
книги / Технология ковки и объёмной штамповки
..pdf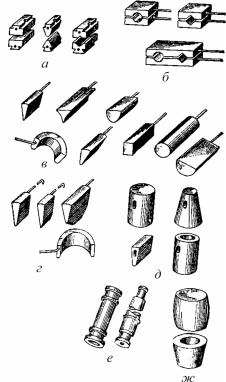
жания и манипулирования поковкой в процессе обработки – это всевозможные патроны, вилки, клещи с различной формой губок.
Рис. 5. Инструмент, применяемый при ковке:
а– бойки; б – обжимки; в – наметки; г – топоры;
д– прошивки; е – оправки; ж – калибры
Рассмотрим основные операции ковки.
Биллетировка слитка представляет собой операцию обжатия ребер заготовки для придания ей формы тела вращения. При этом одновременно со снятием конусности слитка разрушается дендритная структура, происходит заварка пузырей и других дефектов литого металла. Перед процессом биллетировки со стороны прибыльной части обычно производят оттягивание хвостовика, который позволяет удерживать слиток и манипулировать при последующих
11
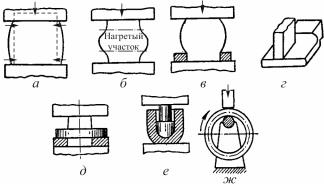
операциях ковки. Биллетировку производят с одного нагрева и заканчивают удалением донной части слитка. Ковку слитка производят в плоских, вырезных и комбинированных бойках (см. рис. 5, а).
Осадка – процесс уменьшения высоты заготовки с одновременным увеличением площади поперечного сечения (рис. 6, а). Осадку производят для устранения литой структуры, повышения степени уковки, получения поковок с относительно малой высотой (для производства зубчатых колес, дисков и пр.) и как предварительную операцию перед прошивкой. Для предотвращения продольного изгиба высоту заготовки при осадке принимают не более 2,5 ее диаметра, при этом процесс выполняют между плоскими и вогнутыми (вырезными) бойками.
Рис. 6. Некоторые операции ковки
Высадка – это осадка части заготовки. При этом происходит увеличение площади поперечного сечения части заготовки. Эта операция может производиться различным образом, например, осаживанием заготовки, имеющей местный нагрев (рис. 6, б), или ограничением деформирования на определенном участке заготовки с помощью колец (рис. 6, в).
Протяжка – это удлинение заготовки или ее части за счет уменьшения площади поперечного сечения (см. рис. 3). Протяжку и ее разнообразные варианты используют при производстве гладких, ступенчатых, коленчатых валов и других изделий;
12
она занимает до 70 % всего времени обработки. При этом применяют бойки различной формы – плоские и вырезные (см. рис. 5, а), обжимки (см. рис. 5, б). Протяжку выполняют последовательной подачей и обжатием заготовки при ее повороте вокруг оси на определенном этапе обработки. Одновременно с протяжкой в качестве подготовительной операции может применяться операция пережима – раздвигания близлежащих слоев с помощью пережимок.
Разгонка используется для увеличения ширины части заготовки за счет уменьшения ее толщины (рис. 6, г). Разгонку чаще выполняют подкладным инструментом (круглым, овальным, плоским). Чтобы иметь при разгонке направление течения металла, перпендикулярное длине инструмента, соотношение между длиной и шириной заготовки принимают в пределах 5…10.
Прошивка представляет собой операцию получения полостей в заготовке за счет вытеснения металла (рис. 6, д, е). Она может выполняться сплошным прошивнем на молотах или прессах, при этом прошиваемая поковка поворачивается на 180°. При сравнительно низких заготовках прошивку выполняют на подкладных кольцах. При получении отверстий значительного диаметра (более 400 мм) прошивни делают полыми для уменьшения усилия прошивки. Придание точных размеров отверстию по диаметру производят продавливанием калибра.
Раскатка – операция, заключающаяся в увеличении диаметра кольцевой заготовки при вращении за счет уменьшения ее толщины с помощью бойка, оправки или роликов (рис. 6, ж). Раскатка используется при изготовлении поковок, имеющих незначительную толщину стенки по сравнению с диаметром отверстия (кольца, бандажи, различные обечайки).
Гибка – образование или изменение углов между частями заготовки или придание ей криволинейной формы. Гибку чаще выполняют между подкладными опорами. При операции гибки возможно образование складки по внутреннему контуру заготовки или образование трещины – по наружному. Чтобы избежать появления данных дефектов, радиус гибки должен быть больше 0,5 Н.
13
Закручивание – поворот части заготовки вокруг продольной оси. Эту операцию применяют при производстве поковок коленчатых валов, крупных спиральных сверл и др. Закручивание выполняют или вручную, или с помощью специального инструмента.
Отрубка – полное отделение части заготовки по незамкнутому контуру путем внедрения в заготовку деформирующего инструмента. Если от заготовки отделяют часть заготовки по незамкнутому контуру, то такую операцию называют разрубкой, а по замкнутому (внутреннему) контуру – вырубкой. При отрубке используют топоры различной формы.
Передача металла – смещение одной части заготовки относительно другой при сохранении параллельности осей или плоскостей заготовки. Подобные операции выполняют при ковке коленчатых валов. Заготовка деформируется на ограниченном участке, когда возникаетнеобходимостьвыполнитьось заготовки ступенчатой.
Кроме рассмотренных существуют и другие операции: кузнечная сварка, растяжка (местное уменьшение поперечного сечения заготовки путем растяжения), прожимка (местное уменьшение поперечного сечения заготовки), обкатка (придание заготовке формы тела вращения путем повторных ударов или обжатий), подкатка (обкатка части заготовки), засечка (выделение части объема заготовки путем нанесения углублений по ее границам), проглаживание (устранение неровностей поверхности заготовки).
В производственных условиях рассмотренные операции в зависимости от вида и размеров поковки могут применяться в различных сочетаниях. Однако при выборе технологического процесса ковки общим является учет необходимого размера укова, значений и последовательности подач, кантовок, формы бойков, температурного режима и количества выносов.
При разработке технологических операций ковки составляют чертеж поковки с припусками на обработку резанием, напусками (некоторым добавлением объема металла в поковке для упрощения её изготовления, например, изготовление поковок без отверстий, имеющихся в готовой детали) и допусками, т.е. значением узаконенных отклонений размеров готовой поковки. Размеры припусков и допусковрегламентируютсясоответствующимиГОСТами.
14
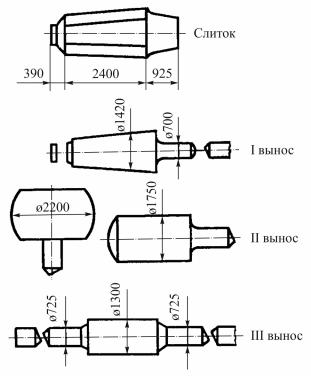
По чертежу поковки определяют ее объем и массу. Учитывая все виды отходов металла в процессе обработки, устанавливают массу исходной заготовки или слитка:
Gис = Gп + Gотх + Gуг + Gобр,
где Gп – масса поковки, кг; Gотх – масса отходов в виде прибыльной и донной частей слитка, кг; Gуг – потери от угара (2…3 % от массы заготовки), кг; Gобр – масса отходов на обрезки (обычно
5…8 %, при сложных поковках 20…30 %), кг.
В качестве примера на рис. 7 показана схема ковки из слитка опорного валка прокатного стана за три выноса.
Рис. 7. Схема ковки опорного валка
15
После первого нагрева производят подкатку прибыльной части слитка под патрон и его биллетировку. Второй нагрев обеспечивает осадку биллетированной заготовки и протяжку осаженного блока. После третьего нагрева обрабатывают боковые поверхности и шейки до требуемых размеров поковки.
3. ОБЪЕМНАЯ ШТАМПОВКА
Штамповку выполняют с использованием специального инструмента – штампа, который состоит из двух частей и более. Полости штампа называются ручьями. Заготовка, деформируясь в ручьях, заполняет полости и принимает форму поковки. Течение метала при штамповке принудительно ограничено поверхностями инструмента, что вызывает перераспределениеобъема металла заготовки.
Распространение штамповки связано с развитием машиностроения, особенно автомобильной промышленности, когда возникла необходимость организации массового производства однотипных поковок. Помимо высокой производительности штамповка обеспечивает получение поковок с высокой точностью размеров, что уменьшает расход металла на изготовление детали и снижает трудоемкость при последующей обработке резанием. Кроме того, штамповка обеспечивает получение высокого качества поверхности поковок, при этом исключается необходимость последующей обработки резанием всей поковки – обрабатывается лишь та ее часть, которая будет соприкасаться с другими деталями. Последующие за штамповкой отделочные операции, например, калибровка в холодном состоянии, повышают качество поверхности поковок, а допуски размеров при этом снижаются до ±0,05 мм. Штамповка обеспечивает получение изделий весьма сложной формы, во многих случаях невыполнимое ковкой без напусков.
Штамповкой изготовляют поковки преимущественно массой до 100 кг, однако производят поковки массой до 400…500 кг, в отдельных случаях до 2 т.
Исходным материалом для горячей штамповки являются сортовой прокат, прессованные прутки, калиброванный металл, литая заготовка и жидкий металл. В крупносерийном производстве дета-
16
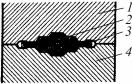
PNRPU
лей находят большое применение заготовки из проката периодического профиля, что обеспечивает в процессе штамповки сокращение подготовительных операций. Исходный материал в заготовительном отделении разрезают на мерные длины. Эту операцию выполняют на хладноломах, кривошипных прессах, механических пилах или производят газовой и электрической резкой. Перед горячей штамповкой заготовки нагревают до температур, определяемых условиями деформирования.
Технологический процесс штамповки отличается значительным разнообразием и определяется видом изделия и применяемым оборудованием. Штамповку производят на молотах, прессах, гори- зонтально-ковочных машинах, вальцовкой, раскаткой, ротационной ковкой и пр.
Горячую штамповку выполняют двумя методами: облойным (с заусенцем) в открытых штампах и безоблойным (при отсутствии заусенца) в закрытых штампах.
Сущность облойного метода заключается в том, что поковка по месту разъема штампа вследствие избытка металла получается с заусенцем (облоем). Наличие облоя (рис. 8) способствует хорошему заполнению полостей штампа, ибо сам заусенец начинает образовываться раньше заполнения ручьев.
При последующей штамповке заусенец создает подпор, т.е. заусенец выполняет определенную технологическую функцию. Поэтому заусенцу придают целесообразную форму – заусеничную щель между частями штампа выполняют в виде специальной канавки по периметру поковки. По окончании пластической обработки облой удаляют на обрезных штампах. Этот способ, несмотря на потери металла в виде заусенца, получил значительное распространение, так как надежно обеспечивает заполнение полостей штампа. Объем заготовки при этом может быть лишь приблизительно равен необходимому.
17
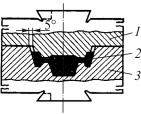
При безоблойной штамповке заготовку помещают в полости одной части штампа (в матрице) и процесс деформирования выполняют другой частью (пуансоном) (рис. 9). При этом облой в изделии не предусматривается. Незначительный заусенец, который может иметь место по плоскости разъема, не оказывает влияния на процесс штамповки и является результатом неточности размеров заготовки.
Для облегчения свободного удаления поковки из штампа его стенки изготовляют с уклоном или применяют выталкиватели. Пониженный расход металла при штамповке данным способом является преимуществом, однако формы поковок при этом менее разнообразны, чем при изготовлении в открытых штампах с облоем.
Как при открытой, так и при закрытой штамповке обработка заготовок может выполняться в одном или нескольких ручьях. В условиях многоручьевой штамповки заготовка изменяется при переходе от одного ручья к другому, в чистовом ручье ей придаются окончательная форма и размеры. В зависимости от условий производства ручьи при многоручьевой штамповке могут размещаться в одном общем или нескольких штампах ковочных машин.
Процесс штамповки выполняют на различных установках. Однако наибольшее распространение получила штамповка на молотах (паровоздушных, фрикционных, бесшаботных), прессах (кривошипных, винтовых, гидравлических) и горизонтальноковочных машинах. Каждый из этих видов штамповки обладает специфическими особенностями.
Штамповка на молотах. Широкое применение молотов при штамповке определяется рядом достоинств этого вида оборудования и методов обработки. При штамповке на молотах можно бы-
18
стро и многократно деформировать заготовку в каждом ручье, осуществлять чрезвычайные энергоемкие операции и большие суммарные деформации.
При штамповке используются паровоздушные молоты с массой падающих частей от 630 кг до 25 т. Используются также фрикционные молоты с доской с массой падающих частей от 500 до 1500 кг. Помимо того применяются бесшаботные молоты, деформирование металла в которых производится путем встречного движения верхнего и нижнего штампов.
При штамповке на молотах используют открытые штампы. В зависимости от сложности получаемого изделия штамповка может быть одноручьевой и многоручьевой. В последнем случае каждый ручей имеет определенное назначение, поэтому их подразделяют на штамповочные и заготовительные.
Штамповочные ручьи – черновой (предварительный) и чис-
товой (окончательный) – обеспечивают получение необходимой формы и размеров изделия. В плоскости разъема чистового ручья штампа по его периметру выполняют канавку для облоя. Обработку в чистовом ручье выполняют обычно за 2–3 удара молота.
Обработка в черновом ручье способствует увеличению стойкости чистового ручья. Обработкой в черновом ручье выполняется значительное формоизменение заготовки, поэтому на него приходится в 1,5…2 раза больше ударов молота по сравнению с обработкой в чистовом ручье.
К другой группе ручьев относятся заготовительные (протяжной, пережимной, формовочный и гибочный, площадка для осадки), используемые для первоначальной обработки при переходе от простейшей формы заготовки к более сложной с постепенным приближением к окончательной форме изделия.
Протяжной ручей используют для удлинения отдельных участков заготовки за счет изменения площади ее поперечного сечения.
Подкатной ручей используют для увеличения поперечного сечения одних участков заготовки за счет уменьшения других при необходимости распределения объема металла в изделии по длине.
19
Пережимной ручей используется в тех случаях, когда необходимо получить местное уширение заготовки без перераспределения металла вдоль оси.
Формовочный ручей применяют для придания поковке необходимой формы в плоскости, параллельной действующей силе, а также для некоторого набора металла.
Гибочный ручей необходим при штамповке изделий, имеющих изогнутую ось в плоскости разъема.
К третьей группе ручьев относятся отрубные – передний и задний ножи. Отрубной нож применяют при отделении поковки от прутка, удалении клещевины, т.е. участка, за который удерживается поковка при штамповке, а также при разрубке поковок на две или более части, если из одной заготовки одновременно штампуют несколько изделий.
В зависимости от конфигурации изделий, размеров и требований в отношении направления волокна в поковке используют те или иные виды ручьев. На рис. 10 показаны расположение ручьев в многоручьевом штампе и последовательность изменения заготовки в готовую поковку шатуна.
При штамповке на молотах применяют не только открытые, но и закрытые штампы. При этом заготовительные ручьи не имеют отличий. Различие наблюдается лишь в штамповочных (чистовых) ручьях и в объеме применяемой заготовки. При обработке в открытом штампе масса облоя составляет обычно 15…20 % от массы поковки, при производстве мелких и сложных изделий масса облоя иногда равна массе самого изделия. Все это указывает на определенную выгодность применения закрытых штампов, когда в заусенец, который получается вследствие незначительного затекания металла в зазоры между частями штампа, попадает всего лишь 1…2 % металла от массы поковок.
При безоблойной штамповке требуемая мощность кузнечных машин может быть на 40 % меньше, чем при облойной штамповке, однако стойкость штампов часто оказывается более низкой.
Штамповка на прессах. Помимо молотов для горячей штамповки широко применяются кривошипные и гидравлические прессы. Штамповка на кривошипных прессах получила значительное распро-
20