
книги / Формовочные материалы
..pdfсвежих материалов в пределах 500–4000 кг на 1000 кг годных отливок (по данным московских заводов ЗИЛ и «Станколит»).
Процесс приготовления песчано-глинистых формовочных смесей складывается из следующих основных операций: предварительной подготовки и обработки свежих формовочных материалов; предварительной обработки отработанной формовочной смеси; приготовления смеси из предварительно подготовленных свежих
иотработанных формовочных смесей, добавок и связующих.
2.3.2.Предварительная подготовка формовочных материалов
Всовременных крупных литейных цехах предварительную обработку свежих формовочных материалов не производят, так как эти материалы поступают в готовом виде: песок просушенный и обогащенный, глина и уголь просушенные, молотые и расфасованные в мешках. Однако многие литейные цехи используют свежие формовочные материалы в сыром виде. В этом случае для приготовления песчано-глинистых смесей проводят предварительную обработку свежих материалов: песок и глину сушат и просеивают; глину и уголь дробят и измельчают в мельницах.
Для сушки песка и глины служат различные сушильные печи. Наиболее распространены барабанные горизонтальные сушильные печи, используют также установки с кипящим слоем и другие. Свежий
песок сушат при 250° С. Производительность таких сушил 5–20 т/ч ивыше.
Сухую глину размалывают в бегунах или в шаровых мельницах до порошкообразного состояния и просеивают. Для тонкого размельчения глины и каменного угля применяют шаровые мельницы. Производительность шаровых мельниц 100–8000 кг/ч. Часто вместо сухой глины применяют глинистую и глиноугольную суспензию (смесь глины или глины и угольного порошка с водой). При использовании суспензии глину и бентонит можно не сушить и не молоть, в связи с чем отпадают некоторые операции подготовки и транспортировки этих материалов.
71
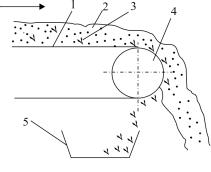
2.3.3. Обработка отработанной формовочной смеси
Отработанную формовочную смесь перед повторным использованием предварительно обрабатывают.
1.Крупные комки смеси, образующиеся после выбивки опок, обычно разминают гладкими или рифлеными вальцами.
2.Металлические частицы отделяют от смеси магнитными сепараторами, установленными на участках передачи отработанной смеси с одного конвейера на другой (рис. 13 ).
Рис. 13. Магнитный сепаратор
Лента 1 с формовочной смесью 2 огибает шкив 4, внутри которого смонтирован электромагнит. Немагнитные частицы формовочной смеси соскальзывают с ленты, а магнитные частицы 3 – застывшие капли металла, крючки, шпильки и т.д. – продолжают двигаться вместе с лентой. Когда действие магнитного шкива прекращается, они попадают в бункер 5.
3.Просеивают смесь на обычном сите или на передвижной смесеприготовительной установке, где происходит отделение металлических и других частиц.
4.Гомогенизируют (выравнивают по составу) смесь.
5.Проводят испарительное охлаждение.
2.3.4. Приготовление формовочных и стержневых смесей
Важной операцией приготовления смеси является перемешивание ее составляющих.
72
Перемешивание смеси необходимо для равномерного распределения ее составляющих по объему. В процессе перемешивания глина или связующие обволакивают зерна песка, разрушаются комки отдельных составляющих и равномерно распределяется влага. Хорошо перемешанная смесь обладает высокими технологическими свойствами: прочностью и газопроницаемостью. Для приготовления песчано-глинистых формовочных смесей используют смесители литейные чашечные, в которых рабочими органами являются катки и плужки. Эти смесители называют также бегунами.
Применяют бегуны непрерывного и периодического действия. В бегунах периодического действия смешивание осуществляется порциями (замесами). Порция материалов загружается в бегуны, перемешивается, а затем выгружается. В смесителях непрерывного действия загрузка, перемешивание и выгрузка ведутся одновременно. Такие смесители чаще применяют в условиях автоматического производства.
По конструкции бегуны могут быть с вертикальными катками и центробежные.
Порядок загрузки составляющих смеси. Сначала загружают сухие материалы: песок, глину и отработанную формовочную смесь. Сухую смесь перемешивают примерно 1–3 мин, затем ее увлажняют. В случае применения глинистой или глиноугольной суспензии влажность регулируют добавлением суспензии и воды. После увлажнения смесь еще раз перемешивают в течение нескольких минут. Связующие загружают последними. Время перемешивания составляет для смеси наполнительной 2–3 мин, облицовочной 5–
10мин.
2.4.Регенерация формовочных и стержневых смесей
2.4.1. Понятие о регенерации
Регенерация (восстановление) заключается в извлечении песка из отработанной смеси и приведении его свойств в соответствие с установленными техническими требованиями на формовочные пески. Необходимость регенерации песка из отработанных смесей обу-
73
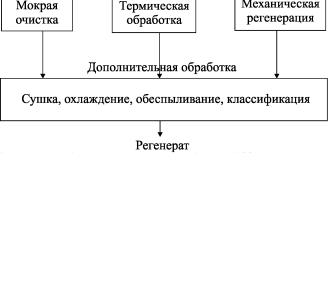
словлена требованиями уменьшения загрязнения окружающей среды, рационального использования месторождений ценных песков, снижения брака отливок.
Рис. 14. Способы регенерации песков
Для регенерации песка используют различные способы (рис. 14). После первичной обработки, во время которой металл отделяют от смеси путем магнитной сепарации, дробления, просеивания, выполняют операцию отделения связующего и добавок от зерен песка. Для этого используют различные способы, выбор которых зависит от состава смеси, характера связующих, добавок, а также условий производства, массы отливок, мощности цеха и т.д.
2.4.2. Изменение свойств смеси при многократном использовании.
Смеси, направляемые в отвал
Известно, что формовочная смесь участвует в технологическом процессе многократно, сначала как сформированная из материалов
74
освежения, а затем как оборотная. Формовочная смесь, находясь постоянно в обороте, постепенно теряет свои первоначальные свойства. Зерна кварцевого песка при резком нагревании разрушаются, появляются более мелкие зерна осколочной формы и пыль. Пыль заполняет поры между песчинками, что резко понижает газопроницаемость смеси, в результате увеличивается склонность ее к образованию пригара.
Комплекс технологических операций по очистке смеси от механических примесей и восстановлению ее технологических свойств называется регенерацией.
Регенерации подвергаются смеси, выбрасываемые «в отвал». «В отвал», т.е. на выброс, направляются:
1)все стержневые смеси;
2)смеси, которые оседают в очистном отделении (т.е. прилипшие к отливке элементы формовочных и стержневых смесей);
3)та часть смеси, которая при подготовке отработанной смеси не проходит через сито.
Эти группы смесей согласно их низким потребительским качествам и определяют понятие «отвал» смесеприготовительного производства.
2.4.3.Возможность и необходимость извлечения песка. Значение регенерации
Доказано, что в смесях, направляемых в отвал, зерна песка еще не все разрушились, есть зерна, которые можно применять в технологическом процессе. Они составляют около 70–80 % массы отвальной смеси. Для очищения годной зерновой части этих песков от примесей используется регенерация.
Отработанная смесь не пригодна для производственных целей, и тем более не пригодна она для жизнедеятельности флоры и фауны в природных условиях.
Актуальность проблемы регенерации формовочных песков обусловлена:
1) резким повышением цен на пески;
75

2)ужесточением экологических требований,
3)увеличением расходов на содержание отвалов,
4)удорожанием транспортных услуг.
Использование регенерированного песка при получениии отливок в оболочковых формах дает ежегодную экономию в сотни тысяч долларов по сравнению с вариантом, предусматривающим применение свежего песка и направление отработанной смеси в отвал, поскольку стоимость свежего песка составляет 22–24 американских доллара за тонну, регенерата – 8–10 долларов за тонну.
Например, в штате Иллинойс (США) в отвалы направляют примерно 800 тысяч тонн смеси, бывшей в употреблении. Расходы на ее годичное содержание вотвалах достигают 40 долларов затонну.
Прогнозируется, что экономическая эффективность регенерации сохранится и в дальнейшем.
К регенерированным пескам предъявляют те же требования, что и к свежим. Однако экономически и технологически это не всегда оправданно1. Регенерированные пески можно использовать, если:
1)качество смесей на регенерированном песке равноценно качеству смесей на свежем песке;
2)качество отливок, изготовленных с применением регенерированных песков, соответствует качеству отливок, изготовленных с использованием свежих песков;
3)в процессе многократного регенерирования песков в них не накапливаются компоненты, ухудшающие санитарно-гигиени- ческие условия работы.
При соблюдении указанных требований допустимо любое отличие регенерированных песков от свежих. При этом подход к регенерации песков из отработанных смесей должен быть дифференцированным.
По степени очистки отработанных песков выделяют два вида регенерации: частичную, при которой в регенерате остается достаточно большое количество глинистой составляющей и органиче-
1 Водеников Ю.А. Регенерация формовочных песков // Литейное производство. 1993. № 1.
76
ских компонентов, и полную, при которой регенерированный песок соответствует свежему исходному песку, втомчислеи обогащенному.
Частичную очистку осуществляют пневматическими и механическими методами регенерации. Гидравлическая регенерация для смесей, содержащих в качестве связующих глинистую составляющую, является полной, а для смесей с органическими компонентами – частичной. Термическая регенерация является полной для смесей, содержащих только органические компоненты. Для обеспечения полной регенерации смесей, содержащих как глинистую составляющую, так и органические компоненты, рекомендуется использовать совмещенную регенерацию, например термическую и механическую.
2.4.4. Способы регенерации: механическая, пневматическая, гидравлическая, термическая
Во время гидравлической регенерации песок перелопачивается
вводе, в результате происходит интенсивное растворение водорастворимых связующих и примесей, а также абразивное снятие обволакивания. Недостаток этого способа заключается в том, что расходуется большое количество воды на промывку и большое количество электроэнергии на высушивание песка.
При термической регенерации происходит обжиг смеси, выжигание органических связующих. Обработку выполняют в печах кипящего слоя, на виброжелобах с инфракрасными горелками. Песок нагревают до температуры выше 800–900° С, при этом сгорают пленки на поверхности песчинок, глинистые вещества легче отделяются от песка, так как теряют прочность. Недостаток метода – необходимость расходовать топливо, чаще всего природный газ; поэтому способ дорогостоящий.
Механическая регенерация заключается в абразивном воздействии на песок, при этом часть песка уносится в виде пыли. Песок либо несколько раз пропускают через дробилку, либо обрабатывают
ввертикальном барабане со множеством полок, заполненных металлической стружкой. Стоимость этого способа регенерации песка наименьшая по сравнению с вышеописанными.
77
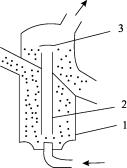
Рис. 15. Пневморегенератор
При механико-пневматической регенерации происходит соударение песчинок в потоке воздуха, трение их друг о друга. Такую регенерацию можно проводить в пневморегенераторах. Один из них показан на рис. 15, где 1 – корпус, 2 – разгонная труба, 3 – отражатель. В пневморегенераторе песчинки, ударяясь друг о друга, под действием воздуха поднимаются вверх, затем песок ссыпается по верхнему правому лотку и поступает в следующую секцию регенератора, их всего три. Воздух с пылью уносится в циклон. Этот способ регенерации прост, не требует больших затрат электроэнергии. Недостатком его является некоторое измельчение песка.
Возможности использования регенерата. Смеси с жидким стеклом в качестве связующего после регенерации можно использовать только в количестве 30 % вместо нового песка. Если использованные холоднотвердеющие смеси подвергались регенерации, то можно вводить до 70 % этих смесей вместо нового песка. Если пневморегенерации подвергались песчано-бентонитовые смеси, то их после обработки можно вводить до 90 % вместо нового песка.
2.5. Методика выбора рациональных составов формовочных и стержневых смесей
Для выбора формовочной смеси необходимо сделать следую-
щее:
1. Определить размеры формы и ее конфигурацию, массу получаемой заготовки, вид сплава.
78
Для получения чугунных отливок массой до 50 кг с толщиной стенки до 40 мм, для стальных отливок массой до 400 кг с толщиной стенки до 25 мм и для отливок из цветных сплавов можно использовать сырые песчано-глинииые смеси. Если масса заготовки больше указанных величин, то применяются подсушенные, сухие или химически твердеющие смеси
2.Определить температуру заливки сплава. Если температура заливки сплава превышает 1400° С, нужно использовать более огнеупорные формовочные материалы.
Отливки массой более 5000 кг из легированных сталей с толщиной стенки более 60 мм рекомендуется получать в формах из цирконового концентрата или хромита. Для марганцовистых сталей возможно применение магнезита.
3.Выбрав метод уплотнения формы, определить предполагаемую прочность формовочной смеси и уточнить используемые в ее составе связующие материалы.
При увеличении массы заготовки или при переходе к формовке на безопочных формовочных линиях следует использовать связующие материалы, придающие смесям большую прочность.
Для выбора стержневой смеси необходимо выполнить следующее.
1.Определить характер производства: крупносерийное, серийное, мелкосерийное, индивидуальное.
2.По характеру производства подобрать способ изготовления стержней.
В мелкосерийном и разовом производстве используются стержневые смеси, отверждаемые в сушилах. В условиях серийного
икрупносерийного производства возможно использование смесей, отверждаемых в оснастке. Это горячетвердеющие, жидконаливные самотвердеющие, холоднотвердеющие, быстрохолоднотвердеющие
идругие смеси.
3.Оценить выбранный способ изготовления стержней с точки зрения качества литой поверхности, оформляемой стержнем.
Если качество литой поверхности ниже заданного на чертеже отливки, необходимо подобрать состав специального покрытия для стержня или изменить способ его изготовления.
79
4.Зная вид сплава и температуру его заливки, определить условия работы стержня в литейной форме.
К этим условиям относятся рабочая температура стержня, наличие размывающего воздействия сплава, газопроводность стержня.
5.По геометрическим размерам, конфигурации, условиям работы в литейной форме и требованиям к качеству литой поверхности определить класс стержня.
6.По таблицам подраздела 2.2.2 подобрать состав смеси.
При выборе составов смесей, отверждаемых в оснастке, необходимо пользоваться специальной литературой.
80