
книги / Формовочные материалы
..pdfПрочность формовочной или стержневой смеси после заливки называют вторичной прочностью. Важной характеристикой является поверхностная прочность – сопротивление поверхностного слоя формы или стержня истиранию. Поверхностная прочность характеризуется осыпаемостью. Косвенным методом определения прочности сырых форм является замер их твердости, определяемой глубиной вдавливания стального шара твердомера в испытуемую поверхность.
Сыпучесть смеси влияет на зависание ее в бункерах, на заполнение и равномерное распределение смеси при засыпке в опоку, на длительность и качество перемешивания в смесителях. С сыпучестью связана комкуемость – способность смеси образовывать комки. Сыпучесть и комкуемость зависят от прочности связей песчинок в местах контакта. Увеличение начальной (насыпной) плотности смеси повышает равномерность уплотнения формы, поэтому смеси должны иметь хорошую сыпучесть – минимальную комкуемость.
В процессе заливки расплава в форму и охлаждения отливки внутренние стенки формы нагреваются до высоких температур, сопоставимых с температурами заливаемого расплава, поэтому и сами формовочные материалы должны обладать высокой огнеупорностью. Это одно из главных требований, предъявляемых к формовочным материалам. Огнеупорность (термохимическая устойчивость) – способность смеси сопротивляться размягчению или расплавлению под действием температуры расплава. Огнеупорность смеси зависит от огнеупорности ее составляющих и их количественного соотношения. Огнеупорность формовочных и стержневых смесей уменьшается с увеличением примесей в песке и глине; чем меньше примесей, пыли, больше диоксида кремния и крупнее зерна песка, тем выше огнеупорность смеси.
При заполнении формы расплавом органические материалы, входящие в состав смесей (например, связующие, опилки), газифицируются, сгорают и выделяют пары и газы. В формовочных материалах содержится вода, ее количество может быть определено с по-
11
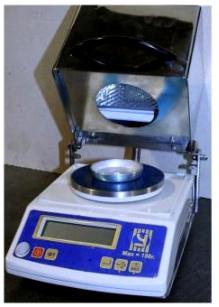
мощью прибора, представленного на рис. 5. Влага, содержащаяся в смесях, испаряется и образует водяные пары. Это свойство смесей называется газотворностью. Газотворность – способность смеси выделять пары и газы при заливке. По количеству паров и газов, выделяющихся из 1 г смеси, определяется ее газотворность. Образующиеся газы, пары и воздух стремятся выйти из формы через ее поры, поэтому формы и стержни должны иметь достаточную газопроницаемость.
Рис. 5. Прибор для ускоренного определения влажности
Газопроницаемость – свойство смеси пропускать через себя газы. Она зависит от качества и количества глинистой составляющей и песчаной основы в смеси. С увеличением песка в смеси, с увеличением его крупности газопроницаемость смеси повышается. При уменьшении этих характеристик песков газопроницаемость смеси снижается. Газопроницаемость смеси зависит также от формы зерен песка, степени его уплотнения, влажности, наличия в нем пыли, угля и т.п. Так, с увеличением количества пыли в песке уменьшается его газопроницаемость. При
12
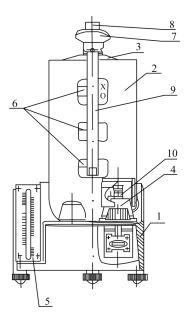
быстром газообразовании и недостаточной газопроницаемости смеси давление газа превышает давление залитого расплава и газ стремится выйти из формы не через смесь, а через расплав. Это способствует появлению газовых раковин в отливках.
Схема прибора для определения газопроницаемости представлена на рис. 6. Переменными и наблюдаемыми на приборе величинами для определения газопроницаемости являются продолжительность прохождения через образец воздуха объемом 2000 см3 и его давление перед образцом.
Рис. 6. Прибор для определения газопроницаемости:
1 – основание; 2 – бак; 3 – колокол; 4 – узел для установки гильзы;
5 – шкала; 6 – таблица; 7 – |
ручка; 8 – кнопка; |
9 – указатель; 10 – |
ниппель |
В процессе затвердевания и охлаждения отливки ее размеры уменьшаются вследствие усадки металла. Песчано-глинистая форма препятствует усадке металла, в результате чего в отливке могут возникнуть напряжения и появиться трещины. Поэтому и
13
формовочные, и стержневые смеси должны обладать податливостью. Податливость – способность смесей сокращаться в объеме и перемещаться под действием усадки отливки.
Высокая прочность и газопроницаемость смесей обеспечиваются однородностью – равномерным распределением в смесях их составляющих в результате перемешивания.
Формовочные и стержневые смеси должны обладать минимальной прилипаемостью к моделям и стержневым ящикам, что зависит от содержания в них влаги, связующей добавки и ее свойств. С увеличением количества жидкости в смеси прилипаемость смеси повышается.
Гигроскопичность – способность формовочной или стержневой смеси поглощать влагу из воздуха. Она определяется свойствами связующей добавки. Например, стержни, изготовленные с применением сульфитной барды, обладают большой гигроскопичностью, поэтому собранные формы с такими стержнями нельзя долго выдерживать перед заливкой металла, так как это ведет к увеличению брака по газовым раковинам.
Долговечностью называется способность смесей сохранять свои свойства при повторных заливках. Чем долговечнее смесь, тем меньше добавляют в отработанную смесь свежих формовочных материалов при ее переработке. Свойства смеси можно восстановить за счет освобождения ее от пыли и добавления в нее свежих песка и глины.
Выбиваемость – способность стержневой смеси легко удаляться из охлажденной отливки при выбивке. Выбиваемость зависит от количества песка, глины и вида связующего в стержневых смесях.
1.1.4. Происхождение песков и глин
Пески и глины относятся к осадочным горным породам, которые образуются в результате разрушения изверженных или первичных горных пород – гранита, порфира, диабаза, базальта и других. Часть этих материалов имеет очень сложный мине-
14
ралогический состав. Под действием солнца, воды и воздуха эти породы постепенно разрушаются. Продукты разрушения горных пород называются метаморфическими породами. Гранит состоит из кварца, слюды, полевого шпата, и, разрушаясь, он распадается на эти составные части.
Известно, что кварц является основной составляющей кварцевых формовочных песков, содержащих 90–98 % этого минерала. Остальную часть составляют различные примеси: слюда, полевые шпаты, окислы железа и щелочноземельных металлов. Все примеси имеют более низкую температуру плавления, чем кварц, и, следовательно, снижают огнеупорность песков. Примеси сообщают пескам ту или иную окраску.
Формовочные пески добывают в карьерах, поэтому часто их название соответствует названию того карьера, где их добывали, например, люберецкий, гусаровский, кичигинский и другие. Формовочные глины также могут носить название карьера. Пески добывают открытым способом. Если песок содержит примеси или имеет неоднородный зерновой состав, на месте добычи песка проводят его обогащение, освобождая от посторонних включений и деля на фракции по размерам зерен.
1.2.Свойства минералов, входящих в состав формовочных и стержневых смесей
1.2.1. Основные свойства минералов
Всостав формовочных материалов входят следующие минералы: окислы (кварц, корунд и др.); карбонаты (кальцит, магнезит); безводные легкоплавкие силикаты (кальциевый, калиевый, натриевый полевые шпаты); безводные тугоплавкие силикаты (циркон и др.); водные силикаты (асбест, каолин, монтмориллонит).
Наиболее существенные для литейного производства свойства минералов представлены в табл. 1.
15

|
|
Свойства минералов |
|
Таблица 1 |
|
|
|
|
|
|
|
|
|
|
Класс |
Название |
Химический состав |
Удельный |
t плавл., |
вес, г/см3 |
ºС |
|||
|
|
|
|
|
Окислы |
Кварц |
SiO2 |
2,65 |
1710 |
|
Корунд |
Al2O3 |
3,5–4,5 |
1900 |
Карбонаты |
Кальцит |
CaCO3 |
2,7 |
880–900 |
|
Магнезит |
MgCO3 |
3,2 |
470–600 |
|
|
|
|
(разложен.) |
Силикаты |
Калиевый |
K2O·Al2O3·6SiO2 |
2,57 |
1140 |
безводные |
полевой |
|
|
|
легкоплав. |
шпат |
|
|
|
Силикаты |
Циркон |
ZrO2·SiO2 |
4,5–4,7 |
Свыше |
безводн. |
|
|
|
2000 |
тугоплав. |
|
|
|
|
Силикаты |
Асбест |
3MgO·CaO·4SiO2·H2O |
2,5 |
1275 |
водные |
Каолин |
Al2O3·2SiO2·2H2O |
2,6 |
1750 |
|
Монтморил- |
Al2O3·4SiO2·nH2O |
1,8 |
Значение |
|
лонит |
|
|
зависит от n |
|
|
|
|
|
Нередко указывается твердость минералов по шкале Мооса. |
||||
Эта шкала |
предложена в 1811 году немецким минералогом |
Ф. Моосом для определения относительной твердости минералов.
В качестве |
эталонов приняты 10 минералов, расположенных |
||
в порядке возрастающей твердости. |
|
|
|
Для |
специалистов-литейщиков |
практический |
интерес |
представляют следующие минералы этой шкалы: тальк – |
твердость 1, |
гипс – твердость 2, кальцит – твердость 3, кварц – твердость 7, корунд – твердость 9.
1.2.2. Кварц и его модификации
Повсеместно применяются для приготовления формовочных и стержневых смесей кварцевые пески, поскольку они широко распространены в природе (земная кора почти наполовину состоит из кислорода и более чем на четверть – из кремния), а поэтому
16
PNRPU
дешевле других песков и вместе с тем обладают необходимыми технологическими свойствами, главное из которых – огнеупорность.
Основной составной частью этих песков является минерал кварц (кремнезем), представляющий собой химическое соединение SiO2 плотностью 2,5–2,8 г/см3 с температурой плавления 1713 ° С. Известно, что кварц – самый распространенный минерал в природе, в земной коре его содержится более 12 %. В природе кварц находится уже в измельченном состоянии, в виде зерен. Характерной особенностью минерала является то, что он не разлагается при нагревании.
Недостатки кварца: при нагреве он переходит в другие кристаллические модификации, что сопровождается изменениями его объема; по своему составу это кислый материал. При 573° С α-кварц переходит в β-кварц, объем изменяется на ± 2,4 %; при 870° С β-кварц переходит в β-тридимит, изменение объема 15,1 %; при 1470° С β-тридимит переходит в β-кристобалит , изменение объема 4,7 %; при 1713° С β-кристобалит переходит в расплав, изменение объема 0,1 %. Линейные размеры изменяются примерно на 1/3 от увеличения объема. Превращения при температурах 870 и 1470° С идут очень медленно, в реальных условиях тридимит и кристобалит не образуются даже при многократном использовании формовочных материалов. Превращение при 573° С опасно еще и тем, что оно обратимо, то есть при охлаждении материала происходит обратный процесс. Таким образом, при многократных нагревах и охлаждениях зерна песка растрескиваются и формовочная смесь загрязняется пылью. Это ведет к уменьшению газопроницаемости смеси.
Второй недостаток кварца в том, что кварц – это кислый материал, а окислы металлов относятся к основным материалам. Эти продукты склонны к химическому взаимодействию, к сплавлению между собой. Сплав компонентов часто имеет температуру плавления более низкую, чем вступившие в реакцию вещества, например эвтектика. Таким образом, идет взаимодействие
17
между окислами и, прежде всего, с участием окислов железа, что способствует образованию пригара наотливках.
1.2.3. Корунд, карбонаты, силикаты
Корунд – минерал, природный безводный глинозем Al2O3. Кристаллизуется в тригональной системе. Кристаллическая структура корунда сложена атомами алюминия, окруженными шестью атомами кислорода, которые образуют плотнейшую гексагональную упаковку. В виде крупных кристаллов корунд встречается редко, чаще вместе с другими минералами образует средне- и тонкозернистые агрегаты. Он имеет твердость 9 по минералогической шкале. Корунд характеризуют большая химическая стойкость и высокая температура плавления. Минерал имеет различную окраску: от буро-серой, розоватой до красной или от голубовато-серой до густо-синей. Цвет определяется составом примесей минерала. В промышленных масштабах искусственные корундовые материалы получают в результате плавления боксита в электропечах с восстановителем, как правило, с железными опилками. Бокситы – это горная порода, состоящая в основном из гидратов глинозема (Al2O3 · H2O) и окислов железа с примесью других минералов.
Электрокорунд – искусственный корундовый материал, способный хорошо проводить тепло. Он амфотерен и, соединяясь с другими элементами, не снижает у них температуру плавления. Его недостатки: высокая стоимость и дефицитность. Используется в качестве добавки в противопригарные краски, в состав которых можно вводить и сам глинозем. Электрокорунд широко применяется при литье по выплавляемым моделям.
Кальцит, известковый шпат – минерал химического состава CaCO3, содержит около 56 % CaO и 44 % CO2, а также примеси магния, железа, марганца (до 8 %), цинка, кобальта, стронция и бария. Кристаллизуется в тригональной системе. Встречается в виде разнообразных кристаллов, в виде плотных зернистых и землистых масс (мел), в натечных (сталактиты) и других формах. В структуре
18
кальцита атомы Ca и C расположены по узлам ромбоэдрических решеток, как бы вдвинутых одна в другую. Атомы O группируются по три вокруг C, располагаясь в одной с ними плоскости.
Кальцит хрупок, твердость по минералогической шкале – 3; плотность 2720–2800 кг/м3. При нагревании разлагается при температурах свыше 825° С; легко растворяется в кислотах. Кальцит – один из наиболее распространенных минералов в земной коре, является главной составной частью известняков, мраморов и других осадочных и метаморфических пород.
Магнезит – минерал из класса карбонатов, состав MgCO3, содержит MgO около 48 % и CO2 около 52 %, изоморфные примеси: часто – железо, реже – марганец, кальций. Кристаллизуется в тригональной системе, имеет совершенную кристаллическую структуру, аналогичную кальциту. Цвет белый, желтоватый. Твердость по минералогической шкале 3,75–4,25; хрупок.
И кальцит, и магнезит считаются вредными примесями в песке, так как при высоких температурах они разлагаются с выделением газа (CO2), а, например, CaO способна образовывать легкоплавкие соединения.
Силикаты – соли кремниевой кислоты. Известны безводные легкоплавкие силикаты: калиевый, кальциевый, натриевый полевые шпаты; безводные тугоплавкие силикаты: циркон, оливинит; водные силикаты: асбест, каолин, монтмориллонит.
Полевые шпаты – группа наиболее распространенных породообразующих минералов, составляющих более 50 % земных горных пород. Полевые шпаты состоят из алюмосиликатов натрия, калия, кальция с примесями бария, стронция, свинца, железа и других элементов. Основой структуры всех полевых шпатов является трехмерный каркас, состоящий из тетраэдрических групп (Al,Si)O4, в которых от одной трети до половины атомов Si замещено Al. Большое число разновидностей полевых шпатов обусловлено сложными соотношениями состава (главных элементов и примесей), упорядоченностью распределения атомов алюминия и кремния по структурным положениям и пр. Твердость
19
полевых шпатов по минералогической шкале 6–6,5; плотность 2500–2800 кг/м3. Полевые шпаты сами по себе бесцветны; различную окраску (серую, розовую, красную, зеленую, черную и др.) им придают мельчайшие включения других минералов.
Кальциевый, калиевый, натриевый полевые шпаты – вредные примеси в песке, так как у них низкая температура плавления.
Циркон (в переводе с персидского – золотистый) – минерал из класса островных силикатов, Zr[SiO4]. Цвет минерала различен: коричневато-желтый, коричневый, сероватый, красный, розовый; может быть бесцветным. Циркон прозрачен до просвечивания. Твердость по минералогической шкале до 7–8 единиц. В природе находится в виде цирконового песка или даже более дисперсного материала. В смесях используется в виде цирконового концентрата, отличающегося химической инертностью и невысоким коэффициентом термического расширения. Последнее свойство важно с технологической точки зрения: при эксплуатации материал не будет растрескиваться. Пылевидный циркон используется при приготовлении противопригарных красок. Подобными свойствами обладает и материал оливинит.
Асбест (в переводе с греческого – неразрушимый) – название, объединяющее группу тонковолокнистых минералов из класса силикатов, образующих агрегаты, сложенные тончайшими гибкими волокнами. Этими свойствами обладают минералы двух групп – серпентина и амфибола, известные под названиями хризотиласбеста и амфиболасбеста, различные по атомной структуре. По химическому составу асбестовые минералы – водные силикаты магния, железа и отчасти кальция и натрия. Наибольшее значение имеет хризотил-асбест (95 % всего используемого асбеста). Цвет минерала в куске зеленовато-серый, блеск шелковистый. Твердость по минералогической шкале 2–2,5; плотность 2500 кг/м3. Волокна гибки, обладают высокой прочностью на разрыв (300 кг/мм2), высокой огнестойкостью (температура плавления около 1500° С), плохо проводят тепло и электричество. Длина волокон – от долей миллиметра до 50 мм, иногда и более, толщина составляет доли
20