
книги / Процессы обработки заготовок. Методы механической обработки поверхностей деталей машин
.pdfдвигателей внутреннего сгорания, коробок скоростей автомашин и станков, предназначенные для передачи с точной согласованностью вращения на повышенных скоростях (прямозубые до 15 м/с, косозубые до 30 м/с) при больших нагрузках, изготавливают по 6-й степени точности. Умеренно нагруженные высокооборотные (прямозубые – до 10 м/с и косозубые – до 15 м/с) изготавливают по 7-й степени точности. Зубчатые колеса общего назначения (например, для станков), не входящие в делительные цепи, зубчатые колеса для сельскохозяйственных машин изготавливают по 8-й степени точности. Слабонагруженные тихоходные зубчатые колеса изготавливают по 9-й степени точности.
Точность зубчатого колеса обозначается трехзначным числом и одной из букв по виду сопряжения. Например, 7-6-6-В или 8-7-6-С. Первая цифра характеризует степень кинематической точности зубчатого колеса, вторая – плавность работы передачи, третья – контакт зубьев, буква – характеризует боковой зазор (С – нулевой, Д – пониженный, Х – нормальный, Ш – повышенный боковой зазор).
Требование получения высокой точности и плавности зацепления зубчатых колес, а также стремление повысить производительность зубонарезания привели к созданию специальных зуборезных станков.
Наиболее распространенными методами нарезания венцов зубчатых колес является зубофрезерование и зубодолбление. При обработке на зубодолбежных станках получается более правильный профиль эвольвенты, чем при зубофрезеровании. Поэтому метод зубодолбления применяется для чистового нарезания зубьев, а метод зубофрезерования двухзаходными и/или трехзаходными фрезами – для чернового нарезания зубьев. На зубофрезерных станках можно нарезать зубчатые венцы шестерен с прямыми и косыми зубьями, червячные зубчатые колеса, червяки, шлицевые валики, цепные колеса.
141
8.1. ОБРАБОТКА ЦИЛИНДРИЧЕСКИХ ЗУБЧАТЫХ КОЛЕС
Нарезание зубьев можно производить методом копирования и методом обката.
8.1.1. Обработка цилиндрических колес методом копирования
Метод копирования заключается в последовательном фрезеровании впадин между зубьями фасонной дисковой модульной фрезой на горизонтальных или универсальных фрезерных станках (в качестве СОЖ применяют эмульсию) при помощи делительных головок, обеспечивая 8–10-ю степень точности. Модульные дисковые фрезы изготавливаются набором из 8 или 15 штук для каждого модуля. Обычно применяют набор фрез из 8 штук, обработка которыми позволяет получать зубчатые колеса 9–10-й степени точности. Для изготовления более точных зубчатых колес (8-й степени точности) требуется набор из 15 фрез. Для получения более высокой степени точности зубчатых колес необходим набор из 24 фрез. Столь большое (от 8 до 24 штук) количество фрез в каждом наборе необходимо потому, что для различного числа зубьев колес размеры впадин между зубьями различны. Каждая фреза набора предназначена для определенного интервала числа зубьев.
Шероховатость поверхности зависит от качества заточки фрез и режимов обработки и, как правило, находится в диапазоне
Ra = 1,5–5,0 мкм.
Зубчатые колеса обычно нарезают по одной (рис. 8.1, а) или по несколько штук на оправке (рис. 8.1, б), что увеличивает производительность обработки за счет уменьшения времени, затрачиваемого на врезание и выход фрезы, а также вспомогательного времени.
Если на шпиндельной оправке расположить две или три фрезы (рис. 8.1, в), каждая из которых будет прорезать впадины зубьев у одной заготовки (группы заготовок), то производитель-
142
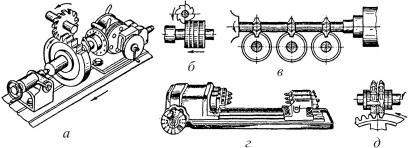
ность будет еще выше. В этом случае применяют многошпиндельные делительные головки (рис. 8.1, г). Применение для этих целей полуавтоматических станков, у которых все вспомогательные движения (подвод заготовок к фрезам, их отвод в исходное положение, поворот заготовок на один зуб и останов станка) совершаются автоматически, также повышает производительность.
Рис. 8.1. Нарезание зубьев зубчатых колес дисковыми модульными фрезами: а – одной заготовки;
б– нескольких заготовок на одной оправке;
в– тремя фрезами одновременно; г – с применением трехшпиндельной головки; д – одновременно двумя модульными фрезами
Значительное повышение производительности достигается применением твердосплавных фрез.
Нарезание зубьев цилиндрических зубчатых колес средних модулей 8–9-й степени точности можно производить двумя дисковыми модульными фрезами (рис. 8.1, д).
Черновое нарезание таких же зубчатых колес средних и крупных модулей осуществляется тремя дисковыми фрезами, но не модульными, а угловыми фрезами (рис. 8.2, а). Черновое нарезание крупномодульных (с модулем более 30 мм) прямозубых колес можно выполнить специальными дисковыми фрезами (рис. 8.2, б), при этом станок должен быть оснащен специальными шпинделями. Одним шпинделем можно фрезеровать отдельно каждую сторону зубьев. Производительность при этом будет
143
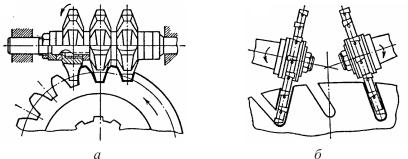
Рис. 8.2. Нарезание зубьев зубчатых колес дисковыми фрезами: а – тремя дисковыми, угловыми фрезами; б – двумя специальными дисковыми фрезами
почти в два раза меньше, но зато можно использовать горизонтальный или универсальный фрезерный станок.
Дисковыми модульными фрезами можно также обрабатывать цилиндрические зубчатые колеса с косым зубом, поворачивая фрезу на угол наклона зуба.
Пальцевыми модульными фрезами нарезают зубья средних и крупных модулей цилиндрических (рис. 8.3, а), шевронных (рис. 8.3, б) зубчатых колес, реек и др.
Обработку производят на вертикальных, горизонтальных или универсальных фрезерных станках (в качестве СОЖ используют эмульсию), обеспечивая 9–11-ю степень точности и шероховатость поверхности Ra = 1,5–2,5 мкм.
Зубья крупных модулей (с модулем более 20 мм) начерно нарезают двухугловой пальцевой фрезой (рис. 8.3, в) или последовательно двумя угловыми пальцевыми фрезами (рис. 8.3, г).
Нарезание цилиндрических зубчатых колес дисковыми модульными фрезами, а также специальными фрезами применяют преимущественно в единичном и мелкосерийном производстве при отсутствии специальных зуборезных станков, так как такой способ нарезания дает сравнительно малую производительность и низкую точность.
144
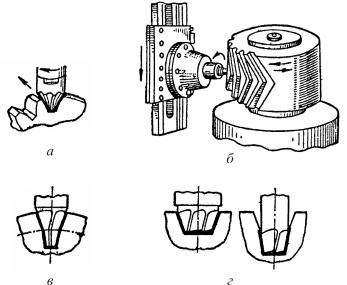
Рис. 8.3. Нарезание зубьев зубчатых колес пальцевыми фрезами: а – прямозубого колеса; б – шевронного колеса;
в– черновое нарезание двуугольной фрезой;
г– последовательно двумя угловыми фрезами
8.1.2.Обработка цилиндрических колес методом обкатки
Зубонарезание на зубофрезерных станках наружных зуб-
чатых колес с прямыми и косыми зубьями, а также червячных колес производится на станках моделей 5Д32, 5Е32 и др. (в качестве СОЖ используется масло типа И-20А) червячными фрезами, обеспечивая 8–9-ю степень точности и шероховатость поверх-
ности Ra = 1,5–2,5 мкм.
Червячные фрезы бывают однозаходными и многозаходными. В процессе нарезания червячная фреза и нарезаемое колесо находятся в состоянии зацепления. Это зацепление соответствует червячной передаче с передаточным числом
145
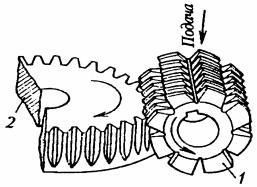
i = nф / nз = zз / k,
где nфи nз – частота вращения фрезы и зубчатого колеса вминуту; k – число заходов червячной фрезы;
zз – число зубьев нарезаемого зубчатого колеса.
Схема нарезания зубьев червячной фрезой представлена на рис. 8.4.
Рис. 8.4. Схема фрезерования зубьев червячной фрезой
Фреза 1 устанавливается под углом подъема зубьев фрезы на делительном цилиндре (на шпинделе зубофрезерного станка). Заготовка 2 получает вращательное движение, а фреза, кроме вращательного движения, имеет еще поступательное движение подачи вдоль образующей поверхности зубчатого колеса.
При нарезании прямозубых цилиндрических колес на станке настраивают три гитары: гитара главного движения, обеспечивающая требуемую скорость резания; гитару осевой подачи, обеспечивающая перемещение фрезерного суппорта за период одного полного поворота зубчатого колеса; гитара обкатки, обеспечивающая равенство скоростей продольного перемещения прямобочной исходной режущей рейки и вращения зубчатого колеса. Для обеспечения обкатки нарезаемого зубчатого колеса по исходной режущей рейке необходимо, чтобы за один оборот фрезы заготовка повернулась на угол, равный отношению числа заходов фрезы к количеству зубьев нарезаемого зубчатого колеса.
146
При обработке зубчатых колес с косыми зубьями настраиваются четыре гитары станка: гитара главного движения, гитара подач, гитара обкатки и гитара дифференциала. Последняя гитара настраивается из условия, что фрезерный суппорт перемещается вдоль оси заготовки на величину шага спирали, обрабатываемого зубчатого колеса за время одного полного оборота заготовки.
При нарезании зубчатых колес с косыми зубьями фрезерный суппорт устанавливается с учетом наклона винтовой линии витков фрезы α и угла спирали зуба зубчатого колеса β.
Если направление наклона винтовой линии фрезы и нарезаемого колеса одинаковы (фреза и зубчатое колесо правозаходные и левозаходные), то угол установки фрезы равен разности углов фрезы и зубчатого колеса, то есть β´ = α – β; если же направление наклона винтовой линии фрезы и зубчатого колеса различно, то угол установки фрезы равен сумме углов фрезы
изубчатого колеса, то есть β´ = α + β.
Взависимости от величины модуля нарезаемого зубчатого колеса устанавливается число проходов фрезы: зубчатое колесо с модулем до 2,5 мм нарезают за один проход – начисто; зубчатое колесо с модулем больше 2,5 мм нарезают за два прохода – начерно и начисто.
Кроме обычной схемы зубофрезерования цилиндрических зубчатых колес, известен метод диагонального зубофрезерования. При этом методе обработка производится при наличии двух подач: продольной – вдоль оси обрабатываемой заготовки и тангенциальной – вдоль оси червячной модульной фрезы.
При такой схеме обработки в резании участвуют все режущие зубья фрезы, что способствует повышению стойкости фрезы. Однако точность обработки при диагональном зубофрезеровании снижается из-за погрешностей в кинематической цепи усложненного механизма фрезерной головки.
При фрезеровании зубьев колес из сталей средней твердости черновые проходы выполняют при скоростях резания 25–30 м/мин,
ачистовые – при 35–40 м/мин. Соответственно продольная пода-
147
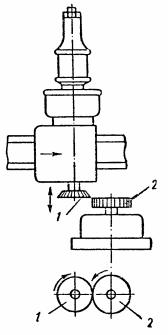
ча фрезы принимается при черновых проходах 1,5–2,0 мм на оборот заготовки и на чистовых проходах – при 0,5–1,0 мм на оборот заготовки. В качестве СОЖ применяют масло.
Нарезание прямых, косых и спиральных (винтовых) зубьев цилиндрических зубчатых колес на зубодолбежных станках отечественных производителей (станки мод. 5А12, 5122, 5122Б, 5122В, 5А14, 5140, 5150, 5А16, 5161) и зарубежных фирм
«Феллоу» (США), «Лоренц» (США) может производиться методом обкатки режущими инструментами – долбяками в виде шестерен (круглые, дисковые долбяки) и в виде гребенок (реек). Долбяками в виде гребенок (реек) можно нарезать зубья колес только наружного зацепления. Долбяками в виде шестерен (круглыми долбяками) можно нарезать зубья колес, как наружного, так
и внутреннего зацепления. |
|
Долбяк, являющийся режущим |
|
инструментом, имеет форму шес- |
|
терни того же модуля, что и наре- |
|
заемое зубчатое колесо. |
|
Способ нарезания цилиндри- |
|
ческого зубчатого колеса методом |
|
обкатки с помощью круглого дол- |
|
бяка заключается в том, что в про- |
|
цессе обработки колеса воспроиз- |
|
водится зубчатое зацепление двух |
|
зубчатых колес, одно из которых |
|
является режущим инструментом |
|
(долбяком), а другое – заготовкой. |
|
Для обработки зубчатого колеса |
|
необходимо (рис. 8.5), чтобы долбяк |
|
1 совершал возвратно-поступатель- |
|
ное движение, как правило, в вер- |
|
тикальной плоскости, в результате |
|
чего на заготовке 2 образуются |
|
зубья. Зубчатая пара, установленная |
Рис. 8.5. Схема обработки |
на зубодолбежном станке, взаимно |
при зубодолблении |
|
148
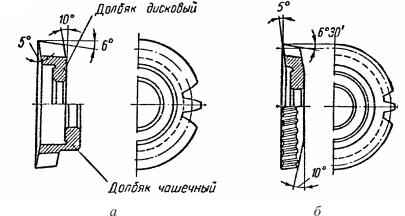
кинематически связана и в процессе обкатки воспроизводит зубчатое зацепление. Колесо 1 (долбяк) служит режущим инструментом и одновременно производит вертикальное возвратнопоступательное движение, последовательно срезая режущими зубьями материал заготовки 2. Долбяк представляет собой зубчатое колесо, на торце которого образованы режущие кромки (рис. 8.6, а). Для нарезания зубчатых колес с винтовым зубом применяется долбяк тоже с винтовым зубом и с тем же углом подъема винтовой линии, что и у нарезаемого зубчатого колеса (рис. 8.6, б); долбяк при обработке зубчатых колес с винтовым зубом получает добавочное вращение по винтовой линии от специального копира, помещающегося в верхней части шпинделя долбяка. Зубодолбление производят за один или несколько ходов, необходимых для нарезания полного профиля зубьев (под ходом при зубодолблении понимается полный оборот заготовки в процессе нарезания). Обработка долбяком за один ход применяется для зубчатых колес с модулем от 1 до 2 мм, за два хода – с модулем от 2,25 до 4 мм и за три хода – при модулях, превышающих 4 мм, а также при меньших модулях, но при повышенных требованиях к точности и шероховатости поверхности.
Рис. 8.6. Виды круглых долбяков
149
Обычно зубчатые колеса средних и крупных модулей предварительно обрабатывают на зубофрезерных станках, а чистовая обработка производится на зубодолбежных станках за один или (реже) два хода.
Предварительное нарезание зубьев средних и крупных модулей на зубофрезерных станках более производительно, чем зубодолбление. При нарезании зубьев с модулем менее 2 мм более производительными иточными являются зубодолбежные станки.
Следует отметить, что быстроходные зубодолбежные станки с числом ходов долбяка от 600 до 700 в минуту обладают достаточно высокой производительностью.
Производительность зубодолбления резко повышается при совмещении чернового и чистового зубонарезания за счет применения комбинированных долбяков. Комбинированные долбяки производят последовательное черновое и чистовое нарезание зубьев за один оборот долбяка. У таких долбяков часть зубьев имеет заниженную толщину. Они выполняют черновое нарезание профилей зубьев, другая часть зубьев удаляет оставшийся припуск при чистовом нарезании. На долбяке предусмотрен участок со срезанными зубьями, который позволяет снимать и устанавливать заготовки без отвода шпинделя с долбяком. Следует отметить, что комбинированные долбяки пригодны для нарезания зубчатых колес только с определенным числом зубьев. Их целесообразно применять только на заводах массового и крупносерийного производства. Комбинированные долбяки пригодны только для нарезания зубчатых колес с малым числом зубьев, так как число зубьев этих долбяков должно быть равно удвоенному числу зубьев нарезаемого зубчатого колеса.
На рис. 8.7 приведены схемы зубодолбления: цилиндрических колес внутреннего зацепления с прямыми зубьями (рис. 8.7, а); цилиндрического зубчатого венца наружного зацепления с прямыми зубьями в блочном зубчатом колесе с двумя венцами разных диаметров (рис. 8.7, б), расстояние между которыми составляет от 4 до 6 мм; цилиндрического зубчатого колеса наружного зацепления с винтовыми зубьями (рис. 8.7, в).
150