
3218
.pdfrate at which it can escape through the core prints and
moulding walls, pressure "builds up until gas bubbles tin
ough the |
metal |
and may be trapped |
beneath the skin of so |
|||
lid mo.tal, |
if |
solidification has |
commenced, |
or beneath a |
||
core • |
|
|
|
|
|
|
Gas holes |
from these reasons are, as a rule, |
readily dls |
||||
tinguished |
from other |
holes such as those duo to high ga |
||||
content |
of |
the |
metal, |
or £o metal-mould reactions. |
||
They are |
usually large |
and well-rounded but |
sometimes th |
defect may |
appear in a completely different form, for ea |
|
ample, |
like |
misruns. |
However |
it |
is mainly inherent in thin walls castings. |
5- due to incomplete drying moulds and cores (at pouring the metal in dry sand moulds) or due to the higher moisture content (at pouring the metal in green sand moulds). Blow holes as the result of the high moist-» ure content usually occur when green sand moulds are used. In this case the main source of gas is the fre water, which, evaporates rapidly as soon as the tempei ature reaches 100°C. Gas is also given off by coaid and by the clay (combined water) but it takes place a temperatures higher than 400°C. Nevertheless it has determined in practice that the major constituent of gas is steam and its amount is great enough. That i
why, when the |
permeability of cores |
and green sand moulds |
is IOVJ, blows |
due to high moisture |
content are inavitable . |
They are also usually found underneath the top surface of the casting or beneath a core, and are frequently comple tely covered by a thin shell of metal, although they some times reach the surface. Their dimensions may be different depending on amount of gases, on the pouring temperature , and on the rate of their evolution,
6- as the result of the incorrect design of a gating sys
tem leading to intensive stirring the metal at the process
of pouring and to entrapping of air with the molten metal
into the mould. Entrapped air is recognized as small, in
ternally oxidized holes just beneath the cope surfacej it
.is found in aluminium and magnesium castings more freque ntly than in other cast metals,
7- by other sources of a gas evolution (soiled and rusty chills or chaplets due to their poor fusion with the basic metalj lumps of pitch or binders, when shell moulds and cores are used, as a result of nonuniform distribution-of binders in mixtures, and so on).
The reason of such defects can be |
easily found |
in |
accord |
|||
ance with the location of their ingate |
holes* |
the |
ingate |
|||
holes of these |
defects, |
as a rule, |
are |
directed to |
the side |
|
of a source a£ |
the gas |
evolution ( |
ch ill, chaplet,e^c). |
Gas holes and porosity in castings can-be eli only at the severe observance of a technological 6i
at a ll stages of the casting production: from, makingn
and preparation |
of an alloy upto cooling a casting. |
||
Measures |
of prevention of gas holes |
and porosity in сг |
|
ngs are |
usually |
divided into three |
groups : |
1- measures, preventing a saturation of a metal withg| during the process of melting.
In this case a preparation of qualitative ohargii materials is of a great umportance, For example, 1%oi rust in a steel charge brings about 2.5m? of gases per] 1 ton of liquid metal into a melting furnace. Thercfoi charge materials are to be carefully cleaned from rust moisture, and o il before melting.
|
In order to prevent gas absorption by alloys nit |
|||||||
furnace, |
the melting |
in |
medium of |
a protective gas is a |
||||
plied. |
|
When alloys |
are |
used for |
the |
manufacture |
of sji® |
|
ia lly |
responsible castings the charge |
materials |
are subj |
|||||
ected |
to |
drying or tempering, but sometimes to vaouuatol |
||||||
-before |
melting. |
|
|
|
|
|
|
|
|
The melting and pouring of |
metals and alley- |
||||||
for castings, in |
v.’hich |
a gas content must be minima-, a |
||||||
usually |
carried |
out |
in |
vacuum melting-pouring asseibli'3 |
Titanium and its alloys, molybdenum, and special high-st rength alloys are melted and poured namely in that way.
The reducing of chances for absorptionoDf gas is
possible |
by keeping |
a ll items, that |
must come into |
cont |
act with |
metal, dry, |
and by melting |
and ponring the |
metal |
at temperatures as low as possible to minimize gas solub ility .
2- It is usually impractical to prevent gas absorption en
tirely . When it is impossible, the hazards |
of dissolved |
|||||||
gases may be reduced by measures providing |
a gas removal |
|||||||
or degassing of the molten metal before |
its |
pouring into |
||||||
a mould or during the pouring process outside a melting |
||||||||
unit'^ |
They may be s remelting |
a metal, |
vacuuming |
in |
a la - |
|||
— |
v*-* |
|
|
|
|
|
|
|
die, |
pouring in vacuum plants, |
a treatment |
of the |
alloy by |
||||
supersound, flushing with |
inert gases ( Fig.2.20). |
|
||||||
|
|
The fir s t method of |
gas |
removal is |
used at |
the |
alu |
|
minium alloy production. |
Ip. this case, |
the |
fact |
that |
gases |
|||
are least soluble in cold, solid metal is applied, i.g . |
||||||||
gases |
may be removal by a sequence of melting, slow cool |
ing, freezing, remelting and heating upto the needed tem perature of pouring. During the cooling and, especially, freezing dissolved gases are removed from the molten metal.
However', except in special cases, this method is too exp
ensive |
and time-consuming to bo used |
in practice • |
At tie |
||||||
same time, |
if |
Sic-verts*law, according to which the |
amount |
||||||
of |
gas |
dissolved |
in a molten metal depends on the press |
||||||
ure |
of |
this gas |
above |
and around the |
metal, |
is used in pri |
|||
ctice, |
it |
is |
possible |
to accelerate |
the gas |
removal from |
|||
the |
metal by creating |
a rarefied atmosphere |
above |
its sun |
face in a ladle. Vacuum degassing the metal in a ladle
is an attempt to combine the advantages of melting in va cuum with the economy of air melting. Hare the metal is melted in air and then placed in an evacuated chamber(for degassing) before pouring. Pouring takes place in the op atmosphere.
Degassing alloys with the help of supersound emploies the seme principle of vacuum creating. Supersound waves of a high frequency impart to particles of a liquid metal elastic oscillations of a different value. As a result of the difference in rates ci moving particles a provisional rupture of solidity and formation of microvoides can be obtained. Dissolved gases rush to these ca vities to form bubbles. At the seад,once ruptures of the alloy* solidity bubbles increase upto critica l siaes.f loat out and are removed to the atmosphere.
Vacuum degassing
Fig. 2.20, Боте methods of metal degassing
Fig.2.21, |
Filling |
a mould in an autoclave s |
||
1- |
the |
autoclave, |
|
|
2- |
the |
hole |
for pouring, |
S4' |
3- |
the |
lid j |
|
|
4- |
the |
mould; |
|
|
5- |
valves. |
|
|
Foundry Department |
"Casting |
defects and |
Dr. V. Bastrakov. |
measures of |
their prevention” |
Flushing with an inert gas is the most common tec hniques of gas removal* Inert gases such as chlorine , nitrogen, or argon arc widely used in practice. Chlorine, interacting with aluminium or ..;agnesium (this method is mainly used for degassing aluminium and magnesium alloys), forms gaseous AlCl^ or М^С12 neutral to the metal.
The gases are bubbled from graphite pipes directly throu
gh the metal. |
Due to the pressure of the dissolved |
gas |
( usually hydrogen ) within each inert gas bubble is |
zero |
|
any dissolved |
gas migrates readily to the bubble where it |
|
is collected |
and taken out to the metal surface. |
|
Last time solid degassers are also widely used for this purpose. For example, hoxahhlorinethane (C2 Clg) is used to give the flushing action to aluminium and. mag nesium alloys i
2 A1 + 3 CgClg |
-----► ?C2C14 |
+ 2 A lC lj |
||
(liqu id)(solid) |
(gas) |
(gas) |
||
In steelmaking practice, |
the |
CO from the carbon boil |
||
( FeO $ C - —» Fe |
00 |
) acts as an inert |
gas to flush |
hydrogen from the metal.
However, taking into account the condition of the formation of a bubble from dissolved gases, according to
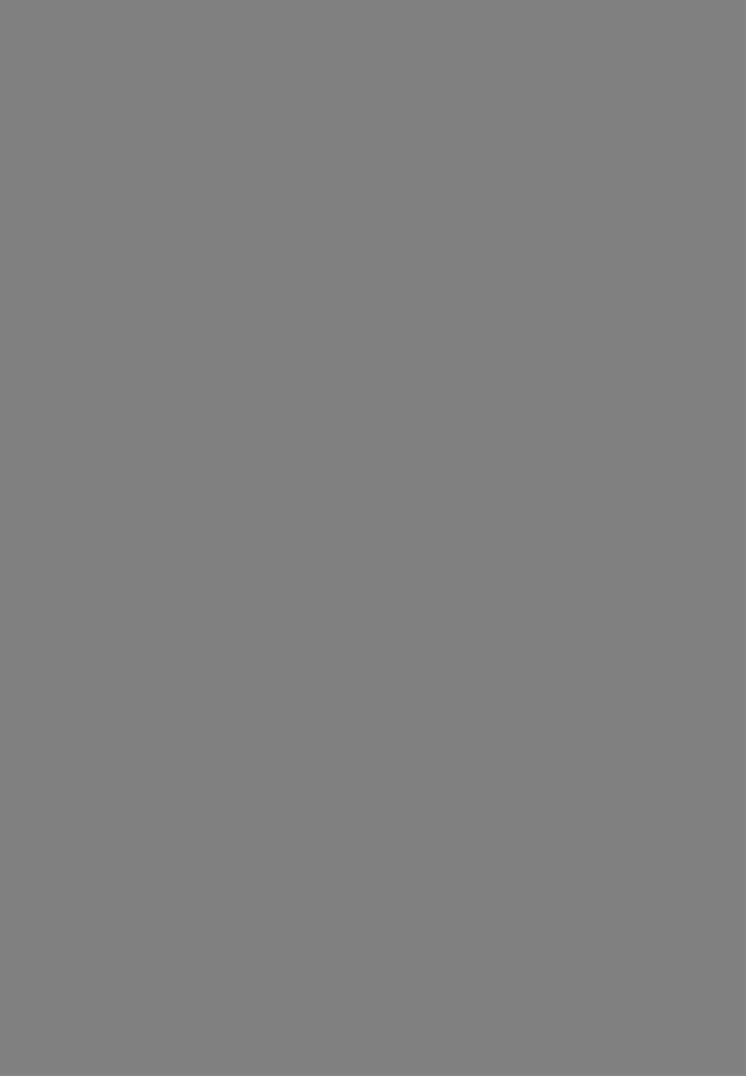
2- Measures improving quality of a mould.
The majority "blow boles is formed an a result of unsatisfactory quality of moulds or some deviations from a technological process of their production.
It should be noted that gas holes as a result of the unquality preparation of a mould especially often oc cur in cast iron and non-ferrous castings. Steel cast ings are subjected to such blow holes in a less degree,as
steel is poured with less overheating and the strong solid skin of the metal, preventing gases of the mould from the penetration into the casting, is formed very quickly at po uring the steel.
Shrinlaage cavities.
Shrinkage is one of the most important characteris tics of alloys which hardly influences on casting quality.
This is the property of metals and alloys to change their volume on solidification and cooling. In nearly a ll cases, solidification and cooling the casting are accoipanied by the reduction of its volume. Usually shrinkage occurs in three stages, in.the molten metal before solidifying(liquid contraction)} in solidifying ( solidification shrinkage )j and in the solid metal during cooling the metal upto room tenperatura ( solid contraction )•
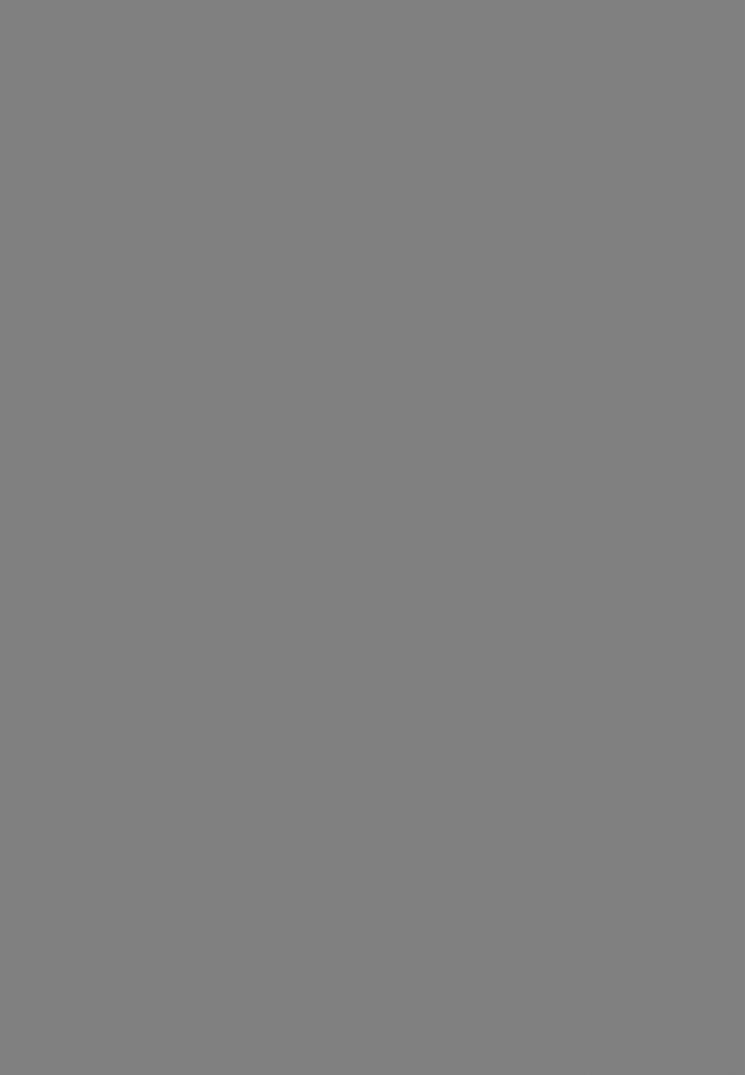