
книги / Ракетные твердые топлива. Ракетные двигатели на твердом топливе
.pdf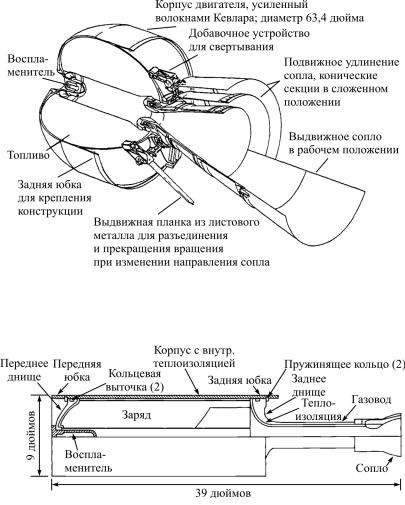
Рис. 6.3. Твердотопливный ракетный двигатель с инерциальной верхней ступенью (inertial upper stage – IUS) с раздвижным выходным конусом (extendible exit cone – EEC)
Рис. 6.4. Упрощенное поперечное сечение типового тактического твердотопливного ракетного двигателя. Газоход позволяет заряду располагаться ближе к центру тяжести летательного аппарата; при работе наблюдается небольшое перемещение центра тяжести. Сопло располагается в задней части ракеты. Кольцевое пространство вокруг газохода обычно заполняется оборудованием систем управления, контроля и другими элементами. Вкладной заряд обычно устанавливается до сборки с задним днищем
231
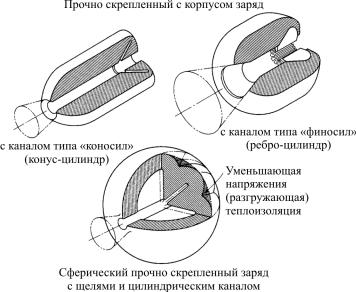
Рис. 6.5. Типичные конфигурации зарядов, использующие комбинации двух основных форм для канала заряда
Комбинированное напряжение не должно превышать рабочее напряжение материала стенки. По мере того как ракетный двигатель начинает работать, внутреннее давление p вызывает увеличение длины камеры, а также ее увеличение по окружности, и эти деформации должны рассматриваться при проектировании опоры двигателя или заряда. Пусть Е – модуль упругости Юнга, – коэффициент Пуассона (0,3 для стали), d – толщина стенки, тогда рост длины L и диаметр D, обусловленный действием давления, составит:
L pLD |
1 2 |
l L 1 2 , |
|||||||
|
4Ed |
|
|
|
|
E |
|
|
|
D |
pD2 |
|
|
|
|
D |
|
|
|
|
1 |
|
1 |
. |
|||||
4Ed |
|||||||||
|
|
|
2 |
|
2E |
|
2 |
232
Для полусферического торца камеры напряжение в каждом из двух направлений под прямыми углами друг к другу равно продольному напряжению цилиндра идентичного радиуса. Для эллиптических днищ локальное напряжение изменяется в зависимости от положения вдоль поверхности, и максимальное напряжение больше максимального напряжения на полусфере. Радиальное перемещение конца цилиндра не является таким же, что
иперемещение полусферических и эллиптических днищ, если рассчитывать их согласно теории тонких оболочек. Таким образом, существует разрыв, который вызывает некоторые сдвиговые
иизгибающие напряжения. Аналогично упор для крепления воспламенителя, установки датчика давления или установки сопла можно сделать с учетом изгибающих или сдвиговых напряжений, которые накладываются на простые растягивающие напряжения корпуса. В этих местах необходимо усиливать или утолщать стенки камеры локально.
Компьютерные программы для анализа напряжений методом конечных элементов существуют и используются компаниями при разработке двигателей в настоящее время для определения конфигурации корпуса с приемлемыми величинами напряжений. Этот анализ должен быть сделан одновременно с анализом напряжения заряда (так как он создает нагрузки на корпус) и с тепловым анализом методом конечных элементов, чтобы определить температурные напряжения и деформации, так как эти анализы являются взаимозависимыми друг от друга.
Быстрый нагрев поверхности внутренней стенки создает температурный градиент и поэтому температурные напряжения через стенку. Теория неустановившейся теплопередачи рассматривалась рядом авторов, и посредством метода релаксации может быть получено допустимое приближение предыстории температура – время в любом месторасположении. Внутренняя стенка корпуса, которая подвергается действию горячего газа, обычно защищается теплоизоляцией. Поэтому теплопередача к корпусу является очень
233
низкой. Фактически для одного единого цикла работы (а не для двух периодов тяги) цель – удерживать температуру корпуса близко к окружающей температуре или максимум выше на 100 °С.
Конструкция корпуса должна включать в себя средства для крепления сопла (редко используется более одного сопла), для крепления корпуса к ракете, установки воспламенителей и приспособления для установки заряда. Иногда также имеются приспособления для крепления аэродинамических поверхностей (стабилизаторов, крыльев, приборов обнаружения, внешних коробок для электрических проводов, захватов для обращения, приводных устройств для управления вектором тяги с их источником энергии). Для верхних ступеней баллистических ракет корпус должен также включать вышибные отверстия для прекращения действия тяги. Типичными деталями для крепления являются конусообразные или прямые пальцы или штыри, выдвижные кольца или болты. Манжеты и/или уплотнительные кольца предотвращают утечку газа.
6.1.2. Металлические корпуса
Металлические корпуса имеют несколько преимуществ по сравнению с корпусами из композиционных материалов: они прочные и могут выдержать сильное механическое воздействие (характерно для многих ракет тактического назначения), являются довольно упругими и могут показывать текучесть металла до разрушения, подвергаться действию высоких температур (от 100 до 1000 °С или от 1292 до 1832 °F и даже более высоких температур при применении специальных материалов) и, таким образом, требуют меньшей теплоизоляции. Они не будут значительно изменять свои свойства во времени или при выдержке в различных погодных условиях и легко воспринимают сконцентрированные нагрузки, если делаются большей толщины на фланце или выступе. Так как металлический корпус имеет намного более высокую плотность и теплоизоляцию меньшей толщины, то он занимает
234
меньший объем, чем корпус из композиционного материала, поэтому для одной и той же внешней оболочки этот корпус может вмещать несколько больше топлива.
На рис. 6.6 показаны различные секции типичных больших корпусов для твердотопливных ракет, сделанных из стали путем сварки. Форма корпуса, в частности отношение длины к диаметру для цилиндрических корпусов, влияет не только на напряжения, которые должен выдержать корпус, но и на количество материала корпуса, требуемого для размещения данного объема твердого топлива.
Для очень больших и длинных двигателей твердотопливный заряд и корпус двигателя делаются секционными: сегменты корпуса механически скрепляются и уплотняются друг с другом на стартовой площадке. Сегментированный твердотопливный ускоритель для «Спейс Шаттл» показан на рис. 6.7. У этого ускорителя суммарный вес топлива 1 106 280 фунт-сила, суммарный вес двигателя 1 255 592 фунт-сила, максимальная тяга в вакууме 3 060 000 фунт-сила, температура от 40 до 120 °F (от 4 до 50 °С), давление в камере сгорания (макс./среднее) 910/662 фунт/дюйм2 (62/45 кг/см2), время работы при 70 °F (120 °С) 123,7 с, длина собранного двигателя 1513 дюйм, диаметр корпуса 146 дюйм, массовая доля топлива (двигат.) 88,2 %, удельный импульс высотный
268,2 с. Топливо: 70 % ПХА, 16 % Al, 14 % PBAN с отвердите-
лем. Скорость горения 0,434 дюйм/с.
Для весьма критического уплотнения между сегментами часто используется множество составных О-образных соединений (рис. 6.8). Сегменты используются в случае, если несегментированный двигатель слишком большой и слишком тяжелый для транспортировки по обычным дорогам (невозможно выполнить повороты) или по железной дороге (не проходит через некоторые тоннели и под некоторыми мостами) и бывает трудным для изготовления.
235
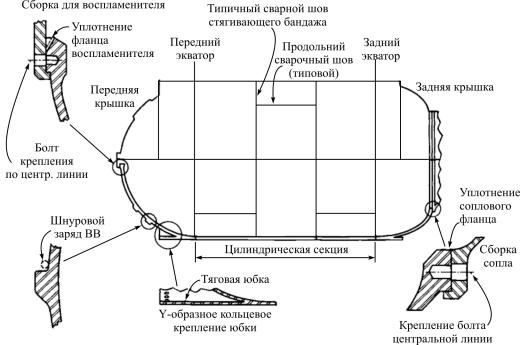
236
Рис. 6.6. Типовой большой корпус твердотопливного двигателя, изготовленный из стали методом сварки
236
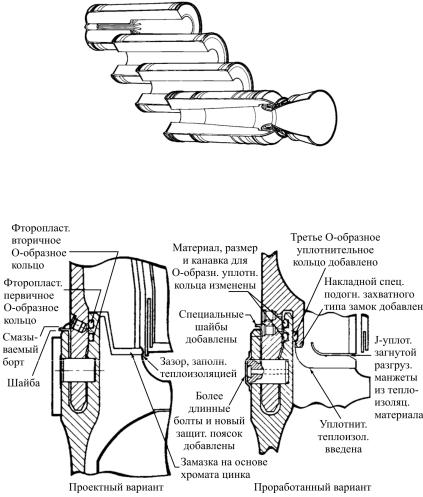
Рис. 6.7. Упрощенная диаграмма четырех сегментов твердотопливного ракетного двигателя «Спейс Шаттл». Детали механизма управления вектором тяги или системы воспламенения не показаны
Рис. 6.8. Проектный и доработанный варианты соединений между сегментами в твердотопливном ускорителе Шаттла (SRB)
Небольшие металлические корпуса для двигателей тактических ракет могут быть получены методом экструзии или путем ковки (и затем механически обработаны) или изготовлены из трех частей, как показано на рис. 6.8. Этот корпус проектировался для вкладного
237
заряда. Корпус, сопло и газоход уплотняются (герметизируются) О-образными соединениями. Так как скорости полета для большинства тактических ракет являются относительно низкими (от 100 до 1500 м/с), их массовые доли топлива также относительно низки (от 0,5 до 0,8) и процент инертной массы двигателя является высоким. Коэффициенты безопасности для корпусов тактических ракет часто бывают довольно высокими, что позволяет с ними грубо обращаться и накопливать повреждения. Поэтому акцент делается при выборе корпусов двигателей (и других его компонентов) не на обеспечение высокого совершенства (самый низкий вес инертной массы двигателя), а на его надежность, длительный срок служебной пригодности, низкую стоимость, прочность или живучесть.
Большинство корпусов изготавливается из высокопрочных сталей, но также используются и другие металлы, подобные алюминию, титану и никелевым сплавам (см. табл. 6.2). В настоящее время многое известно о проектировании и изготовлении корпусов двигателя из сталей (low-alloy) с уровнем прочности до 240 000 фунт/дюйм2 (16 350 кг/см2).
Высокопрочные стали имеют прочности приблизительно до 300 000 фунт/дюйм2 в сочетании с высокой жесткостью при разрушении. Термин «maraging» связан с тем фактом, что эти стали существуют в виде относительно мягких низкоуглеродистых мартенситов в условиях отжига и приобретают высокую прочность при старении при относительно низких температурах.
Стали типа HY (более новые, чем maraging стали) привлекательны из-за их вязкости (жесткости) и сопротивления износу свойства, довольно важного для корпусов двигателя и других сосудов, работающих под давлением, потому что разрушения их являются менее катастрофическими. Эта вязкость или жесткость является характеристикой, которая обеспечивает текучесть до разрушения, по крайней мере, при гидростатических испытаниях на прочность. Стали типа HY имеют прочности между 180 000 и 300 000 Н/см2 (в зависимости от термообработки и добавок).
238
Коррозионное растрескивание под напряжением определенных металлов представляет собой специфическую проблему, которая может приводить к мгновенному разрушению без какого-либо визуального доказательства грозящей катастрофы. Особое внимание должно уделяться тонким металлическим корпусам малого веса, свойства которых ухудшаются из-за коррозии под напряжением и распространения трещин, часто возникающих из-за наличия дефекта на металле, с последующим разрушением, происходящим при уровне напряжений ниже предела текучести.
6.1.3. Корпуса из композиционных материалов
Усиленные нитями корпуса используют непрерывные нити прочных волокон, намотанных вокруг точных форм или моделей и связанных вместе пластиком, обычно эпоксидной смолой. Их основное преимущество заключается в малом весе. Большинство пластиков размягчаются, когда они нагреваются выше 180 °С (или 355 °F); им необходимы вставки или усиления, чтобы обеспечить скрепление или сборку других компонентов и выдержать действие концентрированных нагрузок. Температурное расширение усиленных пластиков часто выше, чем у металла, а удельная теплопроводность намного ниже, вызывая более высокий температурный градиент.
Типичными материалами для увеличения прочности являются стеклянные, арамидные и углеродные (графитовые) волокна (см. табл. 6.2). Обычно инертная масса корпуса, изготовленного из углеволокна, составляет около 50 % массы корпуса, изготовленного из стекловолокна, иоколо 67 % массы корпуса– изволокнаКевлар.
Индивидуальные волокна имеют высокую прочность при рас-
тяжении (2400–6800 МПа, или 350 000–1 000 000 фунт/дюйм2).
Волокна удерживаются на месте с помощью пластикового связующего с относительно низкой плотностью, он предотвращает скольжение волокон и ослабление при сдвиге или изгибе. В намотанных корпусах из композиционных материалов (с действующими кольцевыми, изгибающими и растягивающими напряжениями)
239
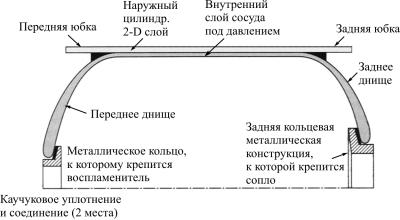
нити не всегда ориентированы вдоль направления действия максимального напряжения, а материал включает в себя пластик с низкой прочностью; поэтому прочность композиционного материала уменьшается в 3–5 раз по сравнению с прочностью самой нити. Полимерное связующее обычно является термореактивной эпоксидной смолой, которая ограничивает максимальную температуру эксплуатации от 100 до 180 °С или от 212 до 355 °F. Хотя имеются смолы с более высокими температурными пределами (295 °C или 563 °F), их адгезия к волокнам не всегда является сильной. Коэффициенты безопасности или запас прочности, которые применяются (в детерминистском структурном анализе) для оценки разрушения, составляют от 1,4 до 1,6 для максимального действующего напряжения, а испытание при проверке прочности корпуса выполняются при создании давления, большего в 1,15– 1,25 раза действующего или рабочего давления.
Типовая конструкция корпуса показана схематично на рис. 6.9. Передний и задний торцы, цилиндрическая часть изготавливаются путем намотки на предварительно подготовленную заготовку или форму, которая уже содержит переднее и заднее кольца.
Рис. 6.9. Упрощенный разрез типовой конструкции намотанного корпуса из композиционного материала
240