
книги / Основы технологической безопасности производств энергонасыщенных материалов и изделий
..pdfсивности (как при переходе горения в детонацию), а высокие – если инициировать интенсивным импульсом (плотным детонатором). Если в заряде рыхлой структуры второго класса скорость детонации (режим низкой скорости) достигнет значения 3000 м/с, то она скачкообразно возрастет и процесс детонации далее будет идти в режиме высокой скорости, т.е. произойдет смена баллистического механизма детонации на центровой.
Смена механизма детонации происходит, когда давление во фронте детонационной волны рыхлой структуры второго класса достигает 1–4 ГПа (в зависимости от состава пороха). Величина давления рассчитана с использованием зависимости p = ρD2/4, где р – давление детонации; ρ – плотность ЭКМ; D – скорость детонации.
При продвижении порохового полуфабриката по сужающемуся каналу винта шнек-пресса происходит его уплотнение с одновременным деформированием зерен. По достижении плотности 1,2–1,3 г/см3 рыхлая структура первого класса, так же как и второго, может детонировать по центровому механизму. Однако при указанной плотности сжимаемость и пористость структуры снижаются настолько, что по баллистическому механизму детонация распространяться уже не может (при реальных значениях площади поперечного сечения канала винта
имассы стенок). Для дальнейшего прохождения в спрессованный порох детонация должна перейти на другой механизм, что возможно лишь в случае достижения ею на этом участке достаточно высокой скорости, обеспечивающей указанное выше давление во фронте.
Скорость детонации в рыхлом полуфабрикате баллиститного пороха зависит от его состава, структуры (плотность, степень желатинизации, размер зерна и т.д.), прочности и массы оболочки шнек-пресса, а также диаметра заряда
икрутизны нарастания плотности по длине заряда. При определенном сочетании указанных факторов происходит весьма необычное явление – разрыв детонационной цепи в заряде
121
нарастающей плотности, при возбуждении в нем детонации с низкой скоростью.
Оригинальные исследования по возбуждению детонации в зарядах нарастающей плотности в стальных оболочках экспериментально подтвердили наличие этого явления. Было установлено, что разрыв процесса детонации происходит в заряде из зерен баллиститного пороха (с монотонно возрастающей плотностью) на участке с плотностью 1,2–1,3 г/см3, при крутизне ее нарастания не менее 1,5 г/(см3·м) в зависимости от структуры полуфабриката, состава пороха, диаметра заряда, а также прочности и массы оболочки. Разрыв процесса детонации происходит в случае, если давление во фронте ударной волны не успеет достигнуть критического значения, необходимого для возбуждения детонации по центровому механизму в последующих, более плотных слоях заряда. Определяющее значение в явлении разрыва детонационной цепи в заряде нарастающей плотности имеет крутизна нарастания плотности (или обратная величина – длина рабочего участка изменения плотностей).
Увеличение скорости и соответственно давления во фронте детонационной волны при детонации заряда нарастающей плотности происходит с отставанием от значений, соответствующих текущим значениям плотности. Это отставание тем больше, чем крупнее и плотнее зерна полуфабриката и чем круче нарастает плотность заряда.
Факторы, влияющие на возможность разрыва детонационной цепи в зарядах нарастающей плотности, учитываются при конструировании шнек-прессов, используемых для формования зарядов из БП. В реальных условиях для каждого состава пороха и конструкции шнек-пресса подбирается (путем испытаний в специальных моделях) пороховой полуфабрикат с такими параметрами (плотность и размер зерен), при которых исключалась бы возможность выхода детонации из рыхлого пороха в плотный, т.е. из шнек-пресса в пресс-инструмент и шашку пороха.
122
4.2.2. Взрывозащита шнек-прессов для изготовления зарядов из БП и БТРТ
В пороховом производстве операция прессования на шнек-прессах является одной из самых опасных и ведется
вжелезобетонных кабинах с большой толщиной стенок. Любое загорание вызывало взрыв пресса и значительные разрушения. Особо возросла опасность этой фазы при переходе на высокочувствительные пороха повышенной мощности и изготовлении из них крупногабаритных шашек диаметром до 800 мм с помощью раструбного инструмента, в котором находится до нескольких тонн пороха.
Оригинальная схема и метод взрывозащиты шнек-прессов былипредложеныиреализованыИ.Я. Петровскимссотрудниками.
Полностью избежать возникновения очага загорания и горения пороха в витках шнек-пресса (стадии 1–4 на рис. 4) не представляется возможным. Поэтому был выбран метод борьбы на стадиях 5–7, разрывающий эту цепочку и не дающий возможности горениюперейти в детонацию.
Впрежней конструкции шнек-прессов переходу горения
вдетонацию (ПГД) способствовали большие прочность и масса корпуса шнек-пресса с впрессованной в него бронзовой втулкой. Была предложена принципиально новая конструкция так называемой динамически ослабленной втулки (ДОВ). Особенность ее заключается в том, что вдоль всей длины втулки
вней прорезались много узких пазов, в которых толщина стенки втулки составляла всего 4 мм (рис. 5). При загорании и нарастании давления до сравнительно небольшого значения стенки втулки в пазах срезались и быстро вылетали, открывая выход газообразным продуктам горения пороха. Для обеспечения свободного выхода в самом корпусе шнек-пресса делались окна. Давление резко падало, порох продолжал гореть, но взрыва уже не происходило. На прессе менялась втулка, и он снова включался в работу.
123
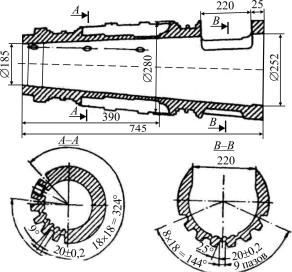
Рис. 5. Конструкция динамически ослабленной втулки к шнек-прессу
В случае, если ПГД все же происходил, срабатывала вторая ступень взрывозащиты – обеспечение разрыва детонационной цепи на участке нарастающей плотности. В результате взрыв, хотя и более сильный, чем взрывное горение без ПГД, охватывал только неуплотненный полуфабрикат, находящийся в бункере и в начальных, транспортирующих витках шнекпресса. Уплотненный порох в пресс-инструменте и готовой шашке не детонировал.
Для обеспечения разрыва детонационной цепи при переработке порохов повышенной мощности и чувствительности применяют ДОВ из легкого сплава, проводят дополнительные операции по укрупнению и уплотнению зерен полуфабриката, используют винт с уменьшенным сечением канала (многозаходный). Эти меры способствуют также и предотвращению ПГД. Также специально для обеспечения разрыва детонационной цепи применяют винт с укороченной зоной уплотнения полуфаб-
124
риката, чем достигается высокая крутизна нарастания плотности (до 3 г/(см3·м) и более).
При выборе материала для изготовления ДОВ необходимо учитывать, кроме статической прочности вышибных элементов, работающих на срез, их поверхностную плотность (массу материала на единицу поверхности), которая при переработке современных БП не должна превышать 2–3 г/см2. Для увеличения массы вышибного элемента автоматически требуется снижение допустимой срезающей статической нагрузки.
Конструктивно ДОВ выполняется в виде ребристой трубы (см. рис. 5) из бронзы, анодированного дюралюминия или других легких и износостойких материалов. Ребра втулки упираются в ограничительные стальные кольца корпуса шнек-пресса, обеспечивающие прочность и жесткость конструкции и не мешающие вылету вышибных элементов.
4.3.ПРОИЗВОДСТВО СМЕСЕВЫХ ТРТ
4.3.1.Особенности детонации в смесевых ТРТ
Смесевые ТРТ являются смесями горючего и окислителя, поэтому по механизму реакции в детонационной волне они сравнимы со смесевыми ВВ (аммониты и динамоны). Детонационная УВ вначале возбуждает химическую реакцию на поверхности раздела окислителя и горючего. Последующими стадиями являются газификация окислителя и горючего, смешение и взаимодействие образующихся при этом продуктов, т.е. детонационная реакция происходит по смесевому механизму.
Большая часть энергии выделяется именно при взаимодействии продуктов газификации исходных компонентов.
Скорость процесса газификации зависит:
♦от свойств вещества;
♦линейных размеров частиц окислителя и толщины слоя связующего;
125
♦интенсивности подвода тепла из зон взаимодействия продуктов газификации;
♦давления газообразных продуктов.
Критический диаметр детонации сухого ПХА (влажность 0,05 %) с размером частиц менее 50 мкм при плотности 1,1 г/см3 равен 32 мм. Увеличение размера частиц приводит к увеличению критическогодиаметрадетонации, причемэтазависимостьлинейная.
Добавление в ПХА даже небольшого количества горючих добавок в порошкообразном виде резко уменьшает время детонационной реакции и, следовательно, критический диаметр детонации. При добавлении в окислитель горючих веществ более некоторого предела (для ПХА – 0,2 %) повышается также и температура в зоне реакции. Следовательно, детонационная реакция в СТРТ представляет собой сложный процесс, отдельные стадии которого взаимосвязаны.
В настоящее время нет единой теории механизма протекания детонационной реакции в смесевых ЭКМ и, в частности, в СТРТ.
Установлена зависимость критического диаметра детонации от линейного размера частиц компонентов, а также установлено повышение детонационной способности при замене в СТРТ обычного (инертного) горючего вещества активным (содержащим окислитель в молекуле).
Влияние соотношения размеров элементарных областей (занятых только окислителем или только горючим) на продолжительность детонационных реакций является сложным вопросом, который нужно рассматривать отдельно для каждой конкретной системы.
Простейшей такой системой является смесь из порошкообразных окислителя и горючего. Количество частиц окислителя и горючего в 1 г смеси равно соответственно:
n1 |
= ω1 |
/ ( |
π |
d12 |
ρ1 ) , |
n2 |
= ω2 |
/ ( |
π |
d22 |
ρ2 ) , |
(7) |
|
6 |
6 |
||||||||||||
|
|
|
|
|
|
|
|
|
|
|
126

где ω1 и ω2 – массовая доля окислителя и горючего соответственно; d1 и d2 – средний размер частиц окислителя и горючего соответственно; ρ1 и ρ2 – плотность частиц окислителя и горючего соответственно.
Из условия равенства п1 = п2 (чтобы элементарная область соответствовала одной частице) после преобразований получим
d1 |
= |
ω2ρ1 |
, |
(8) |
|
|
|||
d2 |
|
ω1ρ2 |
|
т.е. соотношение размеров частиц зависит от соотношения массовых долей компонентов. Если горючего в смеси содержится меньше, чем окислителя, то и размер его частиц для выполнения условия п1 = п2 (при равенстве плотностей) должен быть меньше. Измельчение окислителя при наличии крупных частиц горючего не повысит детонационную способность.
Особенность же смесей с жидким горючим такова, что повышение степени измельчения окислителя будет всегда увеличивать их детонационную способность. Не меньшее влияние на детонационную способность подобных смесей будет оказывать соотношение компонентов. При малом содержании жидкого горючего в смеси детонационная способность системы будет больше, чем при стехиометрии.
Введение в состав топлив активных компонентов (в частности, кристаллических ВВ) увеличивает их восприимчивость к детонации. В связи с этим возникает вопрос о допустимом уровне содержания таких компонентов в составе топлива. Основными факторами, влияющими на протекание детонационной реакции, являются:
1)содержание кристаллического ВВ в составе топлива;
2)гранулометрический состав ВВ;
3)качество кристаллов ВВ.
Известно, что кристаллические ВВ, разбавленные кристаллическими инертными материалами, например поваренной солью, сохраняют способность детонировать при содержании всего
127
5 % ВВ в смеси. В вязком же связующем, характерном для СТРТ, кристаллические ВВ полностью флегматизированы при содержании их до 15–25 %. Таким образом, наличие и количество кристаллического ВВ влияют на протекание детонационной реакции. При введении в состав СТРТ кристаллических ВВ типа гексогена восприимчивость топлива к детонации резко возрастает.
Если введение кристаллических ВВ в баллиститные композиции приводит только к количественному изменению восприимчивости к детонации, то введение кристаллических ВВ в состав смесевых композиций приводит и к качественному изменению. При введении кристаллических ВВ в СТРТ последние приобретают способность детонировать в диаметрах реально используемых зарядов.
Начиная с некоторого предельного значения массовой доли ВВ (30–35 %) изменяется механизм реакции, и детонация происходит по механизму, характерному для флегматизированного, индивидуального ВВ. При этом наблюдается большое различие в значениях критических диаметров детонации для топливных композиций на активном и пассивном связующих. Скорость процесса взрывчатого разложения ВВ типа гексогена в несколько раз превышает скорость газификации и последующего взаимодействия продуктов газификации остальных компонентов СТРТ. Следовательно, когда реакция в гексогене успевает уже завершиться, остальные компоненты топлива разбрасываются волной разрежения в окружающую среду, не успевая прореагировать. При изменении удельной поверхности кристаллов изменяется скорость детонационной реакции и критический диаметр.
4.3.2. Взрывозащита аппаратов типа смеситель непрерывного действия
Аппарат типа смеситель непрерывного действия (СНД) служит для смешивания всех компонентов СТРТ и заполнения готовым топливом изложниц или корпусов ракетных двигателей. Он является наиболее взрыво- и пожароопасным аппаратом
128
в производстве СТРТ. Аппарат состоит из двух смесителей лопастного типа, размещенных друг под другом, у каждого из которых имеется в нижней части шнек для выгрузки смеси. В верхний смеситель, который работает под атмосферным давлением, поступают через дозаторы окислитель, связующее и добавки, а образующаяся смесь через вакуумную камеру непрерывно поступает в нижний (вакуумный) смеситель, где она домешивается и далее с помощью шнека нагнетается в изложницу или корпус РДТТ.
К этому аппарату была разработана специальная комплексная система взрыво- и пожарозащиты.
Учитывая, что СНД является звеном непрерывного поточного процесса, система предназначена обеспечивать локализацию горения в аппарате и предотвращать распространение пламени по смесепроводу в пресс-форму и линию подачи порошкообразных компонентов.
Система взрывопожарозащиты использует принцип сброса давления и подачи воды в пожароопасные зоны. Система состоит из следующих устройств: обнаружения загорания; противовзрывной и противопожарной защиты; пламеотсечения и водопитания.
В комплект устройства обнаружения загорания входят:
реле низкого и высокого давления, фотодатчик и электронная контрольно-пусковая установка.
Устройство противовзрывной защиты состоит из управляемых мембран и втулки. Управляемые мембраны приводятся в действие гидроимпульсным усилителем. Устройство противопожарной защиты обеспечивает прекращение горения в раскрытом аппарате, а также защиту примыкающего оборудования.
Пламеотсекающая часть обеспечивает механическое перекрытие транспортных смесепроводов, соединяющих аппарат с пресс-формой и транспортным шнеком. Устройство пламеотсечения состоит из пламеотсекателей, установленных соответ-
129
ственно на смесепроводе и между предварительным смесителем и транспортным шнеком.
Описанная выше система защиты функционирует следующим образам. При загорании в аппарате СНД происходит нарастание давления, что приводит в действие устройства противовзрывной защиты. Если в этот момент или позже пламя обнаруживается фотодатчиком, то происходит срабатывание устройств пожарозащиты и пламеотсечения. Управление устройствами противопожарной, противовзрывной защиты и пламеотсечения, а также контроль за работой устройства обнаружения загорания осуществляется электронной контрольнопусковой установкой.
В случае отказа электроавтоматики системы противовзрывная защита обеспечивается за счет разрушения предохранительных мембран избыточным давлением, возникающим в аппарате при горении. Площадь защитных проемов принимается не менее 0,1 площади горения. В этом случае горение переходит в режим, при котором возможно тушение пламени распыленной водой. Система действует автоматически с временем срабатывания не более 0,1 с. Для обеспечения большей надежности система имеет разрывные мембраны, вскрывающиеся при давлении в аппарате 0,2 МПа. Пуск воды к насадкам-распылителям и пламеотсекателям осуществляется в этом случае с помощью термомеханического привода.
Установка имеет следующие временные параметры: время до раскрытия управляемых мембран 0,03 с; время подачи воды внутрь аппарата 1,1 с; время срабатывания пламеотсекателя 1,2 с.
Значительная сложность эксплуатации этой системы существенно затруднила ее внедрение.
130