая электронная микроскопия и рентгеноспектральный микроанализ / М.М. Криштал [и др.]. – М.: Техносфера, 2009. – 206 с.
7.Андреев C.E., Зверевич B.B., Перов B.A. Дробление, измельчение
игрохочение полезных ископаемых. – М.: Недра, 1980. – 415 с.
Получено 2.02.2012
84
УДК 621.990
Ю.Ю. Носкова, О.А. Халтурин, Т.Р. Абляз
Y.Y. Noskova, O.A. Khalturin, T.R. Ablyaz
Пермский национальный исследовательский политехнологический университет
State National Research Politechnic University of Perm
МЕТОД КОНТРОЛЯ КОНИЧЕСКИХ РЕЗЬБ ДЛЯ ЭЛЕМЕНТОВ БУРИЛЬНЫХ КОЛОНН
НА КООРДИНАТНО-ИЗМЕРИТЕЛЬНОЙ МАШИНЕ
CONTROL METHOD FOR TAPER THREADS
OF THE ELEMENTS OF DRILL COLUMNS
IN THE COORDINATE-MEASURING MACHINE
Проанализированы существующие методы контроля конических резьб, выявлены недостатки. Представлен современный метод контроля конических резьб на координатно-измеритель- ной машине с учетом этих недостатков.
Ключевые слова: коническая резьба, контроль, измерение, КИМ.
Analyzed the existing methods of control taper threads, identified deficiencies. Presented the modern method of controlling taper threads on coordinate-measuring machine with their account.
Keywords: taper thread, control, measurement, CMM.
В нефтяной промышленности широко используются конические резьбовые соединения. Они обладают большой герметичностью, более просты при сборке. Эксплуатационные свойства резьбовых соединений в значительной степени определяются точностью изготовления и качеством рабочих поверхностей, требования к которым постоянно повышаются.
Несмотря на большой опыт производства деталей с конической резьбой, отсутствуют точные и быстрые методы контроля параметров полученной резьбы, применимые в производственных условиях. В соответствии со стандартами [1 и др.] и сложившейся практикой контроль резьбы осуществляется двумя методами: комплексным и дифференцированным [2].
Дифференцированный контроль резьбы применяют в тех случаях, когда допуски назначены на каждый отдельный параметр резьбовых деталей. Для измерения различных элементов резьбы требуется комплект специализиро-
85
ванных инструментов, номенклатура которых зависит от типа резьбы. Так, для резьб с треугольным профилем применяются измерители глубины профиля, шага резьбы, конусности; для измерения половин угла профиля применяют микроскопы. Измерение среднего диаметра d2 наружных резьб осуществляется с помощью микрометров со вставками и др. Предприятиям, обрабатывающим резьбы по различным стандартам, и даже различных типоразмеров, нужна широкая номенклатура таких инструментов.
При измерении этими инструментами контакт с деталями имеет малую площадь, что в совокупности с переменным значением измерительного усилия приводит к возникновению погрешностей измерения, обусловленных упругими и пластическими деформациями [3]. При дифференцированном контроле используют средства измерения, у которых измерительное усилие находится в пределах от1,2 до 10,0 Н. Погрешность от такого измерительного усилия является составляющей погрешности измерения и зависит от размеров измерительных наконечников, а также от механических свойств контактирующих материалов. Такие виды контроля неотвечают современным требованиям.
Комплексный метод контроля заключается в том, что на один из параметров резьбовой поверхности назначают комплексный допуск, ограничивающий одновременно погрешности нескольких других параметров. Этим параметром является средний диаметр резьбы. К комплексному методу относится контроль резьбы с помощью калибров.
Недостатком комплексного метода является то, что с помощью калибров нельзя произвести объективный контроль и проанализировать точность изготовления элементов профиля, заданную такими параметрами, как конусность, шаг резьбы, половина угла профиля. При определенной комбинации параметров совершенно негодная резьба может быть признана годной. Фактически с помощью калибров контролируется только один виток с наибольшим приведенным средним диаметром резьбы ниппеля (или с наименьшим относительным диаметром резьбы муфты), что трудно признать достаточным [2]. Такой контроль приводит к перебраковке, увеличивает трудоемкость ремонта, снижает срок службы трубы и при этом не исключает пропуск брака. При контроле с помощью калибров определяются не действительные значения проверяемых параметров, а лишь принадлежность измеряемой резьбы к категории годности или дефектности. Кроме этого, результаты контроля резьбы калибрами в значительной степени зависят от субъективных факторов и условий работы контролера.
Калибрами невозможно контролировать высоту резьбы, форму и значения радиусов впадин (вершин), которые обеспечивают прочность колонн и герметичность соединений. Поэтому для контроля этих параметров выборочно изготавляют слепки с резьбы, обмеряя их визуальным способом на
86
микроскопе. В целом на ручной субъектный контроль с помощью слепков требуется до двух суток. Причем такой контроль имеет значительную погрешность вследствие большой усадки слепков.
При контроле резьбы калибрами их рабочие поверхности изнашиваются. Для проверки изменения размеров калибров и корректировки измеряемого натяга применяется контроль калибров контркалибрами. При наличии систематических погрешностей при изготовлении деталей может возникать ситуация, когда с контркалибром калибр контактирует менее изношенной частью, а с резьбой – более изношенной, что может привести к искажению результатов контроля. Для предотвращения этого видится полезным иметь возможность получать и анализировать полный профиль резьбы.
Внастоящее время на передовых предприятиях применяются новые уникальные лазерные компьютерные системы неразрушающих автоматических измерений геометрии наружной и внутренней резьбы, позволяющие корректировать и предотвращать дефекты параметров в реальном времени. Это отвечает современным требованиям машиностроения, в том числе нефтяного [4–7].
Внедрение таких систем требует специальной подготовки производства, больших временных и финансовых затрат. Управление этими системами требует подготовки отдельных высококвалифицированных специалистов. В то же время на многих машиностроительных предприятиях получает широкое распространение применение в процессе контроля различных координатноизмерительных машин (КИМ). Такие установки применяются как к деталям
спростыми, так и сложными поверхностями. К последним относится и резьбовая поверхность, особенно коническая. Контроль сложных поверхностей также требует высокой квалификации метролога и зачастую отдельно поставляемого программного обеспечения, проработки стратегии измерения для каждой вновь водимой детали.
Всвязи с этим мы занимаемся разработкой методики измерения на КИМ параметров конической замковой резьбы для элементов бурильных колонн З-102 ГОСТ Р 50864–96. В качестве измерительной установки нами была выбрана КИМ портального типа Contura G2. Методика основывается на разработке стратегии измерения (рис. 1), заключающейся в сканировании резьбы щупом в осевом направлении с получением совокупности точек в пространстве, описывающих профиль резьбы. Наличие такой совокупности точек дает возможность анализировать непосредственно сам профиль резьбы, оценивать действительную величину параметров резьбы, а также прогнозировать свинчиваемость изделия с калибрами и ответными деталями.
87
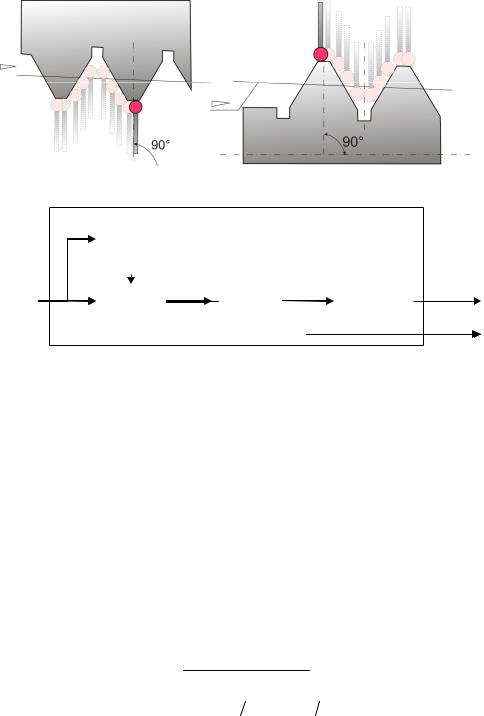
Рис. 1. Стратегия измерения
|
|
|
|
|
|
|
|
Процесс измерения |
|
|
|
|
|
|
|
|
|
|
|
|
CAD |
|
|
|
|
|
|
|
|
||
|
|
|
|
|
|
|
|
|
|
|
|
|
|
|
|
|
|
Типо- |
|
|
|
|
|
|
|
|
|
|
|
|
|
|
|
3D-модель |
|
|
|
|
|
|
|
|
|||||
|
|
размер |
|
|
|
|
|
Данные |
|
Размеры |
|
|
|
|
|
|
|
|
|
|
|
|
|
|
|
||||||
|
|
|
|
|
|
|
|
|
|
|
|
|
|||
Деталь |
|
|
|
|
КИМ |
Пост- |
|
Виртуальное |
|
Натяг |
|||||
|
|
|
|
|
обработка |
|
|
|
свинчивание |
|
|
||||
|
|
|
|
|
|
|
|
|
|
|
|
|
|
|
|
|
|
|
|
|
|
|
|
|
|
|
|
|
|
|
Размеры |
Рис. 2. Методика контроля конических резьб
В среде Calipso возможно параметрическое задание номиналов параметров элементов стратегии, что позволило создать параметрический план контроля, подходящий одновременно для измерения деталей различных типоразмеров в рамках одной конструкции профиля (рис. 2). Кроме того, такая гибкость позволит избежатьнеобходимости выравнивания положения начала витка.
Стратегия измерения состоит из элементов, описывающих основные составляющие впадины профиля конической треугольной резьбы. При этом эти элементы имеют укороченные размеры, позволяющие щупу гарантированно касаться элементов резьбы на реальной детали.
Параметры, определяющие положение и размеры элементов стратегии, рассчитываются исходя из размеров профиля. Положение элементов для каждой впадины одинаково относительно их центров (О' на рис. 3) и отличается только положением самих центров относительно координат детали.
P(cos(2φ)+ cos(α)) H = sin (α)(cos(2φ)+1) ,
p = p − |
P cos(α 2 + φ)sin (α 2) |
, |
||
cos(φ)sin (α) |
||||
1 |
5 |
|
||
|
|
|
88
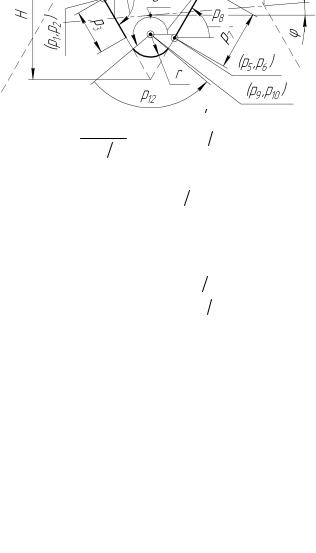
p |
|
= |
P cos(α 2 + φ)cos(α) |
− |
p5 |
|
|
− |
H |
, |
||||||||
2 |
|
|
|
tg(α 2) |
|
|||||||||||||
|
|
|
|
cos(φ)sin (α) |
|
2 |
|
|||||||||||
|
|
|
|
|
|
|
||||||||||||
|
|
|
|
|
|
|
p3 = K3 P, |
|
|
|
|
|
|
|
|
|||
|
|
|
|
|
p4 = −(90°−α 2), |
|
|
|
|
|
|
|||||||
|
|
|
|
|
p5 = K5 P + r cos(α 2), |
|
|
|
|
|
|
|||||||
|
|
p6 |
= |
K5 P |
+ r (2 |
−sin |
(α 2))− |
H |
|
, |
|
|
||||||
|
|
tg(α 2) |
2 |
|
|
|
||||||||||||
|
|
|
|
|
|
|
|
|
|
|
|
|
|
|
||||
|
|
|
|
|
|
|
p7 = K7 P, |
|
|
|
|
|
|
|
|
|||
|
|
|
|
|
|
p8 = 90°−α 2, |
|
|
|
|
|
|
|
|||||
|
|
|
|
|
|
|
p7 = 0, |
|
|
|
|
|
|
|
|
|||
|
|
|
|
|
|
p |
= 2r |
− |
H |
|
, |
|
|
|
|
|
|
|
|
|
|
|
|
|
|
|
|
|
|
|
|
|
|||||
|
|
|
|
|
|
8 |
2 |
|
|
|
|
|
|
|
|
|
||
|
|
|
|
|
|
|
|
|
|
|
|
|
|
|
|
|
||
|
|
|
|
|
p9 |
=180°+ K9 + α 2, |
|
|
|
|
|
|
||||||
|
|
|
|
|
p10 |
=180°− K10 −α 2. |
|
|
|
|
|
|
Рис. 3. Элементы стратегии измерения
Параметрическое описание стратегии производится без применения опционального модуля PCM. Поэтому параметры резьбы и другие константы задаются с помощью псевдоэлементов геометрии (рис. 4), при расчете положения элементов стратегии используются ссылки на значения, указанные в псевдоэлементах (рис. 5).
89
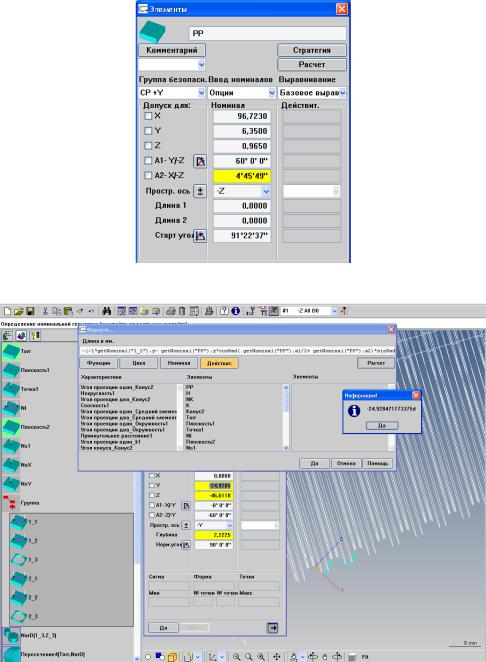
Рис. 4. Задание исходных данных
Рис. 5. Описание элементов стратегии измерения в Carl Zeiss Calipso
Расчет параметров резьбы производится при помощи геометрических построений (рис. 6).
90