
3218
.pdf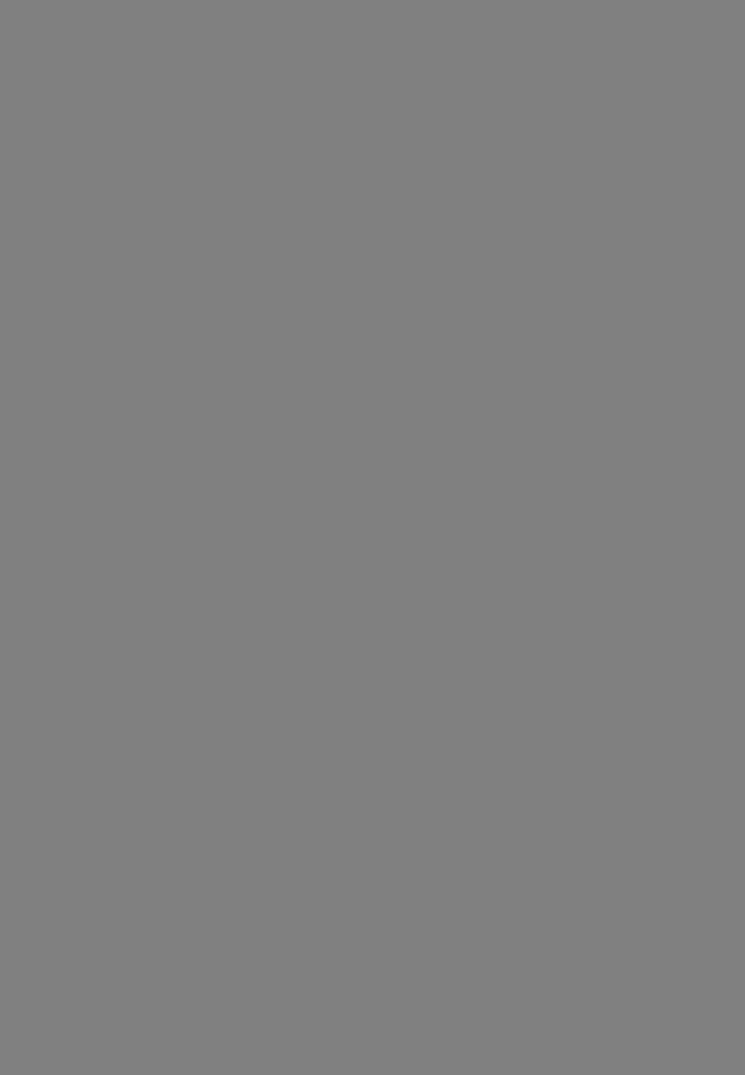
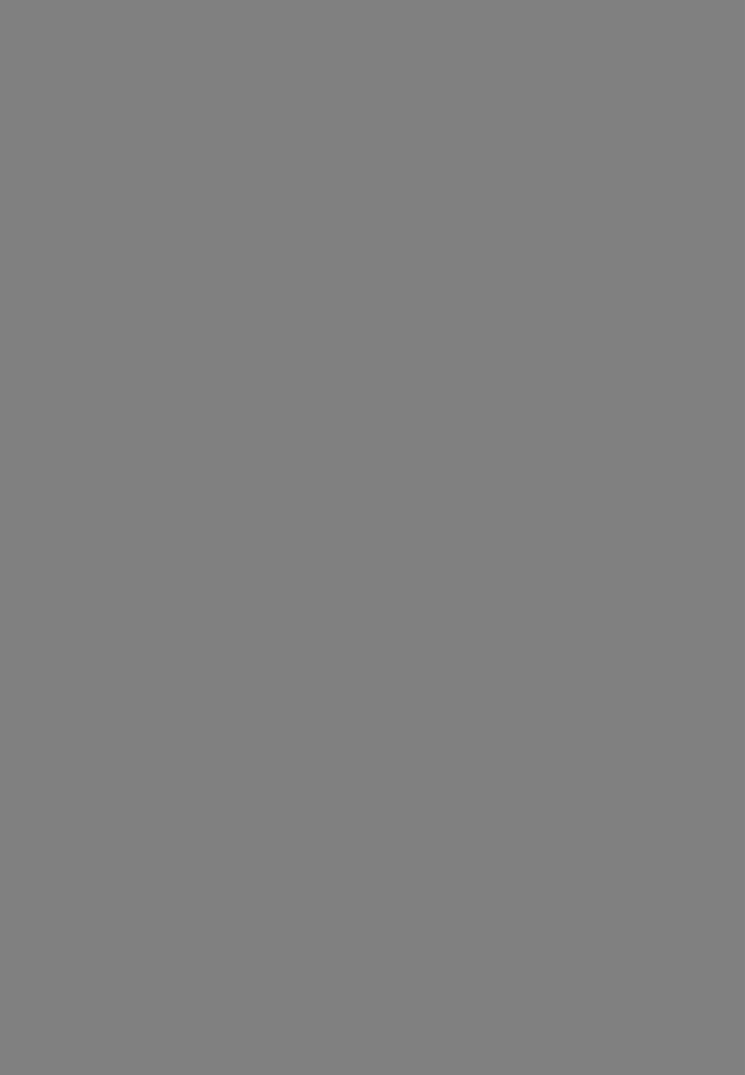
The outer or static pressure w ill promote the penetration making easier moving the metal in narrow capillaries*
But when the molten metal does not wet the high heated moulding sand its penetration into mould pores can begin
only under the condition that outer pressure ea©rted by the
metal exceeds a certain critica l value*
As the penetration is also limited by the pressure of gases
and steams which are elided during the pouring of metal at
the heating of a moulding mixture, |
the critica l |
pressure |
|||
must involve the gas pressure* |
In |
such a way at |
the moment |
||
when the metal pressure |
( Pm ) exceeds the sum of the gas |
||||
(PО) and capillary (P ) |
pressures the penetration of the |
||||
metal into pores of the |
mixture |
w ill take place* |
|
||
Consequently, the mechanical |
burning-on formation begins at |
||||
the moment whenpthe conditionals |
fu lfille d : |
|
|||
m |
g |
о" |
|
|
|
flhis metal pressure |
is |
called |
’’critica l pressure” and |
it is determined as the static pressure of a liquid metal
column of the |
hight (Hor) above |
an appropriate capillary: |
|
|
Hcr |
. JL + 'Pc |
|
|
|
m |
|
where, |
m - |
specific weight of the liquid metal, |
|
The oapillary pressure may be estimated for an appro |
|||
priate |
capillary in accordance |
with Gurgen*s formula: |
cos 0*
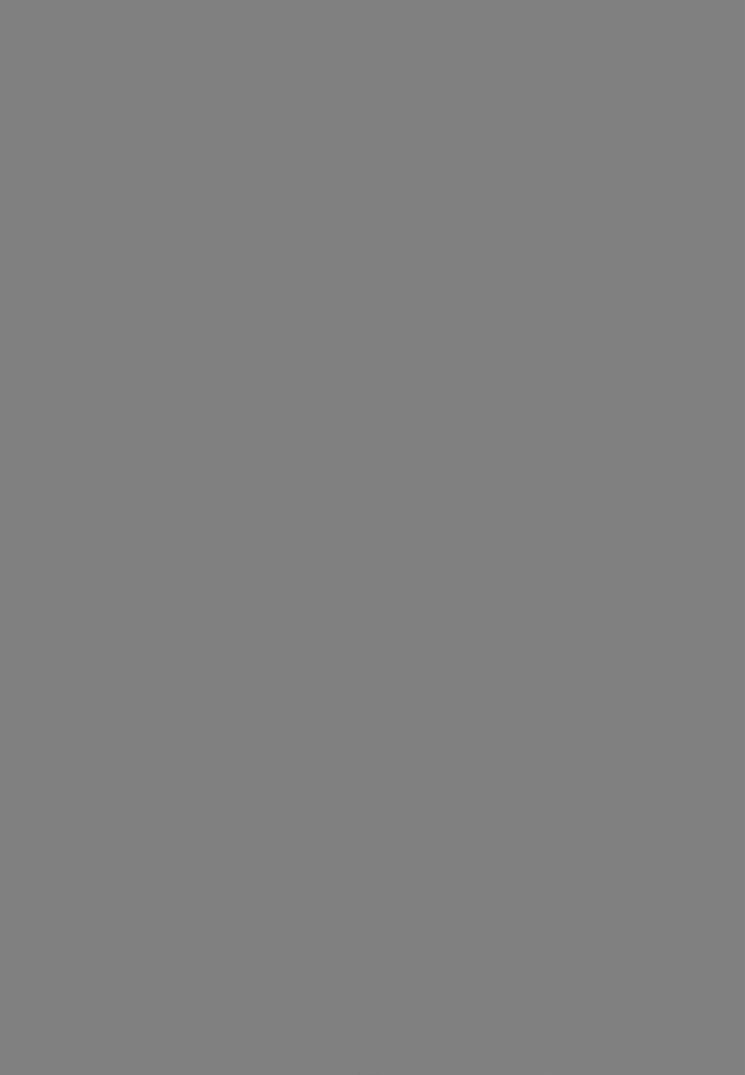
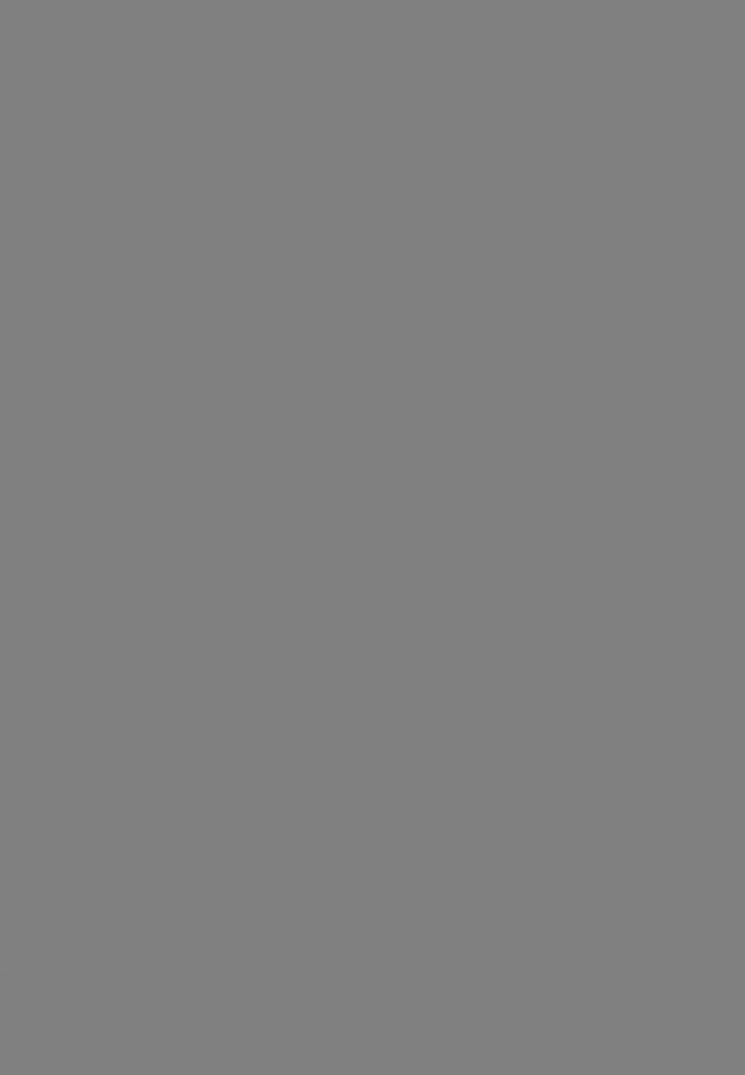
3- by increasing the |
compactness of moulding sands, |
4 - -by using special |
coatings and paints* |
At the first period of time after pouring the r&te of
metal penetration into mould poresis determined by the
гаЬе of face heating to the liquidus temperature* I f on
this stage quick cooling the outer layer of a casting is
carried out its surface w ill be clean evenly repeating
macroroughness of the mould surface layer* The increase
of the metal cooling rate, especially in the fir s t -per5k
of time, is very important and oan be approached by using mould mixtures of higher heat conductivity and heat accuai
lating ability* Such mixtures, as chromium-magnesite and
chromium iron-stone,promote the quick removal of a metal overheat and formation of a solid skin of metal on the
bounary |
’’metal-mould"* This solid metal crust |
counteract |
|
tfeb. steel penetration into mould pores beoause |
it |
has been |
|
formed |
before the moment when a metal pressure |
is |
inoroase |
Up to the cad.tical value*
For example, according to the data of prof# Balandin,G.F,
(13), the depth of metal penetration into mould pores was equal to 0.55mm,” when steel 20xl3HA has been poured into
a clay sand with the coefficient of the heat accumulating ability b_ * VAC/? * 1380 joule /m^.seo* degree),
and it was 0.1 mm in case of |
pouring |
the |
steel into a chr |
omium-magnesite mixture with |
liquid |
glass |
(bs*3350 joule/ |
3 |
|
|
|
(m" •sec. degree). |
|
|
|
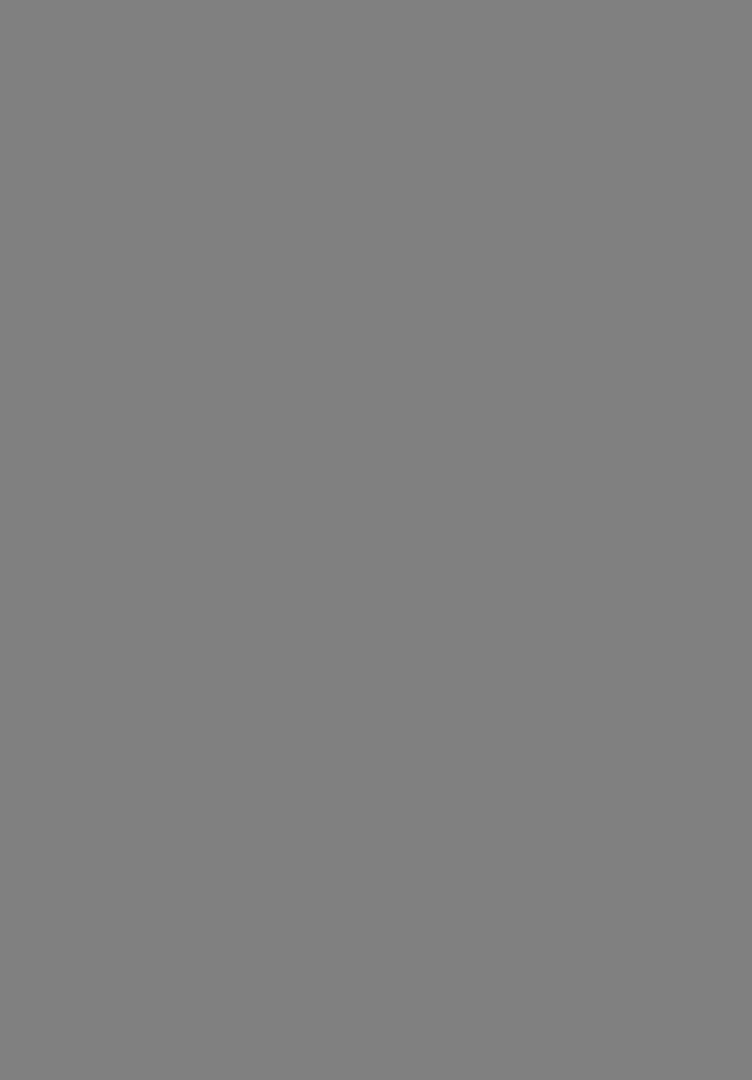
The depth of metal penetration into pores may be deci by the addition of a fine anti-burning -onrefractory matei
into mixtures*
Having a large surface area the combination of fine and o<
grainy gives the higher heat accumulating ability at lov heat conductivitjr.
Prom one hand, the powdered material decreases the porosil
of |
face, but on the other hand, it |
increases the compactne |
of |
the mould mixture due to $Jjat |
heat expansion of the |
facing mixture increases without spoiling, in general, its mechanical properties*
At the manufacture of heavy |
steel castings the folloi |
||||||
ing powdered materials are added |
to facing |
sands» |
|||||
1- 15-30% powdered quartz |
(^94.5% |
SiOg): |
|||||
2- |
up |
to |
25% |
zircon |
sand, |
|
|
3- |
up |
to |
10% |
silvery |
crystalline graphite having high |
thermo-chemical resistance up to the temperature
1800 °C.
In Fig.2.12 results |
of experiments of studyind the influen |
||
ce of the amount of |
quartz dust on the depth of the burnin |
||
on penetration are shown (14). |
|
||
In order tp^prevent burning-on on iron castings coal |
|||
dust is |
added into |
facing and common mixtures. |
It is to |
be able |
to isolate |
not less than 30% volatile |
substances |
and to contain not more than 11% ashes, 2% sulpher, c.n-1
12% moisture. Its amount in mixture and dispersity cfril]
Кь
( & )
Pig.2.11.conditions of the obtaining of middle carbon steel
castings without mechanical burning-on:
b в-the coefficient of heat accumulating ability,
R• the reduced radius of the casting cross-sect- ion,
-the relation of a thickness of coating to the reduced radius of the casting cross-section.
Foundary Department |
"Casting defects and |
Dr. V. Bastrakov |
measures of the^r^jpevent- |
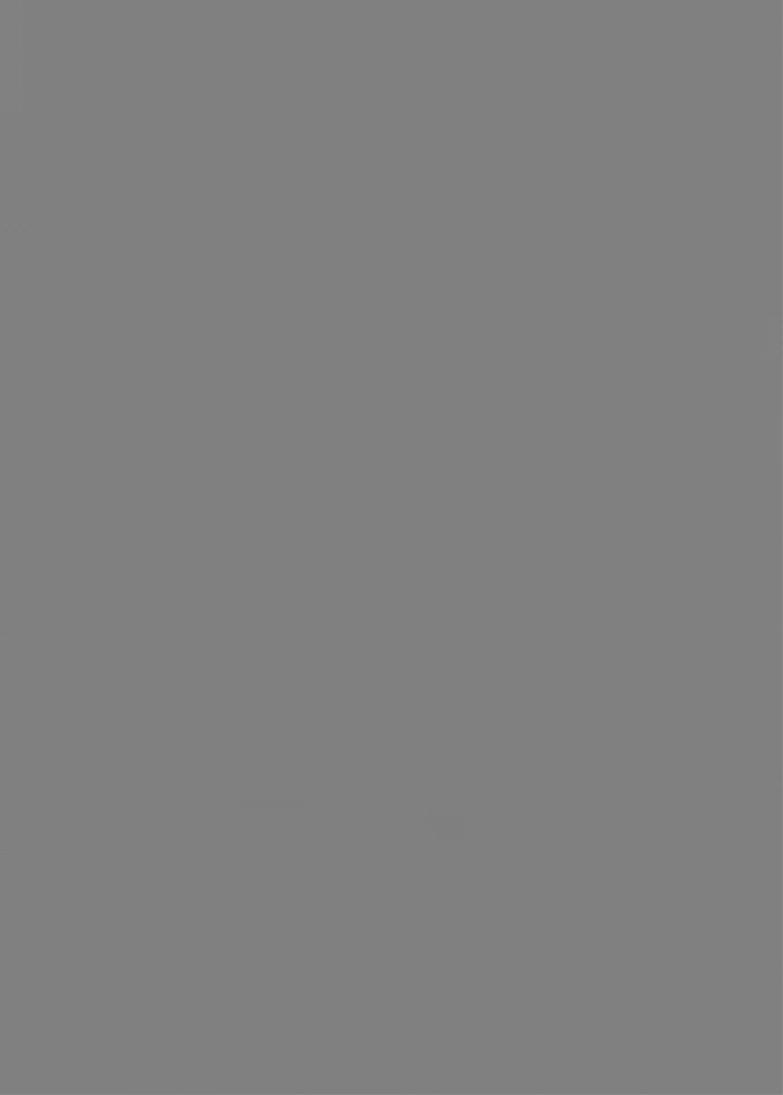