
книги / Менеджмент инноваций управление исследованиями и разработками
..pdfдительное оборудование и на этом получить преимущество перед конкурентами. В отличие от такого западного подхода кайдзен – этофилософияпостепенного, эволюционногосовершенствования.
Цель метода кайдзен – производство без потерь за счет постоянного улучшения и стандартизации производственных действий и процессов.
В японском языке слово «кайдзен» означает непрерывное совершенствование. Исходя из этой стратегии, в процесс совершенствования вовлекаются все – от менеджеров до рабочих, причем ее реализация требует относительно небольших материальных затрат. Философия кайдзен предполагает, что наша жизнь в целом (трудовая, общественная и частная) должна быть ориентирована на постоянное улучшение.
Существуют два подхода к непрерывным улучшениям:
1)создание системы подачи кайдзен-предложений;
2)проведение регулярных кайдзен-мероприятий. Способы подачи предложений может быть различной по
своей форме. На японских предприятиях обычно применяется следующая система. Работник делает предложение по улучшению руководству. Это предложение рассматривается назначенной руководством рабочей группой. Далее эта группа принимает решение – внедрять данное предложение или нет. Затем руководство организует внедрение этого предложения в производственный процесс, а работник поощряется за выдвижение плодотворной идеи. При этом выделяют кайдзен системы и кайдзен процесса. Кайдзен системы или потока ориентирован на поток создания ценности в целом; обычно это зона ответственности менеджеров. Кайдзен процесса ориентирован на отдельные процессы; как правило, это зона ответственности рабочих команд.
Принципы кайдзен:
1. Фокус на клиентах – для компании, использующей кайдзен, важно, чтобы их продукция (услуги) удовлетворяла потребности клиентов.
161
2.Непрерывные изменения – принцип, характеризующий саму суть кайдзен, т.е. непрерывные малые изменения во всех сферах организации – снабжении, производстве, сбыте, личностных взаимоотношениях и т.д.
3.Открытое признание проблем – все проблемы открыто выносятся на обсуждение.
4.Пропаганда открытости – малая степень обособленности между отделами и рабочими местами.
5.Создание рабочих команд – каждый работник становится членом рабочей команды и соответствующего кружка качества.
6.Управление проектами при помощи межфункциональных команд – ни одна команда не будет работать эффективно, если она действует только в одной функциональной группе.
Сэтим принципом тесно связана присущая японскому менеджменту ротация.
7.Формирование «поддерживающих взаимоотношений» – для организации важны не только и не столько финансовые результаты, сколько вовлеченность работников в ее деятельность и хорошие взаимоотношения между работниками, поскольку это приведет организацию к высоким результатам.
8.Развитие по горизонтали (личный опыт должен становиться достоянием всей компании).
9.Развитие самодисциплины – умение контролировать себя и уважать как самого себя, так и других работников и организацию в целом.
10.Самосовершенствование.
11.Информирование каждого сотрудника – весь персонал должен быть полностью информирован о своей компании.
12.Делегирование полномочий каждому сотруднику – передача определенного объема полномочий каждому сотруднику.
13.Управлять – значит начать с планирования и сравнить план с результатом.
14.Анализ происходящего на предприятии и действие на основе фактов.
162
15.Устранение основной причины и предотвращение ре-
цидивов.
16.Встраивание качества в процесс как можно раньше.
17.Стандартизация.
Система Канбан. Система Канбан (Canban – тянущая система, pullsystem) – наиболее распространенная разновидность системы «точно в срок» – система, обеспечивающая организацию непрерывного материального потока при отсутствии запасов: производственные запасы подаются небольшими партиями непосредственно в нужные точки производственного процесса, минуя склад, а готовая продукция сразу отгружается покупателям. Порядок управления производством продукции – обратный: от i-й стадии на (i –1)-й.
В настоящее время наметилась четкая тенденция к росту затрат на хранение запасов, что и стало причиной разработки систем «мгновенного» управления запасами, к которым относится рассматриваемая система Canban, разработанная корпорацией Toyota Motors – одна из первых попыток практического внедрения системы «точно в срок».
Сущность системы Canban состоит в том, что все производственные подразделения предприятия снабжаются материальными ресурсами только в том количестве и к такому сроку, которые необходимы для выполнения заказа. Заказ на готовую продукцию подается на последнюю стадию производственного процесса, где производится расчет требуемого объема незавершенного производства, которое должно поступить с предпоследней стадии. Аналогично, с предпоследней стадии идет запрос на предыдущий этап производства на определенное количество полуфабрикатов. Таким образом, размеры производства на данном участке определяются потребностями следующего производственного участка.
Средством передачи информации в системе Canban являются специальные карточки («canban» в переводе с японского языка – карточка). Применяют два вида карточек: карточки про-
163
изводственного заказа, в которых указывается количество деталей, которое должно быть изготовлено на предшествующей стадии производства. Карточки производственного заказа отправляются с i-й стадии производства на (i –1)-й этап и являются основанием для формирования производственной программы (i –1)-го участка; карточки отбора, в которых указывается количество материальных ресурсов (компонентов, деталей, полуфабрикатов), которое должно быть взято на предшествующем участке обработки (сборки). Карточки отбора показывают количество материальных ресурсов, фактически полученных i-м производственным участком от (i –1)-го. Такие карточки могут циркулировать не только внутри предприятия, использующего систему Canban, но и между ним и его филиалами, а также между сотрудничающими корпорациями.
Предприятия, использующие систему Canban, получают производственные ресурсы ежедневно или даже несколько раз в течение дня, таким образом запасы предприятия могут полностью обновляться 100–300 раз в год или даже чаще, тогда как на предприятии, использующем системы MRP или MAP, – только 10–20 раз в год. Например, в корпорации Toyota Motors на один из производственных участков в 1976 г. ресурсы поставлялись трижды в день, а в 1983 г. – уже каждые несколько минут.
Стремление к снижению запасов становится, кроме того, методом выявления и решения производственных проблем. Накопление запасов и завышенные объемы производства позволяют скрывать частые поломки и остановки оборудования, производственный брак. Поскольку в условиях минимизации запасов производство может быть остановлено из-за брака на предыдущей стадии технологического процесса, то основными требованием системы Canban, кроме требования «ноль запасов», становится требование «ноль дефектов». Систему Canban практически невозможно реализовать без одновременного внедрения комплексной системы управления качеством.
164
Важными элементами системы Canban являются:
♦информационная система, включающая в себя не только карточки, но и производственные, транспортные и снабженческие графики, технологические карты;
♦система регулирования потребности и профессиональной ротации кадров;
♦система всеобщего (TQM) и выборочного (Дзидока) контроля качества продукции;
♦система выравнивания производства.
Основные преимущества системы Canban:
1)короткий производственный цикл, высокая оборачиваемость активов, в том числе запасов;
2)отсутствуют или чрезвычайно низки издержки хранения производственных и товарных запасов;
3)высокое качество продукции на всех стадиях производственного процесса.
Причинно-следственная диаграмма. Причинно-следст-
венная диаграмма – это инструмент, обеспечивающий системный подход к определению фактических причин возникающих проблем.
Цель метода – изучить, отобразить и обеспечить технологию поиска истинных причин рассматриваемой проблемы с целью эффективного их разрешения
Причинно-следственная диаграмма – это ключ к решению возникающих проблем. Диаграмма позволяет в простой и доступной форме систематизировать все потенциальные причины рассматриваемых проблем, выделить из них самые существенные и провести поуровневый поиск первопричины (рис. 4.2).
В соответствии с принципом Парето среди множества потенциальных причин, порождающих проблемы, лишь две-три являются наиболее значимыми. Их поиск и должен быть организован. Для этого осуществляется: сбор и систематизация всех причин, прямо или косвенно влияющих на исследуемую проблему; группировка этих причин по причинно-следственным
165
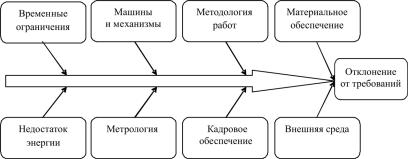
Рис. 4.2. Диаграмма причинно-следственных связей
блокам; ранжирование их внутри каждого блока; анализ получившейся картины.
Достоинства метода: диаграмма позволяет стимулировать творческое мышление, выявить взаимосвязь между причинами и сопоставить их относительную важность.
Недостатки: не рассматривается логическая проверка цепочки причин, ведущих к первопричине, т.е. отсутствуют правила проверки вобратномнаправленииотпервопричиныкрезультатам.
Быстрая переналадка оборудования. Быстрая переналад-
ка оборудования – это один из инструментов совершенствования производства. Создан Сигэо Синго (Япония) в 1970-х гг. В процессе подготовки документов TPS С. Синго ввел для технологии быстрой переналадки оборудования соответствующий термин на японском – сингуру дандори (что дословно означает единичное действие) и на английском– Single Minute Exchange of Die (SMED). Поэтому этот метод управления еще носит назва-
ние Система SMED.
Цель этого метода управления производством – совершенствование производственной деятельности компании за счет сокращения времени переналадки оборудования.
Быстрая переналадка оборудования – это процесс переналадки производственного оборудования при четком понимании различий между внутренними и внешними действиями для пе-
166
рехода от производства одного вида деталей (продукции) к другому за максимально короткое время. Чтобы сократить время переналадки, необходимо не только разделить ее на внутреннюю (когда останавливают оборудование) и внешнюю (производится до останова или после запуска оборудования), но и попытаться преобразовать как можно больше работ по внутренней переналадке во внешнюю. Именно это решение позволяет существенным образом повысить эффективное время использования оборудования путем сокращения его остановов на переналадку.
Система SMED – это совершенно новый способ мышления относительно производства. Система SMED основывается как на теории, так и на многолетней экспериментальной практике. Система SMED представляет собой научный подход к сокращению времени переналадки, который можно применить на любом предприятии и любом оборудовании.
Реализация системы SMED включает в себя:
1.Тщательное изучение и анализ фактических условий на рабочемместе.
2.Разделение действий на внутреннюю и внешнюю переналадку.
3.Преобразование (где это возможно) внутренних действий по переналадке во внешние.
4.Упрощение и упорядочение всех элементарных внутренних и внешних операций переналадки на основе их подробного анализа.
5.Документирование новых процедур и действий. Разработка карты усовершенствования операций.
В случае необходимости (если переналадка занимает более 10 минут) все действия повторяются снова.
Результатом внедрения будет повышение эффективности производства и обеспечение компании конкурентных преимуществ на мировом рынке.
Достоинства метода: сокращение времени простоя оборудования, минимизация запасов, ориентация на производство ма-
167
лыми сериями или под заказ, быстрая адаптация к изменениям спроса. Недостатки метода: требует долгосрочной дисциплины и значительных управленческих навыков в области перемен. Частота и длительность пробных прогонов и корректировки зависит от квалификации инженера-наладчика. Быстрая переналадка оборудования – один из основных инструментов производственной системы Тойота (TPS).
Вопросы для самоконтроля
1.Выявить отличительные особенности методов психологической активизации.
2.Назвать методы систематизированного поиска решений.
3.Охарактеризовать лингвистический процессор А.А. Барышникова.
4.Перечислить инструменты концепции «Бережливое производство».
5.Дать описание философии «кайдзен».
168
Глава 5 МЕТОДОЛОГИЯ УПРАВЛЕНИЯ НАУЧНЫМИ ИССЛЕДОВАНИЯМИ
В научной среде существуют два различных понятия: «методология науки» и «методология научного исследования». Мы будем считать эти понятия синонимами, поскольку обычно под «методологией» понимается учение о способах и методах какой-либо деятельности. А научная деятельность (деятельность каждого исследователя или коллектива ученых) всегда осуществляется по конкретным завершенным циклам – исследованиям или научным проектам: ученый проектирует исследование, осуществляет его и оценивает полученные результаты (рефлексирует), а завершив очередной цикл, приступает к следующему проекту – к следующему исследованию [22]. Поэтому под «методологией науки» в действительности надо понимать учение о способах и методах научного исследования.
Говоря об особенностях научной деятельности, необходимо различать индивидуальную научную деятельность – как процесс научной работы отдельного исследователя – и коллективную научную деятельность – как деятельность всего сообщества ученых, работающих в данной отрасли науки, или как работу научного коллектива исследовательского института, научных групп, научных школ и т.д. Они различны.
Особенности индивидуальной научной деятельности:
1. Научный работник должен четко ограничивать рамки своей деятельности и определять цели своей научной работы. В науке, так же как и в любой другой области профессиональной деятельности, происходит естественное разделение труда. Научный работник не может заниматься «наукой вообще», а должен вычленить четкое направление работы, поставить кон-
169
кретную цель и последовательно идти к ее достижению. Одним из главных качеств научного работника является способность сосредоточиться только на той проблеме, которой он занимается, а все остальные – «побочные» – использовать только в той мере и на том уровне, как они описаны в имеющейся на сегодняшний день научной литературе.
2.Научная работа строится на предшествующих достижениях в данной области исследований.
3.Научный работник должен освоить научную терминологию и строго выстроить свой понятийный аппарат. Исследователь должен провести четкую грань между обыденным и научным языком и определить, в каком смысле он использует то или иное понятие.
4.Результат любой научной работы, любого исследования должен быть обязательно оформлен в «письменном» виде (печатном или электронном) – в виде научного отчета, научного доклада, реферата, статьи, книги и т.д. Во-первых, только в письменном виде можно изложить свои идеи и результаты на строго научном языке. Во-вторых, цель любой научной работы – получить
идовести до людей новое научное знание.
Особенности коллективной научной деятельности:
1.В любом коллективном исследовании каждый ученый имеет право на свою собственную точку зрения; в любом научном исследовании не может быть навязывания другим общей единой точки зрения.
2.Коммуникации в науке. Необходимо обговаривать и обсуждать с коллегами свои идеи, полученные факты, теоретические построения, чтобы избежать ошибок и заблуждений.
3.Внедрение результатов исследования – важнейший момент научной деятельности, поскольку конечной целью науки как отрасли народного хозяйства является, естественно, внедрение полученных результатов в практику. Кроме того, далеко не все исследования могут быть внедрены.
170