
книги / Микроэлектроника толстых пленок
..pdf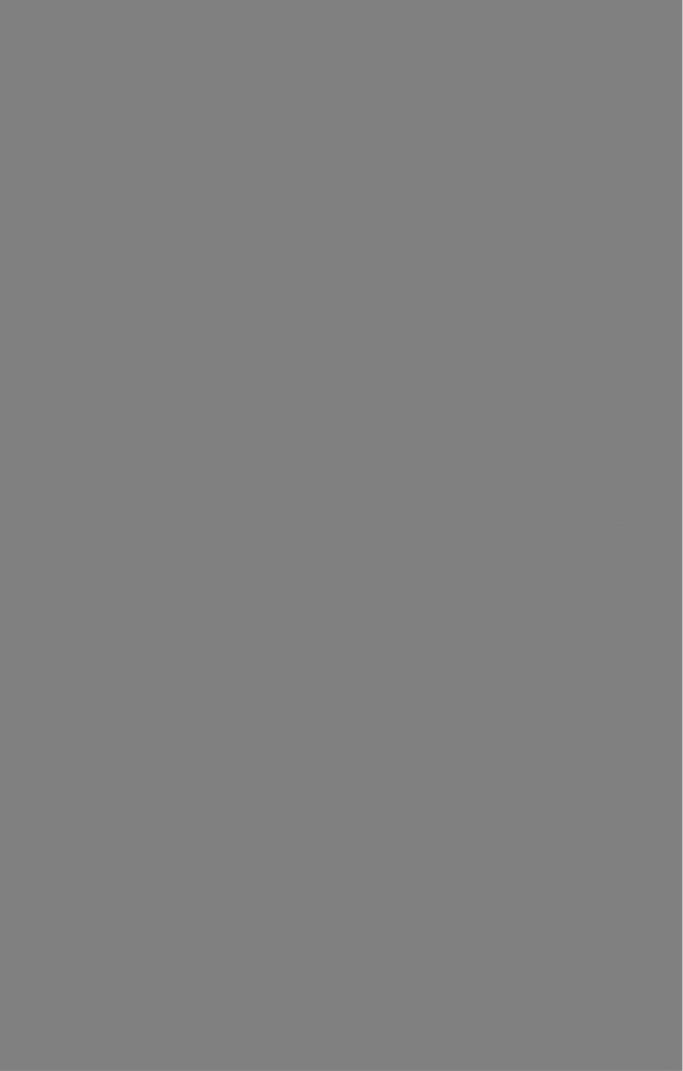
112 |
Г Л А В А 4 |
4.4. Подгонка резисторов
После вжигания толстоплеиочных резисторов типич ный разброс их сопротивлений относительно номинала составляет ± 15%. Если допуск на резисторы меньше 15%, то они нуждаются в подгонке. Подгонка прово дится путем уменьшения толщины резистора или его размеров. Соответственно этому, как уже отмечалось ранее, при проектировании резисторов их толщина или размеры несколько завышаются по сравнению с номи
налом.
Для подгонки резисторов разработано довольно мно го методов. Однако широкое применение нашли лишь абразивный и лазерный методы, а также подгонка им пульсным током. При этом чаще применяется абразив ный метод !). Он заключается в следующем. Через сопло, укрепленное над резистором и имеющее необходимые форму и размеры, продувается порошок окиси алюминия с размерами частиц 25 мкм. При попадании порошка на поверхность резистора некоторая доля материала рези стора удаляется, что приводит к изменению его сопро тивления. При этом методе отклонение от номинала ре зистора не превышает ±5%. Преимуществом метода является то, что подгоночное устройство не касается под ложки, так что образец не подвергается ни ударным воз действиям, ни вибрации, ни тепловому излучению. Этот процесс может быть легко автоматизирован, поверхность подложки не портится, поскольку величина давления порошка может регулироваться. После подгонки поро шок удаляется с подложки вакуумным пылесосом. Не достатком метода является то, что в процессе подгонки вскрывается защитный слой резистора, что увеличивает влияние среды на его свойства. Поэтому приходится по вторно покрывать резистор защитным слоем. Другой недостаток состоит в том, что абразивный порошок мо жет воздействовать и на соседние элементы. Это неже лательное влияние можно исключить, если создать соот ветствующим образом топологию схемы с учетом необ ходимости в возможной подгонке.)*
*) Имеется в виду практика зарубежных фирм. — П рим . ред.
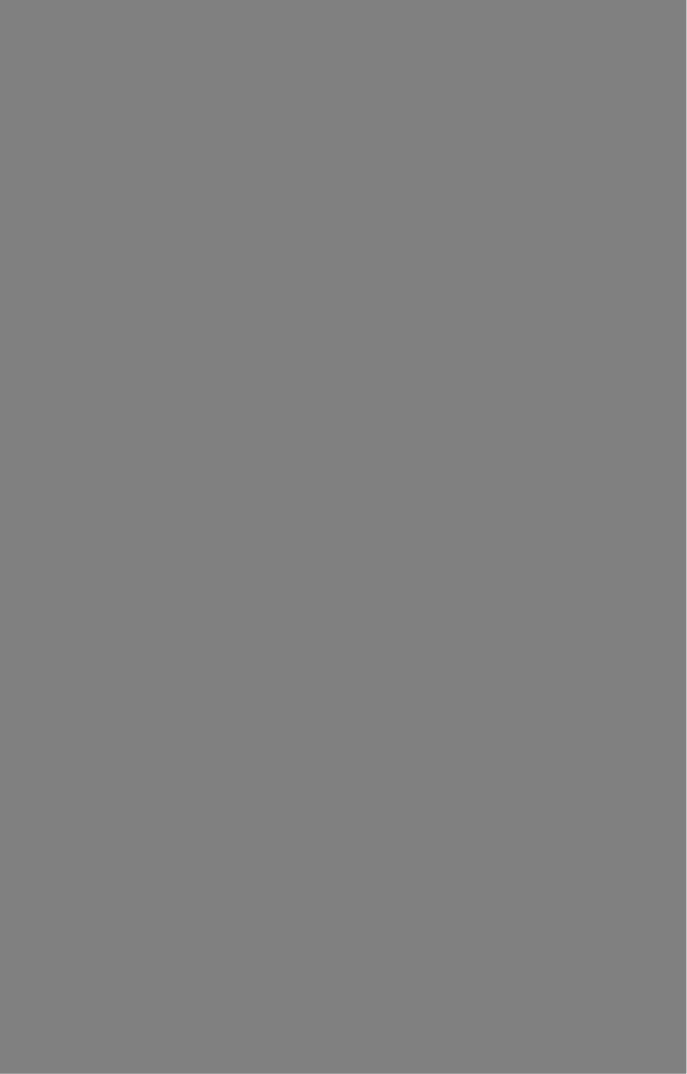
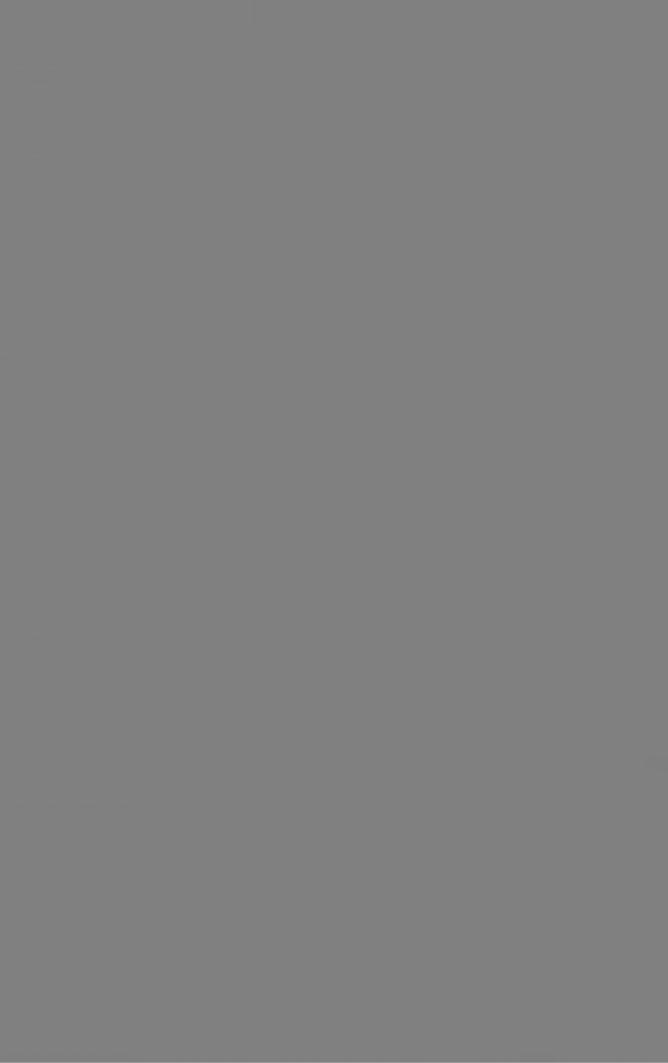
О Б О Р У Д О В А Н И Е И П Р О Ц Е С С С О ЗД А Н И Я СХЕМ |
Пб |
лазера во время подгонки отдельных резисторов |
за |
дается вычислительным управляющим устройством. По сравнению с абразивным метод лазерной подгонки, а также метод высоковольтного разряда обладают тем преимуществом, что при их использовании не повреж дается защитный слой.
При использовании высоковольтного разряда можно как уменьшать, так и увеличивать сопротивление рези сторов. О стабильности резисторов, обработанных этими методами, известно мало. Данные, относящиеся к методу высоковольтного разряда, не обнадеживающие, лазер ный же метод является весьма перспективным. Предпо лагается, что свойства резисторов, подвергнутых лазер ной обработке, не изменяются, тогда как абразивно обработанные резисторы менее стабильны, чем исход ные, и обладают более высоким уровнем шумов. Основ ное оборудование, необходимое для создания лазерного метода, громоздко, и поэтому применение этого метода целесообразно лишь при большом объеме производства. В обоих указанных методах исключена проблема загряз нения подложки абразивным порошком.
4.5. Прецизионная .толстопленочная технология
Наименьшие ширина и расстояние между линиями, которые можно в настоящее время наносить трафарет ной печатью, равны 250 мкм. Однако после внедрения балочных выводов, метода обращенного чипа, а также сложных проволочных соединительных структур на очень малых подложках возникла необходимость уменьшения ширины и расстояния между наносимыми линиями. Раз витие прецизионной технологии трафаретной печати должно дать возможность производить толстопленочные схемы любой сложности, стоимость которых ниже, чем при производстве путем вакуумного напыления и фото литографии. В схемах с балочными выводами удается наносить линии шириной 0,05 мм на площадках шири ной 0,2 мм. Прецизионная трафаретная печать приводит к уменьшению размеров подложки, наносимого рисунка, меньшему использованию паст и к уменьшению разме ров применяемого оборудования.
116 Г Л А В А 4
При прецизионной трафаретной печати особенно важное значение приобретает шероховатость и кривизна подложки. В этом случае подложка должна быть осо бенно гладкой и плоской, а высота шероховатостей не должна превышать 0,4 мкм. Первостепенное значение приобретают реологические и вязкостные характеристи ки пасты. Паста должна протекать через ячейки маски, но не должна растекаться по подложке. Недавно раз работаны желеобразные пасты с высоким содержанием металлической компоненты и вязкостью от 400 до 600 П. Эти пасты содержат тиксотропные составляю щие, уменьшающие текучесть пасты при снятии сжима ющих усилий.
Часто при нанесении прецизионных схем толщина по лучаемых элементов бывает очень малой, в результате чего структура пленок получается островковой; это при водит к увеличению их сопротивления. Применение двой ной печати уменьшает неоднородность пленок, но ус ложняет технологический процесс. При прецизионной печати обычно применяются сетчатые трафареты из не ржавеющей стали, на которую наносится эмульсия тол щиной от 0,01 до 0,0175 мм. Пленки, получаемые при ис пользовании таких масок, очень тонки и присоединять их к внешним выводам очень сложно. Известно, что для хорошего качества пайки пленки после операции вжигания должны иметь толщину не меньше 0,01 мм. В на стоящее время предельное разрешение линий, получен ных при печати через плетеные маски из нержавеющей стали, равно 0,125 мм, на цельнометаллических сетках 0,100 мм, на масках, вытравливаемых по обеим поверх ностям, 0,05 мм.
Недавно для прецизионной печати разработаны не которые новые типы паст с вязкостью 5000 П. При ис пользовании паст этого типа следует применять цельно металлические маски, полученные путем травления, и контактную печать. Для получения пленок с четкими контурами рисунка сдавливающие усилия должны быть достаточно малы. Ракель для вдавливания пасты нужно изготавливать из каучука или пластика с твердостью 80 единиц по Шору. При контактном методе печатания с помощью травленых цельнометаллических масок отделять
О Б О Р У Д О В А Н И Е И П Р О Ц Е С С С О ЗД А Н И Я СХЕМ |
П7 |
маску от подложки лучше вертикально без скольжения, которое всегда имеет место в случае плетеных масок. Если паста имеет высокую вязкость, то для облегчения ее продавливания маску можно немного нагреть. Это облегчает продавливание и предотвращает растекание пасты при ее соприкосновении с холодной подложкой.
При прецизионной трафаретной печати, когда нано сятся тонкие линии, площадь контакта между пастой и
Ф и г . 4.30. Рисунок прецизионно нанесенных пленок.
подложкой может быть весьма малой, что приводит к ухудшению адгезии между ними. Кроме того, вследствие малой толщины элементов, нанесенных на подложку, возникают трудности нанесения на них припоя методом погружения в расплав. Для устранения этих трудностей применяются травленые цельнометаллические маски, использование которых обеспечивает получение более толстых пленок с резко очерченными краями.
Наиболее узкие линии (ширина 0,05 мм) получаются при использовании самоподдерживающихся цельноме таллических масок. Эти маски изготовляются из молиб деновой фольги, на одной поверхности которой вытрав ливается рисунок, а на другой — сетка. На фиг. 4.30 показан тестовый образец, нанесенный методом преци зионной трафаретной печати. На маске нанесены линии различной ширины при различном расстоянии между
118 |
ГЛ А ВА 4 |
ними. Самая узкая линия имеет ширину 0,05 мм, а рас стояние от ее краев до следующей линии равно 0,075 мм. Эти линии иногда неоднородны по толщине вследствие неравномерности застывания пасты высокой вязкости. Но по мере разработки новых типов паст и методов их нанесения толстопленочная технология может обеспе чить такое же разрешение, какое можно было достиг нуть только тонкопленочной технологией. При этом стоимость изготовления будет значительно ниже.
4.6. Разработка новых материалов
Для удовлетворения потребности рынка в материалах для толстоплеиочной технологии в последнее время было организовано много новых фирм. Однако не только но вые фирмы занимаются разработкой и производством усовершенствованных паст для изготовления проводни ков, резисторов и диэлектриков. В эту сферу деятельно сти вовлекаются и старые фирмы.
Усилия этих фирм направлены на создание новых проводящих материалов, облегчающих присоединение внешних выводов; создание проводящих материалов, пригодных для прецизионной трафаретной п.ечати; созда ние резистивных материалов с малым коэффициентом температурного расширения, малым уровнем шумов, ма лым разбросом характеристик относительно номинала сразу после вжигания, широким интервалом значений номиналов; создание диэлектрических материалов с вы соким значением диэлектрической постоянной и боль шой добротностью для производства конденсаторов, а также малым значением диэлектрической постоянной для изоляций пересечений.
4.7. Многослойные керамические материалы
По мере разработки новых материалов и технологи ческого оборудования расширилась область применения толстопленочных схем. Экономическая эффективность технологии производства толстопленочных схем будет выше, если увеличивать число' резисторов и конденсато
О Б О Р У Д О В А Н И Е И П Р О Ц Е С С С О ЗД А Н И Я СХЕМ |
119 |
ров, наносимых на одну подложку. Для создания гиб ридной схемы к подложке с пассивными элементами присоединяются различные диоды и транзисторы. Это приводит к возрастанию числа межсоединений и, таким образом, к существенному ограничению степени свободы на поверхности подложки. Потребность в более эффек тивном использовании поверхности подложки привела
кнеобходимости создания проволочных перемычек,
сквозных отверстий и нанесения пленочных элементов по краям подложки. Все это существенно увеличило стоимость схемы. Создание сквозных отверстий ограни чивает возможность топологических и конструкционных изменений на данной подложке и нуждается в дополни тельных операциях пропускания проводников через эти отверстия или их нанесения, а также пайки. Наносить пленки по краям подложек очень трудно, а зачастую нереально, особенно если боковые грани подложки не закруглены. Недавно сообщалось о нескольких новых методах присоединения многослойных проводников не посредственно к сапфировой подложке. Из этих сообще ний следует, что компактное присоединение активных элементов к пассивным осуществляется гравировкой подложки, утоплением в ней проводящих элементов и созданием в подложках отверстий для выводов комму тационной гребенки. Эти структуры на многослойных керамических подложках могут вжигаться как на воз духе, так и в восстанавливающей атмосфере, и могут металлизоваться различными методами, включая методы припайки проводников жидким или твердым припоем. Кроме того, эти структуры удобны для крепления подлож ки к корпусу и припайки к ним проволочных выводов.
Сырые слои из окиси алюминия, которые наносятся на металлизацию, покрываются под давлением тонкой металлической фольгой и спекаются при температурах выше 1500° С. В настоящее время стоимость и время проведения этих процессов очень велики. С этой точки зрения представляет интерес только разработка много слойных структур, которые могут обжигаться на воздухе. На фиг. 4.31 поэлементно показана типичная многослой
ная |
структура. |
Основная часть |
структуры состоит |
из |
двух слоев |
с уложенными и |
них проводниками. |
а
6
а
в
а
г
Ф иг. 4,31. Компоновка многослойной керамической схемы,
а —штырьки в пластине из окиси алюминия; б —скрытые проводники 1-го слоя; 0 —скрытые проводники 2-го слоя; г —контактные площадки для внешних рыводоц,