
книги / Технология электроэрозионной обработки
..pdf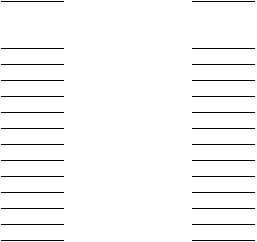
В результате ЭЭО образуется поверхность, представляющая собой совокупность большого количества лунок. Основными характеристиками лунок являются: радиус rл, глубина hл, их соотношение K = rл/hл, а также коэффициент перекрытия лунок β (отношение rл к расстоянию между соседними лунками L). Как правило, данные параметры и определяют основные показатели ЭЭ процесса, такие как производительность, шероховатостьобработаннойповерхностииточностьобработки.
Размеры лунок зависят от многих факторов, одним из которых являются физико-механические свойства обрабатываемого материала. Для оценки влияния этих свойств используется критерий фазового превращения Палатника. Данный критерий определяется как произведение основных физико-механических показателей:
П с Tп2 ,
где с – удельная теплоемкость материала; λ – коэффициент теплопроводности материала; ρ – плотность материала; Тп – температура плавления материала.
По данному критерию также можно судить об эрозионной стойкости того или иного материала. Чем выше значение критерия, тем выше эрозионная стойкость материала.
Физико-механические свойства сталей представлены в табл. 1.1. Таблица 1 . 1
Параметр/ |
ρ, |
3 |
λ, |
с, |
Тп, |
о |
С |
П с T2 |
, |
марка |
кг/м |
Вт/м·К |
Дж/кг·К |
|
п |
|
|||
материала |
|
|
|
|
Дж·Вт/м4 |
|
|||
40 |
7850 |
50 |
470 |
1535 |
6,03·1014 |
|
|||
45 |
7826 |
48 |
473 |
1535 |
5,81·1014 |
|
|||
40Х |
7850 |
41 |
466 |
1535 |
4,88·1014 |
|
|||
5ХНВ |
7900 |
41 |
466 |
1500 |
4,78·1014 |
|
|||
35ХГСА |
7850 |
38 |
496 |
1500 |
4,65·1014 |
|
|||
У10 |
7810 |
40 |
469 |
1535 |
4,79·1014 |
|
|||
У8А |
7819 |
42 |
470 |
1535 |
5,05·1014 |
|
|||
Х12М |
7770 |
42 |
462 |
1500 |
4,90·1014 |
|
|||
Х12Ф1 |
7770 |
30 |
482 |
1500 |
8,01·1014 |
|
|||
5ХГСВФ |
7920 |
38 |
461 |
1500 |
4,36·1014 |
|
|||
5ХНСВ |
7920 |
40 |
480 |
1500 |
4,78·1014 |
|
|||
5ХНМ |
7900 |
42 |
475 |
1500 |
4,95·1014 |
|
11
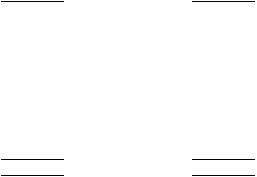
Окончание табл. 1 . 1
Параметр/ |
ρ, |
3 |
λ, |
с, |
Тп, |
о |
С |
П с T2 |
, |
марка |
кг/м |
Вт/м·К |
Дж/кг·К |
|
п |
|
|||
материала |
|
|
|
|
Дж·Вт/м4 |
|
|||
3Х2В8Ф |
7920 |
36 |
482 |
1500 |
9,40·1014 |
|
|||
4Х2В5ФМ |
7950 |
38 |
492 |
1500 |
4,88·1014 |
|
|||
40ХНВА |
7850 |
20 |
495 |
1527 |
2,51·1014 |
|
|||
Р6М5 |
7859 |
34 |
460 |
1520 |
2,84·1014 |
|
|||
Медь М2 |
8860 |
390 |
450 |
1350 |
2,227·1015 |
|
|||
Латунь |
8200 |
150 |
360 |
1158 |
5,979·1014 |
|
|||
ЛС59-1 |
8800 |
|
|
1350 |
|
|
|||
Углеграфит |
125 |
400 |
6,03·1014 |
|
1.3. Стадии нагрева и охлаждения поверхностей электрода при электроэрозионной обработке
Исследования структуры и свойств поверхностного слоя обработанного материала после ЭЭО показали, что они близки к получаемым после термической обработки [5, 10]. Таким образом, для получения качественной поверхности после ЭЭ-обработки необходимо учитывать условиянагрева иохлаждения поверхности единичной лунки.
При нагреве поверхностного слоя в процессе ЭЭО его свойства будут определяться величиной внутренних напряжений, возникающих в результате значительной разности температур. При определенных условиях напряжения могут превышать предел прочности обрабатываемого материала, что приведет кобразованию сеткимикротрещин.
При охлаждении поверхностного слоя заготовки в процессе ЭЭО существенно меняются его структура и свойства. Возможности воздействия на качество поверхности при этом сравнительно широки и определяются подбором состава рабочей жидкости, а также режимами ЭЭО.
На рис. 1.6 показан характер изменения температуры поверхности лунки при воздействии на поверхность электрического импульса длительностью tи.
Тепловой режим I (см. рис. 1.6) связан с образованием плоского мгновенного источника тепла, действующего в течение t ≤ tи. За это время происходит интенсивный нагрев поверхностных слоев элек-
12
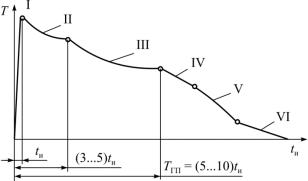
тродов вплоть до их расплавления и испарения. Тепловой режим II охватывает время tи ≤ t = (3…5)tи, т.е. с момента окончания импульса тока до момента дополнительного выброса металла из лунки. В этот период поверхность лунки покрыта перегретым металлом с температурой, превышающей его температуру плавления [10].
Рис. 1.6. Диаграмма изменения температуры поверхности лунки
Тепловой режим III начинается после дополнительного выброса металла из лунки и заканчивается, как можно условно считать, при t = TГП = (5…10)tи, т.е. одновременно с началом ликвидации газовой полости (ТГП – время существования газовой полости). Температура поверхности лунки близка к температуре плавления обрабатываемой заготовки. В это время еще сохраняется значительный градиент температур в поверхностном слое заготовки [10].
Ускоренный процесс охлаждения поверхности лунки (тепловой режим IV) начинается с t > ТГП, т.е. после окончания дополнительного выброса металла из лунки, и особенно в момент, когда диаметр газовой полости приближается к минимальному. В это время газовая полость постепенно уменьшается и ее граница перемещается к центру лунки. Затем наступает момент, когда граница газовой полости, представляющая собой парожидкостную смесь, соприкоснется с периферийной частью поверхности лунки, имеющей высокую темпера-
13
туру. В результате часть рабочей жидкости газовой полости превращается в пар. Появление пузырьков пара приводит к пульсации размеров газовой полости [10].
Как отмечено в работах [11–14], учитывая специфику условий протекания процесса ЭЭО, сомнительно утверждать, что пленочное кипение жидкости в межэлектродном промежутке переходит в пузырьковое, как это имеет место при охлаждении открытых поверхностей. Также отмечалось, что с понижением температуры поверхности лунки рабочая жидкость всё чаще соприкасается с ней и, испаряясь, интенсивно отводит тепло. Охлаждение на этой стадии (тепловой режим V) происходит с наибольшей скоростью.
По мере охлаждения поверхности лунки до температуры кипения РЖ газовая полость ликвидируется и жидкость начинает омывать всю поверхность лунки. Наступает последняя стадия охлаждения (тепловой режим VI), которая характеризуется конвективным теплообменом поверхности лунки с рабочей жидкостью, вступивших в непосредственный контакт. Скорость теплообмена в этот момент умеренная (см. рис. 1.6) и определяется в основном свойствами рабочей жидкости, величиной температурного перепада между поверхностью лунки и РЖ, а также скоростью перемещения рабочей жидкости в межэлектродном промежутке.
1.4. Шероховатость поверхности при электроэрозионной обработке
Шероховатость поверхности оказывает значительное влияние на эксплуатационные свойства деталей.
После электроэрозионной обработки поверхность ЭД имеет некую шероховатость, образованную путем большого количества взаимно пересекающихся лунок. Параметры шероховатости определяются размерами и геометрией двух групп неровностей: полученных в результате взаимного пересечения лунок и образовавшихся в результате искажения профиля лунки. Первая группа неровностей в значительной степени будет определяться размерами лунок: rл, hл, β. С использованием данных факторов становится возможным опреде-
14
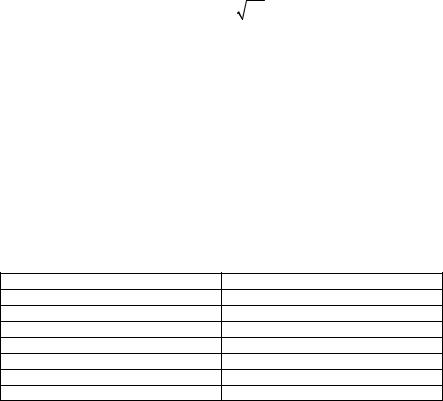
ление параметров шероховатости. Вторая группа неровностей полностью определяется случайными факторами, определение которых практически невозможно. Таким образом, реальный профиль шероховатости можно разделить на две составляющие: систематическую
ислучайную. Случайная составляющая профиля шероховатости составляет примерно 10–15 % от систематической [8].
Шероховатость зависит в первую очередь от энергии импульса
исвойств обрабатываемого материала [6]:
Rz 2 k4 3 Wи , 3
где β – коэффициент перекрытия лунок (для максимальной шероховатости β = 1,2); k4 – постоянная величина, не зависящая от длительности и энергии импульса (значения коэффициента k4 для различных материалов приведены ниже); Wи – энергия импульса.
Чем выше электроэрозионная обрабатываемость материала, тем большую высоту микронеровностей имеет обработанная поверхность. Стоит отметить, что параметры шероховатости поверхности, обработанной электроэрозионным способом, существенно отличаются от параметров поверхностей, обработанных резанием и виброобкатыванием.
Значения коэффициента k4
Материал заготовки |
k·103, см/Дж1/3 |
Al |
12–15 |
Cu |
6–8 |
Fe |
5,5 |
Ni |
67 |
Сталь 45 |
5–6 |
ВК-6 |
1,5–2 |
ВК-15 |
2,5–3 |
На рис. 1.7 представлены общая схема формирования параметров шероховатости поверхности и реальный профиль обработанной поверхности.
15
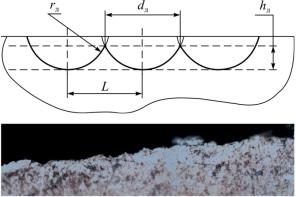
Рис. 1.7. Схема формирования параметров шероховатости
иреальный профиль обработанной поверхности
Сувеличением энергии импульса Wи шероховатость обработанной поверхности возрастает. Это объясняется тем, что с увеличением
Wи будет выделяться большее количество теплоты в течение одного импульса, следовательно, будет наблюдаться большее проплавление металла, что, в свою очередь, приведет к увеличению радиуса лунки
rл и, как следствие, коэффициента перекрытия β. Таким образом, для получения меньших значений параметров шероховатости необходимо правильно подбирать режим обработки.
На рис. 1.8 представлена номограмма режимов и технологических характеристик при обработке стали 45 медным ЭИ на частоте 400 имп/с (режим по току до 600 А). С использованием номограммы
режим обработки выбирается следующим образом: при расчетной
площади обработки Fр = 100 см2 поднимаются от точки 100 см2 нижней шкалы по вертикали до пересечения с наклонной прямой, затем по горизонтали перемещаются влево до пересечения со шкалой тока
иопределяют Iср = 270 А. Следуя по горизонтали, по правой шкале находим производительность Q = 4300 мм3/мин. На верхней шкале показана высота неровностей Rz, которая для рассматриваемого примера равна 0,5 мм [3].
Условно режимы ЭЭО делят на чистовые, черновые и доводочные, но возможно и другое разделение, например на жесткие, средние, мягкие.
16
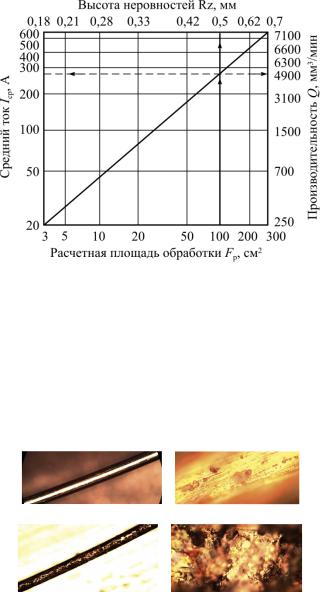
Рис. 1.8. Номограмма режимов и технологических характеристик
Еще одним важным фактором, оказывающим влияние на параметры шероховатости обрабатываемой детали, является износ элек- трода-инструмента.
В работе [12] исследовался процесс изменения свойств ЭД и ЭИ при проволочно-вырезной электроэрозионной обработке. Установлено, что с увеличением средней силы тока (следовательно, и увеличением Wи) при обработке стали 40Х происходит разрушение электрода-инструмента (рис. 1.9), чтосущественнымобразомотражаетсянавеличинеRz.
а
б
Рис. 1.9. Разрушение электрода-инструмента: а – новый ЭИ (×100, ×1000); б – ЭИ после черновой обработки (×100, ×1000)
17
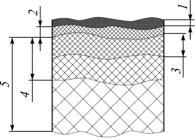
Изученные параметры для каждого материала не являются постоянными и изменяются в пределах исследуемых режимов обработки в большей или меньшей степени.
1.5. Структура и свойства поверхностного слоя обработанной поверхности
после электроэрозионной обработки
Как установлено многими исследователями, свойства поверхностного слоя существенно изменяются в результате ЭЭО [3, 5, 10]. Однако в полной мере свойства этого слоя не определены. Для удобства изучения исследователи разбивают этот слой на зоны. Одни ученые делят его на белый слой и зону термического влияния, другие выделяют в нем несколько зон с различной структурой, третьи отмечают, что он состоит из расплавленного слоя, зоны, подвергшейся химическому воздействию, зоны макродеформации, зоны микродеформации и т.д. [10].
На основе изложенного представляется возможным условное разделение поверхностного слоя после ЭЭО по толщине на следующие зоны (рис. 1.10) [12]: 1 – зону насыщения элементами рабочей
жидкости; 2 – зону отложения ма- |
|
|
териала ЭИ; 3 – белый слой, обра- |
|
|
зованный из расплавленного ма- |
|
|
териала ЭД; 4 – зону термическо- |
|
|
го влияния; 5 – зону пластической |
|
|
деформации. Последовательность |
|
|
образования зон, их количество, |
|
|
структура и свойства в значитель- |
|
|
ной мере зависят от обрабатывае- |
Рис. 1.10. Схематическое |
|
мого материала, а также от режи- |
||
расположение зон поверхностного |
||
ма обработки, применяемой РЖ, |
||
материала ЭИ и условий ведения |
слоя после ЭЭО |
|
|
||
процесса. Между зонами, как |
правило, нет четкой разницы, |
а в большинстве случаев они перекрывают друг друга. Вместе с тем каждая из перечисленных зон имеет свои особенности, влияющие на те или иные свойства поверхности и во многих случаях определяющие возможность успешной эксплуатации детали. При этом каждая зона, даже незначительной толщины, играет важную роль [10].
18
1.5.1. Зона насыщения элементами рабочей жидкости
Зона насыщения элементами рабочей жидкости (зона 1, см. рис. 1.10) определяется тем, что вследствие мощного теплового воздействия при выделении электрической энергии в процессе ЭЭО рабочая жидкость разлагается. Отдельные ее элементы проникают в поверхностный слой заготовки, диффундируют в него и образуют с обрабатываемым материалом химические соединения. Замечено отложение углерода в виде сажи на поверхности заготовки, обрабатываемой электроэрозионным способом на ряде режимов. Углерод образовывался в результате разложения минерального масла, используемого в качестве РЖ. Это, наряду с другими явлениями, приводило в процессе ЭЭО на ряде режимов к шлакованию МЭЗ, что нарушало стабильность процесса. Кроме того, углерод диффундировал в поверхностный слой, образуя карбиды [10].
При ЭЭО в смеси воды с индустриальным маслом 12 на обрабатываемых поверхностях образцов также отлагаются продукты разложения используемой РЖ в виде темных пятен. Эти пятна легко удаляются с поверхности.
Вследствие хрупкости и неравномерной плотности в ряде случаев поверхностный слой может быть дефектным. Он снижает прочностные свойства основного металла, так как при механических, особенно знакопеременных, нагрузках в нем легко возникают трещины, которые могут распространяться в глубь детали. В связи с этим при изготовлении деталей, предназначенных для работы с большими нагрузками, обычно приходится удалять измененный слой одним из способов отделочной обработки или использовать наиболее современные ЭЭ технологии и соответствующее оборудование [3].
1.5.2. Зона отложения материала электрода-инструмента
Образование второй зоны (см. рис. 1.10), которая характеризуется присутствием материала ЭИ, связано с переносом части энергии на заготовку факелами, состоящими из паров материала ЭИ. Материал ЭИ может не только концентрироваться на поверхности заготов-
19
ки, но и диффундировать в более глубокие слои, например в слой расплавленного материала заготовки, и образовывать там различные фазы – твердые растворы, соединения и т.п.
В работе [12] исследовалось изменение химического состава поверхностного слоя стальной заготовки после ее обработки на прово- лочно-вырезном электроэрозионном станке при разных режимах (I – чистовой, II – получистовой, III – черновой). В качестве электро- да-инструмента была выбрана латунная проволока. В табл. 1.2 представлены данные по изменению химического состава поверхностного слоя новой и обработанной заготовок.
Таблица 1 . 2
Химический |
|
Образец |
|
|
состав* |
Новый |
Режим I |
Режим II |
Режим III |
Cr, % |
1,1 |
1,0 |
1,0 |
1,1 |
Mn, % |
0,8 |
0,6 |
0,6 |
0,6 |
Si, % |
0,3 |
0,3 |
0,3 |
0,3 |
Cu, % |
0,2 |
3,6 |
3,7 |
7,3 |
Ni, % |
0,1 |
0,1 |
0,1 |
0,1 |
Zn, % |
0 |
6,1 |
4,8 |
4,8 |
* Основа – Fe. |
|
|
|
|
Как видно из табл. 1.2, стальные детали можно насыщать не только медью, но и другими элементами, содержащимися в электро- де-инструменте.
При обработке стальных деталей электродом-инструментом из графитизированного материала марок ЭЭГ и МПГ и других углеграфитовых композиций углерод, диффундируя в глубь обрабатываемой поверхности, обусловливает образование карбидов.
Образование зоны проникновения металла существенно влияет на свойства поверхностного слоя, а следовательно, на эксплуатационные свойства изготавливаемых деталей.
1.5.3. Белый слой
Толщина белого слоя (зона 3, см. рис. 1.10) металла зависит от величин Wи и tи, а также от температуропроводности материала заготовки. После удаления микропорции металла на поверхности заготовки появ-
20