
682
.pdf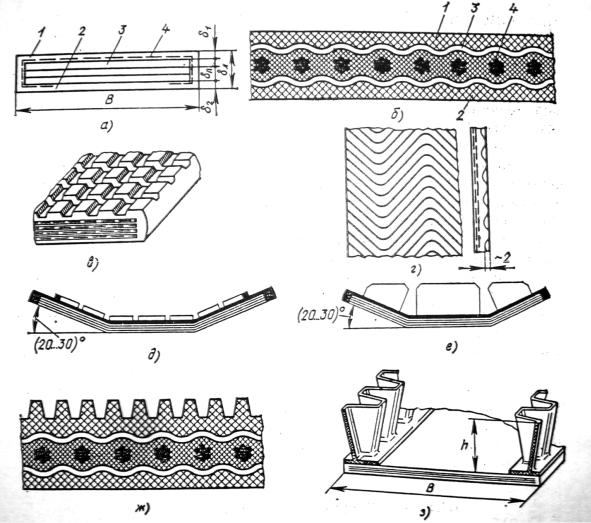
Рис. 3.2. Конвейерные ленты:
а– резинотканевая; б – резинотросовая; в – с прямоугольной насечкой;
г– с волнообразными низкими выступами; д – с низкими прерывистыми фасонными выступами; е – с высокими фасонными выступами;
ж– с непрерывными продольными ребрами;
з– с высокими гофрированными бортами
Наряду с резинотканевыми лентами и резинотросовыми лентами применяются специальные ленты, рассчитанные на особые условия работы. Их применяют в технически обоснованных случаях.
Соединение концов ленты может выполняться разъемным и неразъемным. Неразъемные соединения выполняются методом горячей и холодной вулканизации, а также при помощи заклепок. Соединения на петлях, крючьях, при помощи пластин с болтами являются разъемными. Более надежными являются соединения,
21
выполненные методом вулканизации. Резинотросовые ленты стыкуют только горячей вулканизацией.
В ленточных конвейерах различают приводные, концевые, натяжные и отклоняющие барабаны. С увеличением диаметра барабана уменьшаются напряжения изгиба и увеличивается срок службы. Наибольшие напряжения изгиба имеет место на приводном барабане, поскольку на нем тяговое усилие имеет максимальную величину.
Для резинотканевых лент диаметр барабана определяется по формуле:
D = k1k2i, |
(3.1) |
где k1 – коэффициент, учитывающий тип прокладок; k2 – коэффициент, учитывающий назначение барабана, а также усилие в ленте и угол обхвата лентой барабана; i – число прокладок.
При предварительных расчетах можно принять: диаметры концевых и натяжных барабанов Dк = 0,8D; диаметр отклоняющих барабанов Dот = 0,65D (D – диаметр приводного барабана). Полученный расчетом диаметр барабана округляется до ближайшего размера по ГОСТ 22644. Длина барабана на 150–200 мм принимается больше ширины ленты.
Лента между барабанами конвейера может опираться на роликоопоры, настил из стали или гладких деревянных досок, пластмассы, а также на комбинированные опоры, состоящие из роликоопор и настила.
Сплошной и комбинированные настилы применяются для перемещения штучных грузов и для насыпных пылящих и ядовитых грузов, перемещаемых в закрытом желобе. При транспортировании насыпных и штучных грузов (мешков, тюков, упаковок и т.п.) применяют обычно роликоопоры желобчатой формы. Диаметры роликов опор выбираются в зависимости от ширины ленты, плотности груза и скорости движения ленты.
По длине трассы конвейера роликоопоры устанавливаются на различном расстоянии друг от друга. Для конвейеров общего назначения на грузовой ветви расстояние между роликоопорами устанавливается в пределах 1–1,5 м. Чем больше насыпная плотность груза, тем ближе друг к другу устанавливаются роликоопоры. В зоне загрузки порошкообразных, пылевидных, зернистых и мелкокусковых грузов роликоопоры устанавливаются с шагом в 2 раза меньше принятого для грузовой ветви. На незагруженной
22
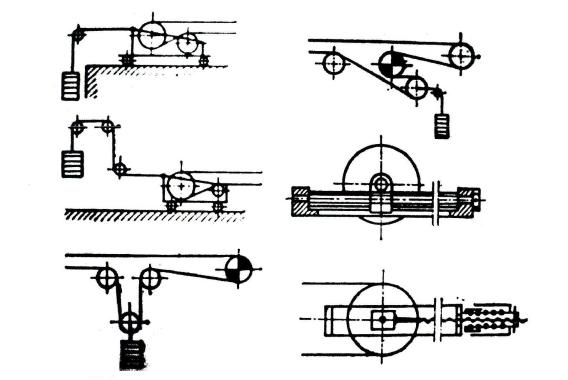
ветви роликоопоры устанавливаются с шагом в 2–3 раза большим
всравнении с грузовой ветвью, но не более 2,5–3,5 м.
Взоне перехода резинотканевой ленты из прямого положения
вжелобчатое на рабочей ветви у головного и хвостового барабанов устанавливаются две или три переходные роликоопоры с раз-
личным углом наклона боковых роликов αж на расстоянии, равном шагу на грузовой ветви. Центрирующие и регулирующие положение ленты роликоопоры чередуются между собой и устанавливаются на рабочей ветви через каждые 10 рядовых роликоопор.
Для штучных грузов массой более 20 кг шаг роликоопор принимается равным половине наибольшего габаритного размера груза и округляется до ближайшего целого числа. В зоне загрузки роликоопоры устанавливаются с меньшим шагом.
Для компенсации удлинения ленты в конвейерах применяются натяжные устройства. При помощи натяжных устройств создается такое натяжение ленты, при котором обеспечивается необходимое сцепление ленты с приводным барабаном, исключается буксование, ограничивается провисание ленты между опорами и компенсируется удлинение в процессе эксплуатации. Натяжение ленты осуществляется перемещением натяжного барабана. Наибольшее применение нашли винтовые, пружинно-винтовые и грузовые устройства (рис. 3.3). Винтовые и пружинно-винтовые устройства не обеспечивают постоянства натяжения тягового элемента.
a) |
г) |
б)
д)
в) |
е) |
23
Рис. 3.3. Натяжные устройства: а, б – хвостовое грузовое; в, г – промежуточное грузовое; д – винтовое; е – пружинно-винтовое
Более совершенными являются грузовые натяжные устройства, позволяющие автоматически регулировать натяжение ленты при ее удлинении и обеспечивающие постоянное натяжение ленты.
Для мощных ленточных конвейеров в ответственных случаях применяют автоматические натяжные устройства, регулирующие натяжение ленты в зависимости от нагрузки на тяговом элементе.
3.2. Загрузочные и разгрузочные устройства конвейеров
Загрузочные устройства конвейеров для насыпных грузов должны обеспечить соблюдение следующих требований: 1) груз должен ложиться равномерно по длине и ширине ленты; 2) в пункте загрузки не должно быть завалов и рассыпания груза; 3) на ленте необходимо оставлять свободные продольные поля; 4) лента и роликоопоры в месте загрузки не должны подвергаться ударному воздействию от подаваемого на ленту груза.
Насыпные грузы загружаются на ленту конвейера из бункеров или с технологических, транспортных и грузовых машин.
Штучные грузы загружаются механизированным способом или вручную.
Для обеспечения равномерной подачи груза на ленту из бункеров применяются различные типы питателей (рис. 3.4).
Часть питателей представляют собой разновидности конвейеров: ленточных, пластинчатых, винтовых, качающихся и вибрационных (рис. 3.4, а–д). Другие разновидности питателей (барабанные, дисковые и цепные) служат для подачи груза из отверстия бункера-накопителя.
На рис. 3.5 показана загрузка груза с одного конвейера на другой. Днище лотка воспринимает удары насыпного груза и установлено под углом α на 8°–10° больше угла трения груза о его поверхность. Вдоль ленты лоток снабжен направляющими бортами, имеющие вертикально расположенные к ленте уплотнения из мягкой износостойкой резины. Ширина направляющих бортов изменяется от B1 до B2 [B1 = 0,5В; B2 = (0,6 – 0,7)B]. Насыпной груз распределяется по ленте на ширину, равную 0,8В.
24
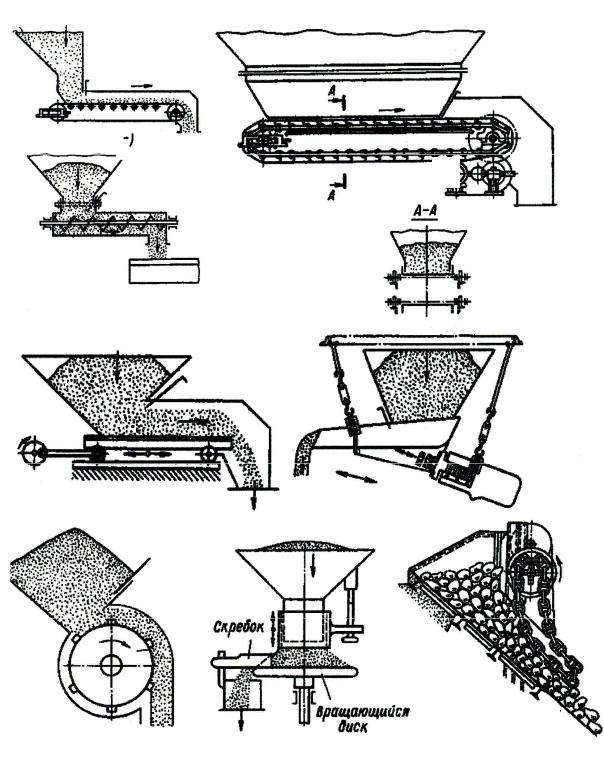
Разгрузка конвейера может осуществляться с концевого барабана или в промежуточных пунктах при помощи различных по конструкции разгрузочных устройств, установленных по длине трассы конвейера. Устройства для разгрузки могут быть стационарными и передвижными.
а) |
в) |
б)
г) |
|
|
|
д) |
|
|
|
|
|
||
|
|
|
|
||
|
|
|
|
||
|
|
|
|
||
|
|
|
е) |
ж) |
з) |
25
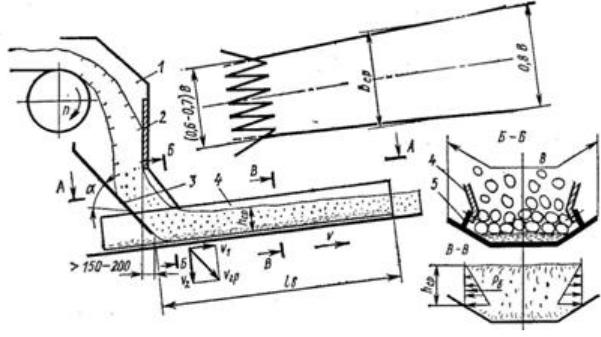
Рис. 3.4. Типовые схемы питателей:
а– ленточный; б – винтовой; в – пластинчатый; г – качающийся;
д– вибрационный; е – барабанный; ж – дисковый; з – цепной
Рис. 3.5. Схема загрузки груза с одного конвейера на другой
Если разгрузка производится в нескольких пунктах по длине конвейера, то либо в каждом пункте устанавливают откидные, включаемые поочередно, сбрасыватели, либо применяют передвижной сбрасыватель.
Для разгрузки конвейера в промежуточных пунктах сыпучих и штучных грузов применяют плужковые сбрасыватели двустороннего и одностороннего действия (рис. 3.6). Они отличаются простотой конструкции, имеют небольшие размеры и массу. Недостатком таких сбрасывателей является истирание ленты в процессе работы и значительное добавочное сопротивление движению.
26
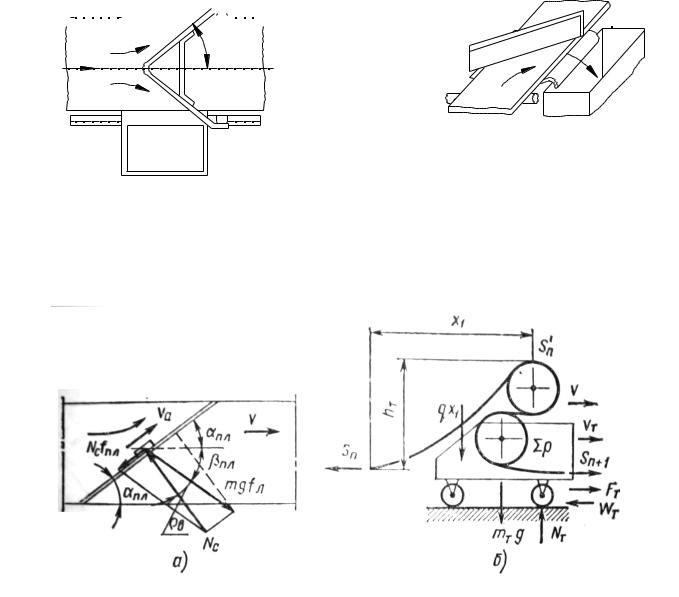
а) |
|
|
|
|
|
|
|
|
|
|
|
|
|
|
|
|
|
|
|
|
б) |
|||||||||||||
|
|
|
|
|
|
|
|
|
|
|
|
|
|
|
|
|
|
|
|
|||||||||||||||
|
|
|
|
|
|
|
|
|
|
|
|
|
|
|
|
|
|
|
|
|
|
|
|
|
|
|
|
|
|
|
|
|
|
|
|
|
|
|
|
|
|
|
|
|
|
|
|
|
|
|
|
|
|
|
|
|
|
|
|
|
|
|
|
|
|
|
|
|
|
пл
Рис. 3.6. Плужковые сбрасыватели двух- и одностороннего действия
Плужковый сбрасыватель для надежной разгрузки ленты должен быть установлен под определенным углом по отношению к продольной оси ленты (рис. 3.7).
Рис. 3.7. Расчетные схемы сбрасывающих устройств:
а– плужкового одностороннего действия;
б– двухбарабанной разгрузочной тележки
Груз движется первоначально со скоростью ленты v. Затем, встречаясь с заслонкой, груз начинает двигаться со скоростью vа.
В момент разгрузки на единичный штучный груз или на кусок (частицу) сыпучего груза массой m действует сила трения mgfл, нормальная реакция со стороны плужка Nс и сила трения груза о плужок Nс fпл (fпл – коэффициент трения груза о плужок).
При постоянной скорости движения груза vа, силы находятся в равновесии. В этом случае справедливо равенство:
27
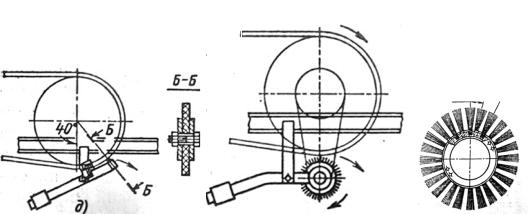
αпл + βпл + ρв = 90o , |
(3.2) |
где αпл – угол установки плужка; βпл – угол направления относительной скорости движения груза по ленте в момент сбрасывания; ρв – угол внешнего трения сбрасываемого груза о стенку плужка.
Так как угол βпл всегда больше нуля, αпл + ρв < 90o , то
αпл < 90o − ρв .
Для надежной разгрузки рекомендуемое значение угла установки плужка составляет αпл = 35o − 40o .
Наиболее рациональным способом разгрузки ленточного конвейера является применение двухбарабанной разгрузочной тележки (рис. 3.7, б).
Вдоль трассы конвейера тележка может перемещаться от собственного привода и производить разгрузку в одну или обе стороны относительно ленты. Двухбарабанные тележки, создавая благоприятные условия работы ленты (в сравнении с плужковым сбрасывателем), сложны по конструкции, имеют высокую стоимость и не применяются для разгрузки штучных грузов.
Большое значение для надежной работы конвейеров имеет наличие очистных устройств при транспортировании насыпных грузов (рис. 3.8, а, б). Для конвейеров, транспортирующих сухие грузы, рационально использовать очистной резиновый скребок. При транспортировании склонных к налипанию грузов применяют барабаны с резиновыми лопастями или вращающиеся капроновые щетки.
а) |
|
|
б) |
|
|
|
|
|
|
|
|
|
|
|
|
Рис. 3.8. Устройства для отчистки ленты ленточных конвейеров: а – скребком; б – вращающейся щеткой
Привод конвейера является ответственным для его надежной работы узлом. Он приводит в движение тяговый элемент конвей-
28
ера с грузом. Необходимое тяговое усилие на ленте конвейера создается силами трения, возникающими между лентой и поверхностью приводного барабана. Типовой привод конвейера включает электродвигатель, редуктор, муфты и барабан. В конвейерах применяются одно- и двухбарабанные приводы.
На тяжелонагруженных и протяженных конвейерах для преодоления всех сопротивлений при движении необходимо создать большое натяжение ленты. В этом случае применение однобарабанного привода является неэффективным, поэтому применяют несколько приводов, установленных вдоль трассы конвейера.
В приводах наклонных конвейеров применяют остановы и тормоза, исключающие обратное движение ленты под действием силы тяжести груза при отключенном двигателе.
Тормоза устанавливают и на горизонтальных конвейерах для уменьшения длины выбега после выключения двигателя.
Контрольные вопросы
1.Общие сведения, классификация и устройство конвейеров.
2.Какие разновидности лент используют в ленточных конвейерах?
3.Виды натяжных устройств.
4.Как осуществляется загрузка и разгрузка конвейеров?
4. РАСЧЕТ ЛЕНТОЧНОГО КОНВЕЙЕРА
Цель расчета состоит в определении параметров, обеспечивающих заданную производительность, натяжения ленты в характерных точках трассы, тягового усилия и мощности привода, характеристик натяжного устройства, типа и размеров ленты.
Исходными данными при выполнении расчета конвейера являются: производительность Q, т/ч, V, м3/ч или Z, шт./ч; род перемещаемого груза – его насыпная плотность ρ, т/м3, кусковатость, размеры и пр.; расстояние перемещения L, м; угол наклона вверх или вниз ±β или разность уровней в начальной или конечной точках ±Н, м; при сложной конфигурации трассы – ее схема с размерами; способ загрузки и разгрузки; условия размещения и эксплуатации.
Определение ширины ленты. Площадь сечения груза на полотне ленточного конвейера определяется шириной ленты В, формой поперечного сечения, придаваемой ей на роликоопорах, и
29
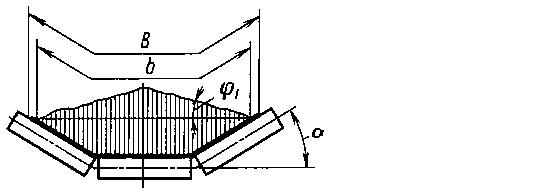
углом естественного откоса груза на ленте (рис. 4.1). Например, с некоторым допущением считают, что на плоской ленте сечение груза имеет форму треугольника (рис. 4.1, а).
Во всех случаях площадь сечения пропорциональна квадрату размера b, принимаемому равным b = 0,9В – 0,05 м. Груз образует на плоской ленте треугольное сечение, на двухроликовой – в виде двух треугольников, а на трехроликовой желобчатой – трапецеидальное в нижней части и треугольное в верхней.
Уравнения для определения производительности принимает следующий вид:
Q = C(0,9B − 0,05)2 vρ, |
(4.1) |
V = C(0,9B − 0,05)2 v. |
(4.2) |
β
Рис. 4.1. Поперечные сечения груза на ленте:
а – при прямых роликовых опорах; б – при желобчатых опорах
Полученные расчетным путем значения коэффициента пропорциональности С с учетом формы поперечного сечения приведены в таблице (табл. 4.1).
Таблица 4.1
Значение коэффициента С
|
|
|
|
|
Форма ленты |
|
|
|
|
|
|
||
|
|
|
|
|
|
|
|
|
|
|
|
|
|
Показатели |
|
|
Желобчатая |
|
|
Желобчатая |
|
|
|||||
|
Плоская |
на двухроли- |
|
|
|
|
|||||||
|
на трехроликовой опоре |
||||||||||||
|
|
|
ковой опоре |
||||||||||
|
|
|
|
|
|
|
|
|
|
|
|||
|
|
|
|
|
|
|
|
|
|
|
|
|
|
Угол наклона боко- |
– |
|
15 |
20 |
|
30 |
|
36 |
|||||
вых роликов β′, град |
|
|
|
||||||||||
|
|
|
|
|
|
|
|
|
|
|
|
|
|
|
|
|
|
|
|
|
|
|
|
|
|
|
|
Угол откоса насыпного |
15 |
20 |
15 |
|
20 |
15 |
20 |
|
15 |
20 |
|
15 |
20 |
груза на ленте ϕ, град |
|
|
|
||||||||||
|
|
|
|
|
|
|
|
|
|
|
|
|
|
30