
книги / Оборудование для подготовки материалов
..pdf
Под действием внешних сил энергия, сообщаемая дробимому телу, нарастает до критической, при которой наступает нарушение межчастичных связей и, как следствие, разрушение тела. Если объем измельчаемого тела невелик и при разрушении интенсивно образуются новые поверхности (измельчение в мельницах), можно пренебречь вторым членом уравнения обобщенного закона. Тогда работа, затрачиваемая на разрушение, может быть определена по формуле Α= σпов∆F.
Если же степень измельчения невелика, а объем разрушаемого тела достаточно большой, можно пренебречь первым членом уравнения. Тогда
Α= σ 2 ∆ V . 2Ε 1
Каждая операция доведения материала до заданной крупности в отдельной дробильной машине называется стадией дробления. В зависимости от крупности дробления определяют тип применяемой дробилки и количество стадий дробления.
1.1.2.1. Дробилки
1.1.2.1.1. Щековые дробилки
По характеру качания подвижной щеки различают щековые дробилки с простым и сложным качанием. В дробилке с простым качанием щеки (рис. 1.9, а) рабочим органом являются неподвижная и подвижная дробящие плиты, укрепленные на щеках 1 и 2. При качании щеки 2 дробящая плита попеременно приближается и удаляется от неподвижной. При этом материал, находящийся между ними, раздавливается и, продвигаясь вниз под действием силы тяжести, при обратном ходе качающейся щеки выгружается из дробилки через выходную щель.
Качание щеки происходит при помощи шарнирнорычажного механизма, состоящего из эксцентрикового вала 3, шатуна 4 и двух распорных плит 5 и 6. При вращении эксцентрикового вала шатун воздействует на распорные плиты, изме-
21
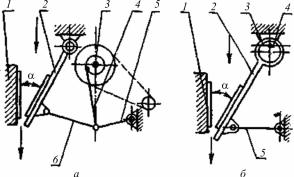
няя угол их наклона и вызывая качание щеки. По концам главного вала насажены маховики, один из которых служит шкивом клиноременной передачи.
В дробилках со сложным качанием (рис. 1.9, б) качающаяся щека 2 вместе с закрепленной на ней сменной дробящей плитой подвешена на эксцентрике 3 главного вала 4 и, таким образом, является одновременно главным шатуном. В нижней части качающаяся щека шарнирно поддерживается распорной плитой 5. Траектории точек щеки в верхней части близки к окружности, в средней имеют форму эллипсов, а в нижней — дуги. Таким образом, здесь материал не только раздавливается, но и частично истирается.
Рис. 1.9. Схемы щековых дробилок: а — с простым качанием щеки; б — со сложным качанием щеки
Рабочее пространство щековой дробилки между качающейся и неподвижной щеками имеет клиновидную форму (рис. 1.10). В него сверху загружают куски материала, а снизу через щель между щеками выпадает продукт дробления. Подвижная щека имеет точку подвеса вверху и качается около нее, нажимая на куски материала и раздавливая их. Щеки обычно делают в виде сменных рифленых плит. При сравнительно небольшом усилии шатуна шарнирный механизм привода обеспечивает большое усилие нажима щеки на раздавливаемый кусок.
22
Угол α между плоскостями щек (рис. 1.11) называется углом захвата щековой дробилки. При качании подвижной щеки уголα , изменяется незначительно. Пренебрегая в первом приближении этим изменением, найдем, каким должен быть уголα , чтобы раздавливаемый кусок материала смог удержаться в выпускной щели дробилки силами трения Pf и P1f, не выталкиваясь из нее кверху. Пренебрегая силой тяжести куска, имеем следующие условия равновесия куска:
Σ Χ= |
Ρ1− Ρf sinα − |
|
Ρcosα = |
0; |
||
Σ Χ= |
P sinα − |
Ρ1 −f |
|
Ρf cosα = |
0, |
|
откуда находим |
|
|
|
|
|
|
|
tg α = |
|
2 tg ϕ |
|
= tg 2ϕ , |
|
|
|
− tg2 ϕ |
|
|
||
|
1 |
|
|
|
где f — коэффициент трения; ϕ — угол трения;
ϕ = arctg f .
Очевидно, что для захватывания кусков материала дробилкой должно быть соблюдено условие
α ≤ 2ϕ ,
т. е. угол захвата должен быть меньше двойного угла трения. Оптимальную частоту вращения вала щековой дробилки
получим из условия, что во время отхода подвижной щеки от неподвижной продукт дробления успевает свободно выпасть через выпускную щель. Угол α также для упрощения принимаем постоянным (рис. 1.12).
При отходе подвижной щеки должен успеть выпасть из
дробилки кусок материала в виде призмы высотойh = |
s |
, где |
|
tg α |
|||
|
|
s — ход щеки, м. Для этого имеется время отхода щеки, равное
23
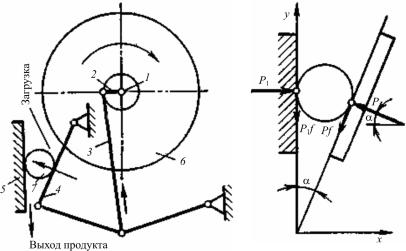
продолжительности полуоборота |
вала |
дробилкиt = |
30 |
с. При |
|||||||||
|
|||||||||||||
|
|
|
|
|
|
|
|
|
|
|
|
n |
|
свободном падении тела |
|
|
|
|
|
|
|
|
|
|
|
|
|
h = |
gt2 |
= |
g |
|
30 2 |
= |
9,81 450 |
|
|
|
|||
|
|
|
|
|
|
|
|
, |
|
|
|||
2 |
2 |
|
|
n |
2 |
|
|
||||||
|
|
|
n |
|
|
|
|
|
|
где n — частота вращения вала, об/мин;
g — ускорение силы тяжести, g = 9,81 м/с2.
Рис. 1.10. Кинематическаясхемащековой |
|
Рис. 1.11. Схема |
||
дробилки: 1 — вал; 2 — кривошип; 3 — |
|
к определению угла захвата |
||
шатун; 4 — качающаяся щека; 5 — |
|
|
||
неподвижная щека; 6 — маховик; 7 — кусок |
||||
дробимого материала |
|
|
||
Необходимо, чтобы |
|
|
||
|
9,81 450 |
= |
s |
. |
|
n2 |
tg α |
|
24
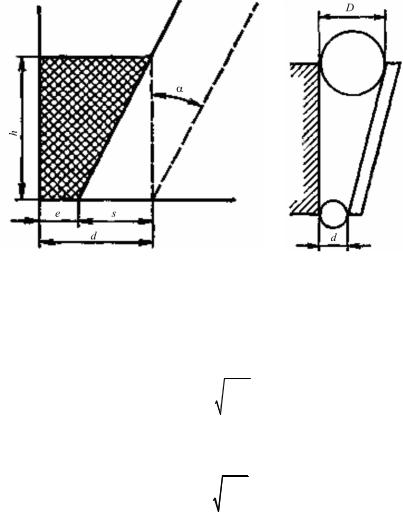
Рис. 1.12. Схема к определению частоты |
Рис. 1.13. Схема |
вращения: е — минимальная ширина выпускной |
к определению работы |
щели; s — ход подвижной щеки; d — |
дробления |
максимальная ширина выпускной щели |
|
Отсюда оптимальная частота вращения, об/мин, вала дробилки
nопт |
= 66,5 |
tg α |
. |
|
|||
|
|
s |
Учитывая трение кусков продукта о щеки, принимаем запас времени высыпания 10 %, тогда
nпракт |
= 60 |
tg α |
. |
|
|||
|
|
s |
Производительность щековой дробилки определится следующим образом. Объем призмы продукта, выпадающего из дробилки за один оборот вала, м3:
V = |
e + (e + s ) |
|
s |
b , |
|
tg α |
|||
2 |
|
|
25
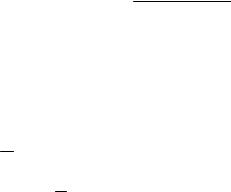
где b — длина выпускной щели дробилки, м. Часовая производительность, т/ч
Q = µV γn 60 = 30µγnbs (2e + s) , tg α
где — коэффициент разрыхления продукта, = 0,25… 0,5; γ — насыпная масса материала, т/м3.
Расход энергии в щековой дробилке найдем исходя из второй гипотезы, приняв наиболее невыгодный случай нагрузки дробилки (рис. 1.13), при котором за один ход дробятся одно-
временно b шаров диаметром D, находящихся на входе, и вы-
D
ходят из дробилки b шаров диаметром d. d
Разность объемов кусков материала до дробления и кусков выходящего продукта в данном приближенном расчете условно берем по объему ряда входящих в дробилку и ряда выходящих из нее кусков:
∆V = |
b |
|
π D3 |
|
− |
bπ d 3 |
=π |
b |
(D2 − d 2 ). |
||||||||
|
|
|
|
|
|
||||||||||||
D 6 |
|
|
|
|
|||||||||||||
|
|
|
d |
|
|
6 |
|
6 |
|
|
|
|
|||||
Работа дробления, кгс·см, при одном ходе, |
|||||||||||||||||
Α= σ2∆ V = |
πσ |
2 |
b(D− |
d |
2 |
) , |
|||||||||||
|
|
|
|
|
|
|
|
|
|
|
2 |
|
|
|
|||
|
|
|
2E |
|
|
|
|
|
|
|
12E |
|
|
|
|
где σ и E — в кгс/см2, a D, d и b — в см. Потребляемая максимальная мощность, л. с.,
N = |
|
An |
= |
σ 2nb(D2− d 2 ) |
. |
|
60 75 |
|
|||
100 |
|
172 104 E |
Усилия по звеньям механизма щековой дробилки при расчете следует определять исходя из работы дробления кусков
26

максимального размера D при наиболее невыгодной загрузке
дробилки, т. е. когда эти куски в количестве b находятся в са-
D
мой верхней части входного отверстия (см. рис. 1.13).
Примем, что в нижнем положении шатуна давление раздавливаемых кусков на подвижную щекуQ = 0, а в верхнем поло-
жении шатуна это давление равно Qmax.
Пусть s0 — ход подвижной щеки в этой точке, см. Приняв для упрощения возрастание силы Q по прямолинейному закону, получим работу дробления
Α= |
0 + Qmax |
s0 |
= |
Qmax s0 |
. |
|
|||
|
|
|
|||||||
|
2 |
|
|
2 |
|
|
|||
Следовательно, максимальная сила, кгс, давления кусков |
|||||||||
материала на щеку |
|
|
|
|
|
|
|
|
|
Qmax = |
|
2 A |
= |
πσ2b(D2 − d 2 ) |
|||||
|
|
|
|
|
. |
||||
|
s0 |
|
|
|
|||||
|
|
|
|
|
6Es0 |
Определив Qmax, легко найдем усилия по всем звеньям механизма. Найденные таким образом усилия следует проверить по мощности электродвигателя и для расчета звеньев на прочность принять большие значения усилий.
Обозначив через P усилие шатуна (в кгс) и приняв для упрощения равномерное возрастание этого усилия от 0 до Pmax, получим работу дробления за один ход, кгс·см:
Α= Ρср 2ε = Ρmax ε ,
где Pср — среднее усилие по шатуну, Pcp = Pmax ; 2
ε— эксцентрицитет коленчатого вала, см.
Сдругой стороны, исходя из мощности N, л. с. получим
27
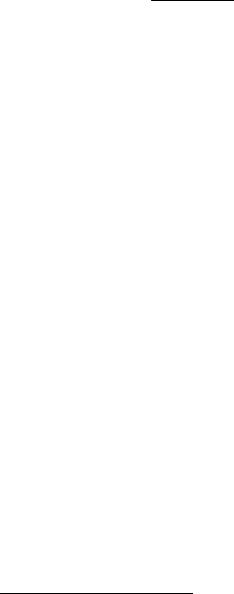
Α= N 75 60 100 кгс·см. n
Из сопоставления этих двух выражений для A получаем
Ρmax |
= 450 |
N |
тс. |
|
|||
|
|
ε n |
Определив усилие по шатуну, легко найти усилия по остальным звеньям механизма.
1.1.2.1.2. Валковые дробилки
Валковая дробилка (рис. 1.14) представляет собой два гладких валка одинакового диаметра, которые вращаются навстречу друг другу с одинаковой частотой вращения. Для хрупких материалов применяют также рифленые и зубчатые валки. Подшипники одного из валков могут проскальзывать в направляющих и удерживаются пружинами. Между подшипниками обоих валков помещают прокладки, которыми регулируют ширину щели между валками. Размер этой щели определяет максимальную величину кусков раздробленного продукта, выходящих из дробилки.
Гладкие валки дробят куски материала, как и щековая дробилка, раздавливанием, затягивая кусок между валками силой трения. Зубчатые валки дробят материал раскалыванием.
Легко видеть, что воображаемые плоскости ОМ и ON (рис. 1.15), касательные к поверхностям гладких валков в точках соприкосновения с затягиваемым куском материала, аналогичны щекам в щековой дробилке. Эти плоскости ОМ и ON образуют между собой угол β = 2α , где α называется углом захвата
валковой дробилки1.
При рассмотрении щековой дробилки было установлено, что для затягивания куска в пространство между щеками долж-
1 В США и Англии углом захвата валковой дробилки называют угол β .
28
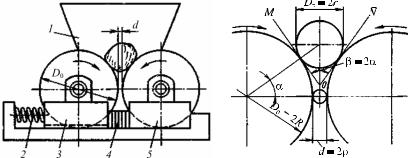
но быть соблюдено условие β ≤ 2ϕ . Отсюда получаем для валковой дробилки α ≤ ϕ , гдеϕ — угол трения материала куска о валки;
ϕ = arctg f .
Рис. 1.14. Схемавалковойдробилки: 1 — |
Рис. 1.15. Схема к выводу |
загрузочная воронка; 2 — пружина; 3 — |
основных соотношений для |
подвижный подшипник; 4 — |
валковой дробилки |
установочные прокладки; 5 — |
|
неподвижный подшипник |
|
Так, для угла f = 0,3 и угол захвата должен бытьα ≤ 16° 42'.
Соотношение между диаметрами валков и поступающих в дробилку максимальных кусков материала определяется по схеме на рис. 1.15 из геометрического соотношения
DB + DK |
cos α = |
DB + d |
, |
|
2 |
2 |
|||
|
|
откуда после преобразований получаем
|
|
cos α − |
1 |
|
|
DB |
= |
e |
, |
||
|
|||||
DK |
1 − cosα |
||||
|
|
29
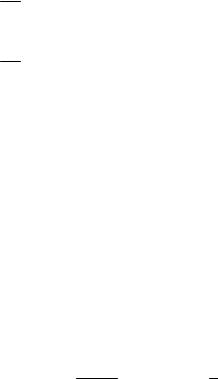
где e = DK — кратность дробления, для гладких валковe = 3… 5 . d
При α = 16° (дробление угля) и e = 4 формула дает отно-
шение DB ≈ 18. Крупные куски по своей форме обычно меньше
DK
приближаются к форме шара и поэтому захват их валками происходит легче. В связи с этим для угля при DK > 50 мм часто
принимают (при гладких валках) |
α = 23° ; |
при DK = 25… 50 мм |
||
α = 19° ; при DK = 12… 25 мм α = |
14,5° . |
|
|
|
Для рифленых валков принимают |
DB |
= 10… 12 , а для зуб- |
||
DK |
||||
|
|
|
чатых валков — 1,5…4. Кратность дробления в дробилках с рифлеными и зубчатыми валками — до 8. Из таких дробилок выходят куски размерами не менее 20 мм.
Определим мощность гладких валков, расходуемую на дробление, исходя из второй гипотезы. При длине образующей валков L изменение объема, см3, при дроблении ряда кусков, захваченных валками (см. рис. 1.15), условно составит
|
L |
π (2r )3 |
L π (ρ2 )3 |
2 |
2 |
|
2 |
|
||||
∆ V= |
|
− |
|
|
|
|
= |
π |
L(r− |
ρ |
|
) . |
2r |
2ρ |
6 |
|
|
||||||||
|
6 |
3 |
|
|
|
|
Работа дробления за один оборот валка, кгс·см,
Α1 = |
σ 2 |
∆ V |
2π R |
, |
|
||||
2E |
|
||||||||
|
|
|
|
2r |
|
|
|
||
или после подстановки |
|
|
|
|
|
|
|
|
|
2 |
2 |
|
2 |
|
2 |
)R |
|
||
Α1 = |
σ π |
|
L(r− ρ |
|
. |
||||
|
|
|
3Er |
|
|
||||
|
|
|
|
|
|
|
|
Потребляемая мощность (без учета трения кусков о валки и трения в подшипниках), л. с.,
30