
книги / Управление качеством руд при добыче
..pdf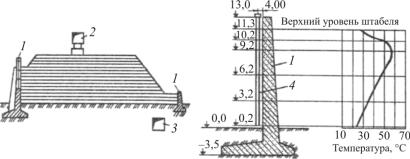
со стороны разгрузочных устройств склада для облегчения разборки штабеля при отгрузке угля.
а |
б |
Рис. 11.22. Склад с подпорной стенкой: а – поперечный разрез штабеля; б – характер изменения температуры по высоте штабеля; 1 – подпорная стенка; 2 – конвейер подачи угля на склад; 3 – конвейер выдачи угля со склада; 4 – измерительная труба
Опыт эксплуатации угольного склада показал, что случаи самовозгорания угля по периметру штабеля полностью прекратились, а зоны наибольшего самонагревания угля с температурой нагрева 58–60 °С переместились в верхнюю часть штабеля и зафиксированы на глубине 2 м от его поверхности (рис. 11.22, б). При этом температура угля у подошвы штабеля оставалась примерно постоянной (20–22 °С) при изменениях температуры окружающего воздуха более чем в два раза.
Отсутствие очагов самовозгорания угля по периметру штабеля в районе подпорных стенок объясняется более качественным уплотнением угольной засыпки при движении бульдозеров вдоль подпорных стенок и отсутствием подсоса воздуха в нижней части штабеля через бетонную стенку.
Предотвращение смерзания угля. При хранении влажного угля на открытых складах в холодное время года возможно смерзание угля в штабеле и дополнительное измельчение его частиц в результате замерзания влаги в микропорах и механического
171
дробления ледоугольного слоя и глыб при погрузочных работах. Неоднократное замораживание и оттаивание угля (особенно бурого) приводит к снижению его механической прочности и потере качества по этому показателю.
Основными способами предотвращения смерзания угля на складах является снижение влажности складируемого угля до 5 %, сепарирование слоев штабеля опилками и добавление в складируемый уголь антифризов.
Вкачестве антифризов, предотвращающих смерзание влажных углей в транспортных средствах, используют каменноугольные и антрацитовые масла и специальные составы «Ниогрин», «Сиверин» и др.
ВСША для борьбы со смерзанием угля в вагонах используют водные растворы хлористого кальция, поставляемого в виде таблеток под названием «Пелладоу» и антикриогенный состав «Формула 1» (смесь крупнозернистого хлористого натрия с антикоррозийным веществом). Ранее в США широко применялась обработка всей массы перевозимого угля минеральными маслами. Угли, обработанные маслом, не смерзаются, не пылят, гидрофобны, имеют большую плотность укладки, большую насыпную массу, меньше окисляются, выветриваются и самовозгораются при хранении. Однако нефтепродукты дороги, дефицитны и токсичны и их применение сокращается.
Антикриогены, содержащие хлор (NaCl, СаС12 и др.), относительно дешевы, но способствуют коррозии металлов при перевозке
ипотреблении и загрязняют окружающую среду при вымывании их атмосферными осадками. Применение хлорсодержащих антикриогенов следуетсогласоватьс потребителями иперевозчикамиугля.
11.8. Перемораживание угля
Одной из складских операций на открытых шахтных складах заполярных шахт является предварительное перемораживание влажных углей, предназначенных к погрузке в железнодорожные
172
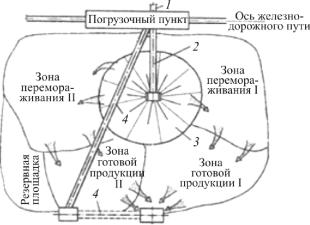
вагоны. Перемораживание угля в холодное время года заменяет сушку углей паром и выполняется на специальных площадках шахтных складов.
Технология перемораживания угля предусматривает следующие операции (рис. 11.23):
–подачу влажного угля от разгрузочного конвейера шахты 1 по эстакаде 2 в первичный конус 3;
–растаскивание влажного угля по площадкам перемораживания бульдозерами;
–замораживание угля под действием атмосферного холода;
–рыхление и перемешивание перемораживаемого угля на площадке перемораживания;
–перемещение перемороженного разрыхленного угля в зону готовой продукции склада;
–возврат готовых продуктов через угольную яму (бункер) и систему передающих конвейеров 4 в бункера погрузочного пункта шахты для погрузки в железнодорожные вагоны.
Рис. 11.23. Схема площадки перемораживания угля перед погрузкой в железнодорожные вагоны (шахта «Северная», ОАО «Воркутауголь»)
173
Перемораживание углей применяют, когда содержание общей влаги в отгружаемом угле превышает допустимую для холодного времени года (табл. 11.1).
Таблица 11.1
Допустимая влажность рассортированных углей при перевозках в холодное время года без проведения профилактических мероприятий, %
Марка угля |
Класс крупности, мм |
|
|
0–6, 6–13, 0–25, 0–100 |
|
13–25 |
|
|
|
||
А |
7 |
|
10 |
Каменные угли всех марок, |
6 |
|
9 |
исключая Г и Д |
|
||
|
|
|
|
Г |
8 |
|
10 |
Д |
12 |
|
14 |
Б |
32 |
|
24 |
Примечания:
1.Уголь крупностью более 25 мм перевозят без применения профилактических мероприятий.
2.Влажность рядовых углей при перевозках без мероприятий не должна превышать 3 %.
В качестве основных недостатков перемораживания угля как способа борьбы с его смерзанием в вагонах назовем следующие:
–оттаивание угля, находящегося в вагонах, в период оттепели с последующим замерзанием при минусовых температурах. Цикл оттаивание – замораживание приводит к смерзанию угля в вагоне и необходимости специального отогревания вагонов в пункте их разгрузки;
–дополнительное измельчение угля в результате разрушения его кусков водой, замерзающей в его порах и трещинах, а также их раздавливания и разрушения гусеницами бульдозеров при перемешивании и дроблении глыб смерзшегося угля на площадке перемораживания.
Таким образом, перемораживание угля применимо только к углям, потребление которых не предъявляет требований к круп-
174
ности его кусков, например, к углям, идущим на коксование или пылевое сжигание.
11.9. Потери массы угля на складе
Потери массы угля при складских операциях и хранении на складе называются естественной убылью угля. Естественная убыль возникает в результате выдувания мелких частиц (пыли) ветром с поверхности штабелей и при погрузке угля и выноса мелких фракций штыба атмосферными осадками. Естественная убыль угля на складах нормируется ГОСТом.
Снижение потерь угля при хранении на открытых складах достигается следующими способами:
1)закреплением поверхности штабеля скрепляющими соста-
вами;
2)размещением штабелей с учетом господствующего направления ветра;
3)переходом на хранение угля на складах с подпорными стенками и на укрытых складах.
В качестве закрепителей поверхностей штабеля могут использоваться акрилатно-лигносульфатный закрепитель (АЛЗ), водобитумные эмульсии, латексные эмульсии и другие отходы заводов нефтяной и химической промышленности, уже обладающие связывающими свойствами и удовлетворяющие требованиям санитарных норм (табл. 11.2).
Латекс СКС-65ГП, предназначенный для закрепления пылящих поверхностей штабелей, должен соответствовать требованиям ГОСТ 10564–75. Латекс СКС-65ГП марки Б выпускается заводами синтетического каучука в виде 40%-ного водного раствора. Нанесение латексных закрепителей на поверхность штабеля осуществляется распылителями, например ДД-30(50), или дальнеструйными дождевальными установками ДНН-100. Радиус действия установок 50–75 и 85 м соответственно. Расход воздуха 15–30 и 115 л/с, давление воды 0,5–0,6 и 0,65 МПа. Удельный расход 5%-ного раствора латекса СКС-65ГП – 1,0–1,5 л/м.
175
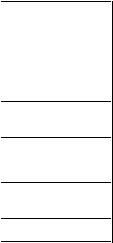
Таблица 11.2
Рекомендуемые покрытия для уменьшения естественной убыли угля на открытых складах
|
|
Толщина пленки |
|
|
|
на штабеле или |
|
Вещества |
Состав |
количествореагента, |
|
|
|
наносимого на 1 м2 |
|
|
|
поверхности |
|
|
|
|
|
Суспензия гашеной извести |
Концентрация 3–4 % |
3 мм |
|
|
|
|
|
Битумно-глинистая паста |
45 % битума марки III, |
2–3 мм |
|
30 % глины и 25 % воды |
|||
|
|
||
|
|
|
|
Битум |
Марка III |
5 мм |
|
|
|
|
|
Дорожная смола |
– |
16 л/м2 |
|
|
|
|
|
Смесь угольной мелочи |
3 % мазута |
25–50 мм |
|
с мазутом или маслами |
и 97 % угольной мелочи |
||
|
|||
|
|
|
|
Водно-мазутная эмульсия |
30–40 % мазутаи70–60 % воды |
2–3 мм |
|
|
|
|
Медленнораспадающаяся 60%-ная битумная эмульсия на сульфитно-спиртовом эмульгаторе изготавливается из битума марки БНД-200/300. Непосредственно на месте производства работ эмульсия разбавляется до 20%-ной и наносится на поверхность штабеля распылительными установками типа ДД-30(50) или ДНН-100. Удельный расход 20%-ного раствора битумной эмульсии 0,5–1,5 л/м.
176
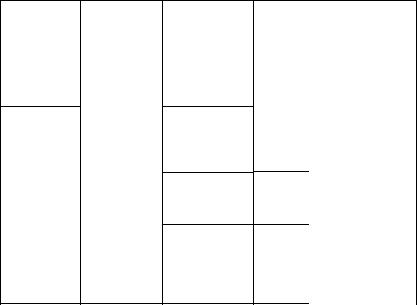
12. СОВРЕМЕННЫЙ УРОВЕНЬ ОСНОВНЫХ ПОКАЗАТЕЛЕЙ КАЧЕСТВА РУД
Универсальных показателей качества, общих для всех полезных ископаемых, нет. Эти показатели могут быть резко различными, даже несопоставимыми для различных видов полезных ископаемых. Например, по каким показателям можно сравнить качество руд золота и каменного угля или стройматериалов и медных руд? Качество полезных ископаемых индивидуализировано в зависимости от типа полезных ископаемых. В этой главе будут рассмотрены качественные признаки наиболее распространенных типов руд.
Таблица 12.1
Основные качественные признаки титановых, никелевых, молибденовых руд и магнезита
|
Назначение |
Основные |
|
|
или отрасль, |
||
|
учитываемые |
||
Руда |
использующая |
||
качественные |
|||
|
полезное |
признаки |
|
|
ископаемое |
||
|
|
||
|
|
Содержание: |
|
Титановая |
|
ильменита |
|
|
|
крутила |
Тип руд: сульфидные мед- но-никелевые с содержанием никеля
Металлургия силикатные никелевые руды с
Никелевые содержанием никеля
Содержание вредныхпримесей:
Fe2O3 + SiO3
MgO
Al2O3
S
Относительный уровень качества, %
Высокий |
Рядовой |
Низкий |
|
|
|
40–50 |
20–30 |
10–20 |
5 |
3–5 |
1,5–3 |
>2 |
1–2 |
0,3–1 |
> 2 |
1,3–2 |
1,1–1,3 |
< 30–35 |
– |
– |
< 2 |
< 5–10 |
< 10–20 |
< 10–12 |
– |
– |
< 12 |
– |
– |
177
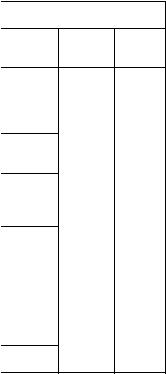
|
Назначение |
Основные |
|
|
или отрасль, |
||
|
учитываемые |
||
Руда |
использующая |
||
качественные |
|||
|
полезное |
признаки |
|
|
ископаемое |
||
|
|
||
Молибденовые |
Металлургия |
СодержаниеМо |
|
в жилах |
и химическая |
|
|
Молибденовые |
Содержаниепо- |
||
промышлен- |
|||
руды |
ность |
путныхкомпонен- |
|
в штокверках |
тов: Cu, Pb, Wo |
||
|
|||
|
Производство |
MgO |
|
|
CaO |
||
|
огнеупоров |
||
|
SiO2 |
||
|
|
||
|
Промышлен- |
|
|
|
ность строи- |
SiO2 |
|
|
тельных мате- |
||
|
|
||
|
риалов |
|
|
|
Абразивная |
|
|
Магнезит |
промышлен- |
MgO |
|
ность |
|
||
|
|
||
|
|
MgO |
|
|
Металлургия |
CaO |
|
|
|
SiO2 |
|
|
Химическая |
|
|
|
промышлен- |
MgO |
|
|
ность |
|
|
|
Пищевая про- |
MgO |
|
|
мышленность |
||
|
|
Окончание табл. 12.1
Относительный уровень качества, %
Высокий Рядовой Низкий
> 1 |
0,5–1 |
0,1–0,5 |
|
|
|
0,3 |
0,1–0,3 |
0,05–0,1 |
45 |
40–44 |
> 40 |
< 1 |
< 1,0–1,2 |
< 1,3 |
< 1,5 |
< 1,5–2,0 |
< 2,6–3 |
– |
– |
– |
|
|
|
– |
– |
– |
> 44 |
|
|
|
|
|
< 2,5 |
– |
– |
< 2 |
|
|
– |
– |
– |
|
|
|
– |
– |
– |
Железные руды. Главный потребитель железных руд (порядка 99 %) – черная металлургия, использующая их для производства чугуна и стали. В относительно малых количествах железная руда применяется в химической промышленности для производства краски, в нефтяной и газовой – в качестве наполнителей глинистых растворов, в цветной металлургии – для производства сплавов, а также в керамической промышленности.
Наиболее ценными являются гематитовые руды (с содержанием железа 55–65 % и более). Ценны также титаномагнетитовые руды, в состав которых кроме железа (25–46 %) входит титан. Содержание вредных элементов – серы и фосфора – в этих рудах обычно незначительно. Богатые руды этих типов,
178
как правило, идут в качестве товарной руды непосредственно на металлургический завод, подвергаясь лишь дроблению, сортировке по крупности и стабилизации.
Бурожелезняковые и сидеритовые руды, содержащие 35–50 %
железа, в основном направляются на обогатительные фабрики для повышения в них концентрации металла, снижения содержания серы и фосфора, улучшения гранулометрического состава и стабилизации качества. Для этого они могут подвергаться на обогатительных фабриках дроблению, измельчению, магнитной сепарации, флотации, обжигу, агломерации, брикетированию, усреднению и другим операциям. Сидериты (содержащие 30–35 % железа) используются обычно совместно с другими типами руд.
Основные вредные компоненты в железных рудах – это сера и фосфор. Даже небольшое содержание серы в металле (0,1 %) делает его красноломким. Для удаления серы в шлак в металлургическую шихту добавляют повышенное количество извести. Но при этом ухудшается режим работы печи, снижается ее производительность. Допускается содержание серы в рудах, предназначенных для непосредственной плавки, до 1,0 %, а для руд, направляемых на агломерацию, до 3 %. Фосфор практически не удаляется при доменном процессе. Наличие фосфора вызывает хладноломкость металла. Допускается в железных рудах, идущих на производство мартеновских и бессемеровских чугунов, содержание фосфора соответственно до 0,15 и 0,03 %. Но при томасовском процессе желательно содержание фосфора в руде в пределах 0,8–1,2 %.
Существенное влияние на переработку железных руд оказывает их гранулометрический состав. Крупнокусковая руда требует предварительного дробления, а мелкая пылеватая – окомкования или гранулирования. При нормальном процессе плавки размеры кусков руды в поперечнике должны быть не выше 120–150 мм для гематитовых руд, 70–100 мм – для магнетитовых, 50 мм – для титаномагнетитовых и 200 м – для бурожелезняковых.
Основные показатели качества железных руд, влияющие на эффективность работы обогатительной фабрики, – это содержа-
179
ние железа, кремнезема и глинозема, текстура, влажность руды, ее гранулометрический состав, а также стабильность этих показателей. Все эти показатели регламентируются для конкретных предприятий (табл. 12.2).
|
|
|
|
Таблица 12.2 |
Основные показатели качества железной руды |
||||
|
|
|
|
|
Назначение |
Основные |
Относительный уровень качества |
||
или отрасль, |
|
|
|
|
учитываемые |
|
|
|
|
использую- |
качественные |
Высокий |
Рядовой |
Низкий |
щая полезное |
||||
ископаемое |
признаки |
|
|
|
|
|
|
|
|
Металлургия |
Содержание |
Содержание |
Содержание желе- |
Бедные |
|
железа, состав |
железа бо- |
за 35–55 %. Руда, |
(ссодержанием |
|
шлакообразую- |
лее 55 %, |
не нуждающаяся в |
железаменее |
|
щих добавок, |
вредные |
обогащении, бо- |
35 %) итрудно- |
|
вредных приме- |
примеси в |
лее бедная, но |
обогатимые |
|
сей серы и фос- |
пределах |
легкообогатимая |
|
|
форов, стабиль- |
нормы |
и самофлюсую- |
|
|
ность показате- |
|
щаяся, с содержа- |
|
|
лей качества |
|
нием примесей в |
|
|
|
|
пределах нормы |
|
Марганцевые руды используются в черной и цветной металлургии при производстве ферромарганца, зеркального чугуна, силикомарганца, сплавов цветных металлов и специальных сталей. При плавке металла марганец оказывает легирующее действие на сталь, в результате чего улучшаются ее физические свойства (прочность, твердость, вязкость). Кроме того, при плавке чугуна или стали марганец вызывает разжижение шлака, способствует удалению серы из металла, предохраняет его от чрезмерного окисления, благоприятствует течению реакций металлургического процесса. Сплавы цветных металлов, имеющие в своем составе марганец, обладают антикоррозийной устойчивостью.
Выделяют следующие типы марганцевых руд:
–окисные, содержащие 19–40 % марганца, 4–5 % кремнезема, 0,1–0,3 % фосфора и 5–24 % окиси кальция;
–карбонатные, с содержанием 10–30 % марганца;
180