
682
.pdfТаблица 1.1
Условия работы конвейера в зависимости от характеристики места установки
Условия |
|
работы |
Характеристика места установки |
конвейера |
|
|
|
|
Чистое, сухое, отапливаемое, хорошо освещенное помещение, |
Легкие |
отсутствует абразивная пыль, конвейер доступен для обслужи- |
|
вания, осмотра и ремонта |
|
|
|
Отапливаемое помещение, небольшое количество абразивной |
Средние |
пыли, временами влажный воздух, средние освещенность и до- |
|
ступность для обслуживания |
|
|
|
Неотапливаемое помещение, наличие большого количества аб- |
Тяжелые |
разивной пыли или повышенная влажность воздуха, плохие |
|
освещенность и доступность для обслуживания |
|
|
Весьма |
Очень пыльная атмосфера и наличие факторов, вредно влияю- |
тяжелые |
щих на работу конвейера |
|
|
Таблица 1.2
Дополнительные параметры, определяющие условия работы
|
|
|
Условия работы |
|
||
Параметр |
|
|
|
|
||
Легкие |
Средние |
Тяжелые |
Весьма |
|||
|
|
|||||
|
|
тяжелые |
||||
|
|
|
|
|
||
Время работы в сутки, ч |
До 6 |
6…12 |
12…18 |
Св.18 |
||
|
|
|
|
|
|
|
Свойства груза: |
|
|
|
|
|
|
1) насыпная плотность, т/м3 |
До 0,6 |
0,6…1,1 |
1,1…2,0 |
Св.2,0 |
||
2) размер куска, мм |
До 20 |
20…60 |
60…160 |
Св.160 |
||
|
|
|
|
|
||
3) абразивность и коррозион- |
нет |
средние |
средние |
повы- |
||
ность |
|
шенные |
||||
|
|
|
|
|||
|
|
|
|
|
||
Влажность воздуха, % |
До 50 |
50…65 |
65…90 |
Св. 90 |
||
|
|
|
|
|
||
Запыленность воздуха, кг/м3 |
До 10 |
10…100 |
100…150 |
Св. 150 |
||
Температура |
окружающей |
+5…+25 |
0…+30 |
–20…+30 |
–40…+40 |
|
среды, °С |
|
|
|
|
|
Режимы работы (табл. 1.3) учитывают при расчете элементов конвейеров на прочность и долговечность.
11

Таблица 1.3
Режимы работы конвейеров в зависимости от классов использования
Режим |
|
Класс использования конвейера |
|
||
|
|
|
|
||
работы |
По времени |
По производи- |
По грузоподъ- |
По натяжению |
|
|
|
тельности |
емности |
тягового органа |
|
ВЛ |
В1 |
П1, П2 |
Н1, Н2 |
Ц1 |
|
Л |
В1 |
П3, |
Н3, |
Ц2, |
|
В2 |
П1, П2 |
Н1, Н2 |
Ц1, Ц2 |
||
|
|||||
С |
В3 |
П1, П2 |
Н1,Н2 |
Ц1, Ц2 |
|
Т |
В4 |
П1, П2, |
Н1, Н2, |
Ц1, Ц2, |
|
В5 |
П1 |
Н1 |
Ц1 |
||
|
|||||
ВТ |
В5 |
П2, П3 |
Н2, Н3 |
Ц2, Ц3 |
|
|
|
|
|
|
Различают пять режимов работы: весьма легкий (ВЛ), легкий (Л), средний (С), тяжелый (Т) и весьма тяжелый (ВТ).
Режимы работы определяются сочетанием классов использования конвейеров по времени (В), производительности (П), грузоподъемности (Н) и натяжению тягового органа (Ц).
В – классы использования конвейеров по времени «В» (табл. 1.4) характеризуются продолжительностью их работы в сутках или в году.
|
|
|
|
|
Таблица 1.4 |
|
Класс использования конвейеров по времени |
||||||
|
|
|
|
|
|
|
Класс использо- |
|
|
|
|
|
|
вания конвейе- |
В1 |
В2 |
В3 |
В4 |
|
В5 |
ров по времени |
|
|
|
|
|
|
|
|
|
|
|
|
|
Время фактиче- |
|
|
|
|
|
|
ское работы кон- |
до 5 |
5…7 |
7…16 |
16…24 |
|
24 |
вейероввсутках,ч |
|
|
|
|
|
|
|
|
|
|
|
|
|
Время фактиче- |
|
|
|
|
|
|
ское работы кон- |
до1600 |
1600...2500 |
2500…4000 |
4000…6300 |
6300…8000 |
|
вейеров в году, ч |
|
|
|
|
|
|
|
|
|
|
|
|
|
П – класс использования конвейера по производительности характеризуется общим коэффициентом загрузки:
Кп = Qc ,
Qmax
12
где Qc и Qmax – средняя и максимальная производительность конвейера.
Н – класс использования конвейера (табл. 1.5) по грузоподъемности характеризуется отношением максимальной фактической нагрузки на грузонесущий элемент Gф к его номинальной грузоподъемной нагрузке Gн:
|
К |
|
= |
Gф |
. |
|
|
н |
|
|
|||
|
|
|
G |
|
||
|
|
|
|
|
||
|
|
|
|
н |
|
|
|
|
|
|
|
|
Таблица 1.5 |
|
|
|
|
|
||
Н1 |
|
|
Н2 |
Н3 |
||
|
|
|
||||
не выше 0,5 |
0,5…0,63 |
0,63…1,0 |
Ц – класс использования конвейера по нагружению (натяжению) тягового элемента (табл. 1.6) определяется в зависимости от отношения максимального фактического натяжения Sф к допуска-
емомуSd :
|
К |
|
= |
Sф |
. |
|
|
Ц |
|
|
|||
|
|
|
Sd |
|
||
|
|
|
|
|
||
|
|
|
|
|
|
Таблица 1.6 |
|
|
|
|
|
||
Ц1 |
|
|
Ц2 |
Ц3 |
||
Не более 0,63 |
0,63…0,8 |
0,8…1,0 |
Контрольные вопросы
1.Область применения МНТ, классификация.
2.Основные свойства штучных и сыпучих грузов.
3.Характеристика тягового элемента МНТ.
4.Охарактеризуйте условия работы конвейеров.
5.Какие критерии определяют режимы работы конвейеров?
2. ОСНОВЫ ОБЩИХ РАСЧЕТОВ ТРАНСПОРТИРУЮЩИХ МАШИН
Поскольку транспортирующие машины (конвейеры) имеют некоторую конструктивную общность, то и формулы, используемые при расчетах, в ряде случаев носят общий характер.
Одни и те же по структуре формулы можно применять для определения одних и тех же параметров.
13
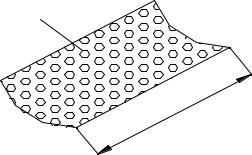
Общие расчеты транспортирующих машин предусматривают определение производительности, сил сопротивления движению рабочего органа на характерных участках трассы, динамических нагрузок в тяговом элементе, тягового усилия конвейера и мощности привода.
Вопросы расчетов динамических нагрузок в тяговом элементе и тягового усилия на характерных участках трассы конвейеров, а также суммарного тягового усилия будут рассмотрены детально в темах, посвященных конкретным типам МНТ.
2.1. Производительность машин непрерывного транспорта
Производительность конвейера – количество груза, перемещаемого в единицу времени.
Различают массовую – Q, т/ч; объемную – V, м3/ч и штучную – Z, шт./ч.
Эти величины связаны между собой следующей зависимостью:
Q = Vρ, |
(2.1) |
||
где ρ – плотность груза, т/м3. |
|
||
Q = |
meZ |
, |
(2.2) |
|
|||
1000 |
|
|
где me – масса единичного груза, кг; Z – штучная производительность.
|
Массовая |
производитель- |
||
q |
ность Q, т/ч: |
|
|
|
|
Q = 3,6qv, |
(2.3) |
||
|
где q – распределенная масса |
|||
м |
груза (рис. 2.1) (масса груза на |
|||
1 |
||||
|
одном метре |
конвейера), |
кг/м; |
|
Рис. 2.1. Груз на одном метре |
v – скорость конвейера, м/с. |
|
||
Если груз |
движется непре- |
|||
конвейера |
||||
рывным потоком и распределен |
||||
|
||||
равномерно на тяговом элементе, тогда: |
|
|
||
|
q = Fпρ, |
|
(2.4) |
14
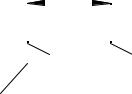
где Fп – площадь поперечного сечения груза; ρ – плотность материала, кг/м3.
Объемная производительность, V, м3/ч: |
|
|
|
|
|
|
|
|
|
|
|
||
V = 3600Fпv. |
(2.5) |
||||||||||||
Штучная производительность, Z, шт./ч: |
|
|
|
|
|
|
|
|
|
|
|
||
Z = |
3600vze |
, |
(2.6) |
||||||||||
|
|||||||||||||
|
a |
|
|
|
|
|
|
|
|
|
|
|
|
где ze – число штучных грузов (рис. 2.2) |
|
|
|
|
|
|
|
|
|
|
|
||
на одном несущем элементе (на подвеске, |
|
|
|
|
|
a |
|
|
|
||||
|
|
|
|
|
|
|
|
|
|
|
|||
люльке, полке); a – шаг несущих элемен- |
|
|
|
|
|
|
|
|
|
|
|
||
|
|
|
|
|
|
|
|
|
|
|
|||
тов, м. |
|
|
|
|
|
|
|
|
|
|
|
||
|
|
|
|
|
|
|
|
|
|
|
|||
Если груз движется отдельными ча- |
|
|
|
|
|
|
|
|
|
|
|
||
|
|
|
|
|
|
|
|
|
|
|
|||
стями массой mn (рис. 2.3, 2.4), то его |
Ze |
распределенная масса: |
|
Рис. 2.2. Несущие |
||
|
mn |
|
|
|
q = |
, |
(2.7) |
элементы конвейера |
|
|
|
|||
|
a |
|
|
где a – шаг между частями груза, м; mn – масса одной части груза, кг.
Если отдельная порция груза состоит из ze единичных грузов массой me , то:
mn = zeme, |
(2.8) |
||
где me – масса единичного груза, кг; ze |
– количество единичных |
||
грузов. |
|
||
Если груз перемещается в ковшах объемом iк, то: |
|||
i |
|
||
q = |
к |
ρΨ, |
(2.9) |
|
|||
a |
|
где iк – вместимость ковша, м3; a – шаг между ковшами, м; ρ – насыпная плотность груза, т/м3; Ψ – коэффициент заполнения
ковша материалом (Ψ < 1). |
|
Производительность пассажирских конвейеров: |
|
Z = 3600Bvzп , |
(2.10) |
где B – ширина настила, м; v– скорость настила, м/с. |
|
|
15 |
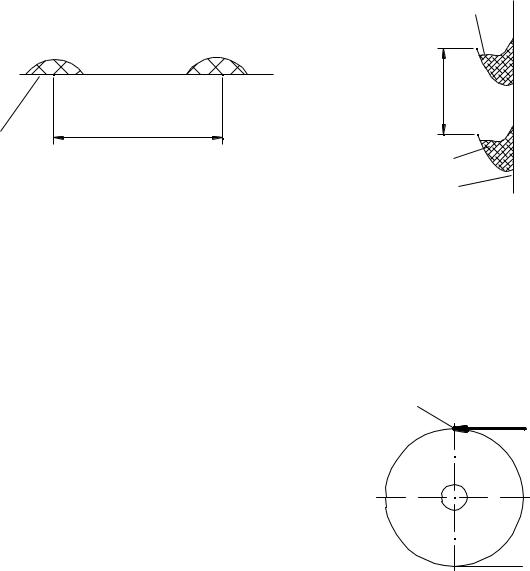
Обычно v в пределах 0,35–0,95 м/с, zп – число пассажиров на
1 м2 настила.
Ковш
|
a |
a |
|
mп |
mп |
|
|
|
Лента |
Рис. 2.3. Конвейер с грузом |
Рис. 2.4. Конвейер с грузом, |
в виде отдельных частей |
перемещаемым в ковшах |
2.2. Мощность приводного электродвигателя, выбор редуктора и тормоза
Следует различать мощность (Вт), передаваемую на тяговый элемент конвейера P0 и мощность на валу приводного элемента Pв .
Мощность, передаваемая на тяговый |
P0 |
|
||
элемент конвейера (рис. 2.5): |
|
W0 |
||
|
|
|||
P0 = W0v, |
(2.11) |
|
|
|
где W0 – окружное усилие на приводном |
|
|
||
элементе, Н; v – скорость тягового орга- |
|
|
||
на, м/с. |
|
|
|
|
Мощность на валу приводного эле- |
|
|
||
мента Pв больше мощности P0 |
из-за по- |
Рис. 2.5. К расчету |
||
терь в подшипниках вала, на изгиб тяго- |
||||
мощности на валу |
||||
вого элемента, а также сопротивления |
||||
приводного барабана |
||||
очистительных устройств (если они |
|
|
||
имеются): |
|
|
|
|
Pв |
= Wвv, |
|
(2.12) |
где Wв – окружное усилие на приводном элементе с учетом потерь на его валу, Н;
Мощность приводного двигателя:
P = |
kзPв |
, |
(2.13) |
|
|||
|
η |
|
|
0 |
|
|
16
где kз – коэффициент запаса (kз =1,15–1,25); η0 – КПД передаточного механизма.
η = η ηzп η |
доп |
, |
(2.14) |
|
0 |
р м |
|
|
|
где ηр – КПД редуктора; ηм |
– КПД муфты; zп |
– число муфт в |
приводе; ηдоп – КПД других передач (цепной, ременной и т.д.). В случае вращения рабочего органа конвейера:
P0 = T0ω, |
(2.15) |
где T0 – момент силы сопротивления вращению, Н м; ω – угловая скорость вращения рабочего органа, с–1.
Определив расчетом мощность P, выбирают по ней мощность приводного двигателя по условию Pдв ≥ P .
По мощности выбранного двигателя подбирают редуктор в соответствии с расчетным передаточным отношением привода i:
i = |
πnдв |
, |
(2.16) |
|
30ω |
||||
|
|
|
где nдв – частота вращения (номинальное значение) вала электро-
двигателя, об/мин; ω – угловая скорость приводных элементов (барабана, звездочки или канатоведущего шкива), с–1.
Если передаточное отношение привода больше, чем у стандартных редукторов, то рассчитывают передаточное отношение дополнительной передачи (цепной, зубчатой, ременной), соединяющей вал редуктора с валом тягового элемента конвейера или выходной вал редуктора с валом двигателя.
Тормоз для вертикальных и круто наклонных конвейеров выбирают по тормозному моменту (определяется расчетом). Тормоз препятствует опасному движению рабочего органа с грузом под действием силы тяжести груза при отключении электрического напряжения.
Контрольные вопросы
1.Производительность машин непрерывного транспорта (массовая, объемная, штучная).
2.Определение мощности приводного электродвигателя.
3.Выбор редуктора и тормоза.
17
3.ЛЕНТОЧНЫЕ КОНВЕЙЕРЫ
3.1.Общие сведения, классификация и устройство
Ленточные конвейеры являются наиболее распространенными машинами непрерывного транспорта и используются для транспортирования насыпных и штучных грузов во многих областях промышленного производства.
Ленточные конвейеры обеспечивают экономическую эффективность при перемещении грузов на расстояние до 14 км и грузообороте до 25 млн т в год. Длина конвейера может составлять 3–5 км для одной машины.
Значительным преимуществом ленточных конвейеров является высокая производительность (до 30000 т/ч), достигаемая при скорости движения ленты в пределах 6–8 м/с. Ленточные конвейеры имеют прямолинейные и комбинированные трассы, состоящие из горизонтальных и наклонных участков. Они отличаются простотой конструкции и удобством в эксплуатации, возможностью дистанционного контроля и автоматизации управления, а также высокой надежностью при работе в тяжелых условиях.
Недостатки ленточных конвейеров: высокая стоимость конвейерной ленты и опорных роликов; трудность транспортирования пылевидных, горячих и тяжелых штучных грузов; ограничение угла наклона трассы к горизонту (до 20°).
Ленточные конвейеры классифицируют по следующим признакам:
по области применения – на конвейеры общего назначения, специальные и подземные;
по конфигурации трассы – на простые с одним прямолинейным участком и сложные с ломаной трассой, состоящей из горизонтальных и наклонных участков;
по направлению движения груза – на подъемные с уклоном вверх и спускные с уклоном вниз;
по форме ленты – на конвейеры с плоской и желобчатой лен-
той;
по типу тягового элемента – на конвейеры с резинотканевой, резинотросовой, стальной и проволочной лентами;
по углу наклона трассы – на горизонтальные, пологонаклонные, крутонаклонные (более 20°) и вертикальные;
18
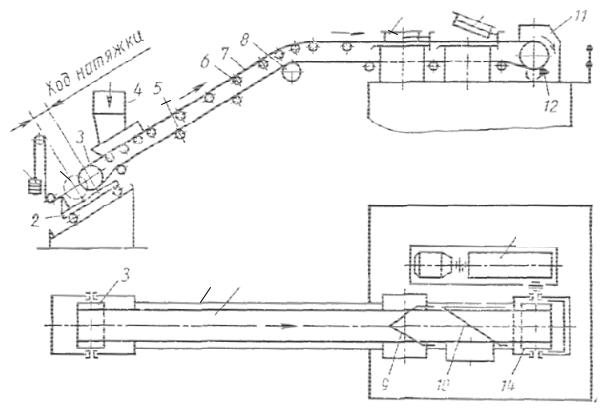
по разделению тяговой и несущей функций между элементами – на канатно-ленточные и ленточно-цепные.
Схема стационарного наклонно-горизонтального конвейера представлена на рис. 3.1.
9 10
1
14
13 7
9 |
|
10 |
|
15 |
Рис. 3.1. Схема стационарного наклонно-горизонтального конвейера
Несущим тяговым элементом конвейера является бесконечная лента 7, опирающаяся верхней (рабочей) и нижней (холостой) ветвями на роликовые опоры 5, 6 и огибающая на концах конвейера приводной 15 и натяжной 3 барабаны. У коротких конвейеров, используемых для перемещения штучных грузов, вместо роликоопор может использоваться деревянный или металлический настил. Движение ленте сообщается фрикционным способом от приводного барабана 15. Натяжение ленты осуществляется натяжным барабаном 3 при помощи грузового натяжного устройства 2. Сыпучий груз подается на ленту через загрузочную воронку 4, установленную у натяжного устройства 2. Разгрузка конвейера осуществляется по-разному: в конце конвейера либо в отдельных пунктах по его длине. С этой целью используют разгрузочные устройства 9 и 10, обеспечивающие движение груза в одну или две стороны. Для очистки рабочей стороны ленты от при-
19
липших частиц груза используют очистное устройство 12 в виде скребка или вращающихся щеток.
Привод ленточного конвейера 14 состоит из барабана 15, электродвигателя, редуктора, соединительных муфт.
Все узлы конвейера монтируются на металлической конструкции (не показана).
Для сыпучих грузов применяют многороликовые опоры, формирующие желобчатую форму ленты, благодаря чему обеспечивается при одинаковой ширине и скорости более чем двукратное увеличение производительности и исключается просыпание груза.
С целью исключения самопроизвольного движения в обратную сторону конвейеров с наклонными участками их оборудуют стопорными устройствами или двухколодочными нормальнозамкнутыми тормозами. На наклонных участках могут также устанавливаться ловители на случай обрыва ленты.
В ленточных конвейерах в основном применяют резинотканевые и резинотросовые ленты (рис. 3.2), реже проволочные и стальные ленты. Резинотканевые ленты (рис. 3.2, а) имеют многопрокладочную конструкцию: послойный тяговый каркас состоит из прокладок синтетической или комбинированной ткани. Прочность каркаса зависит от материала прокладок и их числа. Каркас сверху, снизу и с торцов покрыт слоем резины, которая предохраняет его от внешнего воздействия. Верхняя обкладка ленты, обращенная к грузу, называется рабочей. Нижняя нерабочая поверхность ленты покрыта слоем резины меньшей толщины.
Толщина резины на рабочей стороне ленты до 10 мм, нерабочей – от 1 до 3,5 мм.
Резинотросовые ленты (рис. 3.2, б) состоят из резинометаллического сердечника (одного ряда стальных проволочных канатиков) и наружных резиновых обкладок. Для обеспечения каркасности применяют тканевые прокладки. Поскольку такие ленты имеют высокую прочность, то их используют в подъемных конвейерах, а также в конвейерах с горизонтальными трассами, длина которых до 5000 м и более.
При выборе ленты необходимо учитывать свойства груза и условия работы, а ее прочность должна соответствовать расчетному максимальному натяжению.
20