
книги / Процессы обработки заготовок. Методы механической обработки поверхностей деталей машин
.pdf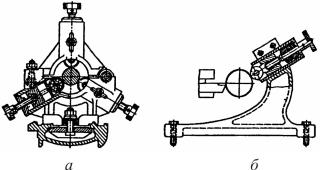
Рис. 2.2. Люнеты: а – с роликовыми опорами; б – подвижный люнет-виброгаситель
Люнеты служат дополнительной опорой, воспринимающей нагрузки. Подвижный люнет, следуя за резцом, воспринимает силу резания. Обрабатываемая поверхность опирается на кулачки люнета. В тех случаях, когда следует обеспечить соосность обтачиваемой поверхности с ранее обработанной, кулачки люнета устанавливают впереди резца, то есть на ранее обработанную поверхность. При скоростном резании кулачки создают значительное трение. Для уменьшения трения применяют люнеты с роликовыми опорами (см. рис. 2.2, а). При скоростном точении часто возникают вибрации, увеличивают шероховатость поверхности и снижают точность обработки. Для устранения вибраций применяют люнеты с виброгасителем (см. рис. 2.2, б). Тарельчатые пружины, помещенные в корпусе виброгасителя, поглощают вибрации резца.
При высоких скоростях резания стружка имеет сливную форму и сходит из-под резца непрерывной лентой. Такая стружка весьма опасна, так как может явиться причиной травматизма (порезов и (или) ожогов). Для размельчения такой стружки применяют специальные устройства – стружколоматели.
В массовом и крупносерийном производствах обработку валов часто производят на многорезцовых станках, которые имеют два суппорта – передний и задний. Передний суппорт,
31
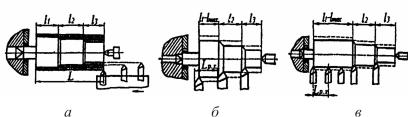
имеющий продольное движение, служит для точения. Задний суппорт, совершающий поперечное движение, предназначен для подрезки торцов и прорезания канавок. Резцы настраивают так, чтобы обработка всех участков заканчивалась одновременно. Многорезцовое обтачивание выполняют тремя способами:
Первый способ – это способ деления общего припуска по глубине. При этом способе припуск на одной из ступеней снимается последовательно несколькими резцами, и передний суппорт совершает путь L, равный сумме обрабатываемых ступеней
L = l1 + l2 + l3 (рис. 2.3, а).
Рис. 2.3. Способы обработки ступенчатого вала на многорезцовом станке: а – способ деления припуска; б – способ деления длины обработки вала; в – способ деления длины максимальной ступени
Второй способ – это способ деления длины заготовки на несколько участков (рис. 2.3, б). Этот способ применяется, когда максимальный припуск может быть удален резцами за один проход. При такой схеме обработки длина хода резца l = L/n (n – количество ступеней).
Третий способ – это способ деления максимальной ступени вала (рис 2.3, в). Более длинная ступень l1 протачивается несколькими резцами, установленными на одинаковую глубину съема.
Установка резцов производится либо по обработанной заготовке, либо по специальному эталону.
Многорезцовую обработку применяют, как правило, на предварительных операциях. Чистовое точение осуществляют на гид-
32
рокопировальных станках 1708, 1Н713, 1Б732 и др., имеющих два суппорта, расположенных в вертикальной плоскости, что позволяет облегчить сход стружки из зоны резания. Точение по копиру осуществляется одним резцом, расположенным на верхнем суппорте. Подрезка торцов осуществляется резцами, расположенными в нижнем суппорте. Точение на многорезцовых станках осуществляется со скоростью резания 30–50 м/мин, а чистовое точение на гидрокопировальных станках – со скоростью резания 150–200 м/мин. В качестве СОЖ обычно применяют эмульсию.
Всерийном и мелкосерийном производствах валы обрабатывают на станках с числовым программным управлением или ручным управлением.
Вединичном производстве обработку валов обычно осуществляют на универсальном оборудовании с ручным управлением.
2.2.ОТДЕЛОЧНАЯ ОБРАБОТКА
Котделочным методам обработки относят тонкое (алмазное) точение, шлифование, притирку, суперфиниш, полирование, алмазное выглаживание и обкатку роликами и шариками.
2.2.1. Тонкое (алмазное) точение
Тонкое (алмазное) точение подробно описано ранее в разделе 2.1.
2.2.2. Шлифование
Шлифование является основным и наиболее распространенным методом обработки наружных цилиндрических поверхностей. Шлифование подразделяют на чистовое и тонкое шлифование. Тонкое шлифование осуществляется шлифовальными кругами или шлифовальными лентами на круглошлифовальных станках с продольной подачей (рис. 2.4) и методом врезания (рис. 2.5), на бесцентрово-шлифовальных станках на проход
33
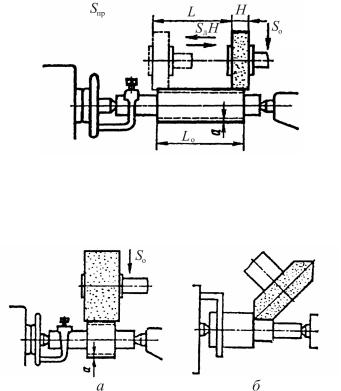
(рис. 2.6) и методом врезания (рис. 2.7), а также на ленточношлифовальных станках. На круглошлифовальном станке заготовка устанавливается в центрах станка. Скорость вращения заготовки составляет 10–15 м/мин, скорость инструментапорядка – 30 м/с.
2.4. Схема круглого шлифования с продольной подачей
Процесс шлифования может осуществляться с продольной подачей (см. рис. 2.4) и методом врезания (см. рис. 2.5).
Рис. 2.5. Схема круглого шлифования: а – методом врезания с поперечной подачей; б – методом одновременного шлифования шейки и уступа вала
В первом случае заготовка совершает возвратно-поступатель- ноепродольноеперемещениеспродольнойподачейSпр= (0,5–0,8) Н (Н – высота круга) за один оборот заготовки, а в конце каждого хода производится поперечная подача (глубиной резания)
0,01–0,03 мм.
34
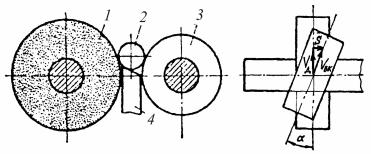
При выхаживающих проходах продольная подача уменьшается до Sпр= (0,2–0,3) Н и глубина резания до 0,005–0,02 мм. Длина продольного хода при шлифовании должна обеспечивать перебег инструмента на сторону, равный (0,2–0,4) Н (Н – высота круга или ширина ленты).
Второй способ заключается в том, что инструменту (шлифовальному кругу или шлифовальной ленте) сообщается только поперечная подача за один оборот заготовки.
Чистовое круглое шлифование в центрах станка обеспечивает точность 5–6-го квалитета и шероховатость поверхности Ra = 0,3–1,25 мкм. Тонкое круглое шлифование в центрах станка обеспечивает точность 3–5 квалитета и шероховатость поверхности Ra = 0,02–0,08 мкм.
При шлифовании на бесцентрово-шлифовальных станках на проход (см. рис. 2.6) заготовку 2 устанавливают между двумя шлифовальными кругами (ведущим кругом 3 и шлифующим кругом 1, обеспечивающим съем материала) на специальный поддерживающий нож 4, изготовленныйизизносостойкого материала.
Рис. 2.6. Схема бесцентрового шлифования на проход
Благодаря скосу, направленному в сторону ведущего круга, деталь прижимается к ведущему кругу, что способствует передаче крутящего момента ведущим кругом детали. Во избежание огранки детали диаметром более 30 мм смещают вверх на 10–15 мм от линии центров шлифовальных кругов.
35
При шлифовании на проход ведущий круг устанавливают под углом α=1–5о.
Величину продольной подачи S при шлифовании на проход назначают в пределах 400–4000 мм/мин. Скорость ведущего круга (ВК) – VВК = 15–30 м/мин при черновом шлифовании. При чистовом шлифовании увеличивают до 100 м/мин и более.
Продольная подача определяется по формуле
S = 1000 VВК sin α ηS ,
окружная скорость вращения детали определяется по формуле
Vд = VВК cos (1 + δ),
где S – продольная подача, мм/мин;
Vд – окружная скорость вращения детали, м/мин;
VВК – окружная скорость ведущего круга, м/мин;
ηS – коэффициент осевого проскальзывания (0,90–0,98);
δ – коэффициент, учитывающий ускоренное вращение изделия за счет скорости шлифующего круга (δ = 0,04–0,07).
Возможно шлифование набором шлифующих кругов разной зернистости, ширина такого круга может достигать 800 мм. Шлифование сборным кругом позволяет за один проход обеспечить обработку по 6–8-му квалитету точности и шероховатость поверхности Ra = 0,16–0,32 мкм.
Бесцентровое шлифование может также осуществляться методом врезания (см. рис. 2.7).
Бесцентрово-шлифовальные станки имеют жесткость в 1,5–2,0 раза большую по сравнению с круглошлифовальными станками. Поэтому они допускают форсированные режимы обработки, обеспечивая более высокую производительность. Они позволяют осуществлять шлифование валов, имеющих малую жесткость. В качестве СОЖ при шлифовании (круглом и бесцентровом) применяют эмульсии иливодные содовые растворы.
36
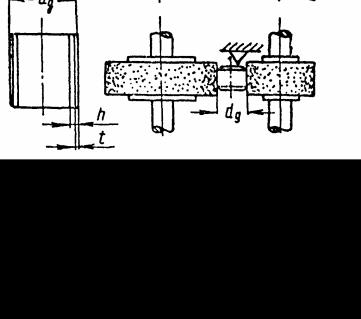
Рис. 2.7. Схема бесцентрового шлифования методом врезания
2.2.3. Хонингование
Хонингование валов производится на специальных станках, снабженных приспособлениями с двумя полукольцами (рис. 2.8), на внутренней стороне которых закреплены шлифовальные бруски, а также на токарных и токарно-револьверных станках с аналогичными приспособлениями, устанавливаемыми на суппорте станка. Хонингование делят на среднее и тонкое. Обрабатываемая деталь, охватываемая двумя полукольцами, получает вращательное движение.
Скорость резания при наружном хонинговании колеблется от 60 до 200 м/мин, а давление брусков – от 0,3 до 1,35 МПа. Кроме того, брускам сообщают продольное перемещение вдоль образующей наружной поверхности со скоростью от 15
37
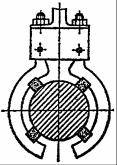
Рис. 2.8. Схема хонингования цилиндрической поверхности
до 100 м/мин. После двух – трех минут хонингования станок автоматически выключается, и деталь освобождается.
В качестве СОЖ используют смесь из 75–85 % керосина и 15–25 % индустриального масла И-20А. Среднее хонингование обеспечивает точность 6–8-го квалитета и шероховатостьповерхности Ra= 0,32–1,25 мкм.
Тонкое хонингование обеспечивает точность 4–5-го квалитета и шероховатость поверх-
ности Ra = 0,08–016 мкм.
Следует отметить, что хонингование наружных цилиндрических поверхностей валов применяют крайне редко.
Значительно чаще для обработки наружных цилиндрических поверхностей валов применяют суперфиниш.
2.2.4. Суперфиниш
Суперфиниш похож на хонингование, так как в качестве обрабатывающего инструмента применяют мелкозернистые шлифовальные (абразивные, алмазные илиэльборовые) бруски.
Отличие суперфиниша от хонингования состоит в том, что при суперфинише наряду с вращательным движением заготовки
ипоступательным продольным движением брусков вдоль образующей заготовки имеется еще колебательное движение брусков, которое является главным рабочим движением (рис. 2.9). Суперфиниширование принято подразделять на чистое, тонкое
идвукратное. Колебательное движение направлено вдоль брусков. При чистом суперфинишировании колебательное движение имеет ход от 2 до 6 мм и частоту колебаний от 300 до 1000 ход/мин. При тонком и двукратном суперфинишировании колебательное движение брусков имеет ход от 0,2 до 2,0 мм и частоту колебаний
38
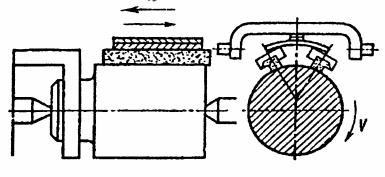
от 1000 до 10000 ход/мин. Толщина срезаемого слоя изменяется от 0,005 до 0,02 мм, а продолжительность обработки 0,2–0,5 минуты. Шероховатость поверхности достигает Rа = 0,04 мкм. В качестве СОЖ используют смесь индустриального масла И-20А с керосином в соотношении 1:10.
Рис. 2.9. Схема суперфиниширования
В начале процесса микронеровности на поверхности детали разрывают масляную пленку. Выступающие гребешки микронеровностей срезаются абразивными брусками. По мере срезания гребешков микронеровность сглаживается и после того, как масляная пленка станет сплошной и не будет иметь разрывов от выступающих зерен, процесс резания прекращается.
При суперфинишировании предъявляются очень жесткие требования к чистоте СОЖ, ибо наличие мельчайших металлических или абразивных частичек может вызвать появление рисок на обрабатываемой поверхности.
Суперфинишу предшествует операция шлифования или тонкого точения, которая обеспечивает шероховатость поверхности Ra ≤ 0,32 мкм.
Чистое суперфиниширование обеспечивает точность 4–5-го квалитетаишероховатостьповерхностиRa = 0,04–0,08 мкм.
Тонкоесуперфинишированиеобеспечиваетточность3–4-го квалитетаишероховатость поверхности Ra = 0,02–0,04 мкм.
39
Двойное суперфиниширование обеспечивает точность 3-го квалитета и шероховатость поверхности Ra = 0,01–0,02 мкм.
Суперфиниш не исправляет дефекты формы, полученные на предыдущих операциях.
2.2.5. Притирка (доводка)
Притирка (доводка) – отделочная операция, подразделяемая на чистовую и тонкую, которую выполняют инструментами – притирами. Притиры изготавливают из чугуна или бронзы и на их поверхность наносят абразивную суспензию (микропорошок с машинным маслом). Относительное перемещение детали и притира должно обеспечивать движение зерен по новым, не повторяющимся траекториям. Для обеспечения этого условия обрабатываемая деталь получает вращение от шпинделя станка, а возвратно-поступательное продольное перемещение осуществляется вручную. В качестве абразивов достаточно часто используют окись хрома (Cr2O3), окись железа (Fe2O3) (порошок окиси железа часто называют крокус) и венскую известь (порошок углекислого кальция с примесью магния и железа). По твердости, режущим свойствам и производительности окись хрома стоит на первом месте. Наиболее чистую поверхность обеспечивает венская известь. В качестве смазывающего материала используют смесь машинного масла с керосином. При использовании венской извести применяют спирт, а при использовании крокуса – вазелин.
Для доводочных работ широко используют суспензии и пасты, например пасты ГОИ (Государственного оптического института). Пасты ГОИ содержат термически обработанную (прокаленную) окись хрома, жиры и органические поверхностноактивные кислоты (олеиновую или стеариновую). Пасты ГОИ делятся на грубые (40 мкм), средние (16 мкм) и тонкие (7 мкм). Цифры указывают толщину снятого слоя со стальной закаленной плитки при 100 возвратно-поступательных движениях притира.
40