
1495
.pdfНа абсорбцию
На абсорбцию
Вода Вода НаДСЖ
Фильтровая £ жидкость
НаДСЖ а
ЕЯ
ЕЯ
е я |
г_ |
ЕЯ |
|
_ЕЙ_ |
|
ЕЯ |
(— |
|
I |
|
I__ |
j £
Известковое
молоко
Пар
Пар
Пар ЕЯ ЕЯ
-------6 На "белое море"
И 1----- к
Рис. 1.41. Схема отделения дистилляции фильтровой жидкости:
дистиллер; 2 — теплообменник дистилляции; 3 — конденсатор-холодильник газа дистилляции; 4 — смеситель; 5 — первый испаритель; 6 — вто рой испаритель; 7 — пароэжектор
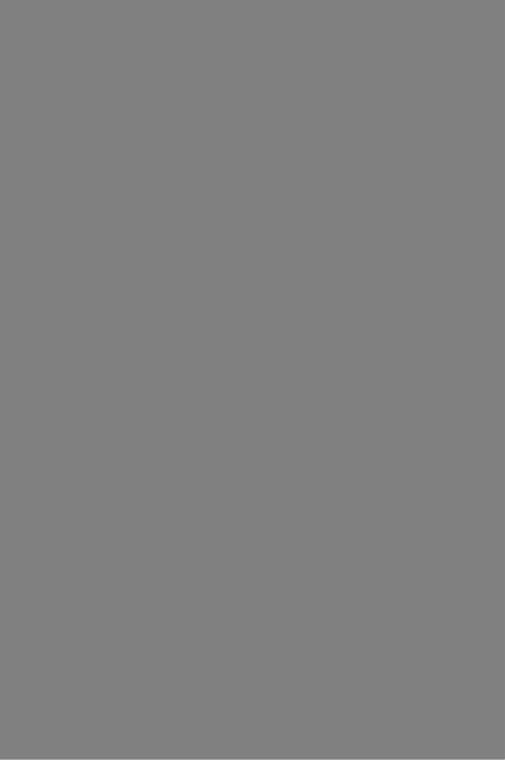
ключительной стадией в производстве технического карбоната натрия. Он сводится к термическому разложению гидрокарбонага натрия до карбоната:
2NaHC03 —у Na2C03 + СО2 + Н2О
Влажный технический гидрокарбонат, поступающий на процесс кальцинации, имеет следующий состав (%, масс.): NaHC03 — 76—84; Na2C03 — 2—3; NaCl — 0,2—0,4; NH4HCO3 — 1—2; (ЫН^СОз— 1; Н20 — 14—20. Наличие влаги в гидрокарбонате натрия снижает сыпу честь. Влага, представляющая собой насыщенный раствор гидрокарбо ната натрия, в процессе кальцинации, а именно при контакте с горячей поверхностью, интенсивно испаряется. В результате выделяющаяся твердая фаза, кристаллизуясь, образует плотно прилипающую к по верхности кальцинатора корку, называемую в производстве «козел». С целью исключения этого явления в производстве исходный влажный гидрокарбонат натрия перед подачей в кальцинатор смешивают с су хим карбонатом натрия (содой). При этом образуется новая твердая фа за— трона — ЫаНСОз'КагСОз^НгО. В процессе смешения свободная влага переходит в кристаллизационную, и продукт становится сыпучим:
NaHCOj +Na2C 03 + 2H20->NaHC03-Na2C03-2H20
Термографическими исследованиями установлено, что трона в процессе нагревания при 111° С теряет кристаллизационную воду:
3(Na2C03-NaHC03-2H20 ) -> Na2C03-3NaHC0 3 + 2Na2C03 + 6Н20
а с достижением температуры 127° С происходит разложение двой ной соли по реакции
2(Na2C03-3NaHC0 3) = 5Na2C 03 + 3C02 + ЗН20
являющейся наиболее медленной, лимитирующей процесс кальцинации. Содержащийся в исходной смеси карбамат натрия-аммония легко
разлагается в присутствии водяного пара:
2NH2COONa + Н20 = Na2C 03 + 2NH3 + С 02
В данном процессе выделяется около половины общего количест ва аммиака, а остальное количество аммиака выделяется в процессе разложения гидрокарбоната натрия, содержащегося в троне.
Карбонат аммония разлагается и в процессе нагревания:
(NH4)2C 03 ->2NH3 + С02 + Н20
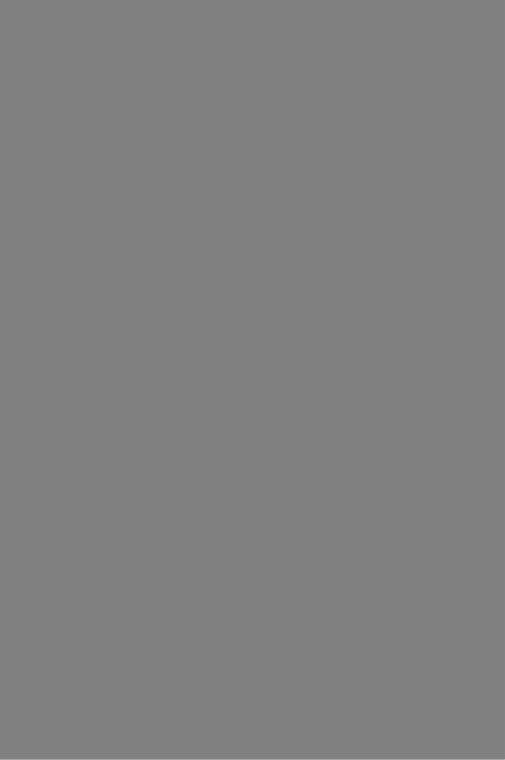
Рис. 1.42. Схема отделения кальцинации:
1— паровой кальцинатор; 2 — питающий смеситель; 5, 15 — ячейковые питатели; 4, 10 — ленточ
ные транспортеры; |
5 — вибропитатель; б — печка-бункер; 7 — плужюовый сбрасыватель; 8, 9, 14, |
16— транспортеры; |
11 — циклон; 12 — коллектор газа кальцинации; 13 — сепаратор; 17 — сборник |
конденсата; 18 — центробежные насосы; 19 — сборник слабой жидкости; 20 — холодильник газа кальцинации; 21 — редукционная охладительная установка (РОУ); 22 — промыватель газа кальци нации; 23 — сборник промывной жидкости
вателе 22. Перед промывагелем газы кальцинации охлаждаются в холодильнике 20.
На процесс орошения в коллектор газа кальцинации подают так называемую слабую жидкость, образующуюся в процессе конденса ции водяных паров в холодильнике газов кальцинации 20. Жидкость, соприкасаясь с газом, поглощает частично аммиак и пыль карбоната
натрия, стекая после |
этого |
в сборник |
19. |
В холодильнике |
20 газ |
проходит |
сверху вниз по межтрубному |
пространству, а в трубах противотоком движется охлаждающая вода. С целью исключения закристаллизовывания трубок холодильника и лучшей промывки газа от пыли карбоната натрия межтрубное про странство орошается неконцентрированной жидкостью. В промывателе 22 с целью дополнительного охлаждения и полной отмывки от карбоната натрия и аммиака газ орошается водой.
Кальцинатор обогревается водяным паром высокого давления. Пе ред подачей в кальцинатор он проходит редукционную охладитель ную установку (РОУ), в которой температура его снижения до 270° С, а давление — до 3 МПа. В трубках кальцинатора пар конден сируется, отдавая теплоту кальцинируемому материалу. Конденсат из кальцинатора выводится в сборник конденсата 17 и далее в расши рители, где преобразуется в пар низкого давления.
Технологическая схема отделения кальцинации карбоната натрия при использовании печей карбоната натрия с ретурным питанием аналогична рассмотренной. При использовании печей с безретурным питанием исходный влажный гидрокарбонат натрия подается в бара бан печи специальным забрасывателем. Смешение его с карбонатом натрия производится внутри печи, поэтому из технологической схе мы исключается смеситель и упрощается транспортирование карбо ната натрия.
Одним из основных аппаратов в производстве карбоната натрия является печь карбоната натрия. На рис. 1.43 показана огневая печь карбоната натрия с безретурным питанием. Топочные газы, получае мые в топке 1 путем сжигания твердого, жидкого или газообразного топлива, обогревают снаружи вращающийся барабан 2 печи карбона та натрия, изготовленный из стали 3. С обоих концов барабан имеет цилиндрические горловины 13, присоединяемые к барабану через ко нические царги 10, которые снабжены ободами 8 с опорными банда жами 9, на которых барабан опирается с обеих сторон на стальные ролики 4 с подшипниками J. Задние ролики снабжены ребордами, фиксирующими положение конца барабана. Привод барабана осуще ствляется через венцовую шестерню 12 от электродвигателя через редуктор. Торцевая сторона горловины задней загрузочной камеры закрыта крышкой с центральным отверстием для ввода в печь вы грузочного шнека 14. Горловина передней части печи входит в непо движную загрузочную камеру. Уплотнение горловины сальниковое.
Загрузочная камера имеет штуцер для отвода газов, образующих ся в процессе кальцинации. К фронтальной стенке загрузочной каме-
Рис. 1.43. Безретурная печь для обжига карбоната натрия:
/ — топка: 2 — барабан печи; 3 — горелка; 4 — ролики; 5 — подшипники; б — загрузочная |
камера; |
||
7— забрасыватель гидрокарбоната; 8 — ободы; 9 — опорные |
бандажи; |
10 — коническая |
царга; |
11 — цепь; 12 — венцовая шестерня; 13 — цилиндрическая |
горловина; |
14 — выгрузной |
шнек |
ры снаружи крепится забрасыватель гидрокарбоната натрия, а с внутренней стороны — цепь 11 для очистки внутренней поверхности барабана от возможных отложений карбоната натрия, а также для перемешивания и дробления комков карбоната натрия. Загрузка гид рокарбоната натрия производится забрасывателем 7.
В последние годы в процессе кальцинации начали применять и паровые кальцинаторы. В процессе кальцинации в качестве теплоно сителя используют пар высокого давления, что дает возможность со здать аппараты с развитой поверхностью теплообмена, которая до
стигает 2500—3000 м2, |
в |
то время как |
в печах |
карбоната |
натрия — лишь 150—200 |
м2. |
Однако высокая |
стоимость |
пара по |
сравнению с жидким и газообразным топливом экономически не по зволяет применять паровые кальцинаторы.
В качестве обобщения изложенного материала по отдельным раз делам призводства на рис. 1.44 приведена принципиальная схема по лучения карбоната натрия.
Согласно схеме, очищенный рассол из сборника 1 подается цент робежным насосом 2 в напорную емкость 3, постоянный уровень рассола в которой поддерживается поплавковым регулятором 4. Из напорной емкости рассол распределяется на три параллельных потока.
Первый (основной) поток, составляющий примерно 75% всего расходуемого рассола, поступает во второй промыватель газа колонн 5. Далее поток проходит последовательно через все шесть царг промывателя сверху вниз навстречу хвостовым газам, поступающим под давлением 140—150 мм рт. ст. в нижнюю часть аппарата из первого промывателя газа карбонизационных колонн 25. Во втором промывателе газа колонн 5 рассол абсорбирует аммиак и частично диоксид углерода из газов, после чего газ, пройдя ловушку б, орошаемую во дой (для улавливания брызг рассола), выбрасывается в атмосферу.
Второй поток, составляющий около 15% от всего потребляемо го рассола, поступает во вторую барботажную секцию (считая сверху) промывателя воздуха фильтров 7, в котором улавливается аммиак из воздуха вакуум-фильтров 34. Промыватель воздуха фи льтров имеет четыре барботажные тарелки и работает под разре жением 350—380 мм рт. ст. Рассол проходит через аппарат сверху вниз, а воздух — снизу вверх, после чего отсасывается вакуум-на сосом 12 и выпускается в атмосферу.
Третий поток в количестве около 10% от общего расхода рассола поступает во вторую сверху барботажную секцию промывателя газа абсорции Р, имеющую также четыре барботажные тарелки. Аппарат работает при разрежении 250—280 мм рт. ст. В нем улавливаются остатки аммиака, содержащиеся в хвостовых газах станции абсор ции. Газ поступает в нижнюю часть промывателя 9 из первого аб сорбера 15 и движется вверх навстречу потоку рассола.
На выходе из промывателя газ содержит до 70% диоксида угле рода. После брызгоотделителя 10 он подается вакуум-насосом 11 в холодильник газа содовых печей 41, в котором объединяется с основным потоком концентрированного диоксида углерода, использу емого для карбонизации аммонизированного рассола. В верхние барботажные секции этих промывателей для улавливания брызг рассола подают воду, которую затем направляют в отстойники. Операция проводится с целью предупреждения отложения солей (инкрустации) в трубопроводах, по которым воздух и газ из этих двух промывате лей поступают в вакуум-насосы.
Второй поток рассола, выходящий из промывателя воздуха филь тров 7, смешивается с третьим потоком рассола, выходящим из про мывателя газа абсорбции 9, и по U-образной трубе стекает в третью сверху барботажную бочку второго промывателя газа колонны 5, где он соединяется с основным потоком рассола.
Выходящий из второго промывателя газа колонн J рассол посту пает самотеком по U-образной трубе в верхнюю барботажную сек цию первого абсорбера 15. Абсорбер имеет шесть барботажных таре лок и работает при разрежении 200—250 мм рт. ст.
В первом абсорбере происходит абсорбция аммиака и частично диоксида углерода из газа, поступающего из второго абсорбера 16. В первый абсорбер поступает также газ со станции переработки так называемых «слабых жидкостей». Первый абсорбер, как и все аппа раты станции абсорбции, работает по принципу противотока. После первого абсорбера рассол содержит 70 н.д NH3 и 24 н.д. CO*'.
Вследствие экзотермичности реакции поглощения аммиака темпе ратура рассола в первом абсорбере поднимается до 70° С. Поэтому выходящий из первого абсорбера аммонизированный рассол поступа-
Рис. 1.44. Схема производства карбоната натрия по аммиачному способу:
1, 20, 38, 42 и 68 — сборники; 2, 21, 23, 27, 37, 43, 44, 58, 67 и 80— центробежные насосы; 3, 13, 18, 35, 40, 46, 51, 60, 69— напорные емкости; 4 — поплавковый регулятор; 11, 50, 70, 71 — поплав ковые регуляторы; 5 — второй промыватель газа карбонизационных колонн; 6 — ловушка-уловитель;
7— промыватель воздуха фильтров; |
8 — холодильник газа дистилляции; |
9 — промыватель |
газа аб |
|
сорбции; 10 — брызгоуловители; 11 |
и 12 — вакуум-насосы; 14, |
17, |
78 — регуляторы |
подачи; |
15 — первый абсорбер; 16 — второй |
абсорбер; 19 — оросительные |
холодильники; 22 — емкость; |
24 — колонна предварительной карбонизации; 25 — первый промыватель газа карбонизационных ко лонн; 26 — сборник предкарбонизованной жидкости; 28 — осадительная карбонизационная колонна;
29, 30 и 31 — компрессоры; 32 — мерные |
колонны; 33 — корыто; 34 — вакуум-фильтр; 36, |
62 и |
64 — транспортеры; 39— промыватель газа |
содовых печей; 41 — холодильник газа содовых |
печей; |
45 — холодильник газа малой дистилляции; 47 — конденсатор малой дистилляции; 48 — малый дис
тиллер; 49 — холодильник; 52 — конденсатор дистилляции; 53 — газоотделитель; |
54 — теплообмен |
|||||||
ник |
дистилляции; |
55 — дистиллер; |
56 — испаритель; |
57 — пескоуловитель; |
59 — смеситель; |
|||
61 — элеватор; 63 — циклон; 65 — вертикальный смеситель; |
66 — содовая печь; |
72 — приемный |
||||||
бункер; 73 — вращающееся сито; |
74 — вибрационное сито; |
75 — подогреватель; 76 — гаситель изве |
||||||
сти; |
77— шаровая |
мельница мелкого |
помола; 79 — сборник |
шлама; 81 — бункер; |
82 — ковшовый |
|||
конвейер; 83 — электрофильтр; |
84 — загрузочное устройство; 85 — ячейковый |
выгружатель; |
86 — кольцевой транспортер; 87 — «улита»; 88 — вентилятор; 89 — известково-обжигательная печь
ет самотеком в оросительные холодильники (устанавливаемые обыч но вне здания), в которых он охлаждается водой до 30° С.
Охлажденный аммонизированный рассол поступает самотеком в верхнюю барботажную секцию второго абсорбера 16. Число барботажных тарелок во втором абсорбере — три. Рассол проходит после довательно все три барботажные бочки сверху вниз. При этом про исходит абсорбция рассолом аммиака и частично диоксида углерода из газа, поступающего со станции дистилляции в нижнюю секцию второго абсорбера и проходящего через аппарат снизу вверх.
Потери аммиака в производстве компенсируются добавкой во дных растворов аммиака. При этом 20%-ные водные растворы из за водских хранилищ подаются центробежным насосом в напорную ем кость 13, откуда через регулятор подачи 14 поступают в верхнюю барботажную секцию второго абсорбера 16.
Вследствие выделения значительного количества теплоты в процес се поглощения аммиака рассолом температура последнего во втором абсорбере также повышается до 70° С. Поэтому выходящий из второго абсорбера аммонизированный рассол, содержащий 100— 102 н.д. NH3 и 35—37 н.д. СО*', проходит самотеком через охлаждаемые водой ороси тельные холодильники 19, в которых температура рассола снижается до 30—35°С. Охлажденный аммонизированный рассол далее поступает в запасные сборники 20, откуда он направляется на карбонизацию.
С целью предохранения аппаратуры станции абсорбции от корро зии в первый абсорбер подается в небольших количествах раствор сульфида натрия (из расчета 0,75 кг 62%-ного сульфида натрия на 1 т карбоната натрия). Раствор сульфида натрия готовится в емкости 22 на очищенном рассоле с добавкой конденсата, после чего полу ченный раствор перекачивают центробежным насосом 23 в напорную емкость 18, из которой с помощью регулятора подачи 17 он дозиру ется в трубопровод, подающий рассол из второго промывателя газа колонн 5 в первый абсорбер 15.
Процесс карбонизации аммонизированного рассола производят в три стадии: в колонне предварительной карбонизации 24, в первом промывателе газа колонн 25 и осадительных карбонизационных ко лоннах 28, в которых в основном происходит осаждение гидрокар боната натрия. После трех-четырех дней работы в осадительных колоннах накапливается гидрокарбонат и их поочередно переключа ют на промывку. Промывка колонн производится пропусканием че рез них аммонизированного рассола с одновременной подачей в колонну диоксида углерода известково-обжигательных печей. Таким образом, промывка колонн осуществляется в процессе предварите льной карбонизации. В качестве колонны предварительной карбо низации поочередно используется переключаемая на промывку оса дительная колонна.
92