
книги / Новые материалы и технологии
..pdfВ практике изготовления стеклопластиковых труб имеют место дополнительные расходы исходных материалов, связанные с технологическими остатками или перерасходом. Например, остатки связующего в ванночке намоточного станка, короткие остатки ровингов на использованных бабинах, небольшие расходы при входном контроле материалов и т.д. Поэтому на практике расчетные результаты увеличивают на
3…5 %.
Практическое занятие № 6
ОПРЕДЕЛЕНИЕ ДЛИНЫ ПРОЛЕТА МЕЖДУ ОПОРАМИ ПРИ ПРОЕКТИРОВАНИИ СТЕКЛОПЛАСТИКОВОГО ТРУБОПРОВОДА
Стеклопластиковые трубопроводы нашли в настоящее время широкое применение в самых различных направлениях:
магистральные трубопроводы водоснабжения;
нефтепроводы первичного сбора нефти;
воздуховоды, защитные трубы кабельных сетей;
системы водослива и канализации;
внутриквартальные сети горячего водоснабжения;
технологические трубопроводы химических предприятий;
трубопроводы для нефтехимической промышленности;
трубопроводы промышленной транспортировки питьевых
ипищевых жидкостей;
и другие.
При проектировании трубопроводов одним из этапов является расчет опор и длины пролетов между ними. Нормативными параметрами в таких расчетах являются допустимые прогибы труб, деформации изгиба, коэффициенты запаса по герметичности стеклопластиковых труб и другие параметры. При крепле-
31
нии трубопровода на опорах участки труб между ними, вследствие действия различных нагрузок, прогибаются. Величина прогиба зависит от расстояния между опорами, размеров трубы, физико-механических характеристик стеклопластика, действующих нагрузок, способов крепления труб на опорах.
Целью данного практического занятия является рассмотрение методики расчета трубопровода. Для лучшего усвоения материала проделаем это на конкретном примере.
Исходные данные:
стеклопластиковый трубопровод холодного водоснабже-
ния;
внутренний диаметр труб d = 300 мм;
толщина стенки труб = 10 мм;
напорное давление воды p = 10 кг/см2 (атм);
плотность стеклопластика км = 1,9 г/см3;
вид намотки труб – спирально-перекрестная;
конструктивная прочность композита в кольцевом направлении к = 70 кг/мм2; в осевом – о = 40 кг/мм2;
модуль упругости в кольцевом направлении Ек = 4800 кг/мм2;
восевом направлении Ео = 2800 кг/мм2.
1. Расчет действующих нагрузок
Схема крепления стеклопластикового трубопровода на одном из участков показана на рис. 11. Она включает фрагмент трубы, закрепленной на двух опорах. Здесь взяты два типовых вида крепления: на левой опоре – жесткое крепление (заделка) в кольцевом металлическом ложементе, на правой опоре – шарнирное крепление, позволяющее трубе сдвигаться в осевом направлении, а также поворачиваться при изгибе на небольшой угол.
32
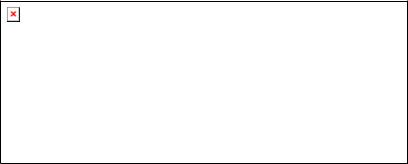
|
max |
|
3 |
|
d |
||
1 |
2 |
|
|
|
|
L
Рис. 11. Фрагмент стеклопластикового трубопровода, закрепленный на двух опорах: 1 – жесткое крепление; 2 – стеклопластиковая труба; 3 – шарнирное крепление; max – максимальный прогиб трубы в средней части; L – длина пролета; d – диаметр стеклопластикового трубопровода
На трубу действуют несколько нагрузок:
собственная масса трубы;
масса воды в трубе;
внутреннее давление воды в трубе;
осевые усилия от температурных деформаций;
другие факторы.
Мы рассмотрим только два первых вида нагрузок, наибольшим образом влияющих на прогибы.
Будем пользоваться расчетными формулами, известными из сопромата, для определения прогиба балки (стержня, трубы и т.п.). В этих формулах, в соответствии с нашим примером, задаются погонные нагрузки на единицу длины. Примем в расчетах погонных нагрузок за единицу длины трубы 1 см.
Погонную массу стеклопластиковой трубы – вес участка трубы длиной 1 см – определим по формуле
qтp dcp l тp , |
(31) |
где dср = 31 см – средний диаметр трубы;– толщина стенки трубы;
l – погонная длина участка (l = 1см);тр – плотность материала трубы.
Подставим исходные данные в формулу (31):
33
qтр = 3,14 31 1 1 1,9 = 185 г/см.
Далее определим погонную нагрузку от массы воды в трубе
на 1 см ее длины: |
|
|
|
q R2l |
, |
(32) |
|
в |
в |
|
|
где R – внутренний радиус трубы; |
|
|
|
в = 1 г/см3 – плотность воды. |
|
|
|
Подставим исходные данные в формулу (32): |
|
||
qв = 3,14 152 1 |
1 = 706 г/см. |
|
|
Так как обе нагрузки вызваны гравитационными |
силами |
и направлены в одну сторону, вниз, то общая погонная нагрузка будет равна их сумме:
q qтр qв 185 706 891 г/см = 0,89 кг/см. |
(33) |
2. Определение прогиба трубы
Из сопромата известны формулы для определения максимального прогиба балки (трубы) с учетом условий крепления и действующих нагрузок. Для нашего случая формула имеет вид
max |
qL4 |
, |
(34) |
|
50EJ |
||||
|
|
|
где q – погонная поперечная нагрузка на трубу; L – расстояние между опорами (пролет);
50 – коэффициент, учитывающий способ крепления трубы; Е – модуль упругости композита (в осевом направлении); J – момент инерции трубы.
Определим момент инерции трубы по формуле
J |
d 3 |
, |
(35) |
н |
|||
|
8 |
|
|
где dн – наружный диаметр трубы.
34

J |
3,14 323 |
1 |
4 |
8 |
|
12 860 см . |
|
|
|
|
Необходимо задать также длину пролета, примем L = 10 м. Тогда максимальный прогиб трубы
max |
|
0,89 10004 |
4,94 см. |
|
50 |
280 000 12 860 |
|||
|
|
3. Оценка деформаций от прогиба
Из сопромата известна формула для определения деформаций стержня (трубы) при прогибе на двух опорах
|
6 max2 |
d . |
(36) |
|
L |
|
|
Подставим исходные данные в эту формулу:
6 10004,942 32 0,001 0,1 %.
4.Определение длины пролета
Из практики эксплуатации стеклопластиковых трубопроводов известно, что герметичность труб сохраняется до уровня деформаций 0,35…0,40 %. С учетом коэффициента запаса по герметичности, который принимаем kг = 2, допускаемый уровень деформаций будет 0,17…0,20 %. Сравнивая полученную деформацию трубы = 0,1 и допустимый уровень 0,18…0,20 %, видим, что есть возможность увеличить расстояние между опорами, тем самым уменьшить общее количество опор трубопровода. Увеличим длину пролета с 10 до 12 м и повторим расчеты по формулам (34), (36).
Максимальный прогиб max |
|
0,89 12004 |
11,6 см. |
|
50 |
280 000 12 860 |
|||
|
|
35

Максимальная деформация max 6 11,6 232 0,00158 0,16 %. 1200
Полученная деформация по своему значению меньше допустимой, но достаточно близка к ней. Поэтому примем окончательно следующие параметры:
L = 12 м – длина пролета (расстояние между опорами);
max = 11,6 см – максимальный прогиб трубы в ее средней части;
max = 0,16 % – максимальная деформация трубы при изгибе. Для закрепления пройденного материала предлагается решить аналогичный пример для трубы с диаметром d = 200 мм
и толщиной стенки = 3 мм.
Практическое занятие № 7
РАСЧЕТ ЛИНЕЙНОЙ ПЛОТНОСТИ КОМПЛЕКСНЫХ СТЕКЛОНИТЕЙ ДЛЯ ПЛЕТЕНИЯ АРМИРУЮЩЕГО КАРКАСА ЗАДАННОГО ДИАМЕТРА И ТОЛЩИНЫ
Производство изделий из композиционных материалов связано с применением разных методов формования. Наиболее отработанный и применяемый – это метод намотки. Намотка обеспечивает большое разнообразие изделий: труб, конусов, оболочек, сосудов давления типа «кокон», сферических емкостей и других форм.
Использование в качестве армирующего материала нитей, жгутов, ровингов, лент позволяет при намотке добиваться такой ориентации армирующих волокон и структуры композита, которая бы наиболее полно соответствовала характеру напряженнодеформированного состояния, вызванного действующими на изделие нагрузками.
Другой способ формования, также широко применяемый, – это выкладка с последующим прессованием. В качестве арми-
36
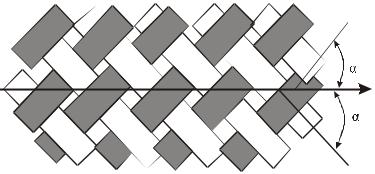
рующего компонента в нем используют в основном ткани и ленты. Способ эффективен для конструкций плоской, близкой к плоской, выпуклой формы с незамкнутым поперечным сечением.
Для трубчатых, стержневых, профильных длинных элементов применяют формование экструзией или пультрузией. В качестве армирующего элемента используют короткие волокна, дисперсные частицы, а также непрерывные прочные нити.
Сотрудниками кафедры «Технология, конструирование и автоматизация в специальном машиностроении» Пермского государственного технического университета в 1998–2003 годах разработана новая технология формования изделий из композитов, основанная на применении плетеных армирующих каркасов. Схема композиционного материала с плетеным армирую-
щим каркасом приведена на рис. 12.
x
Рис. 12. Схема плетеной армирующей структуры
Структура имеет пространственную форму, образованную двумя семействами нитей, направленных по пересекающимся спиральным траекториям. При этом каждая нить одного направления последовательно проходит под и над нитями другого направления. Фрагмент плетеного каркаса из комплексных стеклонитей показан на рис. 13.
37
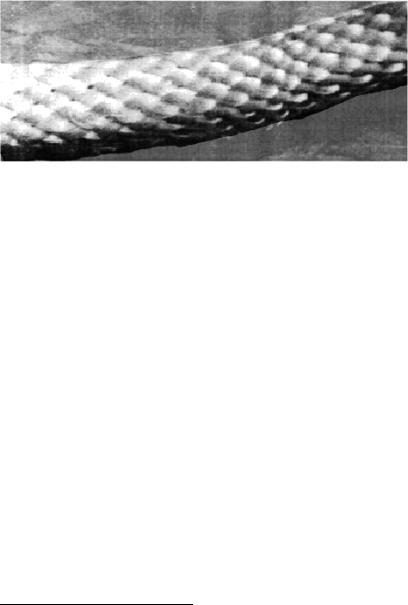
Рис. 13. Плетеный армирующий каркас
Каркас плетут на специальной установке на оправку, по мере плетения он плавно стягивается с оправки, трансформируется на направляющих роликах с трубчатой формы в плоский рукав, который наматывается на приемную кассету. В таком удобном виде каркасы складируются, и по мере производственной потребности нужный каркас разрезается на заготовки, которые используют для армирования композитных изделий. Дальнейшая технология состоит в одевании каркаса на формообразующую основу, пропитке его связующим и последующем отверждении. Подробно с технологией изготовления различных изделий можно ознакомиться по учебному пособию «Новые технологии в производстве труб и других изделий из композитов»*.
На данном занятии рассмотрим решение практической задачи по технологической подготовке к плетению каркаса заданного диаметра и толщины. Приведем расчеты для конкретного каркаса.
Исходные данные:
d = 110 мм – диаметр каркаса (оправки);
= 1,0 мм – толщина каркаса;
= 40 – угол армирования каркаса;
n = 96 – количество комплексных нитей для плетения кар-
каса;
*Олейник Б. Д. Новые технологии в производстве труб и других изделий из композитов. Пермь: Изд-во Перм. гос. техн. ун-та, 2006.
38
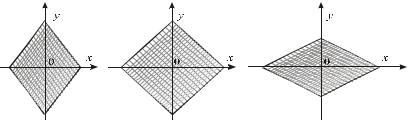
армирующие нити: комплексные высокопрочные стеклонити марки ВМП.
Необходимо рассчитать линейную плотность комплексных стеклонитей, которые обеспечат будущему каркасу заданную толщину = 1,0 мм.
1. Особенности структуры плетеного каркаса
Плетеный каркас представляет собой совокупность большого количества структурных ячеек в форме ромбов, образованных пересечениями и переплетениями двух семейств нитей. Каждая структурная ячейка образована двумя парами соседних нитей (рис. 14).
Формы, указанные в вариантах, определяются в зависимости от угла армирования :
при 45 реализуется вариант а;
при ≈ 45 реализуется вариант б;
при 45 реализуется вариант в.
а |
б |
в |
Рис. 14. Виды структурных ячеек: а – ромб, вытянутый в осевом направлении; б – квадратная ячейка; в – ромб, вытянутый в окружном направлении; x – окружное направление в каркасе; y – осевое направление в каркасе
Из рис. 15 можно определить размеры ромба, а количество ромбов в окружном направлении равно половине числа нитей, участвующих в плетении.
Окружная диагональ АС определяется по формуле
AC |
2 d |
, |
(37) |
|
n |
||||
|
|
|
||
|
|
|
39 |
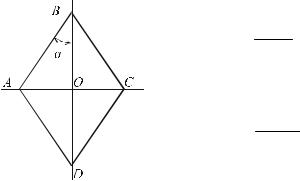
|
осевая диагональ ВD – по формуле |
||||
|
BD |
2 d |
, |
(38) |
|
|
|
|
n tg |
|
|
|
а сторона ромба АВ определяется по |
||||
|
выражению |
|
|
|
|
|
AB |
d |
. |
(39) |
|
|
|
|
n sin |
|
|
|
Из этих формул следует, что гео- |
||||
Рис. 15. Схема структур- |
метрические |
размеры |
структурной |
||
ячейки зависят от диаметра оправки, |
|||||
ной ячейки |
числа нитей и угла армирования. |
||||
|
|||||
Варьируя этими параметрами, можно получать множество вари- |
|||||
антов структурных элементов, а следовательно, и вариантов |
|||||
каркасов. |
|
|
|
|
|
2. Понятие застильности структурной ячейки |
Рассмотрим один из основных структурных параметров – линейную плотность комплексных стеклонитей. В простом понимании линейная плотность нити ассоциируется с ее толщиной. Но толщина одной и той же нити величина нестабильная, неустойчивая. Слегка скрученная нить будет иметь форму сечения, близкую к кругу, некрученная нить имеет форму, близкую к эллипсу. Одна и та же нить, в зависимости от ее подготовки, натяжения и других влияющих факторов может иметь различную форму сечения. Поэтому термин «толщина нити» здесь будет неопределенным, некорректным.
Понятие линейной плотности нити, выраженной конкретным числом и размерностью, позаимствовано из текстильной отрасли. Оно означает вес в граммах данного типа нити длиной 1000 м; единица измерения линейной плотности называется «текс». Например: комплексная нить имеет линейную плотность Т = 1600 текс, это означает, что отрезок этой нити длиной 1000 м имеет массу 1600 г. При плетении каркасов используют
40