
Metod_2542
.pdfиспользования прогрессивных решений, реализованных в действующих единичных процессах сборки аналогичных изделий.
Проведение размерного анализа конструкции собираемого изделия, выбор технологических баз и схем базирования, установление рациональных методов сборки. При проведении раз-
мерного анализа конструкции собираемого изделия выявляют и строят все сборочные размерные цепи и проводят соответствующие размерные расчеты. На основе выполнения расчетов и анализа сборочных размерных цепей определяют необходимую точность сборки компонентов и наиболее экономичные методы ее достижения. Обоснование выбора технологических баз, схем базирования и схем относительной ориентации компонентов на позициях сборки осуществляют на основе расчета технологических размерных цепей и условий собираемости компонентов. При выборе технологических баз используют принцип совмещения технологических баз с измерительными и конструкторскими возможностями с целью повышения точности и использования рациональных методов сборки. При выборе технологических баз также предусматривают возможность обеспечения постоянства и рациональной последовательности смены при выполнении сборки изделия. При этом при выполнении анализа возможных схем базирования рассчитывают погрешности установки компонентов и точность сборки, обеспечиваемую применением различных схем базирования. При выборе технологических баз также учитывают: удобство установки и снятия собираемого изделия; его устойчивость и надежность закрепления; удобство установки присоединяемых компонентов и подвода сборочного инструмента и т.п.
Составление технологического маршрута сборки изделия. На данном этапе определяется последовательность выполнения технологических операций, которая в наглядной форме представляется в виде технологической схемы сборки. Определяются содержание технологических операций и нормы времени на их выполнение, а также состав средств технологического оснащения сборки.
Разработка технологических операций. На этом этапе реша-
ются задачи рационального выбора технологических операций и их структуры. Устанавливаются рациональная последовательность и содержание переходов в операциях. Определяются требования к базирующим устройствам, устройствам относительной ориента-
53
ции, сборочным головкам и другим функциональным элементам оборудования. Устанавливаются исходные данные, необходимые для расчетов оптимальных режимов сборки, и проводится их расчет. Осуществляется выбор оборудования, обеспечивающего оптимальную производительность и требуемое качество сборки. Выполняется расчёт загрузки оборудования. Выбираются оснастка и вспомогательное оборудование.
При разработке операций устанавливают возможность совмещения выполнения технологических переходов во времени, при этом время на выполнение операций увязывается с расчетным действительным тактом сборки. Последнее достигается за счет объединения технологических переходов в операции таким образом, чтобы сумма времени на их выполнение приближалась по значению к действительному такту сборки. Обеспечение наибольшего приближения данных значений достигается за счет переноса некоторых технологических переходов из одной операции в другую, сокращения времени выполнения операций и др. Сокращение времени выполнения операций осуществляют за счет повышения уровня автоматизации процесса сборки, совмещения выполнения технологических переходов, повышения скорости сборки, уменьшения времени вспомогательных ходов, применения рациональных методов сборки и схем построения операций и т.п.
Сокращение времени на выполнение операций и совмещение переходов могут достигаться применением соответствующих схем построения сборочных операций. Схемы построения сборочных операций могут быть одноместные и многоместные в зависимости от числа устанавливаемых на позицию сборки изделий; одноин-
струментные и многоинструментные в зависимости от числа од-
новременно применяемых при сборке инструментов. По последовательности осуществления технологических переходов операции могут быть последовательного, параллельного и параллельнопоследовательного выполнения. При различном сочетании указан-
ных выше схем образуется комплекс схем построения операций, в значительной степени отличающихся друг от друга по времени выполнения и себестоимости сборки. На рис. 2.19 показаны примеры схем построения сборочных операций: одноместных (см. рис. 2.19, а–в); многоместных (см. рис. 2.19, г–е); одноинструментных (см. рис. 2.19, а, г); многоинструментных (см. рис. 2.19, б, в, д, е), а
54

также последовательного (см. рис. 2.19, а, г), параллельнопоследовательного (см. рис. 2.19, б, д) и параллельного (см. рис. 2.19, в, е) действия.
а) |
б) |
в) |
г) |
д) |
е) |
Рис. 2.19. Схемы построения сборочных операций
При разработке технологических операций определяют оптимальные режимы сборки (усилия запрессовки, моменты затяжки резьбовых соединений, температуру нагрева и охлаждения компонентов при сборке с термовоздействием и т.п.) и находят настроечные размеры для наладки оборудования. После принятия схем построения сборочных операций и выполнения расчета режимов сборки определяют требования к базирующим устройствам, устройствам относительной ориентации, сборочным головкам и другим функциональным элементам сборочного оборудования, а также к оборудованию в целом. При проектировании сложных технологических операций, выполняемых на многопозиционном сборочном оборудовании, определяется загрузка оборудования по отдельным позициям и строятся циклограммы его работы.
Устанавливаются структура и основные технические характеристики сборочного оборудования: структурная схема, степень автоматизации рабочего цикла, кинематические и динамические характеристики, грузоподъемность, число степеней подвижности, размеры рабочего пространства, мощность привода, система управления, степень переналаживаемости и др. На основе этих данных определяется соответствующая модель серийно выпускаемого оборудования; при отсутствии такого оборудования разрабатывается техническое задание на его проектирование. При сборке изделия на автоматизированных линиях устанавливают структуру и тип линии, схему компоновки линии и необходимую стыковку ее с другим технологическим оборудованием и производственными участками, применяемое оборудование и транспортную систему, загрузку и надежность работы отдельных позиций, необходимые заделы и накопители и др. На основе этих данных составляется техническое задание на проектирование линии.
55
Устанавливаются конструкция и основные параметры оснастки, и определяется соответствующий тип серийно выпускаемой стандартной и унифицированной оснастки. Составляется техническое задание на конструирование специальной оснастки (приспособлений и инструмента) с указанием схем базирования, способов закрепления, автоматической подачи и ориентации компонентов и др. Устанавливаются структура и содержание операций контроля и выбираются средства технологического оснащения процессов технического контроля. Определяется тип блокировочных устройств для предупреждения аварийных ситуаций и брака при сборке. Выбираются необходимые подъемно-транспортные средства и другое вспомогательное оборудование.
2.4.5. Выбор средств технологического оснащения сборки
К средствам технологического оснащения сборки относят со-
вокупность орудий производства, необходимых для осуществления технологического процесса сборки, включая сборочное, транспорт- но-загрузочное, вспомогательное и подъемно-транспортное технологическое оборудование, а также технологическую оснастку (приспособления и инструменты).
Выбор варианта технологического оборудования начинается с анализа параметров собираемого изделия, методов и последовательности его сборки и режимов сборочного процесса, на основе которого для возможных вариантов оборудования устанавливаются отношения: основного времени, штучного времени, приведенных затрат на выполнение сборки различными методами. При этом лучшим вариантом оборудования является тот, для которого значения данных показателей являются минимальными. Окончательный выбор варианта технологического оборудования осуществляется на основе анализа затрат на реализацию технологического процесса сборки изделий в установленный промежуток времени при заданном качестве сборки, который предусматривает сравнение возможных вариантов оборудования и выбор варианта, основывающегося на анализе следующих данных: технических требований, предъявляемых к изделию, количества и сроков выполнения сборки изделий, технических возможностей оборудования, затрат на приобретение оборудования и его эксплуата-
56
цию, требований техники безопасности и производственной санитарии. При этом выбор технологического оборудования производят по главным параметрам, в наибольшей степени определяющим его технические возможности (максимальному усилию запрессовки, крутящему моменту, размерам рабочей зоны и т.п.).
На выбор сборочного оборудования оказывают влияние: кон-
струкция собираемого изделия и его составных частей; их геометрическая форма, размеры и масса; требования, предъявляемые к сборке изделия; такт сборки и программа выпуска собираемых изделий; размеры партий изделий и число запусков, режимы процесса сборки и другие факторы. При определении вида и конструкции сборочного оборудования осуществляется обоснование и выбор его составляющих элементов: загрузочных устройств, сборочных головок, базирующих устройств и устройств относительной ориентации компонентов на позициях сборки, устройств контроля, вспомогательных и транспортных устройств, устройств управления.
При выборе компоновки и структуры сборочного оборудования определяется оптимальный уровень автоматизации по всем технологическим переходам и операциям. В зависимости от числа собираемых компонентов nк выбирается однопозиционное (обычно при nк ≤ 3…4) или многопозиционное оборудование. При числе выполняемых технологических операций nо ≤ 6…8 обоснованным может быть выбор многопозиционного станка, а при nо > 8 — сборочной линии. При числе nк ≤ 6 и действительном такте сборки Тд < 2…3 с целесообразным может быть использование многопозиционного оборудования непрерывного действия, а при Тд > 3 с — многопозиционного оборудования дискретного действия. При габаритных размерах собираемого изделия более 300 мм целесообразным может быть использование многопозиционного оборудования линейной компоновки, а при размерах менее 300 мм — многопозиционного оборудования с поворотным столом.
Для многопозиционного оборудования устанавливается вид компоновки (линейная, кольцевая, прямоугольная и др.) и выбирается вид транспортной системы. Далее по всем операциям с учетом технологической совместимости выбираются конструкции загрузочных устройств, сборочных головок и устройств контроля. Устанавливаются конструкции базирующих устройств и устройств
57
относительной ориентации компонентов на позициях сборки с учетом обеспечения собираемости компонентов. Выбираются вспомогательные устройства (кантователи, средства нагрева и охлаждения компонентов и др.) и система управления сборочным оборудованием.
Выбор средств (устройств) контроля осуществляется на ос-
нове заданных показателей процесса контроля (точности измерений, достоверности, трудоемкости и стоимости контроля и др.) и анализа затрат на выполнение контроля в установленный промежуток времени при заданном качестве сборки изделия. Выбор средств контроля выполняется в следующей последовательности.
1.Выявляются контролируемые параметры и характеристики собираемого изделия и процесса сборки и определяются показатели процесса контроля, определяющие выбор средств контроля.
2.Устанавливается состав средств контроля, использование которых обеспечивает заданные показатели процесса контроля без нарушения протекания технологического процесса сборки изделия.
3.Дается экономическое обоснование выбираемых средств контроля.
4.Для специальных средств контроля определяются исходные данные для проектирования их конструкций и разрабатываются технические задания на проектирование. По результатам выбора средств контроля оформляется соответствующая технологическая документация.
При проведении анализа и обосновании выбора средств контроля учитывают: конструктивные особенности собираемого изделия (конфигурацию, доступность, размеры и т.п.); виды контролируемых признаков (геометрический размер, физические параметры, относительное расположение поверхностей и т.п.); допустимые погрешности измерения; наличие измерительных баз; повреждаемость (деформируемость) при контроле; производительность контроля и т.д.
Выбор конструкции технологической оснастки осуществля-
ется на основе анализа затрат на выполнение технологического процесса сборки с установленным тактом сборки при заданном качестве собираемых изделий. На основе проведения такого анализа выбирается наиболее экономичная оснастка соответствую-
58
щего уровня механизации и автоматизации, а также степени специализации и переналаживаемости.
Выбор технологической оснастки предполагает выполнение комплекса работ, включающих проведение анализа конструктивных характеристик собираемого изделия (габаритные размеры, точность и т.д.), а также технологических и организационных условий сборки изделия (вид сборочной операции, схема базирования, организационная форма сборки и т.д.); группирование сборочных операций для использования наиболее рациональной системы технологической оснастки; установление исходных требований к оснастке и отбор конструкций, соответствующих установленным требованиям, из имеющейся номенклатуры оснастки; определение необходимых исходных расчетных данных и разработку технических заданий на проектирование и изготовление новых конструкций оснастки.
Конструкцию оснастки определяют с учетом имеющихся стандартных и типовых решений для данного вида сборочных операций на основе габаритных размеров и вида собираемого компонента, необходимой точности его параметров и конструктивных характеристик поверхностей, оказывающих влияние на конструкцию оснастки, технологических схем базирования и характеристик оборудования, объемов выпуска собираемых изделий и т.п.
2.4.6. Контроль качества сборки изделий
При проектировании технологических процессов одной из важнейших задач является обеспечение качества собираемых изделий. Качество обеспечивается проведением своевременного соответствующего контроля и предупреждением брака на всех этапах процесса сборки изделий.
При выполнении сборки изделий проверяют: точность взаимного расположения сопряженных деталей и правильность положения узлов в изделии; наличие деталей в собираемых узлах (изделиях), приспособлениях, накопителях, лотках и т.п.; точность относительного положения собираемых деталей на позициях сборки; зазоры и натяги в собранных соединениях; усилия затяжки резьбовых соединений, плотность и качество постановки заклепок, усилия запрессовки деталей и др.; герметичность соединений; правильность функционирования составных частей изделий (легкость и скорость
59
вращения, точность перемещений, качество контакта и др.); уравновешенность деталей и узлов в изделии; внешний вид собранных изделий (отсутствие повреждений деталей, загрязнений и др.) и т.п. В процессе сборки также контролируют: последовательность выполнения сборочных операций и переходов (порядок затяжки резьбовых соединений, последовательность наложения сварных швов и др.); выполнение вспомогательных операций (промывка, очистка, сушка, нагрев, охлаждение и др.); правильность функционирования сборочного оборудования и оснастки и др.
Задача проектирования технологии сборки связана с выбором наиболее рациональных методов и средств контроля, а также ор- ганизационно-технических форм его проведения, обеспечивающих заданное качество собираемых изделий. Классификация видов контроля сборки представлена на рис. 2.20.
Технический контроль сборки разрабатывается в виде процесса — совокупности технологических операций технического контроля, выполняемых при сборке изделия или его составной части. Эти процессы разрабатывают для входного, операционного и приемочного контроля. Выбор оптимального варианта процесса (операции) технического контроля осуществляется на основе проведения соответствующих расчетов экономической эффективности. На процессы контроля разрабатывают технологические паспорта, журналы контроля технологических процессов.
Процессы (операции) технического контроля разрабатывают совместно с технологическим процессом сборки, при этом уровень механизации и автоматизации процессов (операций) контроля должен отвечать требованиям процесса сборки, а также условиям и типу производства. При разработке процессов (операций) контроля должно по возможности обеспечиваться единство конструкторских, технологических и измерительных баз. При операциях контроля необходимо предусматривать получение информации для регулирования технологического процесса сборки, а также обеспечивать предупреждение с заданной вероятностью пропуска дефектных сборочных единиц для последующего изготовления изделия. Процессы (операции) контроля фиксируются в утвержденных технологических документах, которые подвергаются метрологической экспертизе.
60
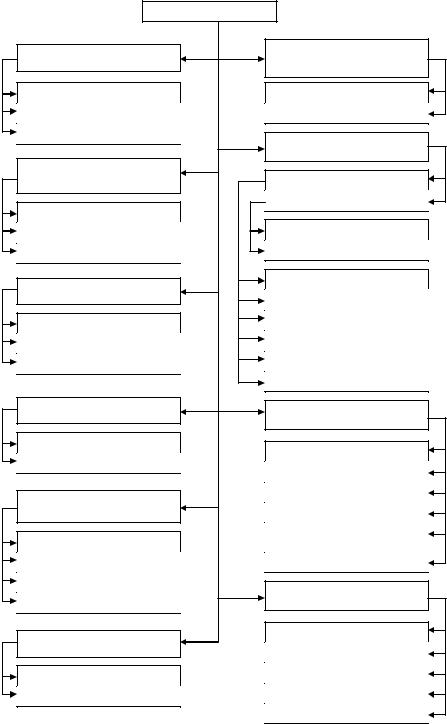
Виды контроля
По этапам процесса производства
входной
операционный
приемочный
По связи с объектом контроля во времени
летучий
непрерывный
периодический
По полноте схвата контролем
сплошной
выборочный
статистический
По влиянию на объект контроля
неразрушающий
разрушающий
По степени механизации и автоматизации
ручной
механизированный
автоматизированный
автоматический
По месту проведения
подвижный
стационарный
По степени воздействия на ход процесса
активный
пассивный
По применяемым средствам контроля
измерительный
органолептический
визуальный контроль
Технический осмотр
механический
электрический
оптический
магнитный
ультразвуковой
другие методы
По типу контролируемых признаков
геометрических параметров
физических параметров
функциональных параметров
качественных признаков
технического состояния, функционирования, работоспособности
другие
По объекту контроля
качества изделия
технологического процесса
средств технологического оснащения
технической документации
технологической дисциплины
Рис. 2.20. Классификация видов контроля, применяемого в сборочном производстве
Разработка процессов (операций) технического контроля включает следующие основные этапы.
1. Подбор и анализ исходных материалов для разработки процессов контроля с использованием конструкторской и технологической документации, данных по программам и срокам изготов-
61
ления изделий, инструкций на проведение контроля, описаний прогрессивных методов контроля и т.п.
2.Классификация и выбор объектов контроля. На этом этапе решаются задачи создания однородных групп объектов контроля
ивыбора типовых представителей групп, а также определения номенклатуры объектов контроля.
3.Группирование объектов контроля с целью создания укрупненных групп объектов контроля, разработка (выбор) комплексного объекта контроля для каждой группы и разработка предложений по унификации собираемых изделий и их элементов.
4.Выбор действующего типового, группового процесса технического контроля или поиск аналога единичного процесса технического контроля.
5.Составление технологического маршрута процесса технического контроля.
6.Выбор контролируемых параметров для определения номенклатуры параметров собираемого изделия, подвергаемых техническому контролю.
7.Разработка технологических операций технического контроля и определение объема контроля (с учетом рационального назначения выборок в партии объектов контроля).
8.Выбор схем контроля (определение контрольных точек, выбор поверхностей базирования средств контроля, оценка точности
инадежности базирования по производительности контроля).
9.Выбор методов и средств контроля.
10.Расчет точности, производительности и экономической эффективности вариантов процессов (операций) контроля и выбор оптимальных вариантов.
11.Оформление документов на процессы (операции) контроля с учетом требований Государственной системы обеспечения единства измерений и Единой системы технологической документации.
12.Разработка документации результатов контроля (технологических паспортов, карт измерения, журналов контроля технологических процессов).
Необходимость проведения каждого из рассмотренных выше этапов разработки процессов (операций) технического контроля определяется разработчиком в зависимости от условий производства или устанавливается стандартами предприятия. В зависимо-
62