
книги / Специальные стали. Теория легирования
.pdf
Прокаливаемость зависит от соотношения действительной скорости охлаждения и критической скорости закалки.
Если ʋд ˃ ʋкр – сквозная прокаливаемость; ʋд ˂ ʋкр – нет закалки;
ʋдпов ˃ ʋкр |
несквозная прокаливаемость |
||
ʋдсердц |
˂ ʋкр |
||
|
Низкая прокаливаемость ограничивает применение сталей в машиностроении. Основной задачей, которая стоит перед разработчиками материалов, является повышение прокаливаемости, а это увеличение действительной скорости и понижение критической; задачи могут решаться как по отдельности, так и вместе.
Скорость действительная зависит от нескольких факторов: ох-
лаждающая способность среды, габаритные размеры деталей, коэффициент теплопроводности металла.
При охлаждении с высокими скоростями высок риск коробления и трещинообразования детали, накопление большого количества внутренних напряжений, которые могут релаксировать в любой момент (по этой причине для многих сталей в технологии оговаривается время между закалкой и низким отпуском не более 2 часов). На коэффициент теплопроводности влияют легирующие элементы. Для некоторых сталей с низким коэффициентом теплопроводности применяют ступенчатые варианты нагрева под закалку, чтобы нагрев был более равномерным и однородным.
Критическая скорость закалки – характеристика, зависящая от ряда факторов: химический состав аустенита, размер зерна, наличие частиц второй фазы.
Легирующие элементы влияют на все три фактора, включая косвенное влияние на размер зерна и частицы второй фазы.
В качестве меры прокаливаемости используют Dкр. Различают реальный и идеальный критический диаметр.
Dкр идеальный – используют в расчетах, закалка со скоростью, во много раз превышающей критическую скорость закалки данной стали.
81
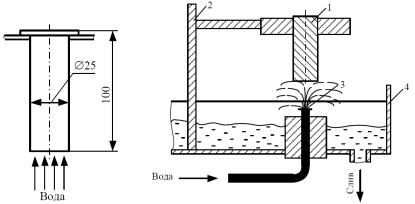
Dкр реальный – это максимальный диаметр сечения, в котором закалка получается сквозной при охлаждении в конкретной охлаждающей среде (вода или масло).
Критический диаметр – это характеристика индивидуальная для каждой стали, для каждой охлаждающей среды, его значения приводят в справочниках или определяют экспериментальным путем: методом торцевой закалки с помощью марочных полос прокаливаемости.
Существует еще несколько способов определения прокаливаемости, в основу которых положены: внешний вид излома, распределение твердости по сечению образца, а также метод торцевой закалки (методом Джомини), который является наиболее простым и надежным.
Испытания методом торцевой закалки проводят с использованием стандартных образцов и специальной установки согласно ГОСТ 5657–69. Внешний вид образца и его размеры представлены на рис. 35, схема установки на рис. 36.
Рис. 35. Вид образца |
Рис. 36. Схема установки для проведения |
для торцевой закалки |
торцевой закалки по методу Джомини: 1 – образец; |
|
2 – штатив; 3 – сопло для подачи охлаждающей |
|
жидкости; 4 – контейнер для скопления и слива |
|
жидкости |
82 |
|
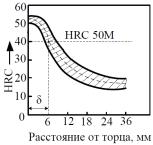
Образец стандартных размеров (см. рис. 35) нагревают под закалку в муфельной печи в течение 30 мин. После нагрева образец быстро переносят в специальную установку, где его охлаждают с торца струёй воды. Скорость охлаждения образца в разных точках его длины будет различной. Максимальная скорость охлаждения достигается у торца, минимальная (соответствующая охлаждению на воздухе) – у противоположного конца образца. На торце и в сечениях, где скорость охлаждения была больше критической, получается структура мартенсита.
После проведения эксперимента осуществляют замер твердости образца на предварительно снятой лыске (лыски снимают с двух противоположных сторон для замера твердости). Измерение твердости проводят по мере удаления от закаливаемого торца на определенных, заранее отмеченных расстояниях (как правило, это 1,5 мм; 3 мм; 4,5 мм и так далее через 1,5 мм). Замеры проводят до тех пор, пока твердость не перестанет закономерно падать и примет стабиль-
ное значение (рис. 37). |
|
На рис. 37 пунктирной лини- |
|
ей обозначена полоса прокаливае- |
|
мости стали конкретного химиче- |
|
ского состава (одного образца). |
|
Для того чтобы построить мароч- |
|
ную полосу прокаливаемости, про- |
|
водят серию испытаний на образ- |
|
цах с разным химическим соста- |
|
вом, входящим в диапазоны |
Рис. 37. Полоса прокаливаемости |
данной марки. Получают в итоге |
|
марочную полосу прокаливаемо- |
среднеуглеродистой стали |
|
|
сти (см. ГОСТ для легированной |
|
стали), схематичное изображение полосы схоже с рис. 37, но кроме сплошной линии она имеет еще и две пунктирных, расположенных одна выше верхней сплошной, вторая ниже нижней сплошной (- – - – - (пунктирная) – обычная выплавка стали; ______ (сплошная линия) – суженный интервал химического состава).
83
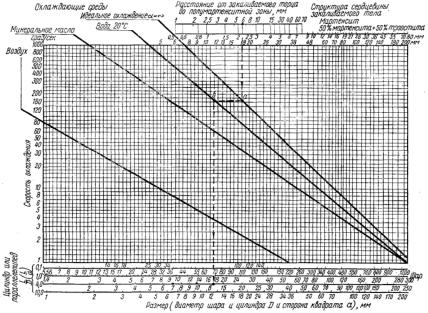
Нижняя линия означает минимальное содержание легирующих элементов и углерода, верхняя – максимальное возможное для данной марки содержание элементов. Для определения критического диаметра достаточно нижней полосы, для определения прокаливаемости понадобится вся полоса.
Далее требуется применение полос для оценки желаемой твердости в зависимости от содержания углерода и доли мартенсита, после чего по полученному значению твердости определяют Lкр и уже с использованием номограммы Блантера вычисляют Dкр
(рис. 38).
Рис. 38. Номограмма М.Е. Блантера
Для оценки влияния каждого элемента на прокаливаемость рассмотрим следующие примеры. В технически чистом железе (0,04 % С) скорость нормального γ→α-превращения (рекристаллизационного типа), особенно при 700–600 °С, настолько велика, что обычной обработкой не удается добиться переохлаждения, достаточного для мар-
84
тенситного перехода. Однако опыт показал, что нелегированное железо (0,01% С; 0,05% Мn) можно закалить, если нагрев под закалку произвести выше 1150–1200 °С. Экспериментальные данные показывают, что нормальное γ→α-превращение особенно сильно замедляется при одновременном легировании хромом и никелем.
Время полупревращения γ-фазы, например, при 600 °С в нелегированном железе составляет 7–10 с, в железе с 2,5% Ni – 14–15 с, в железе с 7% Сr 35–40 с, а в сплаве с 7% Сr и 2,5% Ni около 10 мин. Добавление около 1% Мо или W (0,01% С; 6,3% Сг; 3% Ni; 1,3% Mo) приводит к тому, что даже для превращения 0,5% γ-фазы требуется пятичасовая выдержка. Превращение γ→α ускоряется кобальтом, но значительно замедляется при одновременном легировании хромом и кобальтом. Такой сложный характер изменения скорости нормального γ→α-перехода в железе, по-видимому, связан с влиянием легирующих элементов на межатомное взаимодействие. Таким образом, скорость γ→α-превращения рекристаллизационного типа заметно понижается при легировании хромом и марганцем, никелем и молибденом.
Комплексное легирование низкоуглеродистого железа с сочетанием элементов Сr-Ni, Cr-Mn позволяет увеличить устойчивость аустенита до 240 мин и исключить бейнитное превращение, одновременно повысив точку Мн до 400 °С.
Влияние хрома. При содержании 0,04–0,08 % С и 2 % Мn устойчивость сталей с 2 % Сr соответствует прокаливаемости на воз-
духе, равной 3–10 мм, с 3–4 % Сr – 30–60 мм, с 5 % Cr – 140 мм, при 7 % Сr – до 400 мм.
Влияние марганца. При содержании 0,06% С и 7% Сr прокаливаемость стали с 1,5 % Мn – 55 мм, с 2 Мn – 220 мм; прокаливаемость стали 06Х2Г2 – 10 мм, а стали 06Х2Г3 – более 600 мм. Очевидно, увеличение содержания марганца от 2 до 3 % чрезвычайно эффективно увеличивает прокаливаемость, более эффективно, чем увеличение содержания хрома с 2 до 7 %.
Влияние молибдена. Прокаливаемость стали 06Х7Г2 – 220 мм, а стали 06Х7Г2М0,4 – 600 мм; стали 06Х2Г2 – 10 мм, а стали
06X2Г2M0,9 – 55 мм; стали 06Х5Г2 – 140 мм, а стали 06Х5Г2М0,3 –
85
600 мм. Таким образом, при содержании молибдена 0,3 % и более прокаливаемость хромомарганцевых низкоуглеродистых сталей сильно увеличивается.
Влияние меди. Добавка 2 % Сu повышает прокаливаемость стали 06Х7Г2 с 220 до 400 мм, однако влияние 2 % Сu менее эффективно, чем влияние 0,4 % Мо; так, прокаливаемость стали
06Х7Г2М0,4 более 600 мм.
Стали хромоникелевого состава
Влияние хрома. Прокаливаемость стали 11X3H2 – 90 мм, 11Х4Н2М – 280 мм, 08Х5Н2 – более 600 мм, 11X6H2 – более
1500 мм, т.е. повышение содержания хрома в стали от 3 до 6 % значительно увеличивает прокаливаемость, но и прокаливаемость стали 11X3H2 достаточна для закалки на воздухе изделий диаметром до 90 мм.
Влияние никеля. Прокаливаемость сталей 11X4H1 на воздухе составляет 55 мм, сталей 11Х4Н2 – 280 мм, 11X6H1 – 90 мм, 11X6H2 – более 1500 мм. Таким образом, увеличение содержания никеля от 1 до 2 % резко увеличивает прокаливаемость низкоуглеродистых мартенситных сталей. Для изделий толщиной менее 90 мм можно использовать стали, содержащие 1 % Ni.
Влияние никеля, марганца, молибдена. С целью экономии ни-
келя целесообразно заменять его в ряде сталей более дешевым марганцем. Из полученных данных следует, что замена 1 % Ni на марганец снижает прокаливаемость с 600 до 140 мм. Однако добавка 0,2–0,3 % Мо может увеличить прокаливаемость до 600 мм.
Таким образом, определенное сочетание легирующих элементов и углерода (рис. 39) позволяет создавать стали с необходимой устойчивостью аустенита, обеспечивающей образование мартенситной структуры при низких скоростях охлаждения, и прежде всего на воздухе. Каждый легирующий элемент может как отрицательно, так и положительно влиять на разные характеристики механических свойств. Поэтому предпочтительно всегда легировать не одним элементом (монолегирование), а несколькими (комплексное легирование), тогда можно обеспечить одновременное увеличение комплекса механических свойств.
86
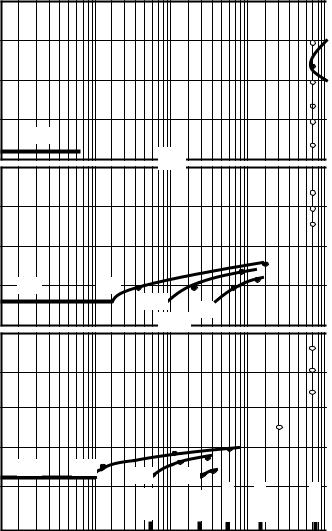
t, °С
700
600
500
400 t, °С
600
500
400
300
t, °С
600
500
400
300
Мн
а
Мн 5 %
25 % |
50 % |
|
|
|
б |
Мн |
5 % |
25 % |
50 % |
|
|
|
|
|
|
|
|
||
|
|
1 мин |
5 мин |
10 мин |
30 мин |
2 ч |
1 |
10 |
|
102 |
|
103 |
104 |
в
Время, с
Рис. 39. Диаграммы изотермического превращения аустенита сталей,
содержащих 2 % Cr, 3 % Mn и добавки 0,04 % С (а); 0,09 % С (б); 0,13 % С (в); tауст = 900 °C
87
Конкретный состав стали определяется также условиями ее эксплуатации и технологическими требованиями, обусловленными методом упрочнения, для получения заданного комплекса физикомеханических свойств
Лекция 11. Превращения при отпуске в легированной стали
Влияние легирующих элементов на превращения при отпуске
Отпуском называется операция нагрева закаленной стали на температуру ниже Ас1. Цели у отпуска могут быть разные, одной из них является снятие закалочных напряжений, получение требуемого комплекса характеристик механических свойств, устранение/уменьшение количества остаточного аустенита. В некоторых случаях операция отпуска проводится после механической обработки или после сварки сложного элемента конструкции с целью снять накопившиеся напряжения от предыдущей операции. Поэтому нагрев важно проводить под отпуск до температуры не выше той, на которую был проведен отпуск по технологии после закалки. В случае несоблюдения данного требования комплекс свойств, который был получен ранее при окончательном режиме термической обработки, будет утрачен деталью или конструкцией.
После закалки основной фазой в структуре стали является мартенсит, в отличие от равновесных фаз он обладает двумя особенностями из-за которых он метастабилен:
–мартенсит – это пересыщенный по углероду твердый раствор на основе α-железа (имеет тетрагональную решетку при определенной концентрации углерода);
–высокая плотность дислокаций.
Таким образом, мартенсит – это неустойчивая составляющая структуры (возможно образование более устойчивых составляющих), поэтому процессы в мартенсите могут проходить самопроизвольно. Незначительные перемещения атомов углерода в структуре мартенсита могут происходить и при комнатной температуре.
88
Выделяют три процесса перемещения атомов углерода в пределах элементарной ячейки.
1. Передвижение атомов углерода из одного междоузлия в другое, чтобы все атомы углерода расположились вдоль одного направления, совпадающего с осью деформации Бейна. Более выгодно такого рода перемещение в том случае, если не требуется диффузия атомов углерода. Данное кооперативное смещение атомов приводит к увеличению степени тетрагональности решетки (возможно в сталях с высокой температурой Мн и в стали с реечным мартенситом и концентрацией углерода до 0,6 %).
2.Следующий вариант перемещения атомов углерода – это перемещение атомов С к дислокациям. Данный процесс требует диффузии атомов углерода на расстояния большие, чем в предыдущем случае. При комнатной температуре перемещения такого рода сильно затруднены (один перескок за 25 с).
3.Осаждение углерода на дислокациях. Данный процесс завершается образованием атмосфер Котрелла, на дислокации может расположиться 0,2 % углерода, имеющегося в стали. В сталях с содержанием углерода до 0,2 % атмосферы Котрелла не образуются. Для того чтобы осаждение произошло при комнатной температуре, потребуется несколько часов. Также возможны образование кластеров, скопления атомов углерода одноатомной толщины. И атмосферы Котрелла, и кластеры – это участки с повышенным содержанием углерода, т.е. те места, где возможно образование карбидов. Для образования карбидов требуется флуктуация по концентрации углеро-
да. В сталях с высокой температурой Мн превращения при отпуске подчиняются правилам термодинамики (рис. 40).
Мартенсит превращается в феррито-карбидную смесь постепенно, поэтому процесс можно остановить в любой момент и получить необходимый комплекс свойств. Структурные составляющие, которые получаются при отпуске углеродистой стали, в разных температурных интервалах имеют свои названия:
– температура отпуска менее 300 °С – мартенсит отпуска;
– температура отпуска от 300 до 450 °С – троостит отпуска;
– температура отпуска от 450 до 650 °С – сорбит отпуска.
89
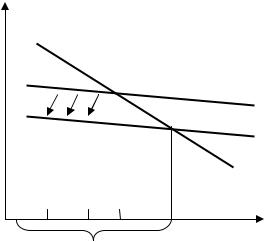
F
М
∆F
ФКС
А
Т, °С
Ас1
Тотп
Рис. 40. Термодинамические условия превращения
С увеличением легирующих элементов устойчивость мартенситной структуры возрастает и получение более разупрочненной структуры происходит при более высокой температуре.
Так как в структуре кроме мартенсита закалки присутствует еще и остаточный аустенит, то в процессе отпуска он тоже будет распадаться ввиду своей нестабильности. Температура распада остаточного аустенита также будет зависеть от степени легирования.
Следует помнить, что если в структуре стали после закалки есть нерастворенные при нагреве частицы карбидов, то в процессе отпуска они не участвуют. В процессе отпуска будут участвовать только две составляющие – мартенсит и остаточный аустенит.
Все процессы, протекающие при отпуске, можно классифицировать и выделить пять основных стадий:
1)распад мартенсита;
2)распад остаточного аустенита;
3)карбидное превращение;
4)коагуляция карбидов;
5)уменьшение закалочных напряжений и рекристаллизация
α-фазы.
90