
книги / Сварка магниевых сплавов
..pdf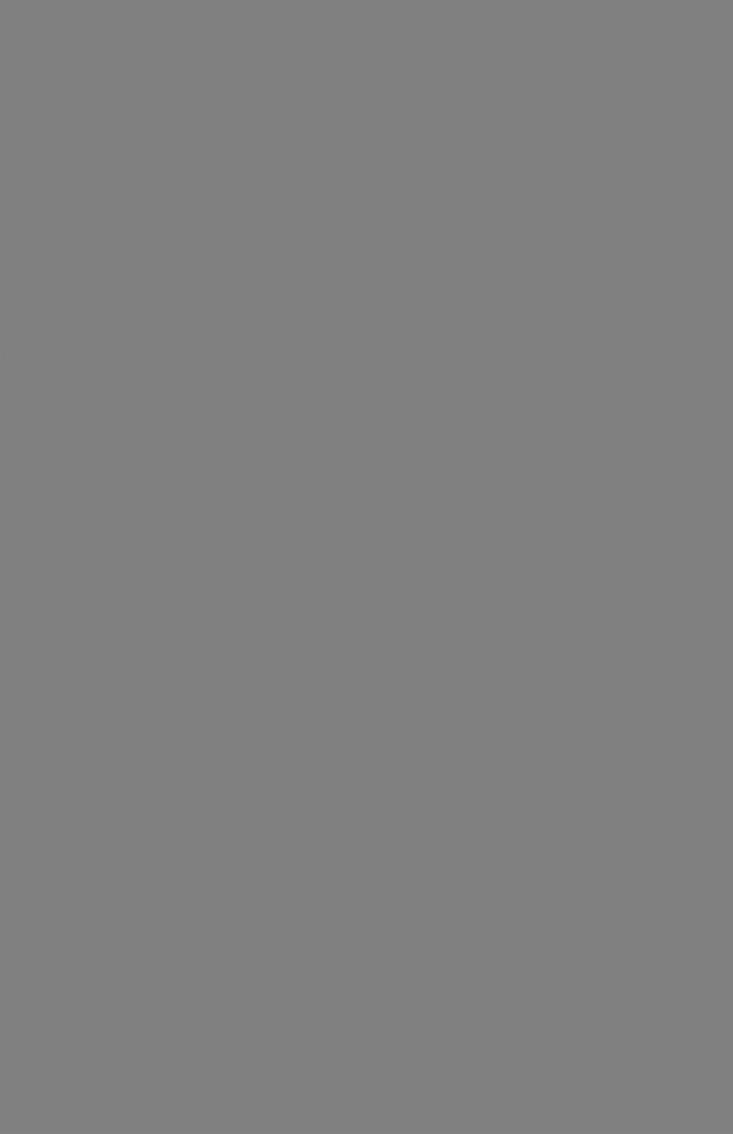
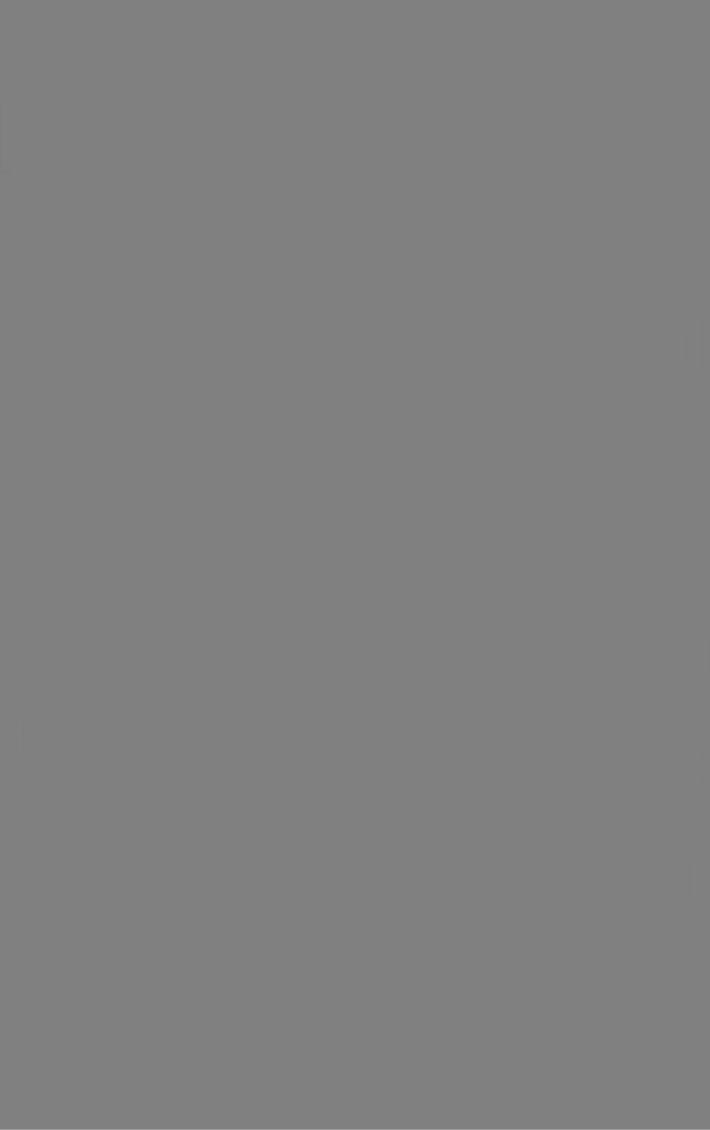
а также автоматически обеспечивать направление электрода по* стыку. В качестве примера можно назвать системы универсаль ных блоков типовых сварочных автоматов и блоки автоматическо го регулирования процесса сварки; последние выполнены на бесконтактных элементах (рис. 38).
Развитие сварочной техники привело к созданию специали зированных сварочных установок, характерные свойства кото рых— узкая специализация, высокая степень механизации вспо могательных операций и высокая производительность (рис. 39).
Рис. 40. Электрическая схема установки |
Рис. 41. Электрическая схема уста |
||||
для аргоно-дуговой сварки плавящимся |
новки для аргоно-дуговой сварки- |
||||
электродом на постоянном токе: |
|
трехфазной |
дугой: |
||
1— сварочный |
генератор ; |
2 — осциллятор; |
1 — сварочный трансформатор; 2 — ба |
||
3— сварочная |
горелка; 4 — свариваемое |
из |
тарея конденсаторов; |
3 — сварочная |
|
|
делие |
|
|
горелка; 4 — свариваемое изделие |
|
Толстолистовые |
(свыше 10 |
мм) |
соединения из |
магниевых |
сплавов целесообразно сваривать плавящимся электродом на постоянном токе обратной полярности. В качестве источниковпитания дуги могут -быть использованы сварочные преобразова тели ПС-300, ПС-500, ПСГ-350, ПСГ-500 и др., а также полу чившие распространение сварочные преобразователи с селено выми выпрямителями ВСС-120 и BGC-300. В иностранной лите ратуре имеются сведения о специальных источниках тока для сварки плавящимся электродом, которые имеют восходящую вольт-амперную характеристику и обеспечивают надежное само регулирование дуги, вследствие чего длина дуги поддерживает ся постоянной. Для полуавтоматической сварки рекомендуются полуавтоматы типа ПШПА-б, ПШП-9, ПШП-10, ПДА-300 и др., для автоматической сварки плавящимся электродом — автома ты типа АДСП, УСА-500С, АДПГ-500 и др. (рис. 40).
В 'последнее время широкое применение находит сварка трех фазной дугой, предложенная для сварки алюминиевых сплавов Столбовым В. И. [12]. Этим прогрессивным методом сварки можно успешно сваривать и сплавы на основе магния (рис. 41).
е а
Источником тока 'служит установка ИТД 600/1000. Автомат АСТВ-2М для сварки трехфазной дугой может переналаживать ся на однофазную сварку (см. рис. 37).
ТЕХНОЛОГИЧЕСКИЕ МАТЕРИАЛЫ
Материалами, используемыми -при дуговой сварке в среде защитного газа, являются инертные газы, вольфрамовые элек троды и присадочные проволоки.
Защитные газы. Для сварки магниевых сплавов в качестве защитного газа 'может быть использован любой из применяемых для сварки алюминия инертных газов — аргон или гелий. В слу чае применения гелия падение -напряжения на сварочной дуге заметно больше, чем при применении аргона. Поэтому при том же источнике переменного тока и тех же условиях сварки сва рочная дуга, горящая в среде гелия, имеет большую тепловую мощность, чем дуга, горящая в аргоне. Однако разрушения по верхностной окисной пленки дугой, горящей в гелии, практиче ски не происходит. В связи с этим для сварки алюминиевых •сплавов за рубежом часто используют смесь телия с аргоном в соотношении от 1 :1 до 1 :5. В нашей стране для сварки маг ниевых (и алюминиевых) сплавов используют почти исключи тельно чистый аргон по ГОСТу 10157—62, что объясняется как его более низкой, чем гелия ценой, так и главным образом его хорошими технологическими качествами; в атмосфере аргона дуга горит спокойнее и формирование шва получается лучшим, чем при сварке в среде гелия.
|
|
Таблица 29 |
|
|
Таблица 30 |
|
Состав1 аргона по ГОСТу 10157-62 в % |
Средний расход аргона при сварке |
|||||
|
магниевых сплавов |
|||||
|
' |
|
|
(стыковые соединения) |
||
Марка |
Ат |
о, |
N |
|
Расход аргона в л/м ин |
|
|
|
|||||
|
|
|
|
Толщина |
при сварке электродом |
|
|
|
|
|
металла |
|
|
|
|
|
|
в мм |
вольфрамовым |
плавящимся |
А |
99,99 |
0,003 |
0,01 |
|
||
|
|
|
||||
Б |
99,96 |
0,005 |
0,04 |
1—3 |
7—9 |
|
|
|
|
|
4—9 |
10-13 |
— |
|
|
|
|
|
|
|
В |
99,90 |
0,005 |
0,10 |
6—8 |
13—15 |
18—20 |
|
|
|
|
10—12 |
17—90 |
20—22 |
|
|
|
|
20—30 |
22—24 |
21—23 |
1 Содержание влаги не более 0.03 г/м*. |
Свыше 30 |
25—28 |
25—27 |
Промышленность выпускает аргон нескольких сортов, отли чающихся друг от друга степенью чистоты (табл. 29). Авторы исследовали влияние содержания влаги в аргоне на образова ние пор в сварных швах листовых магниевых сплавов МА8 и
>64
МА2-1, используя аргон имеющий влажность по точке росы: —35, _ 40 и —45° С при содержании азота 0,018 и кислорода 0,005%. Результаты рентгеноконтроля сварных соединений пока зали, что только при использовании аргона с влажностью -по точке росы —35° С в 'сварных швах имеются единичные поры диаметром 0,2—0,5 мм. При сварке в аргоне с точками росы —40 и —45° С поры в швах не обнаружены. Влажность аргона замеряли непосредственно из баллона.
Никифоров Г. Д. и Антонов Е. Г. исследовали [6] влияние влажности аргона с учетом возможного увлажнения его при прохождении через газовые трубопроводы на сварочной уста новке. Они показали, что «-концентрация влаги в аргоне, вызы вающая пористость швов сплава МА2-1 при самых неблаго приятных условиях его сварки, должна -быть очень высокой (более 4,84 г на 1 м3 газа), т. е. в 3 раза больше, чем она мо жет быть на практике. При сварке сплава ВМД-3 влажность аргона, неизбежно вызывающая пористость швов, должна быть еще больше».
ГОСТ 10157—62 устанавливает допустимое содержание вла ги в аргоне при давлении 760 мм рт. ст. не более 0,03 г/,и3, что соответствует приближенно точке росы —50° С. Исследования показали, -что даже намного большая влажность не приводит к образованию пор в швах магниевых сплавов. Другие примеси в аргоне — кислород и азот — существенно не влияют на каче ство сварных соединений при содержании их в пределах, допу скаемых ГОСТом. В научно-технической литературе нет сведе ний об отрицательном влиянии повышенных содержаний кисло рода или азота на качество 'сварных соединений, а также об исследованиях в этой области. Изложенное позволяет считать пригодным для сварки магниевых сплавов аргон всех трех вы пускаемых .промышленностью марок.
При расчете расхода газа на сварку необходимо учитывать дополнительный расход газа на подготовительные операции (продувку газовых коммуникаций перед началом сварки в те чение 3—5 сек) и заключительные операции (защиту вольфра мового электрода от окисления после гашения сварочной дуги в течение 5—10 сек). Дополнительный расход газа на подгото вительные и заключительные операции не зависит от протяжен ности шва и скорости сварки и определяется принятым расхо дом газа по ротаметру и продолжительностью операции (табл. 30).
В качестве приборов для контроля за расходом газа приме няются ротаметры. Для сварочных установок можно рекомен довать ротаметры типа PC-3, РС-5, PC-ЗА конструкции завода «Манометр» или ротаметры типа ИРКС-6,5 и ИРКТ-13, выпус каемые заводом «Теплоконтроль», Ротаметры тарированы по воздуху, т. е. позволяют измерять расход газа, по плотности соответствующего воздуху. Для работы с другими газами и, г.
5—34 |
65 |
частности, с аргоном необходимо иметь дополнительно тарировочную кривую или пересчитывать расход с учетом разницы в плотности газов.
Вольфрамовые электроды. На практике в качестве наплавящихся электродов при сварке магниевых сплавов в инертной среде применяются вольфрамовые прутки, обычно изготовленные из чистого вольфрама марки ВЧ (табл. 31). Активирующие при-
Таблица 3!
Химический состав1 вольфрамовых электродов в %
Электрод |
Диаметр |
Вольфрам |
Окись |
Окись |
Окись |
|
Металли |
в мм |
лантана |
тория |
иттрия |
|
ческий |
||
|
|
|
|
|
|
1 |
тантал |
|
|
|
|
|
|
|
|
ВЧ |
0 ,2 — 10 |
99,85 |
|
|
— |
1 |
— |
ВЛ-10 |
1,0 — 10 |
98,36 —9 9 ,0 |
1 ,0 — 1,49 |
— |
|||
ВЛ -20 |
1,0 — 10 |
9 7 ,8 5 - 9 8 ,5 |
1 , 5 - 2 , 0 |
— |
|
1 |
— |
|
|
||||||
ВТ-15 |
0 ,2 — 10 |
97,85 — 9 8 ,5 |
|
— |
1 |
— |
|
— |
1 , 5 - 2 , 0 |
||||||
|
|
|
|
|
|
|
|
ВИ -30 |
1,0 — 10 |
96,75 — 9 7 ,5 |
■-- |
— |
2 ,5 — 3,1 |
! |
0,01 |
|
|
|
|
|
|
! |
|
1 Остальное— примеси.________________________________________________ _
садки — окись тория, окись лантана и др. — вводятся в вольф рам с целью повышения устойчивости катодного пятна и ста бильности горения дуги, а также предотвращения оплавления конца электрода при сварке сталей меди, никеля, титана, туго плавких металлов на постоянном токе. При сварке алюминие вых и магниевых сплавов на переменном токе дуга, горящая между электродом из чистого вольфрама и основным металлом, имеет вполне удовлетворительные технологические характери стики, в этом случае применение вольфрамовых электродов с активизирующими присадками не требуется.
Институтом электросварки им. Е. О. Патона и Московским электроламповым заводом предложен вольфрамовый электрод марки ВИ, содержащий добавки окиси иттрия и металлического тантала. Этот электрод отличается повышенной стойкостью к токовой нагрузке по сравнению с электродом из чистого вольф рама при одинаковом диаметре и рекомендуется для сварки вы сокоамперной дугой переменного тока алюминиевых сплавов. Очевидно, что этот электрод может быть с равным успехом ис пользован и при сварке магниевых сплавов.
Применение вольфрама при сварке в качестве иеплавящегося электрода возможно только при наличии иеокислительной среды. При нормальной величине сварочного тока для данного диаметра электрода расход вольфрама весьма невелик благода ря малой летучести его при высоких температурах (0,04—0,08 г на 1 м шва). На практике расход вольфрамовых электродов значительно больше вследствие встречающихся на производстве
66
нарушений процесса сварки такого характера, как загрязнение конца электрода при замыкании на сварочную ванну или приса дочный металл, перегрев электрода из-за повышенных значений сварочного тока, плохая защита конца электрода и т. п. (табл. 32). Диаметр электрода выбирают в первую очередь в за висимости от величины сварочного тока (табл. 33).
Таблица 32
Нормы расхода вольфрама при аргоно-дуговой сварке
алюминиевых и магниевых сплавов
Толщинаме таллав мм |
|
Расход вольфрама в г |
|
|
на 100 м шва |
||
Диаметр |
при |
с:варке |
|
электрода |
|
|
|
|
в мм |
ручной |
механи |
|
|
зированной |
|
1 |
1 ,5 |
8 ,3 |
3 ,9 |
1 ,5 - 2 |
2 ,0 |
2 3 ,4 |
10,9 |
3 , 0 - 4 |
3 ,0 |
8 3 ,3 |
3 9 ,0 |
5 , 0 - 6 |
4 ,0 |
132,2 |
125,0 |
7 |
5 ,0 |
165 ,0 |
156,0 |
Таблица 3$
Выбор диаметра вольфрамового электрода (ток переменный)
|
Допустимая величина силы |
|
Диаметр |
сварочного тока в а |
|
электрода |
|
|
в мм |
Аргон |
Гелий |
|
||
1 - 2 |
20— 100 |
1 0 -6 0 |
3 |
100 -160 |
60— 100 |
4 |
140—220 |
100 -160 |
5 |
200—280 |
160 -200 |
6 |
2 5 0 -3 6 0 |
2 0 0 -2 5 0 |
8 |
3 5 0 -4 2 0 |
2 5 0 -3 4 0 |
Присадочные материалы. В качестве присадочного металла при сварке неплавящимся вольфрамовым электродом и свароч ной электродной проволоки при сварке плавящимся электродом используется проволока из магниевых сплавов, полученная пу тем прессования. Поскольку при прессовании проволоки длина ее ограничена для использования при автоматической сварке, прутки сначала сваривают, затем стыки зачищают и проволоку свертывают в бухту. Практика изготовления сварных узлов из магниевых сплавов с применением проволоки, сваренной из прутков, показала, что при автоматической подаче проволоки в зону дуги разрывов ее не происходит.
Магниевые сплавы сваривают в основном с применением присадочного металла. В отдельных случаях можно использо вать сварку по буртику — на механически обработанных дета лях или по отбортовке. Сварка по отбортовке может применять ся только для тонколистовых конструкций, так как отбортовка магниевых сплавов затруднительна.
Диаметр присадочной проволоки при автоматической сварке неплавящимся электродом выбирают в зависимости от толщины свариваемого металла, а при сварке плавящимся электродом — в зависимости от силы сварочного тока и скорости подачи про волоки (табл. 34).
5* |
67 |
|
|
|
|
Таблица 34 |
Выбор диаметра присадочной проволоки из магниевых сплавов |
||||
а) Сварка вольфрамовым электродом |
б) Сварка плавящимся электродом |
|||
Толщина металла |
Диаметр присадочной |
Диаметр |
Скорость |
Сила свароч |
в мм |
проволоки в мм |
сварочной |
||
|
|
проволоки |
подачи прово |
ного тока в а |
|
|
в мм |
локи в мм/сек |
1 |
|
1 ,5 -2 |
|
|
|
До 2 |
0,8 |
37—41 |
160—165 |
|
2—3 |
2 - 2 ,5 |
|||
4 - 6 |
2,5 |
1,2 |
20—22 |
180—200 |
8 |
3,0 |
1,6 |
13—15 |
220—265 |
Свыше 10 |
3—4 |
2,0 |
10—12 |
270—300 |
|
|
2,5 |
8—9 |
320—350 |
|
|
3,2 |
7—8 |
420—440 |
При сварке |
магниевых сплавов применяется присадочный |
металл, как правило, того же состава, что и свариваемый. Од нако в отдельных случаях для придания сварному соединению определенных технологических свойств используют присадочный металл другого состава.
С поверхности присадочной проволоки перед сваркой необхо димо обязательно удалять окисную пленку. Лучшие результаты дает химическое травление или электрополирование. Возможно также химическое полирование и механическая обработка по верхности любыми режущими инструментами.
ПОДГОТОВКА МАТЕРИАЛОВ ПОД СВАРКУ
Изготовлению любой сварной конструкции предшествуют операции подготовки под сварку: расконсервация листов, разметка и вырезка элементов конструкции, гибка, разделка кро мок и зачистка последних под сборку и сварку.
Для получения высокого качества сварных соединений из магниевых сплавов необходимо обеспечить чистоту поверхности в местах сварки. При расконсервации листов следует удалить с них заводскую смазку специальными скребками и щетками, затем обезжирить растворителями. В качестве органических растворителей могут быть применены бензин, уайт-спирит, аце тон технический, ацетоновая или авиационная смывка. Проти рать необходимо до исчезновения сажистого налета на чистой ветоши. Обращение с указанными растворителями должно со ответствовать действующим правилам техники безопасности. Удалять консервирующие смазки с листов, профилей, деталей необходимо не ранее, чем за 20 суток до запуска их в работу.
Вырезать детали из листов магниевых сплавов можно на обычном оборудовании, применяемом для обработки стали. Маг ниевые сплавы хорошо режутся гильотинными ножницами, пи лами и т. п. Разделку кромок под сварку можно выполнять на
68
строгальных и фрезерных станках. Эта операция необходима при больших толщинах свариваемых кромок для обеспечения провара по всему сечению. Способ резки выбирается в зависи мости от размеров деталей, их толщины и оборудования. Гибку ведут на трехили четырехвалковых гибочных вальцах.
После изготовления деталей непосредственно перед сваркой кромки под сварку зачищают окончательно или механическим путем (щеткой, шабером, напильником), или химическим путем с применением травления. Зачистка поверхности свариваемых кромок с помощью абразивов, наждачной или стеклянной бу маги и пескоструйной обработки не допускается, так как в этом случае могут быть внесены новые загрязнения в виде включений карборундовой, корундовой или кварцевой пыли и др.
Эффективным способом очистки поверхностен деталей и уз лов от слоя окисной пленки и загрязнений является химическая обработка — травление. Схема технологического процесса хи мической обработки поверхности деталей из магниевых сплавов (кроме сплава МАИ) под сварку следующая:
1. Химическое обезжиривание при температуре 60—90°С в течение 5—10 мин в ванне состава: 20—30 г/л тринатрийфосфата ИазРО^НгО; 30—50 г/л соды кальцинированной ЫагСОз; 20—50 г/л едкого натра NaOH; 3—5 г/л жидкого стекла;
2.Промывка в проточной горячей воде при температуре 50— 60°С в течение 0,5—1 мин.
3.Удаление защитного покрытия в течение 10—15 мин при температуре 70—80°С в ванне с едким натром NaOH (200— 300 г!л).
4. Промывка в проточной горячей воде, как |
указано в п. 2. |
5. Промывка в холодной воде. |
течение 0,5— |
6. Травление при комнатной температуре в |
2 мин в ванне состава 150—200 г/л хромового ангидрида СгОз; 25—35 г/л азотнокислого натрия NaN03; 2—3 г/л фтористого кальция CaF2;
Величина съема металла в 1 мин составляет 2,5—3 мкм.
7.Промывка в холодной проточной воде с применением гид ропульта до удаления с поверхности деталей и присадочного металла хромового электролита.
8.Сушка сжатым воздухом при температуре 60—90°С, очи
щенным от масла, воды и других механических загрязнений. Указанный вид химической обработки целесообразен в усло
виях серийного производства сварных узлов небольших габа ритных размеров. При сварке крупных узлов, как показала практика, удовлетворительные результаты получаются при уда лении защитной (оксидной) или естественной окисной пленки на свариваемых кромках и участках, прилегающих к нему, ме ханическим путем, лучше всего шабрением (рис. 42).
Кприсадочному металлу должны предъявляться такие же и,
вряде случаев, более жесткие требования в отношении качества
69
его очистки. Объясняется это тем, что доля участия присадоч ного металла в формировании сварного шва может быть боль> ше, чем основного, и, следовательно, вероятность попадания в
|
шов окиси магния и других |
|||
дш |
загрязнений с присадочным ме |
|||
таллом |
будет больше. |
|||
20+30 |
||||
1__ |
Большое внимание следует |
|||
| л*о+д т | Т ^ |
уделять |
хранению |
проволоки |
|
после химического |
травления. |
|||
|
Хранение проволоки |
во влаж |
||
Рис. 42. Места удаления защитной или |
ной атмосфере приводит к бы |
|||
строму |
росту на ее |
поверхно |
||
естественной пленки на стыковом |
||||
и тавровом соединении |
сти окисной пленки и адсорби |
рованию в этом слое водорода,
Таблица 35
Механические свойства соединений из сплава МА2-1 толщиной 3 мм,
сваренных в различное время после травления
междуВремятравле деталейниеми их всваркойсутках |
|
|
1 |
|
|
|
Без зачистки торцов перед сваркой |
|
|||
|
(с прихваткой) |
|
|
|
|
|
Ов в кг/мм1 |
*, ■ % |
; |
Угол |
|
|
изгиба |
|
|||
|
|
|
J в |
градусах |
! |
|
|
|
) |
|
|
3—4 ч |
26,5-28,0 |
> |
74—112 |
|
|
5,4-11,1 |
|
||||
1 |
27,3 |
7,3 |
|
93 |
|
26,7-27,6 |
6 ,0 -6 ,6 |
70-150 |
|
||
2 |
27,1 |
6,4 |
|
98 |
|
26,9-27,6 |
6 ,6 -7 ,7 |
76-84 |
|
||
3 |
27,2 |
7,0 |
|
81 |
|
26,8-27,4 |
j 6 ,6 -7 ,1 |
80—90 |
|
||
4 |
27,1 |
6,8 |
|
84 |
|
27,2—28,0 |
5 ,7 -7 ,1 |
70-84 |
|
||
7 |
27,5 |
6,4 |
|
77 |
|
27,1—27,7 |
6 ,0 -7 ,4 |
79—81 |
|
||
10 |
27,3 |
7,0 |
|
80 |
|
26,9-27,5 |
6 ,0 -7 ,4 |
70—85 |
|
||
15 |
27,2 |
6,7 |
|
78 |
|
27,5—28,3 |
6 ,6 -8 ,6 |
71—150 |
|
||
|
27,9 |
7,8 |
|
ПО |
i |
|
|
|
|
|
С зачисткой кромок перед сваркой (без прихватки)
Ов в кГ /ммг |
б&в % |
Угол |
|
изгиба |
|||
|
|
в |
градусах |
26 ,6 -27,5 |
613—8,6 |
71—131 |
|
27,0 |
|
7,2 |
92 |
25,9—26,8 |
5,7 |
—6,9 |
73 -83 |
26,5 |
|
6,0 |
77 |
— |
|
— |
— |
2 6 ,9 -2 7 ,6 |
6,0 |
—7,4 |
69—79 |
27,2 |
|
6,8 |
75 |
27,2—27,8 |
6 ,3 - 7 ,1 |
79—85_ |
|
27,5 |
|
7,0 |
81 |
2 6 ,6 -2 7 ,5 |
6,0 |
—7,4 |
72—98_ |
27,2 |
|
6,8 |
81 |
26,2—27,6 |
* |
СО 00 1 |
80—83_ |
|
со со |
||
26,8 |
|
7,0 |
81 |
27,2—27,4 |
6,3 |
—7,1 |
68—160, |
27,3 |
|
6,7 |
101 |
Приме ча ние . Образцы размером 450X150X3 мм сварены травленой присадочной проволокой.
70