
книги / Специальные стали. Теория легирования
.pdfРаспад мартенсита
Мартенсит закалки на этой стадии превращается в мартенсит отпуска. Этот процесс происходит с закономерным уменьшением концентрации углерода в α-матрице, и к концу распада она становится более равновесной, близкой к концентрации углерода для феррита – 0,01 %.
Полностью завершится распад мартенсита при температуре 400 °С, в некоторых участках при более низких температурах. Таким образом, даже для одной и той же стали нет одной температуры, при которой завершается распад мартенсита – это всегда интервал от 300 до 400 °С.
Превращения при отпуске – это процесс, который зависит от температуры и химического состава мартенсита. Чем выше температура отпуска, тем ниже концентрация углерода в мартенсите. Этот процесс зависит от диффузионной подвижности атомов углерода
иподразделяется на две стадии.
1.Температура от 150 до 200 °С. В этом интервале невозможна интенсивная диффузия атомов углерода. На этой стадии происходит двухфазный распад мартенсита, когда в структуре одновременно существуют два твердых раствора с разной концентрацией углерода
ис разной степенью тетрагональности решетки α-фазы. На стадии двухфазного распада в участках, обогащенных углеродом (на сегрегациях углерода), образуются дисперсные частицы, процесс их образования сдвиговый, зародыш имеет форму пластины или стержня
икогерентен с матрицей – на этом этапе образуется ε-карбид. На его образование расходуется углерод из ближайшей области твердого раствора, и именно поэтому они не подрастают и распад мартенсита проходит в результате увеличения дисперсных карбидов, когерентных матрице.
Время распада твердого раствора мартенсита характеризуется временем полураспада – это такое время, за которое образуется примерно равное количество мартенсита обедненного, который располагается вблизи ε-карбида и мартенсита исходного, который вдали от ε-карбида. На стадию двухфазного распада мартенсита леги-
91
рующие элементы не влияют (нет диффузии атомов углерода, не на что влиять). В низкоуглеродистых сталях (с концентрацией углерода до 0,2%) стадии двухфазного распада нет, ε-карбид не образуется.
2. Однофазный распад. Температура отпуска от 150–200 °С. На этой стадии уже возможна интенсивная диффузия атомов
углерода, происходит выравнивание состава мартенсита. Есть возможность роста карбидов в результате диффузионного притока углерода из отдаленных участков, где в свою очередь происходит снижение концентрации углерода в мартенсите.
ε-карбиды еще сохраняют свою пластинчатую форму и когерентность с матрицей. На однофазный распад легирующие элементы влияют так, как влияют на диффузию атомов углерода (все карби-
дообразующие элементы и кремний затрудняют диффузию ато-
мов углерода), поэтому затрудняют распад мартенсита на этой стадии. Наличие этих элементов приводит к тому, что мартенсит сохраняется до более высоких температур. В легированных сталях наблюдают сохранение мартенситной структуры при отпуске до температуры 300–400 °С. В быстрорежущих сталях мартенсит сохраняется до 600 °С.
3. Карбидное превращение – это такое превращение, в результате которого меняется тип карбида. ε-карбид, который образовался
врезультате двухфазного распада мартенсита, является метастабильной фазой, термодинамически более выгодно образование цементита, поэтому на этой стадии происходит превращение ε-карбида
вцементит. В углеродистых сталях это единственное возможное
превращение. ε-карбид (Fe2C) при температуре 300–400 °С превращается в цементит (Fe3C). Образование цементита из ε-карбида начинается при температуре 200 °С, но наиболее интенсивно этот процесс начинается при температуре 300–400 °С. Цементитные частицы на ранней стадии, так же как и ε-карбиды, когерентны с матрицей и имеют пластинчатую форму, после образования цементита происходит разрыв когерентности. Эти выделения становятся самостоятельной фазой. Рассматривают два механизма образования цементита:
1)«механизм на месте» – происходит перестройка решетки ε- карбида в решетку цементита;
92
2) выделение цементита из твердого раствора. В этом случае выделению цементита предшествует растворение ε-карбида с увеличением концентрации углерода в локальном участке, далее в этом месте происходит выделение цементита.
В легированных сталях в зависимости от химического состава стали может происходить одно или несколько карбидных превращений. Если при отпуске не происходит образование специального карбида (недостаточное количество карбидообразующего элемента в твердом растворе, или недостаточны температура, или время для образования специального карбида), то в легированных сталях происходит только одно превращение, как и в углеродистых.
Например, в стали с концентрацией хрома менее 2 % при отпуске будет происходить только одно карбидное превращение:
MCr → αмСr + εкарбид εкарбид → Fe3C
Fe3C → (Fe, Cr)3C – такое карбидное превращение возможно только при температуре отпуска выше 500 °С.
В рассмотренном примере в стали с указанной выше концентрацией хрома присутствует только одно карбидное превращение (εкарбид → Fe3C). Образование легированного цементита не является карбидным превращением, так как не изменяется тип карбида.
Например, сталь с концентрацией хрома 3 %. В стали с такой концентрацией углерода возможно два превращения, так как образуются 2 типа карбида.
MCr → αмСr + εкарбидα;
1.εкарбид → Fe3C;
Fe3C → (Fe, Cr)3C;
2.(Fe, Cr)3C → (Cr, Fe)7C3.
При более высокой концентрации хрома, кроме этих двух типов, может образоваться карбид (Cr, Fe)23C6. Образование специальных карбидов возможно только при температуре выше 500 °С, так как для образования специальных карбидов необходима диффузия атомов легирующих элементов и флуктуация атомов хрома. Механизмы образования специальных карбидов те же, что и цементита:
93
«на месте» и из твердого раствора. Экспериментально установлено, что для образования карбидов хрома возможны оба механизма, но предпочтительнее механизм «на месте». Для других карбидообразующих элементов имеет место второй механизм образования карбидов. Заметное образование специальных карбидов наблюдается при температуре отпуска 500–600 °С, при этом температура образования специального карбида зависит от типа специального карбида. Чем выше карбидообразующая способность элемента, тем позднее произойдет выделение специального карбида.
С другой стороны, температура образования зависит от диффузионной подвижности атомов карбидообразующего элемента, так как для образования специального карбида необходимо локальное обогащение атомами легирующего элемента: чем выше диффузионная подвижность атомов карбидообразующего элемента, тем раньше начинается образование его карбида. Учитывая вышесказанное, можно указать следующие интервалы образования специальных карбидов при отпуске:
Cr – V – 450 °C;
Mo – W – 500 °C;
Nb – Ti – 550–600 °C.
Cr и V имеют меньшую разницу в атомных радиусах относительно железа и поэтому легко диффундируют по кристаллической решетке.
Коагуляция карбидов
Это процесс, при котором происходит сфероидизация или округление и укрупнение карбидов. В момент образования карбид имеет пластинчатую форму и, как следствие, большую поверхностную энергию. При температуре выше 400 °C начинается процесс коагуляции цементитных частиц, этот процесс идет самопроизвольно, так как ведет к уменьшению свободной энергии, склонность к коагуляции зависит от устойчивости карбида.
Коагуляция частиц цементита в углеродистых сталях происходит в три этапа:
94
1)растворение мелких частиц и переход углерода в твердый
раствор;
2)диффузия атомов углерода по кристаллической решетке; движущей силой является выравнивание концентрации;
3)подрастание более крупных частиц.
Коагуляция частиц легированного цементита происходит аналогичным образом, но этот процесс проходит более трудно. Частицы легированного цементита всегда более устойчивы к коагуляции. Для того чтобы процесс коагуляции начался, требуется:
–разрушение межатомных связей в частицах легированного цементита, при этом легирующие элементы и углерод переходят
втвердый раствор;
–карбидообразующие элементы, находясь в твердом растворе, затрудняют диффузию атомов углерода;
–таким образом, скорость процесса коагуляции определяется скоростью растворения частиц и скоростью диффузии атомов углерода.
Необходимо помнить, что частицы легированного цементита гораздо меньше, чем обычного.
Коагуляция частиц специальных карбидов
Механизм у данного процесса тот же, что и при коагуляции частиц цементита, но протекает гораздо труднее. Эти частицы более устойчивы к растворению, и, переходя в твердый раствор, легирующие элементы будут затруднять диффузию атомов углерода, которая нужна для процесса коагуляции. Для коагуляции частиц специальных карбидов потребуется диффузия атомов легирующих элементов, что делает этот процесс еще более затруднительным, а специальные карбиды очень устойчивы к растворению. При одинаковом режиме отпуска частицы специальных карбидов в десятки раз меньше, чем частицы цементита, и более устойчивы к коагуляции. Ряд устойчивости карбидов к коагуляции (от минимальной к наибольшей):
Me3C – Me7C3 – Me23C6 – Me6C – Me2C – MeC
95
Распад остаточного аустенита
В углеродистых сталях распад остаточного аустенита происходит в интервале температур 200–300 °С. В результате распада получаются те же продукты, что и при распаде мартенсита:
– Аост → Мотп (αм + εк) – механизм этого превращения схож с промежуточным, но протекает при температуре 200–300 °С; если температураотпусканижечем200 °С, товструктуресохранитсяАост;
Мзак + Аост → Мотп + Аост (температура меньше 200 °С); Мзак + Аост → Мотп или ФКС (температура выше 300 °С).
При температурах отпуска ниже 200 °С распад мартенсита идет, а остаточный аустенит остается, так как при этих температурах затруднена диффузия атомов углерода. Влияние легирующих элементов на остаточный аустенит чисто количественное и может быть как положительным, так и отрицательным. Влияние легирующих элементов на аустенит остаточный схоже с влиянием на аустенит переохлажденный, поэтому отметим, что элементы, которые затрудняют распад аустенита переохлажденного, затрудняют и распад аустенита остаточного. В том случае, если в состав введено большое количество легирующих элементов, кинетика распада остаточного аустенита описывается теми же диаграммами, что и переохлажденного. В этом случае продукты превращения будут зависеть от диаграммы превращения переохлажденного аустенита и от температуры отпуска стали. При температуре отпуска 500 °С существуют области длительной устойчивости аустенита и превращение не происходит ни по механизму Аr', ни по Аr'' (рис. 41).
При отпуске стали, имеющей диаграмму, схожую с изображенной на рис. В2 б, в области Аr'' аустенит остаточный распадается по бейнитному механизму, при отпуске в области Аr' – из аустенита остаточного образуется ФКС. Следует помнить, что при высоком отпуске в некоторых сталях возможно снижение ударной вязкости, что связано с образованием пластинчатых карбидов, которые приводят к снижению характеристик вязкости.
Еще одна ситуация, которая может произойти исходя из рис. 41: вобласти А → К (повышенной устойчивости аустенита) при выдержке
96
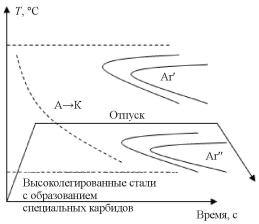
происходит выделение карбидной фазы из аустенита, и при этом изменяется химический состав аустенита, в первую очередь по углероду ипо легирующим элементам, что приводит к повышению мартенситных точек стали и возможности пройти мартенситному превращению при охлаждении с данной температуры отпуска. По сути, при отпуске становится возможным мартенситное превращение: Аобедн → Мзак; такоеявлениеназываетсявторичнойзакалкой.
Рис. 41. Диаграмма устойчивости переохлажденного аустенита высоколегированных сталей
Для протекания вторичной закалки не требуется охлаждения с большой скоростью. Образование мартенсита возможно и на воздухе. В результате этого процесса наблюдается закономерное повышение твердости и возникновение закалочных напряжений, поэтому, если при отпуске прошла вторичная закалка, необходим дополнительный отпуск для снятия напряжений. Температуру для отпуска с целью снятия напряжений выбирают либо ту же, либо ниже. При этом происходит распад мартенсита закалки на мартенсит отпуска или ФКС. В высоколегированных сталях за одну операцию отпуска невозможно избавиться от всего остаточного аустенита, требуется 2-3-кратный отпуск иногда и 4-кратный.
97
Явление отпускной хрупкости стали
Конструкционные стали, подвергаемые закалке и отпуску, имеют склонность к отпускной хрупкости. После отпуска при определенной температуре может наблюдаться повышение температуры вязко-хрупкого перехода.
Различают два рода отпускной хрупкости:
1)необратимая отпускная хрупкость (НОХ) (при отпуске око-
ло 300 °С);
2)обратимая отпускная хрупкость (ООХ) (при температуре от 500 °С).
НОХ присуща практически всем углеродистым и легированным сталям в интервале температур 200–400 °С, при повторном отпуске при более высокой температуре сталь становится к ней не склонна, даже при повторном отпуске уже в опасный интервал температур. Этот вид хрупкости не зависит от скорости охлаждения после отпуска.
Возможные причины отпускной хрупкости:
•карбидное превращение при распаде мартенсита;
•сегрегации вредных примесей на границах зерен (P, As, Sb);
•распад остаточного аустенита;
•образование на границах микрообъемов, легированных мар-
ганцем.
Методы борьбы с отпускной хрупкостью:
•увеличениепротяженностиграницзерен(измельчениезерна);
• вредные примеси чаще всего начинают диффундировать к границам зерен при температуре 500 °С, поэтому не могут являться причиной НОХ;
•Мо и W в следующих концентрациях полностью устраняют склонность стали к НОХ: Мо 0,4–0,5 %, W 1,2–1,5 %;
•кремний – смещает интервал отпускной хрупкости к более высоким температурам;
•на практике стараются избегать попадания в опасные интервалы температур.
98
Причиной НОХ принято считать выделение карбидов по границам при распаде мартенсита.
Обратимая отпускная хрупкость (ООХ) наиболее присуща легированным сталям после высокого отпуска в интервале 500–650 °С и медленного охлаждения после отпуска. На ООХ влияет скорость охлаждения после отпуска, при быстром охлаждении ее удается подавить, но медленное охлаждение и длительные выдержки в этом интервале приведут к ухудшению характеристик вязкости. Она может быть устранена при отпуске с более высоких температур, но опять проявит себя при отпуске в нужный интервал температур. Системы легирования Cr, Ni, Mn; Cr, Mn, Si – усиливают ООХ. Введение в состав стали Мо 0,4–0,5 %, W при концентрации 1,2–1,5 % приводит либо к полному устранению, либо к уменьшению ООХ.
Наиболее распространенными причинами ее образования являются:
–образование карбидов хрома и марганца по границам зерен;
–сегрегация вредных примесей P, As, Sb и других на границах
зерен.
Методы борьбы: легирование молибденом и вольфрамом.
Лекция 12. Конструкционная прочность
Конструкционная прочность характеризует возможность реализации в конкретных условиях эксплуатации той прочности, котрая определена в стандартных условиях при одноосном центральном растяжении. Реализованная прочность сталей или конструкционная прочность в конкретной конструкции зависит от условий эксплуатации (напряженного состояния, скорости и цикличности нагружения, среды, температуры и т.д.) и комплекса свойств стали, который обусловливает реализуемый механизм упрочнения, определяющийся составом и свойствами.
Прочность сталей, определенная при одноосном растяжении, зачастую не реализуется в конкретных условиях эксплуатации. Степень реализации прочности в конструкции можно определить как отношение напряжений в момент разрушения в конкретных услови-
99
ях эксплуатации детали к пределу прочности, определенному при стандартных испытаниях.
Классическое определение конструкционной прочности: характеристика материала, представляющая собой комплекс свойств, обеспечивающих длительную и безотказную работу конкретных деталей в реальных условиях эксплуатации. Она включает в себя три группы характеристик:
1)характеристики прочности (σв, σ0,2, σупр и др.);
2)характеристики долговечности, характеризующие срок
службы материала (коррозионные испытания, испытания на износостойкость, в данном случае подбирают характеристики, максимально приближенные к условиям эксплуатации);
3) характеристики надежности – характеризуют способность материала хотя бы кратковременно работать в нерасчетных условиях эксплуатации.
Материал с высоким уровнем надежности имеет низкую склонность к хрупкому разрушению. К характеристикам надежности относятся следующие: относительное удлинение, относительное сужение (δ, ψ), характеристики ударной вязкости (KCU, KCV, KCT). Причем последние более информативны и показательны при оценке надежности материала. Ударная вязкость является энергетической характеристикой (удельная работа разрушения при ударе), характеризует энергоемкость в процессе разрушения. Оценивать надежность по величине ударной вязкости можно, используя любой вид надреза (U, V, T), но наиболее жесткие условия, а следовательно, и приближенные к реальным ситуациям, – при эксплуатации образца с Т-образным концентратором напряжений.
Следующей характеристикой, для оценки надежности служит Т50 или Ткр – температура вязко-хрупкого перехода. Данная характеристика определяется с помощью графика зависимости КCU от Т: та температура, при которой в структуре будет 50 % вязкой и 50 % хрупкой составляющей в изломе, и будет являться критической.
К1с и другие вышеперечисленные характеристики могут дать более полную информацию о материале с точки зрения надежности.
100