
книги / Технология получения и отбелки полуфабрикатов бумажного производства
..pdf(Na2SiO3). При рН > 10,5 усиливаются побочные реакции щелочи с волокном, вызывающие потемнение массы и приводящие к снижению ее белизны.
Вести отбелку пероксидом при низких рН не имеет практического смысла, так как в кислой среде пероксид нестоек и легко разлагается на воду и молекулярный кислород, который бесполезно выделяется из древесной массы в воздух. Разложение пероксида увеличивается в присутствии ионов тяжелых металлов – Fe, Mn, Cu, Ni, которые образуют нестойкие пероксиды или комплексные соединения гидропероксидных ионов, ускоряющие разложение. Повышение температуры при отбелке в кислой среде еще более усиливает разложение пероксида. Для уменьшения вредного действия ионов тяжелых металлов в качестве стабилизатора добавляют MgSO4, однако при этом наблюдается уменьшение белизны.
Условия отбелки ДМ перексидом водорода:
расход пероксида |
2…5 % к а. с. волокну |
|
концентрация массы |
12…20 % |
|
температура |
50…70 °С |
|
рН начальный |
10,5…11,0 |
|
рН конечный |
7,5…8,5 |
|
продолжительность отбелки |
0,5…2,0 ч |
|
расход щелочи (NaOH) |
1,0…1,5 % |
|
расход силиката натрия |
5 % |
|
расход трилона Б |
0,2…0,5 % |
|
или тринатрийфосфата |
||
|
||
расход MgSO4 |
0,05 % |
Содержание Н2О2 в водном растворе (перманганатометрический метод) можно определить следующим образом.
10 мл раствора пероксида водорода разбавить в мерной колбе до 100 мл. В колбу для титрования (на 250 мл) поместить 10 мл разбавленного раствора пероксида водорода, 25 мл дистиллированной воды и 20 мл серной кислоты (1:4). Содержимое колбы титровать 0,1 н.
21
KМnО4 до появления розовой окраски, не исчезающей в течение 1 мин.
Н2О2 = а · 0,0017 · 1000,
где а – объем 0,1 н. KМnО4, пошедшего на титрование;
0,0017 – количество Н2О2, соответствующее 1 мл, точно 0,1 н. КМnО4.
Дитионит натрия Na2S2O4 · 2Н2О находит применение в качестве отбеливающего реагента в целлюлозно-бумажной промышленности. Этот сильный восстанавливающий агент является солью дитионистой кислоты H2S2O4, которая в свободном состоянии не получена.
Безводный дитионит натрия представляет собой мелкий кристаллический порошок белого цвета, хорошо растворимый в воде. Он вполне устойчив, в закрытых емкостях может сохраняться несколько месяцев.
Водный раствор дитионита натрия разлагается на воздухе до сульфита и сульфата натрия:
Na2S2O4 + Н2О + О2 = NaHSO4 + NaHSO3.
Реакция между дитионитом и кислородом воздуха – основная причина больших потерь дитионита.
В отсутствие воздуха растворы дитионита также нестабильны и происходит их разложение (самоокисление) на гидросульфит и тиосульфат:
2Na2S2O4 + Н2О = 2NaHSO3 + Na2S2O3.
Поэтому водные растворы дитионита, кроме S2O42–, содержат
SO42–, S2O32–, SO32–.
Применение дитионита натрия для отбелки древесной массы не требует сложного технологического оборудования, больших затрат дитионита, он хорошо отбеливает массу из хвойных пород. Отбелка дитионитом натрия не приводит к уменьшению показателей механической прочности, к снижению выхода древесной массы, поскольку восстановительная отбелка носит лигносохраняющий характер.
22
Отбелка дитионитом имеет следующую особенность: отбелку проводят при исключении доступа воздуха, для этого отбельный раствор дитионита натрия смешивается с древесной массой низкой концентрации непосредственно перед башней отбелки.
Дитиониты, являясь сильными восстановителями, при соответствующих рН среды и температуре значительно повышают белизну массы даже при небольшом их расходе. Расход дитионита натрия при отбелке еловой древесной массы колеблется от 0,5 до 1 %. При увеличении расхода дитионита свыше 1 % эффективность отбелки снижается.
Особую роль при отбелке дитионитом натрия играет рН среды, при которой протекает отбелка. Это связано с тем, что в зависимости от рН среды в водном растворе дитионита присутствует различное количество серосодержащих анионов, таких как SO42–, S2O32–, SO32–, НSO3–, НSO4–. Кроме того, разложение водного раствора дитионита сильнее всего происходит при рН = 4 и ниже. При таком рН в растворе образуется до 25 % тиосульфат-ионов, вызывающих коррозию оборудования и, как следствие, происходит попадание ионов тяжелых металлов в массу.
Оптимальной величиной рН, при которой должна протекать отбелка дитионитом, является рН = 5,0…5,5. При этом рН скорость разложения дитионита наименьшая.
При рН от 6,0 до 8,0 растворы дитионита медленнее разлагаются, однако присутствие щелочи отрицательно сказывается на отбелке древесной массы.
Существует несколько точек зрения на отбелку древесной массы дитионитом.
Считается, что белящимреагентомявляется дитионит-ионS2O42–. Однако некоторые исследователи считают, что в воде происходит разложение Na2S2O4 на гидросульфит Na и соль натрия непрочной сульфоксильной кислоты, которая является отбеливающим реа-
гентом:
Na2S2O4 + Н2О → NaHSO3 + NaHSO2.
23
Подтверждением данной теории является то, что отбелка древесной массы происходит и в том случае, когда в растворе практически отсутствуют дитионит-ионы. Восстановительная способность дитионита возрастает с повышением температуры, соответственно, увеличивается и эффективность отбелки, уменьшается ее продолжительность.
Условия отбелки дитионитом натрия (Na2S2O4):
расход Na2S2O4 |
1…1,5 % |
концентрация массы |
3…6 % |
температура |
50…70 °С |
начальный рН |
5…6 |
конечный рН |
3…4 |
продолжительность отбелки |
30…60 мин |
При отбелке дитионитом с целью уменьшения отрицательного воздействия ионов металлов, главным образом железа, обычно используются полифосфаты (триполифосфат ТПИФ Na5Р3O10), тринатрийфосфат, азотсодержащие органические соединения типа этилендиаминтетрауксусной кислоты (ЭДТА). Эти комплексообразующие соединения повышают конечную белизну массы. Расход этих веществ 0,2…1,0 % от а.с. волокна. Подают их в массу до перемешивания с дитионитом или одновременно с ним.
1.6.2. Пример расчета химических реагентов при отбелке древесной массы
Рассчитать количество реагентов, необходимых для отбелки 50 г а.с. ТММ пероксидом водорода по следующему режиму:
концентрация массы |
10 % |
расход к массе а.с. волокна |
|
Н2О2 |
3 % |
Na2SiО3 |
5 % |
ЭДТА |
0,20 % |
24 |
|
Принимаем влажность ТММ 60 %; начальный рН 11.
Исходя из заданного количества ТММ и концентрации массы рассчитывается объем отбельного раствора:
50 100 500 ì ë,
10
где 50 – масса а.с. ТММ, г; 10 – концентрация массы, %.
При влажности ТММ 60 % на отбелку потребуется
50 100 125 ã ÒÌ Ì ,
40
где 50 – масса а.с. ТММ, г; 40 – содержание а.с. ТММ в 100 г влажной ТММ, г.
Количество пероксида водорода, требующегося для отбелки при заданном расходе реагента 3 %,
50 3 1,5 ã,
100
где 50 – масса а.с. ТММ, г; 3 – расход Н2О2, %.
При концентрации исходного раствора Н2О2 50 г/л (раствор получается разбавлением концентрированного раствора пероксида водорода в 5…6 раз) для отбелки надо взять
1,5 1000 30 мл разбавленного раствора Н2О2. 50
При расходе Na2SiО3 5 % к массе а.с. волокна для отбелки 50 г ТММ потребуется
50 5 2,5 ã силиката натрия
100
или
2,5 1000 20,5 ì ë 1 М раствора, 122
25
где 122 – количество безводного силиката натрия, содержащегося в 1 л 1 М раствора.
Количество ЭДТА, добавляемое при отбелке в раствор, составит
50 0,20 0,1 ã
100
или при использовании 0,1 М раствора ЭДТА
0,10 1000 27 ì ë, 37,2
где 37,2 – количество ЭТДА, содержащееся в 1 л 0,1 М раствора. Количество воды, которое надо добавить для получения задан-
ного объема отбельного раствора (500 мл), составит
500 – (125 + 30 + 20,5 + 27) = 500 – 202,5 = 297,5 мл.
Примечание: при расходе Na2SiО3 5 % добавление щелочи для получения рН отбельного раствора, равного 11, не требуется.
После промывки массы проводят кисловку серной кислотой для инактивации оставшейся Н2О2 и для стабилизации белизны со снижением рН до 5,5…6,5. Кисловку проводят в течение 15 мин, затем массу отмывают дистиллированной водой до рН 5,5…6,5. Расход H2SО4 примерно 0,7 % к массе а.с. волокна. Концентрация массы при кисловке 5 %.
Отбелка дитионитом может проводиться самостоятельно в одну ступень или при отбелке в две ступени – после отбелки пероксидом.
Расчеты для отбелки проводят аналогичным образом (как и при отбелке пероксидом).
Для проведения отбелки рассчитывают необходимое количество сухого дитионита в граммах (из расчета 1,0…1,5 % к массе а.с. волокна) и растворяют его в воде, которая используется для разбавления ДМ (ДДМ или ТММ) до концентрации, необходимой для отбелки (например 4 %).
Готовить раствор дитионита нужно непосредственно перед отбелкой, так как он разлагается очень быстро, особенно при доступе воздуха.
26
2.ТЕХНОЛОГИЯ ЦЕЛЛЮЛОЗЫ
2.1.Способы делигнификации древесного сырья
Выделение целлюлозы из древесного или другого растительного сырья называется процессом варки. В связи с тем, что основным веществом, от которого стремятся освободить древесину в результате химической обработки (варки), является лигнин, процесс получения целлюлозы называется делигнификацией. Продуктом делигнификации является техническая целлюлоза.
В зависимости от свойств и вида применяемых химических реагентов все известные способы делигнификации делят на группы: кислотные, щелочные, окислительные, ступенчатые, комбинированные
иорганосольвентные.
Кгруппе кислотных способов из числа применяемых в промышленности относятся сульфитный, бисульфитный и азотнокислый способы, а также ряд исследованных в лабораториях способов.
В сульфитном способе варки в качестве реагента используется так называемая сульфитная варочная кислота, представляющая собой раствор сернистой кислоты, содержащий некоторое количество бисульфита кальция, магния, натрия или аммония.
Особенность сульфитного способа получения целлюлозы: для варки используются только малосмолистые хвойные породы древесины (ель и пихта). Достоинством сульфитного способа является высокий выход (по сравнению с сульфатным) и более легкая отбеливаемость целлюлозы.
Для бисульфитного способа варки реагентом служит водный раствор бисульфита натрия или магния (в последнее время также
аммония). По свойствам бисульфитная целлюлоза очень близка к сульфитной, но отличается от нее более высокой механической прочностью (по механическим показателям приближается к сульфатной целлюлозе). Важное достоинство способа – можно варить любые породы древесины.
27
Азотнокислый способ производства целлюлозы не нашел широкого распространения главным образом по экономическим причинам (нет регенерации химикатов). Способ по существу комбинированный: 1-я ступень – варка с азотной кислотой; 2-я ступень – щелочная обработка.
К щелочным способам относятся натронный и сульфатный, а также их модификации, включая варки в присутствии антрахинона. Натронный используется редко и главным образом для варки лиственных пород древесины. При сульфатной варке реагентом является смесь едкого натра и сульфида натрия (NaOH + Na2S). Антрахинон наиболее эффективно действует при натронной варке. При сульфатной варке применение антрахинона позволяет уменьшить сульфидность щелока и тем самым сократить вредные серосодержащие выбросы при варке, снизить расход активной щелочи на варку, повысить выход целлюлозы, уменьшить температуру и сократить время варки.
Одной из модификаций сульфатного способа является полисульфидный процесс. При полисульфидной варке за счет большого сохранения углеводов древесины по сравнению с сульфатной варкой выход технической целлюлозы при одинаковой степени провара может быть увеличен на 2…6 % от массы древесины.
В основе окислительных способов лежит разрушение лигнина древесины разнообразными окислителями, такими как кислород, пероксид водорода, надкислоты и др.
К ступенчатым способам относят двухступенчатые варки (би- сульфитно-сульфитная, моносульфитно-сульфитная, моносульфит- но-бисульфитная и бисульфитно-моносульфитная), в которых на разных ступенях процесса используются сульфитные варочные растворы с различным значением рН. В эту же группу входит двухступенчатый сульфитно-сульфитный способ, в котором на обеих ступенях процесса применяется сульфитная варочная кислота, но с различным содержанием основания. Существуют также варианты трехступенчатых варок с применением сульфитных варочных реагентов.
28
В число комбинированных сульфитных способов входят суль- фитно-щелочные процессы, в которых сульфитный или бисульфитный способ используется лишь в первой или же в двух первых ступенях, а в последней ступени применяется какой-либо щелочной способ делигнификации – сульфатный, натронный, содовый. К комбинированным методам варки относятся двухступенчатые суль- фитно-сульфатный, сульфитно-содовый, бисульфитно-содовый, трехступенчатый бисульфитно-сульфитно-содовый и некоторые другие разновидности. К комбинированным способам также относится двухступенчатый натронно-сульфитный способ, при котором щелочной реагент (NaOH) применяется в первой ступени варки, а сульфитная кислота – во второй.
2.2. Сульфитный способ получения технической целлюлозы
2.2.1. Общая схема производства
Производство сульфитной целлюлозы из древесины состоит из следующих стадий:
–подготовка древесины (операции по выгрузке и хранению древесины, очистке ее от коры, распиловке и измельчению в щепу);
–приготовление варочной кислоты в виде раствора бисульфита
Са, Mg, Na или NH3 с избытком диоксида серы (сюда входят операции по сжиганию серы или колчедана, очистке и охлаждению сернистого газа и поглощению его с образованием кислоты);
–варка щепы с сульфитной кислотой в котлах под давлением 0,5...1,0 МПа (5...10 кгс/см2) при температуре 130...150 °С, включая
операции по регенерации SO2 и промывке сваренной целлюлозной массы;
–очистка целлюлозной массы от непровара, костры и минеральных загрязнений;
–отбелка и облагораживание целлюлозы с целью повышения белизны и улучшения физико-химических свойств;
–обезвоживание и сушка целлюлозы.
На рис. 6 приведена технологическая схема сульфит-цел- люлозного производства.
29
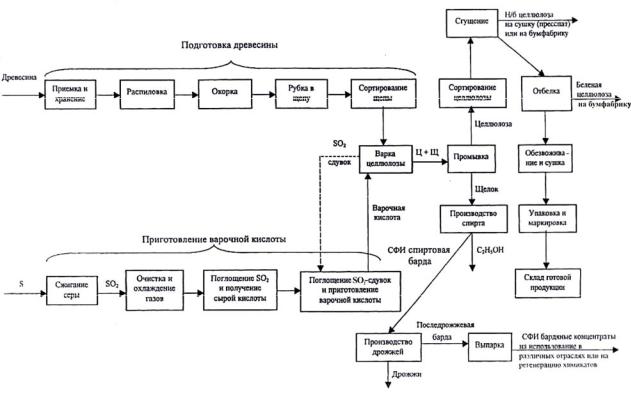
Рис. 6. Технологическая схема сульфит-целлюлозного производства
30