
книги / Плавка цветных металлов
..pdfВопросы для самоконтроля
1.Как взаимодействует магний и его сплавы с газами печной атмосферы?
2.Чем характеризуется окисление магния?
3.В каких тиглях плавят магниевые сплавы?
4.Какие флюсы используют для защиты от окисления?
5.Для чего вводят компоненты-утяжелители во флюсы?
6.Каково назначение промывочных флюсов?
7.Какие защитные атмосферы применяют при плавке?
8.Для чего в магниевые сплавы вводят бериллий?
9.Почему при плавке сплавов с РЗМ рекомендуются бесхлоридные флюсы?
10.Какие газы можно использовать для плавки под защитными атмосферами?
11.Что собой представляет элегаз?
12.Как рафинируют магниевые сплавы?
13.Как проверяют качество рафинирования?
14.Как модифицируют магниевые сплавы?
15.В чем механизм модифицирования перегревом?
16.Чем устраняют очаги горения магниевых расплавов?
101
5. ПЛАВКА ТИТАНОВЫХ СПЛАВОВ
Освоение технологии плавки титановых сплавов имело наибольшие трудности по сравнению с освоением всех других литейных материалов. Это связано с высокой химической активностью титана. Долгое время отливки из титана получали только в лабораториях отраслевых институтов. В настоящее время все трудности преодолены и на ряде машиностроительных заводов успешно действуют участки фасонного титанового литья, оснащенные современным плавильно-заливочным оборудованием.
5.1. Физико-химические особенности плавки титановых сплавов
Титан активно взаимодействует со всеми газами – кислородом, азотом, водородом и др.
При взаимодействии с кислородом на поверхности титана образуется плотный слой оксида TiO2, который при значениях температуры ниже 500 °С защищает металл от дальнейшего окисления. При нагреве на воздухе кислород диффундирует внутрь и под слоем TiO2 появляется рыхлая прослойка из смеси TiO2 и TiO, а под ними слой, насыщенный кислородом. Кислород повышает стабильность α-фазы, поэтому этот слой называют альфированным. В расплавленном титане кислород растворяется, а при кристаллизации переходит в твердый раствор. Растворенный кислород увеличивает прочность и твердость титана, но резко снижает пластичность и ударную вязкость. В связи с этим содержание кислорода в титановых сплавах не должно превышать 0,2 %.
Азот также растворяется в титане и его сплавах. При кристаллизации азот остается в твердом растворе и образует нитрид TiN, снижающий пластичность. Влияние азота на механические свойства сплава проявляется в большей степени, чем влияние кислорода (табл. 16), и его содержание в сплаве не должно превы-
шать 0,05 %.
102

Растворимость водорода в титане исключительно велика. В отличие от других металлов, составляющих основу промышленных сплавов, растворимость водорода в титане уменьшается с ростом температуры от 7000 см3/100 г при комнатной до 400–150 см3/100 г в расплаве, перегретом на 50–100 °С. Часть водорода удаляется при плавке. Оставшийся водород стабилизирует α-фазу и охрупчивает сплав. Ввиду этого его содержание не должно превышать 0,015 %. Расплавленный титан взаимодействует с парами воды, углеводородами, СО, СО2 и другими газами [13].
|
|
|
|
|
Таблица 16 |
|
Влияние газов и углерода на механические свойства титана |
||||||
|
|
Влияние на свойство 0,01 % добавки |
|
|||
Свойство |
|
|
||||
O2 |
|
N2 |
H2 |
C |
|
|
|
|
|
||||
σ, МПа |
12,3 |
|
35,0 |
67,2 |
7 |
|
НВ, МПа |
39,0 |
|
59,0 |
109 |
20 |
|
δ, % |
–(1–2) |
|
45,0 |
41 |
– |
|
Суглеродом титан образует карбид TiC. Каждая сотая доля процента углерода повышает предел прочности на 7 МПа и твердость на 20 МПа.
Вторая особенность титана заключается в том, что он в жидком состоянии реагирует со всеми известными огнеупорными материалами и материалами литейных форм. Практически невозможно полностью исключить взаимодействие расплава с плавильным тиглем и литейной формой.
5.2.Гарнисажная плавка титановых сплавов
Сучетом высокой химической активности титана его плавку
иразливку можно вести только в вакуумных печах. Плавильнозаливочные установки включают в себя: вакуумную электродуговую гарнисажную печь, камеру для установки и заливки форм, механизмы загрузки и выгрузки форм, вакуумную систему и источник питания [3]. Источником нагрева служит электрическая дуга. Плавку металла гарнисажным способом ведут в водоохлаждаемом тигле, на
103
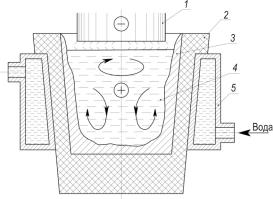
стенках которого намораживается корка твердого металла (гарнисаж), которая изолирует расплав от стенки тигля. Плавку можно вести с расходуемым или нерасходуемым электродом.
При освоении технологии плавки титана предпочтение отдавали тиглям из плотного электродного графита. При всех предосторожностях гарнисажной плавки происходило насыщение металла углеродом. В связи с ужесточением требований к чистоте металла переходят на плавку в медных водоохлаждаемых тиглях, которые позволяют увеличить количество переплавляемых отходов и температуру перегрева сплава, что имеет большое значение при получении тонкостенных крупногабаритных отливок.
Расходуемыми электродами служат слитки одинарного или двойного переплава или кованые прутки заданного химического состава. Нерасходуемые электроды изготовляют из тугоплавких металлов, например вольфрама. Возможно получение расходуемого электрода из отходов, которые режут на мерные заготовки, загружают в цилиндрическую изложницу и заливают жидким сплавом. В итоге получается монолитный электрод, который можно использовать для получения фасонных отливок.
Сущность гарнисажной плавки показана на рис. 25. Перед началом плавки на дно тигля 2 укладывается до 30 % собственных отходов (прибыли, литники и бракованные отливки).
Рис. 25. Схема гарнисажной плавки
104
Между отходами и электродом 1 разжигается электрическая дуга. Торцевая часть электрода расплавляется, и капли жидкого металла стекают в тигель. Плавку ведут до получения необходимого количества расплава 4. Поскольку тигель установлен в медном водоохлаждаемом корпусе 5, на его стенках образуется твердая корочка металла 3, называемая гарнисажем.
В ходе плавки должна строго выдерживаться оптимальная толщина гарнисажа δ (50–60 мм в донной части, 12–16 мм на стенках). В случае ее уменьшения жидкий металл насыщается углеродом. Увеличение толщины приведет к уменьшению массы готового сплава и снижению его температуры. Толщина гарнисажа регулируется мощностью электрической дуги и интенсивностью теплоотвода.
Отходы собственного производства перед загрузкой в тигель подвергаются механической и химической очистке. Механическая очистка производится в галтовочных, дробеструйных или дробеметных барабанах. С поверхности отходов может быть удалено до 0,1 мм поверхностного слоя. После этого отходы обрабатываются
в горячих (130–145 °С) |
щелочных растворах |
следующего |
соста- |
ва, г/л: 600–650 NaOH, |
200–250 NaNO3 и |
50–60 NaNO2 |
или |
500–700 NaOH и 150–250 NaNO3. Время обработки может доходить до 2 ч. Затем отходы промывают теплой и холодной водой и травят при комнатной температуре в кислотном растворе: 60–70 мл/л H2SO4 и 60–140 мл/л HF. Скорость травления 0,2–0,5 мм/ч. Очищенные отходы промывают холодной водой и сушат при 110–150 °С [2].
Некондиционные отходы (сплески, заливы, гарнисаж тиглей, литники с засорами) могут быть использованы при производстве ферротитана или для изготовления таких деталей и изделий, к которым не предъявляются повышенные требования по коррозионной стойкости и механическим свойствам.
Перед загрузкой отходов рабочее пространство печи очищается от пыли и других загрязнений при помощи пылесоса и протирается спиртом. После загрузки отходов печь герметизируется, электрод приваривается к огарку (остатку электрода предыдущей плавки) и начинается плавка.
105
Давление в камере плавильно-заливочной установки должно составлять 0,13–1,33 Па. Для создания вакуума используют мощные вакуумные системы, которые поддерживают в камере заданное разрежение.
5.3. Конструкции плавильно-заливочных установок для плавки титановых сплавов
Процесс плавки и заливки титановых форм осуществляется
водном устройстве – плавильно-заливочной установке (ПЗУ).
Всостав любой ПЗУ входит собственно вакуумная электродуговая гарнисажная печь, источник питания и вакуумная система. Современные ПЗУ снабжены устройствами для загрузки и выгрузки форм.
Питание плавильных печей производится постоянным током, обеспечивающим устойчивое горение дуги. Катодом служит электрод, а анодом ванна жидкого титана. Такая схема называется схемой прямой полярности. Источниками питания являются полупроводниковые выпрямительные устройства, которые выдают постоянный ток силой от 5 до 40 кА с напряжением 75 В.
Конструкция печи зависит от способа разливки металла по формам. По этому признаку все печи делятся на две группы: печи с разливкой металла при горящей дуге (разливка из-под дуги) и печи с разливкой металла после выключения дуги. Различные схемы разливки металла по формам показаны на рис. 26.
Впечах первой группы при сливе металла не происходит охлаждения ванны, что способствует сохранению жидкотекучести расплава и лучшему заполнению литейных форм. Однако эта схема разливки усложняет конструкцию печей и условия их эксплуатации.
Впечах с малым объемом тигля, работающих по схеме с разливкой металла при горящей дуге (см. рис 26, а), узел электрод– тигель и литейная форма жестко связаны с корпусом печи и разливка осуществляется путем ее поворота. В промышленных печах такая схема реализуется путем наклоняющегося узла тигель–электрод внутри неподвижного корпуса или поворотного коробчатого тигля
106
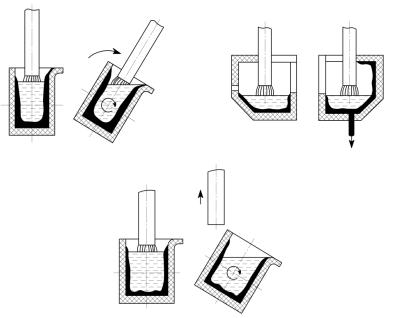
(см. рис. 26, б). В боковой стенке такого тигля расположено сливное отверстие (летка) с таким расчетом, чтобы до него не доходил уровень жидкого металла при плавке. После поворота тигля на 90° летка оказывается внизу, а относительное положение электрода и зеркала ванны не меняется, поэтому дуга может гореть во время слива.
а |
б |
в
Рис. 26. Схемы разливки металла в дуговых гарнисажных печах: а, б – при горящей дуге; в – при отключенной дуге
В печах второй группы, чтобы не препятствовать повороту тигля, остаток электрода поднимается, прерывая горение дуги (см. рис. 26, в). Такиепечиширокораспространенывпромышленности.
На рис. 27 приведена конструкция такой печи типа ВДЛ-1. Расплав после поворота корпуса попадает в литейную форму путем свободной заливки из тигля.
Основные технические характеристики некоторых современных ПЗУ приведены в табл. 17.
107
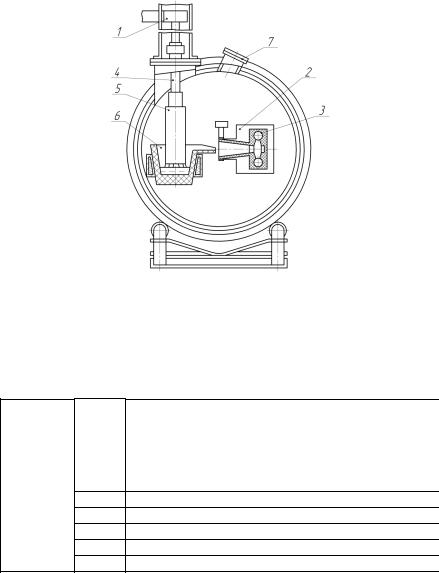
Рис. |
27. Схема гарнисажной печи поворотного |
типа: 1 – токоподвод;. |
2 – |
кожух литейной формы; 3 – форма; 4 |
– электрододержатель; |
5 – электрод; 6 – графитовый тигель; 7 – смотровое окно
Таблица 17 Технические характеристики некоторых гарнисажных ПЗУ
ЕмСила
Тип ПЗУ кость тока тигля, дуги,
кг кА
833Д |
130 |
16 |
ДВЛ-200 |
250 |
25 |
ДВЛ-250 |
400 |
25 |
ДВЛ-250М |
600 |
37,5 |
ДВЛ-160М |
400 |
25 |
Заливочный контейнер |
Габариты, мм |
||||
Количество |
Диаметр, мм |
Высота, мм |
Длина |
Ширина |
Высота |
1 |
1000 |
640 |
7000 |
6500 |
7600 |
1 |
1350 |
1000 |
10 000 |
10000 |
9450 |
2 |
1380 |
1350 |
12 400 |
9700 |
10 200 |
2 |
2200 |
800 |
12 400 |
8700 |
10 200 |
– |
2250 |
1800 |
– |
– |
– |
Для получения тонкостенных отливок в печах использован метод принудительного заполнения форм под действием центробежных сил или дополнительного давления.
108
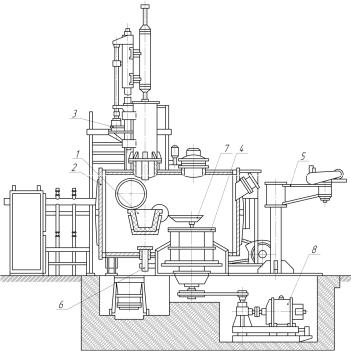
На рис. 28 показана конструкция ПЗУ 833Д. Она предназначена для мелкосерийного производства титановых отливок небольших и средних габаритов.
Рис. 28. Вакуумная плавильно-заливочная установка 833Д
Графитовый водоохлаждаемый тигель 1 расположен внутри цилиндрической вакуумной камеры 2. Механизм подачи электрода 3 состоит из электропривода рабочей подачи и пневмоцилиндра для отброса электрода перед разливкой. Контейнер 4 с литейными формами устанавливают при помощи консольного крана 5 на центробежный стол с бесступенчатым приводом 8. Скорость вращения стола диаметром 1000 мм от 200 до 600 об/мин. Разливка металла производится после выключения дуги поворотом тигля с помощью гидропривода (не показан) вокруг оси, проходящей через сливной носок, по направляющему лотку 7. Краном 5 производится и уста-
109
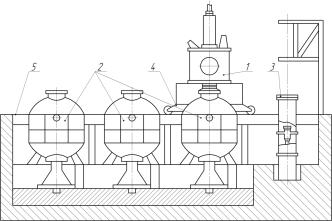
новка нового электрода 6 на позицию приварки к огарку. ПЗУ 833Д является агрегатом периодического действия с продолжительным циклом получения отливок. После заливки форм останавливают центробежный стол, охлаждают в вакууме отливки до температуры 300–400 °С, производят разгерметизацию камеры печи и извлекают контейнер с литейными формами [3].
ПЗУ ДВЛ-160М (рис. 29) отличается более высокой производительностью, так как является многопозиционной. Она состоит из одной плавильной 1, трех заливочных камер 2 и стенда приварки электродов 3. В каждой заливочной камере размещен центробежный стол диаметром 2250 мм.
Рис. 29. Вакуумная плавильно-заливочная установка ДВЛ-160М
Плавильная камера перемещается на тележке 4 над стендом приварки и заливочными камерами по рельсам 5. Стыковка плавильной камеры с заливочными камерами производится при помощи вакуумных затворов. Каждая заливочная камера имеет свою вакуумную систему. Плавка ведется в графитовом тигле емкостью 400 кг. После разливки плавильная камера отсоединяется от заливочной камеры без нарушения в них вакуума и перемещается по рельсам к следующей заливочной камере, подготовленной к заливке [3].
110