
книги / Технология ковки и объёмной штамповки
..pdf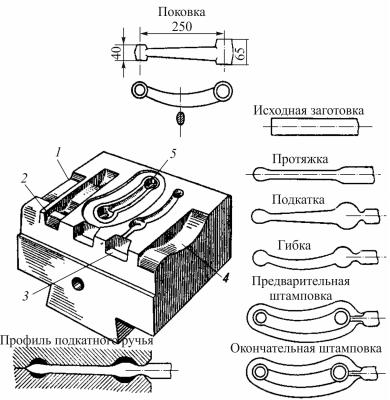
странение лишь к середине XX века и в результате заметного экономического эффекта во многих случаях вытесняет штамповку на молотах. Кривошипные прессы изготовляют усилием от 630 до 80 000 кН и более. Соответствие мощности молотов и кривошипных прессов10 000 кНсоответствует1 т весападающихчастеймолота.
Рис. 10. Молотовой штамп и схема изменения заготовки в поковку шатуна: 1 – протяжной ручей; 2 – подкатной ручей;
3 – предварительный ручей; 4 – гибочный ручей; 5 – окончательный ручей
Ползун кривошипного пресса совершает возвратнопоступательное движение под действием кривошипно-шатунного механизма и имеет постоянное значение хода и определенные
21
нижнее и верхнее положения. Поэтому штамповку в каждом ручье обычно производят за один ход ползуна, а размеры изделия по высоте получаются более точными, чем при штамповке на молотах.
Наличие у кривошипных прессов выталкивателей позволяет в 2…3 раза уменьшить штамповочные уклоны по сравнению с уклонами молотовых штампов, что снижает припуски на механическую обработку. Следует также отметить отсутствие потерь металла на клещевину, которая необходима во многих случаях при ковке в молотовых штампах.
Кроме того, на кривошипных прессах широко используют менее дорогостоящие составные штампы. Производительность механических прессов на 30…50 % выше производительности молотов, так как изделие выполняется за один ход ползуна, при этом упрощается возможность применения автоматизации, улучшаются условия труда рабочих. Штамповка на кривошипных прессах имеет также то преимущество, что скорость движения ползуна к моменту соприкосновения с заготовкой составляет всего лишь 0,3…0,8 м/с, т.е. по крайней мере в 25 раз меньше скорости инструмента в момент удара на молотах, что свидетельствует о неударном характере пресса. Это позволяет устанавливать оборудование в зданиях облегченного типа.
К недостаткам штамповки на кривошипных прессах следует отнести их меньшую универсальность по сравнению с молотами, высокую стоимость самих прессов (в 3…4 раза выше стоимости такого же по мощности молота), худшее заполнение полостей штампа ввиду меньших скоростей деформации на прессах, что требует большего количества ручьев по сравнению с молотовыми штампами.
Горячую штамповку на кривошипных прессах выполняют в открытых (с образованием облоя в плоскости разъема) и закрытых штампах. Вместе с этим на механических прессах выполняют штамповку выдавливанием, штамповку прошивкой и различные комбинированные операции. Процесс выдавливания применяют в тех случаях, когда необходимо получить поковки, имеющие длинные отростки и, следовательно, значительную разницу поперечных сечений. Этот процесс аналогичен прессованию металла.
22
Штамповка прошивкой представляет собой процесс вдавливания пуансона в заготовку круглого, квадратного или другого сечения. В результате этой операции получаются поковки с полостью. При закрытой (глухой) прошивке в процессе штамповки часть металла заготовки может выдавливаться против хода пуансона в зазор между пуансоном и матрицей.
Штамповка на гидравлических прессах получила распространение при производстве различных рычагов, зубчатых колес, полых корпусов, коленчатых валов, сферических днищ сосудов, лопастей авиационной техники и других изделий из прокатной и листовой заготовки и из кованых заготовок с массой в несколько сотен килограммов и более (до 5 т). Штамповку на гидравлических прессах выполняют в открытых и закрытых штампах.
Усилие обработки гидравлических прессов для штамповочных работ составляет до 750 МН. В сравнении со штамповочными молотами, имеющими соответствующую массу падающих частей, гидравлические прессы более дорогостоящие, более тихоходные и обеспечивают меньшую производительность. Поэтому их применяют при штамповке крупных поковок, при штамповке труднообрабатываемых сплавов с низкими скоростями деформирования, при штамповке изделий с применением операции выдавливания, прошивки, протяжки и других, требующих значительного хода инструмента.
Поскольку обработка на кривошипных и гидравлических прессах выполняется за один ход ползуна, вся окалина может вдавиться в поверхность поковки. Чтобы избежать ухудшения качества поверхности изделий, применяют различные способы очистки заготовки от окалины (например, гидравлическая очистка), а при производстве мелких и средних по размеру изделий стремятся вести безокислительный нагрев заготовок (чаще всего в индукционных печах).
По окончании горячей штамповки возникает необходимость в ряде отделочных операций. К ним в первую очередь относят удаление облоя и заусенца, что выполняют в обрезных штампах, обычно устанавливаемых на кривошипных прессах, в холодном
23
состоянии. Облой поковок, получаемых на молотах с массой падающих частей выше 1…1,5 т, удаляют в горячем состоянии. После удаления облоя в некоторых случаях требуется правка поковок, которая может быть выполнена в специальном правочном или чистовом ручье. Правку мелких изделий производят в холодном состоянии, крупных – в горячем.
К отделочным операциям относят также и калибровку, которая придает поковке точные размеры и форму и повышает качество поверхности. Калибровку выполняют как в горячем, так и в холодном состоянии. Кроме того, для улучшения качества поверхности изделий и удаления окалины применяют дополнительную обработку: травление, пескоструйную и дробеструйную очистку и обработку в галтовочных (вращающихся) барабанах. Большое внимание уделяется термической обработке поковок (замедленное охлаждение, нормализация, отжиг и др.).
Штамповка на горизонтально-ковочных машинах. Горизон-
тально-ковочные машины (ГКМ) представляют собой кривошипные прессы с перемещением главного и зажимного ползунов в горизонтальной плоскости.
На ГКМ штампуют поковки болтов, гаек, колец, втулок, клапанов, шестерен и др. При этом штамповка может выполняться как за один ход пуансона, так и за несколько переходов. При многоручьевой штамповке переходы имеют существенное отличие от применяемых на молотах и прессах. На ГКМ производят такие операции, как набор, т.е. получение высадкой некоторого утолщения на исходной заготовке, которую выполняют в зависимости от объема высаживаемой части и диаметра заготовки непосредственно из заготовки или после осуществления наборных переходов; прошивку, т.е. получение сквозных или несквозных отверстий, удаление заусенца; отрезку конца прутка.
В качестве исходного материала обычно применяют прокатанную заготовку повышенной точности и калиброванный металл, чаще круглого и реже квадратного сечения. Штамповку от прутка без предварительной его разделки следует считать наиболее целесообразным процессом.
24
ГКМ имеют высокую производительность (до 400…900 изделий в час). Работа на них безударна, удобна и менее опасна, при этом имеется возможность полной автоматизации процесса штамповки. Существуют полностью автоматические ГКМ с горизонтальным разъемом матриц.
К недостаткам ГКМ следует отнести меньшую универсальность, поэтому номенклатура штампуемых на них изделий заметно ограничена; пониженную стойкость штампов, так как в закрытых штампах ГКМ в полости ручьев возникают перегрузки; сравнительно высокую стоимость (в 1,5 раза выше стоимости кривошипных прессов той же мощности).
Помимо рассмотренных способов штамповки на молотах, прессах и ГКМ в штамповочном производстве встречается обработка металла на машинах специализированного назначения, например, гибка в горячем или холодном состоянии, выполняемая на кривошипных машинах с горизонтальным перемещением ползуна в одноручьевых и многоручьевых штампах.
Для производства фасонных заготовок в ковочно-штампо- вочных цехах широко используют ковочные вальцы, обработка в которых представляет собой обычную прокатку периодического профиля. Для получения поковок кольцевой формы применяют процесс раскатки. Деформирование металла в данном случае выполняется между вращающимися валками-роликами при непрерывном вращательном движении кольцевой заготовки в той же плоскости, что и ролики. Некоторые виды поковок (ступенчатые и конические валики, трубы с оттянутыми на конус концами и др.) производят на ротационно-ковочных машинах (процесс редуцирования) в холодном и горячем состояниях. В данном случае получают изделия высокой точности, а ротационно-ковочные агрегаты отличаются высокой производительностью.
Разнообразные сравнительно мелкие изделия сложной формы из стали и цветных металлов и их сплавов изготовляют объемной штамповкой в холодном состоянии. В зависимости от сложности формы изделия процесс штамповки может выполняться за одну или несколько операций. Холодная объемная
25
штамповка обеспечивает получение изделий высокой точности (в пределах ±0,02…0,05 мм) с качественной поверхностью (шероховатость Ra = 0,32…2,6 мкм).
4. ХОЛОДНАЯ ОБЪЕМНАЯ ШТАМПОВКА
Важным преимуществом холодной объемной штамповки является возможность исключения нагрева металла из технологического процесса, а следовательно, исключение окалинообразования, что позволяет обеспечить высокое качество поверхности и точность размеров. При этом условии трудоемкость последующих операций механической обработки существенно сокращается, уменьшаются отходы металла и повышается производительность процесса. Одновременно с этим повышаются прочностные характеристики, что позволяет в ряде случаев низколегированные и среднеуглеродистые стали заменять более дешевыми низкоуглеродистыми.
До недавнего времени холодной штамповкой изготавливали детали типа стержней и труб с фланцами и стаканов из низкоуглеродистых сталей, известных металлов и сплавов в массовом и крупносерийном производстве. Накопленный к настоящему времени опыт позволяет расширить область применения до изготовления деталей типа тройников, крестовин, шестерен и прочего из компактных пористых и порошковых материалов. Наибольшие размеры деталей, изготовляемых холодной объемной штамповкой,
впоперечном сечении на более 75–100 мм.
Взависимости от характера течения металла технологические операции холодной объемной штамповки можно представить в виде основных операций (рис. 11).
Отрезку заготовки от сортового, трубного и листового проката осуществляют на металлорежущих станках, пилах, лазерами, в штампах и др.
Для холодной объемной штамповки наиболее приемлемой является отрезка в штампах как наиболее дешевая, производительная и металлосберегающая (рис. 12).
26
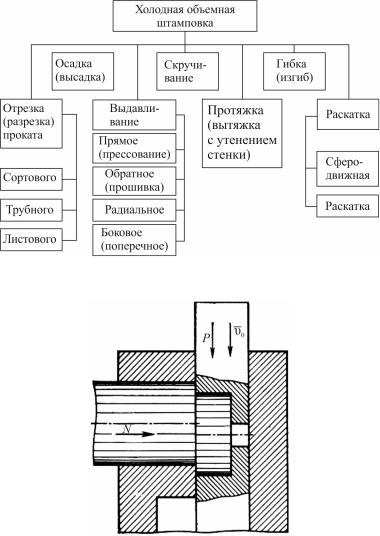
Рис. 11. Классификация операций холодной объемной штамповки
Рис. 12. Отрезка сортового проката на заготовки в закрытом штампе
Отрезка в штампах представляет собой совокупность формоизменяющего и разделяющего процесса. Холодной отрезкой в штампах из сортового проката изготавливают заготовки диамет-
27
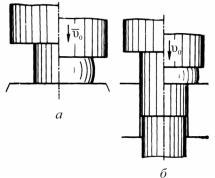
ром (сторона квадрата) до 70 мм и высотой (толщиной) свыше 0,5 диаметра (сторона квадрата); из трубного проката – с относительной толщиной стенки свыше 0,05.
Осадка (высадка) – технологическая операция, в процессе которой происходит уменьшение высоты всей (части) заготовки
(рис. 13).
Рис. 13. Осадка (а) и высадка (б)
В холодной объемной штамповке осадку применяют, если диаметр отрезанной заготовки меньше диаметра контейнера (матрицы); высадку – для образования буртов или утолщений концевых частей стрежневых заготовок.
Прямое выдавливание + (прессование) – технологическая опе-
рация штамповки, в процессе которой происходит истечение металла, заключенного в замкнутую полость, в направлении движения пуансона через отверстие (окно матрицы), форма которой определяет поперечное сечение выдавливаемой части деформируемой заготовки (рис. 14)
Прямое выдавливание применяют для изготовления изделий из сортового и трубного проката.
Обратное выдавливание (прошивка в закрытой матрице) – технологическая операция штамповки, в процессе которой происходит истечение металла из замкнутой полости в направлении, обратном (встречном) движению пуансона (рис. 15).
28
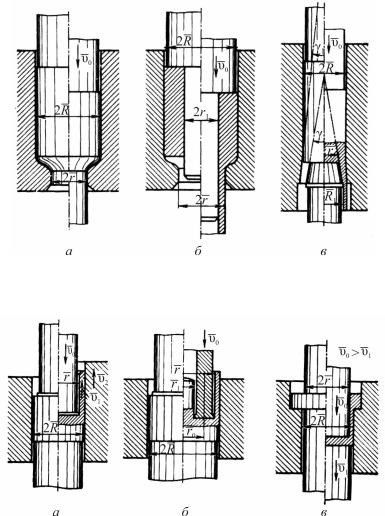
Рис. 14. Прямое выдавливание: а – цилиндрической заготовки; б – трубной; в – прямое выдавливание с раздачей
Рис. 15. Обратное выдавливание стаканов:
а – цилиндрического, б – с отростком, в – с фланцем
Радиальное выдавливание – технологическая операция штамповки, в процессе которой происходит течение металла из замкнутой цилиндрической полости (контейнера) через щель, расположенную по периметру боковой поверхности (рис. 16).
29
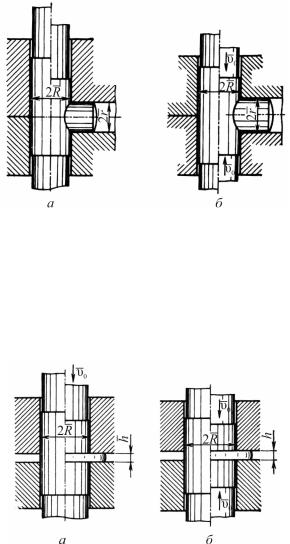
Рис. 16. Радиальное выдавливание: а – одностороннее, б – двустороннее
Радиальное выдавливание применяют при штамповке поковок с фланцами. Боковое выдавливание – технологическая операция штамповки, в процессе которой происходит истечение металла из замкнутой полости (контейнера) через отверстие в боковой поверхности (рис. 17).
Рис. 17. Боковое выдавливание: а – одностороннее, б – двустороннее
Скручивание – технологическая операция, в процессе которой происходит поворот поперечных сечений вокруг продольной оси заготовки (рис. 18). Штамповку скручиванием совмещают с осад-
30