
книги / Материаловедение. Технология металлов и сварки
.pdf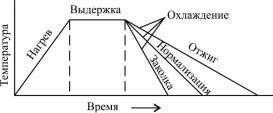
Глава 5 ОСНОВЫ ТЕРМИЧЕСКОЙ И ХИМИКО-ТЕРМИЧЕСКОЙ
ОБРАБОТКИ МЕТАЛЛОВ
5.1. Общие понятия
Термической обработкой называются технологические процессы, состоящие из нагрева и охлаждения металлических изделий с целью изменения их структуры и повышения физико-механичес- ких свойств.
Термическую обработку характеризуют следующие параметры:
нагрев до определенной температуры,
выдержка до этой температуры,
скорость нагрева и охлаждения.
В зависимости от температурных режимов термическая обработка подразделяется на следующие виды: отжиг, нормализация, закалка (рис. 5.1). После закалки, как правило, следует отпуск.
Рис. 5.1. Виды термической обработки
Основой для разработки видов термической обработки стали является: часть диаграммы состояния железо – цементит, соответствующая содержанию углерода 2,14 % или стальной угол, который расположен ниже линии солидус.
Стальной угол характеризуется тремя критическими точками, которые обозначаются буквами А (рис. 5.2).
Нижняя критическая точка А1 соответствует геометрическому месту точек на линии PSK. Точка А3 соответствует геометрическому
31
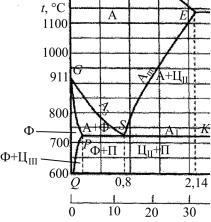
месту точек на линии GS, точка Аm – геометрическому месту точек на линии SE.
Рис. 5.2. Стальной угол и критические точки
Если идет нагревание относительно этих линий, то добавляется латинская буква «c» (Ас1, Ас3, Асm). Если идет охлаждение относительно этих линий, то добавляется латинская буква «r» (Аr1, Ar3, Arm).
5.2. Виды термической обработки
Отжиг заключается в нагреве стали выше линии GSK (точки Ac3, Ac1) на 30–50 °С, выдержке при данной температуре и медленном охлаждении (вместе с нагревательным устройством). Цель отжига – снятие напряжений и уменьшение твердости, устранение химической и структурной неоднородности.
Различают следующие основные виды отжига:
полный отжиг – нагрев стали до температуры на 30–50 °С выше точки Ас3 с последующим медленным охлаждением. После охлаждения в структуре стали образуются феррит и перлит. Отжигают в основном конструкционные стали, для получения однородной структуры;
32
неполный отжиг – нагрев стали на 30–50 °С выше точки Ас1. Отжигают в основном инструментальные стали. В структуре стали наблюдается перлит и цементит;
диффузионный отжиг (гомогенизация) – производится при температурах 1100–1200 °С для устранения структурной неоднородности. Отжиг длится очень долго – в течение 30–50 ч.
Структура стали после охлаждения соответствует диаграмме состояния, т.е. образуются Ф+П или П+Ц.
Нормализация стали. Нагрев стали до температуры выше
линии GSE (точки Ас1, Ас3, Асm) на 30–50 °С, выдержке при этой температуре и последующем охлаждении на воздухе. Цель нормализации – снятие напряжений, исправление структуры стали и сварных швов. При нормализации стали имеют ту же структуру, что и при отжиге, но более дисперсную, т.е. более мелкокристаллическую.
Закалка заключается в нагреве стали выше линии GSK на 30– 50 °С (точки Ac3, Ac1) с последующим быстрым охлаждением, чаще
вводе или масле.
Цель закалки – получение высокой твердости и прочности. Доэвтектоидные стали нагревают выше точки Ac3 (линия GS) –
это полная закалка. Заэвтектоидные стали нагревают выше точки Ac1 (линия PSK) – это неполная закалка.
Свойство стали приобретать высокую твердость при закалке называется закаливаемостью.
Способность стали закаливаться на определенную глубину на-
зывается прокаливаемостью.
С увеличением содержания углерода возрастает способность стали к закалке. При содержании углерода менее 0,3 % сталь не закаливается.
Быстрое охлаждение доэвтектоидных сталей при закалке предотвращает превращение аустенита в перлит, образуется мартенситная структура из мелкоигольчатого мартенсита и остаточного аустенита (1–2 %).
Мартенсит – это пересыщенный твердый раствор внедрения углерода в α-железо. При быстром охлаждении (300–500 °С/с) про-
33
исходит мгновенная перестройка γ-железа в α-железо, при этом весь углерод аустенита переходит в решетку α-железа, искажает ее и преобразует в тетрагональную, т.е. происходит мартенситное превращение.
Мартенситная структура отличается высокой твердостью и малой пластичностью и имеет игольчатое строение.
Заэвтектоидные стали подвергают неполной закалке (нагрев выше точки Ас1 на 30–50 °С). Структура этих сталей состоит из мартенсита и цементита.
Отпуск – нагрев стали до температур ниже точки Ас1 (линия PSK) с выдержкой при данной температуре и последующим охлаждением с заданной скоростью, обычно на воздухе.
Цель отпуска – уменьшение закалочных напряжений, снижение твердости, улучшение физико-механических свойств металлов.
Основное превращение при отпуске – распад мартенсита, т.е. выделение углерода из его пересыщенного раствора в виде мельчайших частичек карбида железа (цементита).
Отпуск всегда проводится после закалки и является окончательной термической операцией.
Различают следующие виды отпуска:
Низкий отпуск. Проводится при температурах 150–250 °С
собразованием структуры отпущенного мартенсита. При этом уменьшаются остаточные напряжения. Твердость меняется мало.
Средний отпуск. Проводится при нагреве стали до температур 350–450 °С с образованием структуры троостита отпуска – мелкодисперсной смеси кристалликов феррита и цементита. При этом значительно снижается твердость, заканчивается образование карбидной фазы железа. Рекомендуется для рессор и пружин.
Высокий отпуск. Проводится при температурах 500–650 °С
собразованием структуры сорбита отпуска – мелкодисперсной смеси кристалликов феррита и цементита. Сталь со структурой сорбита имеет хорошие механические свойства. Применяют в машиностроении для изделий из конструкционной стали для обеспечения высокой механической прочности и плотности. Сочетание закалки
34
с высоким отпуском на сорбит называется улучшением стали. Улучшение проводят для среднеуглеродистых сталей с содержанием углерода 0,35–0,65 %.
5.3. Химико-термическая обработка
Механизм химико-термической обработки (ХТО). Химико-
термическая обработка – процесс насыщения поверхности металлических материалов различными элементами для придания ей соответствующих свойств.
От других видов обработки ХТО отличается тем, что кроме структурных изменений в поверхностном слое происходит изменение его состава и строения за счет диффузии в поверхность элементов в атомарном состоянии из внешней среды при высоких температурах.
Основная цель ХТО – упрочнение поверхности деталей, повышение твердости, износостойкости, а также повышение стойкости против агрессивных сред.
Механизм ХТО характеризуется четырьмя одновременно протекающими процессами:
1. Диссоциация. Заключается в распаде молекул и образовании активных атомов. Степень распада молекул в процентах называется степенью диссоциации. Например:
2СО t, C C CO2, 2NH3 t, C 2N 3H2.
2.Адсорбция. Захват поверхностью металла активных атомов насыщаемого элемента и его частичное проникновение в решетку металла.
3.Диффузия. Заключается в проникновении насыщаемого элемента в глубь металла.
4.Десорбция. Уход с поверхности продуктов реакции во внешнюю среду.
35
Виды химико-термической обработки. Цементация – про-
цесс насыщения поверхности углеродом.
Цель – придание поверхности твердости при сохранении мягкой сердцевины. Цементации подвергают низкоуглеродистые стали
ссодержанием углерода не более 0,25 %. Температура цементации – 900–970 °С, толщина цементированного слоя 0,1–3,4 мм.
Цементацию проводят в твердых, жидких и газообразных средах, которые называются карбюризаторами.
Твердый карбюризатор состоит из древесного угля с добавка-
ми от 10–30 % BaCO3, K2CO3, Na2CO3. Процесс длится несколько часов.
Газовый карбюризатор – СО и предельные углеводороды, пары бензола.
Жидкие карбюризаторы – смесь цианистых солей и буры. Глубина слоя от времени изменяется по параболическому за-
кону. После цементации следует закалка и низкий отпуск. Азотирование – процесс насыщения стали (металлов) азотом.
Цель азотирования – придание поверхности высокой твердости, износостойкости, устойчивости против коррозии, повышение прочности.
Газовое азотирование заключается в воздействии на сталь аммиака при температурах 500–600 °С. Атомарный азот, который образуется на поверхности, образует с составляющими стали нитриды
свысокой твердостью. Толщина слоя 0,25–0,75 мм. Азотированию подвергают в основном легированные стали.
Цианирование – процесс насыщения поверхности одновременно углеродом и азотом в расплавленных цианистых солях при температурах 820–950 °С. Толщина слоев 150–350 мк, максимально
2000 мк.
После цианирования проводят ТО, закалку и нормальный отпуск. Недостаток – токсичность цианистых солей.
Нитроцементация представляет собой процесс насыщения поверхностного слоя одновременно азотом и углеродом в газовой
среде следующего состава: N2 – 20 %, H2 – 40 %, CO – 20 % при температуре 850–870 °С в течение 4–10 ч.
36
Цель – повышение износостойкости, твердости, коррозионной стойкости. После закалки и низкого отпуска толщина составляет 0,2–0,8 мм. Широко применяется в автомобилестроении и тракторостроении. По сравнению с цементацией более низкая температура процесса.
Контрольные вопросы
1.Дайте определение термической обработке (ТО).
2.Какими основными параметрами характеризуется ТО?
3.Назовите основные виды ТО.
4.Что является основой для назначения режимов ТО?
5.Назовите критические точки стального угла.
6.Что такое отжиг и какие виды отжига вы знаете? Структуры
отжига.
7.Что такое нормализация? Структуры нормализации.
8.Дайтеопределение закалки, виды закалки. Структуразакалки.
9.Что такое закаливаемость и прокаливаемость?
10.Отпуск, виды отпуска, структуры отпуска.
11.Что такое улучшение стали?
12.Дайте определение химико-термической обработке. Чем она отличается от ТО?
13.Из каких стадий состоит механизм ХТО?
14.В чем заключается цементация стали?
15.В чем заключается азотирование стали?
16.Вчем заключается цианированиеинитроцементация стали?
37
Глава 6 ЛЕГИРОВАННЫЕ СТАЛИ
6.1. Влияние легирующих элементов
Легированными называются стали, в которые кроме железа и углерода, вводят легирующие добавки в определенных количествах для придания стали специальных физико-механических свойств.
Основными легирующими элементами являются марганец, кремний, хром, никель, вольфрам, молибден, кобальт, титан, ванадий, цирконий, ниобий и др. Легирующие элементы по-разному влияют на свойства стали.
Хром и кремний повышают твердость, прочность, жаростойкость, коррозионную стойкость. При содержании хрома более 13 % сталь становится нержавеющей.
Никель и марганец повышают прочность, пластичность, электрическое сопротивление.
Вольфрам и молибден уменьшают величину зерна в сталях, повышают твердость и прочность, улучшают режущие свойства и коррозионные свойства.
По общему содержанию легирующих элементов легированные стали подразделяются на низколегированные (до 2,5 % легирующих элементов); среднелегированные (2,5–10 %); высоколегированные
(более 10 %).
Маркируют легированные стали: буквами и цифрами, которые указывают на химический состав стали.
Первые две цифры указывают содержание углерода в сотых долях процента. Затем ставится буква, указывающая на легирующий элемент, после буквы ставится цифра, указывающая на среднее содержание этого элемента в процентах. При содержании элемента менее 1 или равным 1 цифра не ставится.
Легирующие элементы обозначаются следующими заглавными буквами русского алфавита: К – кобальт, Д – медь, В – вольфрам,
38
Ю – алюминий, Х – хром, Н – никель, М – молибден, П – фосфор, Ц – цирконий, Ч – редкоземельные элементы).
Пример: 12ХН3А – 0,12 % С, 1 % Cr, 3 % Ni; буква А указывает, что сталь высококачественная.
6.2. Жаростойкие и жаропрочные стали
Способность металла сопротивляться окислению при высоких температурах называется жаростойкостью (окалиностойкостью).
Окалиностойкость в основном зависит от состава стали и мало от ее структуры. Для повышения прочности в стали добавляют хром, алюминий. Эти металлы обладают большим сродством к углероду и образуют на поверхности стали плотные оксидные пленки: Al2O3, SiO2, Cr2O3, которые предохраняют металл от дальнейшего окисления.
Примеры: 12Х18Н9Т – нержавеющая сталь, обладает высокими технологическими свойствами (хорошо сваривается, куется, поддается обработке давлением). Аналогичными свойствами обладает сталь мартенситного класса 2Х13.
Многие материалы работают при высокой температуре и испытывают при этом значительные нагрузки. Такие стали изготавливают из жаропрочных сплавов.
Жаропрочность – способность материала противостоять механическим нагрузкам при высоких температурах.
Требования, которые предъявляются к жаропрочным сплавам, разнообразны. В данном случае решающее значение имеют не только температурный фактор, но и фактор времени.
Для оценки механических свойств жаропрочных сплавов разработаны специальные виды испытаний, которые учитывают как фактор времени, так и температуры. При таких испытаниях определяют предел ползучести и предел длительной прочности.
Предел ползучести – напряжение, которое вызывает определенную скорость деформации при данной температуре. Обозначает-
ся Т/ , где T – температура, δ – относительная деформация, τ – время. При ползучести деформации идут в пограничных зонах, наблю-
39
дается межкристаллитное разрушение. Поэтому крупнозернистый металл в условиях высокой температуры является более жаропрочным, чем мелкозернистая.
Предел длительной прочности – напряжение, которое вызыва-
ет разрушение образца при данной температуре через определенный промежуток времени. Обозначается T .
6.3. Алюминий и его сплавы
Алюминий (Al) – металл серебристого цвета, плотность ρ = = 2,7 г/см3, tпл = 660 °С. Имеет ГЦК решетку без аллотропических превращений, обладает высокой электро- и теплопроводностью, хорошей коррозионной стойкостью за счет образования на его поверхности плотного окисла Al2O3. Стоек к концентрированной HNO3 (азотная кислота). Ввиду низкой прочности применяют в ненагруженных деталях (фольга, трубопроводы, теплообменники, провода и т.д.).
Алюминиевые сплавы нашли широкое применение в промышленности благодаря малой плотности при достаточно высоких характеристиках прочности, высокой стойкости против коррозии, как в атмосферных средах, так и в других средах, хорошими технологическими свойствами (обрабатываемость, свариваемость). В качестве основных легирующих элементов используются медь, магний, марганец, кремний, цинк.
По технологии изготовления изделий алюминиевые сплавы делят на 2 группы: деформируемые и литейные.
Деформируемые сплавы могут быть упрочняемыми и неупрочняемыми термической обработкой.
К термически неупрочняемым сплавам относятся системы Al – Mn (АМц) и Al – Mg (АМг). Эти сплавы хорошо обрабатываются давлением, хорошо свариваются, имеют высокую коррозионную стойкость.
Сплавы групп АМц и АМг не упрочняются термической обработкой. Их прочностные свойства повышают за счет холодного пла-
40