
книги / Термоциклическая обработка сталей и чугунов
..pdf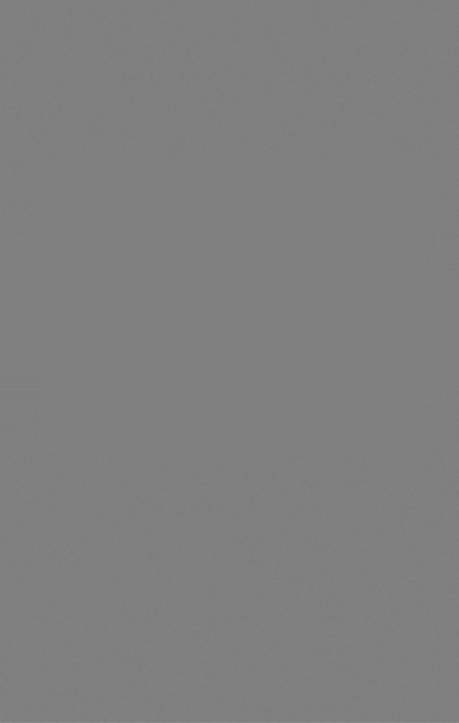
единиц. Не случайно поэтому стойкость резцов из стали типа Р6М5 производства, например Франции, в 1,5 раза превышает стойкость резцов из отечественной стали Р18.
Итак, отжиг после сварки заготовок из быстрорежущих п конструкционных сталей не только требует значительных произ водственных затрат, но и существенно снижает качество гото вой продукции — инструмента. Необходима более совершенная технология предварительной термообработки сварных загото вок инструмента.
§ 5. Способ ускоренного термоциклического отжига сварных заготовок инструмента
Лабораторные исследования показали, что термоциклическая обработка литых сталей РЛ-1 и Р18 мало отличается от ТЦО на сверхмелкое зерно конструкционных сталей 45 и 40Х. По этому первоначально ТЦО сварных заготовок инструмента из сталей Р6М5 и 45 велась с ориентацией на литое состояние стали Р6М5, т. е. по режиму, показавшему удовлетворительные результаты применительно к стали РЛ-1. В дальнейшем, изме няя температуру нагрева и подстуживаиия, а также число тер моциклов (эксперименты проводились в лабораторных усло виях), было установлено, что при использовании скоростного печного нагрева оптимальный режим ТЦО сварных заготовок из сталей Р6М5 и 45 следующий: четырех-пятикратный быст рый нагрев до 800—810° С с последующим охлаждением на воздухе до 600° С; полное охлаждение с последнего нагрева— на спокойном воздухе.
В процессе ТЦО в структуре шва наблюдался распад метастабильных фаз с формированием структуры, аналогичной по
составу той, которая |
получается обычно |
в результате |
отжи |
га — сорбитообразный |
перлит и карбиды |
в стали Р6М5. |
Отли |
чительными особенностями структур сварных швов, прошедших ТЦО, в сравнении с отожженными являются более узкая фер ритная прослойка и более мелкие зерна микроструктуры ста ли 45.
Две партии заготовок, сваренных разными способами — тре нием и электрооплавлением — подвергались термической обра ботке. Половина заготовок (30 шт) прошли отжиг, а вторая часть — ТЦО. Заготовки, сваренные разными способами, име ли после отжига и ТЦО с печным нагревом разные показатели
механических свойств. Результаты |
механических испытаний |
|||
сведены в табл. 11. |
|
|
|
|
Следует отметить, что участок повышенной твердости нахо |
||||
дится |
в быстрорежущей |
части заготовок и его |
толщина около |
|
1 мм. |
При механической |
обработке |
заготовок |
затруднений в |
обрабатываемости не было. Таким образом, лабораторные ис следования показали, что ТЦО сварных заготовок ииструмеи-
62
Т а б л и ц а 11
Механические свойства сварных соединений сталей Р6М5 и 45
|
Термо- |
V |
6 |
'Г |
Мкруч' |
н п с |
Место |
||
Сэлрка |
|
Н |
|||||||
обрабонса |
МПа |
|
м (КГС'М), |
разрушения |
|||||
|
|
(КГС/ММ9) |
|
|
010 мм |
|
|
|
|
|
Отжиг |
635 |
8,5 |
18,0 |
52 (5,2) |
>30 |
По |
сварке |
|
Трением |
|
(63.0) |
|
60,4 |
|
|
|
|
|
ТЦО |
650 |
16,1 |
61 (6,1) |
>35 |
По |
стати |
|||
|
|||||||||
|
|
(65.0) |
|
|
|
|
45 |
||
Оплавле |
Отжиг |
604 |
9,8 |
23,6 |
48 (4,8) |
>30 |
По спарк |
||
ТЦО |
(60,4) |
17,1 |
58,3 |
72 (7,2) |
>35 |
По |
стали |
||
нием |
687 |
||||||||
|
|
(68,7) |
|
|
|
|
45 |
та из сталей Р6М5 и 45 по описанному в данном параграфе режиму дает удовлетворительные результаты. Однако макси мальные значения твердости по Роквеллу (НКС) в зоне шва желательно иметь меньшими. Повышенная твердость в указан
ной |
зоне остается, по-видимому, |
из-за того, что интенсивность |
а |
у-превращений при печном |
нагреве невелика и распад |
структур, подзакаленной при сварке зоны, идет медленно. Не обходимо увеличить скорость нагрева заготовок при ТЦО. Это го можно достичь, используя не печной нагрев, а нагрев в со ляных ванных.
Установлено, что оптимальным режимом ТЦО сварных за готовок инструмента с использованием нагревов в соляной ван не (50% ЫаС1 и 50% ВаС12) является четырехкратный нагрев
заготовок до полного их прогрева в расплаве солей, |
имеющем |
|||
температуру 810±5°С и последующее охлаждение |
на воздухе |
|||
до |
температур |
650—600° С. Охлаждение |
с последнего нагрева |
|
до |
комнатных |
температур — на воздухе. |
При таком |
термоцик- |
лнческом воздействии в материале сварного соединения из бы строрежущей и конструкционной стали восемь раз происходит довольно интенсивное а^у-превращение, что приводит под действием ряда факторов на структуршбразование при уско ренных перекристаллизациях к быстрому распаду ледебуритной эвтектики и подзакаленной структуры в сварных швах. Это резко снижает твердость в месте сварки. Относительно не большая температура нагрева и отсутствие выдержки при на гревах не повышает твердости быстрорежущей части загото
вок.
Длительность термоцикла 3—5 мин для небольших партий заготовок и 15—20 мин для заготовок с общей массой в 100— 120 кг. Продолжительность термоциклической обработки в за висимости от массы термообрабатываемых изделий составляет от 15—20 до 60—100 мин. В сравнении с длительностью обыч-
63
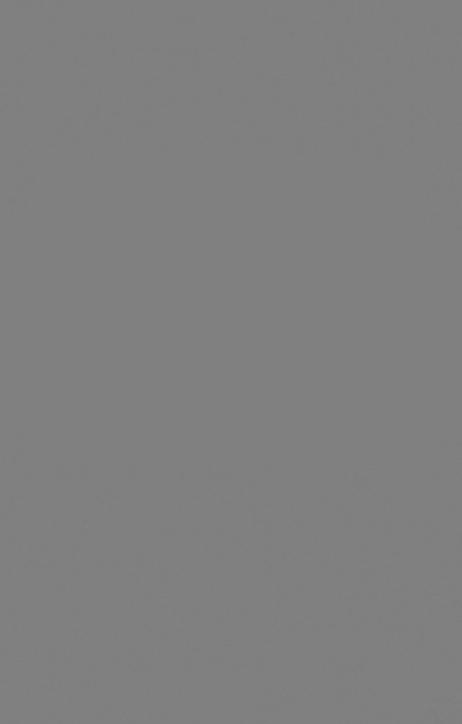
(табл. 12). Инструмент, при из ем
готовлении которого сварной |
шов |
я |
|||||||||
не подвергается |
|
закалке, |
|
обла |
X |
||||||
дает в зоне сварки такими свой |
гг |
||||||||||
ствами, какие приведены в табл. |
Оа |
||||||||||
11, 12. Металлографический ана Н |
|||||||||||
лиз микроструктур сварных швов |
|
||||||||||
и замеры |
микротвердости |
|
пока |
|
|||||||
зывают, что переход от быстро |
|
||||||||||
режущей |
части |
к |
конструкцион |
|
|||||||
ной более |
плавный. |
Сваренные |
|
||||||||
стали в результате ТЦО оказы |
|
||||||||||
ваются |
не разделенными |
|
мало |
5 |
|||||||
прочным ферритом и поэтому в |
Ю |
||||||||||
месте сварки |
нет |
прежней |
|
кон |
а |
||||||
|
|
|
|
|
|
|
|
|
|
|
СО |
центрации |
напряжений |
и дефор |
«в |
||||||||
маций. |
Подтверждением |
этому |
о |
||||||||
ч |
|||||||||||
|
|
|
|
|
|
|
|
|
|
|
«в |
служат |
перенос |
разрушения |
из |
н |
|||||||
о |
|||||||||||
места сварки в зону стали 45 и |
* |
||||||||||
равномерное |
снижение |
микро |
О |
||||||||
|
|
|
|
|
|
|
|
|
|
|
. 5 |
твердости |
при |
замерах |
ее |
|
в |
на |
X |
||||
правлении |
от |
стали |
Р6М5 |
к ста |
X |
||||||
«=* |
|||||||||||
ли 45. |
|
|
|
|
|
|
|
|
|
|
а> |
|
|
|
|
|
|
|
|
|
|
о |
|
Таким |
образом, |
разработан |
о |
||||||||
* |
|||||||||||
ный способ ТЦО приводит к удо |
3 |
||||||||||
влетворительным |
|
микроструктуре |
а |
||||||||
и свойствам |
сварных |
заготовок |
сз |
||||||||
со |
|||||||||||
инструмента, |
что |
позволило |
ре- |
«3 |
|||||||
комендовать |
|
промышлениым |
и |
||||||||
|
н |
||||||||||
предприятиям |
ТЦО |
вместо |
от |
о |
|||||||
* |
|||||||||||
|
|
|
|
|
|
|
|
|
|
|
о |
жига. |
Термоцнклическая |
|
обра |
X |
|||||||
|
и |
||||||||||
ботка, |
выполняющая |
основную |
о |
||||||||
функцию |
обычного |
отжига, |
|
как |
X |
||||||
|
X |
||||||||||
в данном случае, может быть |
|
||||||||||
названа |
термоцпклическнм |
|
от |
|
|||||||
жигом. |
|
|
|
|
|
|
|
|
|
|
|
§ 6. Промышленная технология ТЦО сварных заготовок режущего инструмента
Промышленное |
опробование |
|
и внедрение технологии |
ускорен |
|
ного термоциклического |
отжига |
|
производилось на |
Сестрорецком |
инструментальном заводе им. Бос ова [115]. Одной из главных за
Место разрушения
Ох
а«
X Е
<и
гоО
77
сЗ
с
ьСЗ
сварке |
стали 45 |
сварке |
стали 45 |
По |
По |
По |
По |
о |
С '! |
о |
ю |
со |
СО |
СО |
со |
1 |
1 |
1 |
1 |
1 |
1 |
1 |
1 |
г— |
г— |
Г- |
<м |
С1 |
сч |
сч |
со |
со со со со
с^см‘Оо‘ "т тг ю ю
~ ~ о со |
ГМ СМ СТ; СП |
о с - - * |
СО 0 0 2 0 оо |
о . |
С"-. со |
со 1'-" <м стГ
ЮСМ ю
со. |
со. |
|
с— |
о ». |
|
оо“ |
со" |
|
о " |
ю “ |
|
541 |
(54,1) 570 |
(57.6) |
'—' |
и—ч |
|
—' |
|||||
|
|
|
СО СО. о |
«о |
|
|
|
|
с5 о |
оо оо* |
|
|
|
|
Ю ю ^ |
ю |
|
|
-3* ю ^ |
гг |
оо 00 |
||
СО со' °0 оо" |
СМ О ! О |
О |
|||
со со ^ |
со |
со со |
|
|
О* О
н
Е— |
О н |
|
а> |
|
<и |
|
|=; |
|
а |
си |
га |
<=: |
|
сх, |
п |
Н |
О |
<55
дач производственного опробования способа ТЦО была про верка применимости способа к заготовкам из различных сталей, а также практическая (производственная) оценка обрабаты ваемости резанием термоцнклнчески обработанных заготовок, Термоциклическую обработку заготовок с нагревами в соля ных ваннах первоначально проводили в термическом цехе не большими партиями — по 20—25 шт. вручную. В дальнейшем были изготовлены две промышленные партии сверл (диаметром 12 мм) в 10 000 и 1000 шт. Термоциклическая обработка этих партий заготовок производилась на полуавтоматической линии ТА-32, предназначенной для высокого отпуска сверл после про дольно-винтового проката. ТЦО заготовок на линии ТА-32 про изводилась в корзинах по 150—200 шт. в каждой (масса заго товок —100 кг). Из всех заготовок были изготовлены фрезеро
ванные сверла.
Опыт изготовления инструмента из заготовок, подвергнутых ТЦО вместо отжига, показал, что ТЦО значительно производи тельнее отжига, а обрабатываемость заготовок удовлетворитель ная, так как не вызвала каких-либо затруднений в условиях производства.
Оценка качества готового инструмента, прошедшего ТЦО вместо отжига, производилась не только контролерами ОТК, но и сотрудниками центральной заводской лаборатории завода. Кроме того, эксперименты по определению стойкостных свойств сверл опытно-промышленной партии и аналогичных сверл, изготовленных по существующей технологии (с отжигом), по казали несколько большую твердость и износостойкость. Изве стно, что в исходном состоянии, т. е. перед окончательной тер мической обработкой (закалкой и трехкратным отпуском), твердость НВ стали Р6М5 должна быть не более 2550 МПа, а
структура — сорбитообразиый перлит и |
карбиды |
[38]. При та |
кой микроструктуре стали Р6М5 после |
закалки |
инструмент |
обычно имеет твердость Н Я С = 62-*-64, а последующий тройной отпуск повышает твердость до Н Я С = 65.
Практически металлургические заводы поставляют сталь Р6М5 с более низкой твердостью. Это отрицательно сказыва ется на свойствах готового инструмента, а отжиг после свар ки усугубляет это отрицательное влияние, еще больше снижая твердость быстрорежущей стали. Так, одна партия сварных сверл была изготовлена из стали Р6М5, имевшей в состоянии поставки НВ=2230 МПа=223 кгс/мм2. Заготовки из этой ста ли, сваренные со сталью 45, были подвержены ТЦО так, что нагревались и охлаждались только сварные швы и сталь 45. Часть же заготовок отжигалась по заводской технологии. При отжиге твердость снизилась до НВ=2070-^-2120 М Па=207н- ч-212 кгс/мм2.
Готовый инструмент (сверло), прошедший различную пред варительную термическую обработку, имел и разную твердость.
66
Твердость |
термоциклироваиного инструмента |
была |
НКС = |
||
= 62,7±0,7, |
а у |
прошедшего отжиг |
НЯС = 60,0±1,2. |
Значит |
|
ТЦО повышает |
качество инструмента |
не только |
упрочнением |
сварного шва, н-о и повышением твердости его режущей части. Повышение качества инструмента при замене отжига термоцикличеокой обработкой — один из важных'.показателей эф
фективности ТЦО.
При проведении ТЦО на линии ТА-32 производилось хроно метрирование процесса и другие наблюдения с целью определе ния возможности термоцикличеокой обработки в автоматиче
ском режиме н нахождения технологических |
параметров про |
||||
мышленной |
технологии. В |
табл. |
13 приведена промышленная |
||
|
|
|
|
|
Т а б л и ц а 13 |
Технология ТЦО сварных заготовок режущего инструмента |
|||||
|
|
|
т . |
мин |
|
Операции |
Среда |
'оп* |
|
°с |
|
|
|
|
010—29 мм030—60 мм |
||
Загрузка |
|
_ |
, |
_ |
|
Нагрев |
Расплав |
солей |
8 |
15 |
810*5 |
Охлаждение |
Воздух |
солей |
5 |
8 |
До 650 |
На грев |
Расплав |
3 |
7 |
810-г 5 |
|
Охлаждение |
Воздух |
|
5 |
8 |
До 650 |
Нагрев |
Расплав солей |
3 |
7 |
810+5 |
|
Охлаждение |
Воздух |
|
5 |
8 |
До 650 |
Нагрев |
Расплав солен |
3 |
7 |
8Ю ±5 |
|
Охлаждение |
Воздух |
|
20 |
30 |
До 18-20 |
Выварка |
Вода |
|
30 . |
30 |
8 0 -9 0 |
Промывка |
Вода |
— |
0.2 |
0,2 |
8 0 -9 0 |
Выгрузка |
|
— |
— |
— |
технология термоциклического отжига сварных заготовок инст румента (в корзинах по 150—200 шт.).
Термоциклический отжиг сварных заготовок инструмента з условиях массового производства рекомендуется производить на специальной автоматической линии ТЦО.
Исследования по применению метода термоциклической об работки к сварным заготовкам инструмента позволили сделать следующие выводы:
—оптимальным режимом ТЦО является четырехкратный нагрев в соляной ванне до температуры 810±5°С с последую щим охлаждением на воздухе до 650° С (охлаждение до 20° С с последнего нагрева на воздухе);
—процесс ТЦО может быть автоматизирован;
—ТЦО дает значительное сокращение длительности произ
водственного цикла;
— в результате ТЦО, применяемой вместо отжига, улучша ется качество готовой продукции (инструмента) вследствие
67
упрочнения сварного шва и увеличения твердости режущей ча сти инструмента;
— технология ТЦО позволяет увеличить производитель ность, повысить культуру производства и улучшить условия труда термистов.
Все это позволяет взамен традиционного отжига реко»мендовать к внедрению на заводах, изготавливающих инструмент, технологию термоциклической обработки сварных заготовок режущего инструмента из быстрорежущих и конструкционных сталей. Экономический анализ эффективности внедрения ТЦО сварных заготовок инструмента приведен в гл. IX.
Г ЛАВА V
ВЫСОКОТЕМПЕРАТУРНАЯ ТЕРМОЦИКЛИЧЕСКАЯ ОБРАБОТКА СТАЛЕЙ
§ 1. Циклическая электротермическая обработка (ЦЭТО) углеродистых и низколегированных конструкционных сталей
Способ двойной закалки известен давно. |
С его помощью |
|||
удается, например, .на стали 40 |
получить |
(То = 3100 |
МПа = |
|
= 310 кгс/.мм2. Однако при такой обработке |
сталь |
не |
облада |
|
ет пластичностью. |
поставлена |
задача |
получения |
|
В работе [59] впервые была |
закалкой большой прочности с сохранением удовлетворитель ной пластичности (1|);>20-г-30%). При использовании много кратной закалки (многократность термического воздействия) п электронагрева был разработан способ циклической электро термической обработки (ЦЭТО) конструкционных сталей [59].
Этот способ заключается в |
электронагреве |
со скоростью |
|||||
50°С/с до температуры .полной |
аустенизации, |
охлаждении |
|||||
воздухом со скоростью |
50°С/е |
до температуры |
наиболее |
бы |
|||
строго изотермического |
распада |
аустенита |
420—450°С |
и |
вы |
||
держки (200 с). По окончании |
выдержки |
производят |
второй, |
третий и последующие циклы изотермических электрозакалок. Последний термоцикл — обычная электрозакалка. Схема ре жима ЦЭТО показана на рис. 37. Термоциклической обработ ке по описанному режиму подвергались проволочные образцы диаметром 2,0 мм и длиной 225 мм. Исследуемые материалы: сталь 40 ХН и сталь 40 ХНМ.
Для проведения ЦЭТО была создана специальная уста новка с электроконтактным нагревом образцов проволоки. Экспериментальные исследования влияния ЦЭТО на механиче
ские свойства сталей |
40 ХН и 40 ХНМ показали, |
что для этих |
сталей при данном |
способе ТЦО п0пт = 2. |
Сопоставление |
характеристик механических свойств сталей, обработанных по режиму ЦЭТО и способом двойной электрозакалки, показало, что максимальное значение прочности при ЦЭТО незначи тельно превышает прочность при двойной закалке, в то время как пластичность увеличивается. Относительное сужение ста
69
ли 40ХН при ЦЭТО иа 30% больше, чем после двойной электрозакалки. В сравнении с «печной закалкой ЦЭТО дает еще более ощутимые преимущества. Предел прочности возра
стает иа 400—500 МПа, т. е. |
иа 40—50 кгс/мм2, а относитель |
ное сужение увеличивается на |
10—40%. Сопоставление свойств, |
получаемых ЦЭТО и ВТМО, позволяет сделать вывод о том, что ЦЭТО значительно повышает механические характеристики стали (как прочности, так и пластичности) в сравнении с обыч ной закалкой независимо от исходного состояния материала.
Только |
ВТМО |
даст |
результаты, |
сопоставимые |
с |
ЦЭТО |
|||||||||
(табл. |
14). |
|
|
|
|
|
|
|
|
|
|
|
|
|
|
Микроструктурный анализ показал, что при ЦЭТО проис |
|||||||||||||||
ходит |
измельчение зерен. Размер зерен |
после |
печной |
за |
|||||||||||
|
|
|
|
|
|
калки |
сталей |
40 |
ХН |
и |
|||||
|
|
|
|
|
|
40 ХНМ |
составляет |
|
17— |
||||||
|
|
|
|
|
|
20 мкм, а после ЦЭТО — |
|||||||||
|
|
|
|
|
|
7—8 мкм. |
|
|
характерис |
||||||
|
|
|
|
|
|
Повышение |
|||||||||
|
|
|
|
|
тик |
прочности |
и |
пластич |
|||||||
|
|
|
|
|
ности |
при |
ЦЭТО |
объясня |
|||||||
|
|
|
|
|
|
ется |
спецификой |
электро- |
|||||||
|
|
|
|
|
нагрева. |
При |
очень |
|
быст |
||||||
|
|
|
|
|
|
ром нагреве |
аустенит |
пер |
|||||||
|
|
|
|
|
воначально |
имеет |
большую |
||||||||
Рис. 37. |
Схема циклической |
электро |
неоднородность |
по |
|
угле |
|||||||||
роду. |
Последующее |
|
|
ох |
|||||||||||
термообработки |
(ЦЭТО) |
лаждение, |
фиксируя |
|
|
эту |
|||||||||
неоднородность, |
|
приводит |
|
|
|||||||||||
|
к |
формированию |
аналогич- |
||||||||||||
ного по лнквационной структуре мартеисита. |
|
Исследования, |
|||||||||||||
выполненные на сталях 40, 40Х, 40ХН |
н |
др. |
|
показали, |
что |
||||||||||
вторым |
фактором, |
улучшающим механические |
|
свойства |
при |
||||||||||
ЦЭТО, |
является |
измельчение |
зерен |
[58]. Одновременно с |
появ- |
||||||||||
|
|
|
|
|
|
|
|
|
|
Та б лица |
14 |
||||
Влияние ЦЭТО и ВТМО на механические свойства сталей |
|
|
|||||||||||||
|
|
|
|
40ХН и 40ХНМ |
|
|
|
|
|
|
|
|
|
||
Сталь |
Пехотное |
|
Окончательная |
|
|
V |
|
|
|
»г. % |
|||||
состояние |
|
обработка |
|
|
|
|
|
||||||||
|
|
|
МПа (кгс/мм*) |
|
|
|
|
||||||||
|
Нормализация |
Печная |
закалка |
|
1900(190) |
|
|
> 3 |
|||||||
|
ЦЭТО |
|
|
|
2400(240) |
|
|
38 |
|||||||
40 X И |
|
|
|
|
|
|
|
|
|||||||
|
|
|
Печная |
закалка |
|
1900.190) |
|
|
> 3 |
||||||
|
Отжиг |
|
|
|
|
|
|||||||||
|
|
. ЦЭТО |
|
|
|
2300(230) |
|
|
48 |
||||||
|
|
|
|
|
|
|
|
||||||||
|
Нормализация |
Печная |
закалка |
|
2000(200) |
|
|
38 |
|||||||
|
ЦЭТО |
|
|
|
2380 (238)' |
|
|
45 |
|||||||
40ХНДГ |
|
|
|
|
|
|
|
|
|||||||
|
|
ВТМО |
|
|
|
2400(240) |
|
|
38 |
||||||
|
Отжиг |
|
|
|
|
|
|
||||||||
|
|
|
ЦЭТО |
|
|
|
2380 (238) |
|
|
45 |
|||||
|
|
|
|
|
|
|
|
|
70