
книги / Новые материалы и технологии
..pdfОпределение всего комплекса этих характеристик представляет сложную и трудоемкую задачу, поэтому ее решают, разделив на две части. Основные характеристики определяют экспериментальными исследованиями (испытывая образцы КМ), остальные – с помощью расчетов по формулам (так называемым математическим моделям).
Целью данного занятия является ознакомление с методикой прогнозирования на конкретных примерах ее применения. Для однонаправленно-армированного композита при прогнозировании его свойств часто применяют известное правило аддитивности (формулу смесей)
a a1С1 a2С2 , |
(7) |
где a |
– прогнозируемое свойство композита; |
a1 и a2 |
– аналогичное свойство компонентов (волокна и связую- |
|
щего); |
С1 иС2 |
– объемныедоликомпонентоввкомпозите(С1 + С2 = 1). |
Пример 1. Прогноз прочности стеклопластика
Определить прочность на растяжение однонаправленно-ар- мированного стеклопластика по известным свойствам его компонентов:
в = 250 кг/мм2 – прочность стекловолокна;св = 8 кг/мм2 – прочность эпоксидного связующего;
Св = 0,5 иСсв = 0,5 – объемныедоливолоконисвязующеговКМ. Подставим эти значения в формулу (7):
KM 250 0,5 8 0,5 125 4 130 кг/м2 . |
(8) |
Из формулы (8) видно, что с увеличением доли волокон (Св) предел прочности композита ( КМ) линейно возрастает. Однако экспериментальная проверка показывает, что это возрастание идет только до определенного значения Св .
11
Для стеклопластиков оптимальное значение Св = 0,70…0,72; для органопластиков – 0,62…0,65. При этих значениях прочность композита достигает своего максимума. Если увеличивать долю волокон далее, то это приводит к снижению прочности. Объяснить такую ситуацию можно тем, что в композите становится слишком мало связующего и его не хватает на все волокна. Отдельные волокна остаются непропитанными, они «не включаются» в работу, что в конечном итоге приводит к понижению прочности КМ.
Пример 2. Определение модуля упругости органопластика
Определить, используя формулу смесей, модуль упругости органопластика по известным свойствам его компонентов: Ев = = 9000 кг/мм2 и Есв = 300 кг/мм2 – модули упругости органоволокон и связующего; Св = 0,6 и Ссв = 0,4 – объемные доли волокон и связующего.
Этот пример предлагается решить самостоятельно.
Пример 3. Прогноз плотности композита
Определить плотность композиционного материала по известным его компонентам:
в = 2,6 г/см3 и Св = 0,5 – плотность и доля стекловолокон;св = 1,3 г/см3 и Ссв = 0,5 – плотность идоля связующего вКМ. Применив правило аддитивности, получим
ρKM ρвСв свСсв 2,6 0,5 1,3 0,5 1,3 0,65 1,95 г/см3.
Следовательно, прогнозируемая плотность будущего стеклопластика составит 1,95 г/см3.
Пример 4. Определение плотности трехкомпонентного КМ
Определить плотность композиционного материала, если соотношение углеродных волокон к эпоксидному связующему составляет 60 : 40 (объемных процентов), а в композит добавлен
12
третий компонент – алюминиевый порошок, его доля в композите составляет 8 % (по объему).
Этот пример предлагается решить самостоятельно.
Пример 5. Прогноз температурного удлинения стержня
Планируется изготовить стеклопластиковый стержень длиной l0 = 1500 мм с круглым поперечным сечением, с однонаправленным армированием вдоль оси. Соотношение компонентов (волокна и связующего) – 55 : 45 (объемных процентов). Стержень работает в температурном диапазоне от
–50 С до +80 С.
Необходимо сделать прогноз изменения начальной длины стержня (соответствующей температуре +20 С) в указанном температурном диапазоне. При расчетах принять, что коэффициент линейного температурного расширения стекловолокон и эпоксидного связующего остается в указанном диапазоне температур постоянным. При расчетах рекомендуется использовать формулы:
KM |
1 |
( вСвЕв свСсвЕсв ) ; |
(9) |
|
|||
|
EKM |
|
|
|
KM (Тк Т0 )l0 , |
(10) |
где км и Екм – коэффициент температурного линейного расширения и модуль упругости стеклопластика;
в, Св, Ев – коэффициент температурного линейного расширения, доля и модуль упругости стекловолокон;св, Ссв, Есв – коэффициент температурного линейного расширения, доля и модуль упругости эпоксидного
связующего; Т0 и Тк – начальная (20 С) иконечная температура стержня;
l0 – начальная длина стержня;
– изменение длины стержня вследствие перепадов температуры.
13
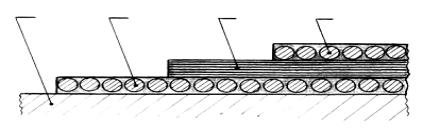
Недостающие данные для расчета нужно взять из литературных источников.
Этот пример предлагается решить самостоятельно.
Пример 6. Прогноз прочности стеклопластиковой оболочки
Сделать прогноз конструктивной прочности стеклопластиковой оболочки, полученной спирально-перекрестной намоткой, с углом армирования = 60 , с соотношением компонентов (волокон и связующего) 60 : 40 (объемных процентов). Под конструктивной прочностью здесь следует понимать прочность на растяжение материала оболочки в кольцевом и осевом направлениях. При их расчете следует использовать формулу из практического занятия № 1.
Этот пример предлагается решить самостоятельно.
Практическое занятие № 3
РАСЧЕТ ТЕХНОЛОГИЧЕСКИХ ПАРАМЕТРОВ ФОРМОВАНИЯ СТЕКЛОПЛАСТИКОВОЙ ТРУБЫ МЕТОДОМ НЕПРЕРЫВНОЙ НАМОТКИ
Метод непрерывной намотки рассматривался нами ранее, он описан в учебном пособии «Новые технологии в производстве труб и других изделий из композитов». Этим методом изготавливают стеклопластиковые трубы разного назначения. Толщина стенки трубы формуется по типичной трехслойной схеме
(рис. 6).
1 |
2 |
3 |
4 |
Рис. 6. Трехслойная схема армирования стеклопластиковой трубы: 1 – оправка; 2 – внутренний кольцевой слой; 3 – средний продольный слой; 4 – внешний кольцевой слой
14

В техническом задании (ТЗ) и конструкторской документации на трубу задаются следующие исходные показатели: толщина стенки трубы, соотношение армирующих волокон кольцевого и продольного направлений. Технологу приходится, используя эти данные, определять параметры формования, т.е. рассчитывать, сколько и какого стеклоровинга положить при намотке в кольцевые и продольные слои. Рассмотрим такую технологическую задачу на конкретном примере.
Пример
Методом непрерывной намотки изготавливается стеклопластиковая труба с внутренним диаметром d = 205 мм, с толщиной стенки = 5 мм. Труба предназначена для работы под действием внутреннего давления транспортируемой жидкости, оптимальное соотношение кольцевого и продольного армирования в этом случае соответствует соотношению
К : П = 2 : 1, |
(11) |
где К иП – количество кольцевой и продольной арматурывтрубе; 2 : 1 – оптимальное численное соотношение данных направ-
лений армирования.
Намотка каждого кольцевого слоя ведется 18 ровингами с линейной плотностью Т = 1600 текс, собранными в ленту и пропитанными связующим. Продольное армирование (среднего слоя) обеспечивается псевдолентой, состоящей из двух ровингов.
Суть данной методики* заключается в том, что подсчитываются веса намотанной на оправку кольцевой и продольной арматуры при заданном их соотношении. Затем под эти массы подбирается количество армирующего материала определенного типа. Для упрощения расчеты проводят не для всего объема
* Методика предложена канд. техн. наук, доцентом Б. Д. Олейником.
15
пластика в трубе, а для 1 оборота оправки, что приводит к тому же результату.
Масса ровинга, используемого для армирования двух кольцевых слоев (нижнего и верхнего), определяется по формуле
mк qкlк , |
(12) |
где qк – вес одного погонного метра стеклоровинга;
lк – длина ровинга, использованного на 1 оборот оправки. Аналогично определяется и расход ровинга для продольного
армирования
mп qпlп . |
(13) |
Если взять для кольцевого и продольного армирования ровинги с одинаковой линейной плотностью, то qк = qп и выражение (11) можно будет записать в следующем виде:
mк |
|
lк |
2 :1. |
(14) |
|
l |
|||||
m |
|
|
|
||
п |
|
п |
|
|
|
Общая длина кольцевых ровингов на 1 оборот оправки вы- |
|||||
числяется следующим образом: |
|
|
|||
lк dcp nк , |
(15) |
где dср = 210 мм – средний диаметр трубы;
nк = 2 18 = 36 – суммарное количество ровингов кольцевого направления.
Подставив эти значения в формулу (15), получим
lк 3,14 210 36 23740 мм = 23,74 м.
Продольное армирование осуществляется псевдолентой, схема ее получения и укладка на оправку изображены на рис. 7.
16
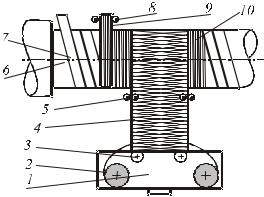
PNRPU
Рис. 7. Схема получения псевдоленты и ее укладка на оправку: 1 – нитеукладчик (вертлюг); 2 – бабина со стекложгутом; 3 – катушка со стеклонитью; 4 – получаемая псевдолента; 5 – ролики; 6 – оправка; 7 – фторопластовая лента; 8 – ролики; 9 – лента кольцевой намотки; 10 –
кольцевой слой
Псевдолента состоит из двух краевых нитей малой линейной плотности и двух ровингов большой линейной плотности, уложенных по зигзагообразным пересекающимся траекториям.
Псевдоленту получают следующим образом. При вращении оправки и вертлюга краевые нити, прикрепленные концами к оправке, протягиваются через зону вертлюга. При этом вокруг них обматываются два ровинга, образуя пересекающиеся зигзаги. Ровинги, уложенные в зигзаги, являются продольным армирующим элементом в будущем пластике. Угол определяет плотность зигзага и направление укладки продольной арматуры по отношению к оси оправки. Расстояние между краевыми нитями определяет ширину псевдоленты, а скорость вращения вертлюга задает определенную плотность укладки жгутов (ровингов) в зигзаги. Количество продольной арматуры, заданное для трубы, обеспечивается за счет соотношения оборотов вертлюга на 1 оборот оправки. Вертлюг имеет кинематическую связь с оправкой, соотношение их оборотов можно регулировать в широком диапазоне от 4 до 30 оборотов вертлюга на 1 оборот оправки.
Расход продольной арматуры определим по формуле
lп 2b cos ω m , |
(16) |
17

где b = 210 мм – ширина псевдоленты;
= 10 – угол укладки продольной арматуры;= 15 – число оборотов укладчика на 1 оборот оправки;
m = 2 – количество ровингов продольного армирования. Подставив эти значения в формулу (16), получим
lп 2 210 cos10° 15 2 11850 мм = 11,85 м.
Сделаем контрольную проверку полученного соотношения кольцевого и продольного армирования. Для этого подставим полученные результаты в формулу (14):
lк 23,74 2 :1. lп 11,85
Полученное соотношение соответствует заданному по ТЗ. Таким образом, определены некоторые параметры для изготовления стеклопластиковой трубы. Заметим, что часть параметров вошла в исходные данные (количество ровингов n = 18 для кольцевого слоя и m = 2 для продольного армирования),= 15 оборотов, b = 210 мм и другие величины взяты из дополнительных расчетов (здесь не приведенных), стеклоровинг
с Т = 1600 текс взят на основе опыта.
Практическое занятие № 4
ОПТИМИЗАЦИЯ КОНСТРУКТИВНЫХ ПАРАМЕТРОВ ДВУХСЛОЙНОЙ ОБОЛОЧКИ ИЗ МЕТАЛЛА И КОМПОЗИТА
Некоторые конструкции, представляющие собой сосуды давления, например цилиндрическую оболочку под действием высокого внутреннего давления, с целью снижения массы целесообразно выполнять двухслойными. Внутренний слой представляет тонкую металлическую оболочку, внешний изготовлен
18

из легкого прочного композита. При этом толщина металлической оболочки должна быть достаточной для обеспечения высокой герметичности, а сама оболочка должна выполнять роль формообразующей основы (оправки) при намотке композиционного слоя.
Таким образом, внутренняя металлическая оболочка выполняет функцию конструкционного элемента, герметизирующего слоя и технологическую функцию оправки для верхнего слоя. Композиционный слой является силовым элементом конструкции, а также дополнительным защитным (антикоррозионным); он отличается высокой прочностью и низкой плотностью. Такую конструктивную схему используют для спецтехники оборонной отрасли, где одним из основных требований является сочетание высокой несущей способности и минимального веса. Рассмотрим в качестве примера вариант исполнения двухслойной цилиндрической оболочки, а точнее ее модели. Эскиз модельной двухслойной оболочки показан на рис. 8.
1 |
2 |
3 |
н в
dв
L
Рис. 8. Эскиз двухслойной модельной оболочки: 1 – внутренний металлический слой; 2 – внешний слой композита; 3 – торцевая подмотка под заглушки
19
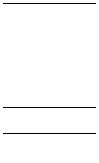
Эта модель взята на основе отраслевого стандарта ОСТ 1189-6046. Внутренний слой выполнен из высокопрочной стали 30ХГСА, толщина этого слоя ст = 0,8 мм. Такая толщина взята как минимально допустимая исходя из технологичности исполнения. Верхний композиционный слой должен быть прежде всего высокопрочным и легким, по основным физикомеханическим характеристикам близким к внутреннему слою. Это необходимо для обеспечения совместности работы обоих слоев. Если слои будут отличаться существенно по модулям упругости, то слой с меньшим модулем будет недогружен, а с большим – перегружен. В результате по суммарной несущей способности двух слоев будет очевидный проигрыш.
Также необходимо учитывать такой эксплуатационный параметр, как температурное воздействие на конструкцию. В этом плане желательно, чтобы коэффициенты температурного линейного расширения слоев отличались не намного. У внутреннего слоя – стали 30ХГСА – этоткоэффициентравен 8…10 10–6 1/град.
Сделаем выбор КМ исходя из этих требований. В табл. 1 приведены основные физико-механические характеристики трех наиболее применяемых КМ: стеклопластика, органопластика и углепластика.
|
|
|
|
Т а б л и ц а 1 |
Основные физико-механические характеристики КМ |
||||
|
|
|
|
|
|
Предел |
|
|
Коэффициент |
|
прочности |
Модуль |
Плот- |
температурно- |
Тип композита |
на растя- |
упругости, |
ность, |
го линейного |
|
жение, |
кг/мм2 |
г/см3 |
удлинения |
|
кг/мм2 |
|
|
×10–6 1/град |
Стеклопластик |
120…130 |
6500…7000 |
1,95 |
15 |
|
|
|
|
4 |
Углепластик |
140…150 |
13000…15000 |
1,65 |
|
|
|
|
|
–3 |
Органопластик |
160…170 |
7000…8000 |
1,35 |
|
|
|
|
|
|
20