
книги / Оборудование литейных цехов
..pdfопасности, так как для рабочего процесса тогда применяли газ метан или пропан с кислородом. В 1977 г. германская фирма G. Fischer усовершенствовала этот процесс: для реакции горения в камере сгорания использовался кислород, находящийся в атмосферном воздухе, что намного упростило и удешевило конструкцию и процесс. Конструкция была дополнена лишь вентилятором для перемешивания газовоздушной смеси. Газоимпульсные установки несколько проще, чем воздушно-им- пульсные. Камера сгорания в этих установках не имеет специальных перегородок, отделяющих ее от формовочной смеси, поскольку давление горючей газовоздушной смеси до воспламенения составляет всего ~ 0,1 атм. Кроме того, отсутствуют всякого рода импульсные клапаны, достаточно сложные по своей конструкции. Как и в воздушно-импульсном процессе низкого давления, в газоимпульсном, как правило, не применяются венты. Стоимость энергозатрат при газоимпульсном процессе существенно ниже, чем в воздушно-импульсном [41]. Для поджигания газовоздушной смеси применяют почти всегда лишь один источник зажигания, независимо от габаритов опоки.
И все же процесс газоимпульсного уплотнения уступает место воздушно-импульсному низкого давления. Причина заключается в том, что газоимпульсный процесс более опасен, а точнее – взрывоопасен, и в экологическом отношении более вреден из-за выделения при сжигании в составе отходящих газов СО или других оксидов.
11.1. Анализ газоимпульсного процесса уплотнения
Газоимпульсная установка (рис. 11.1) состоит из камеры сгорания 1, трубы-дефлектора 2, запальной свечи 3, вентилятора 4, переходной камеры 8, наполнительной рамки 9, модельноопочной оснастки 10, 11, 12.
211
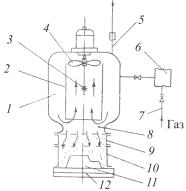
Горючий газ подается по |
|
|||||
трубопроводу 7 в дозатор 6 |
|
|||||
объемного типа и далее в ка- |
|
|||||
меру сгорания 1. Перед пода- |
|
|||||
чей горючего газа в камеру |
|
|||||
сгорания |
ее |
проветривают |
|
|||
вентилятором |
при |
открытой |
|
|||
свече 5. Таким образом, окис- |
|
|||||
лителем |
при |
сгорании |
газа |
|
||
является атмосферный воздух, |
|
|||||
находящийся в камере сгора- |
Рис. 11.1. Газоимпульсная |
|||||
ния в соотношении |
1:10 |
(на |
||||
установка |
||||||
один объем газа 10 |
объемов |
|||||
|
воздуха). Газ подается в камеру сгорания, как правило, самотеком. Объем дозы определяется электроконтактными манометрами (ЭКМ), установленными в дозаторе. При достижении заданного давления газа в дозаторе от ЭКМ подается команда на закрытие впускного клапана и открытие выпускного. При снижении давления в дозаторе до ≈ 0,01 МПа выпускной клапан закрывается и открывается впускной. При образовании искры в источнике зажигания происходит мгновенное сгорание газовоздушной смеси. Источником зажигания может служить автомобильная свеча, а лучше – авиационная. Образовавшаяся волна давления продуктов сгорания через переходную камеру 8 мгновенно воздействует на формовочную смесь, находящуюся в наполнительной рамке 9 и опоке 10, разгоняет ее в направлении модели 11 и модельной плиты 12, где она резко тормозится и под действием сил инерции уплотняется. Давление газов над смесью в период рабочего процесса составляет обычно 0,4–0,5 МПа, а давление смеси на модельную плиту достигает 0,6–0,8 МПа. Верхние слои смеси при этом остаются неуплотненными. Характер распределения плотности формовочной смеси по высоте опоки при газоимпульсном процессе уплотнения аналогичен процессам встряхивания и воздушно-импульсному.
212
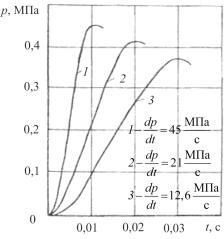
Для получения технологически необходимой плотности и прочности формы необходимо создать над смесью необходимую величину градиента давления dp/dt (скорость нарастания давления) (рис. 11.2). Значения этих величин находится в преде-
лах: р = 0,5..0,6 МПа, p = 10,0…50,0 МПа/с; t = 0,02…0,03 с.
Рис. 11.2. Влияние на градиент давления длительности импульса
Механизм уплотнения смеси при ГИФ. Опытным путем установлен прямо пропорциональный характер зависимости деформации ε от скорости нагружения dp/dt [27] при импульсном уплотнении. Их соотношение остается практически постоянным, что свидетельствует о том, что при импульсном уплотнении формовочная смесь ведет себя подобно упругому телу Гука. Газоимпульсные процессы можно разбить на три стадии. Первая – разрушение первичных когезионных связей между оболочками отдельных частиц и их агрегатов и превращение смеси в «кипящий слой» из частиц, создающих сопротивление объемному уплотнению только силами сухого трения. В этот период устраняются так называемые «арочные» конструкции и сокращается объем внутренних пор. Вторая стадия происходит почти
213
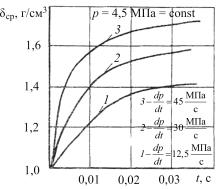
одновременно с первой: как только частицы приобретают свободу от связей, тут же начинается их движение в сторону распространения нарастающего давления.
Третья стадия характеризуется взаимодействием элементарных слоев смеси с модельной оснасткой. Верхние слои, тормозясь об оснастку, давят на нижние, еще больше уплотняя их. Одновременно интенсивно восстанавливаются когезионные связи между частицами за счет более плотной укладки частиц в объеме формы. Время достижения необходимого уровня нагружения (σ = 0,4…0,5 МПа) смеси существенно влияет на конечное уплотнение. Если это время относительно велико, получается низкий уровень уплотнения, и, наоборот, если прирост напряжения высок, меньше времени затрачивается на разрыв первичных когезионных связей, частицы получают большую скорость движения – эффективность уплотнения повышается
(рис. 11.3).
Рис. 11.3. Влияние градиента давления и длительности импульса на среднюю плотность формы
Для описания газоимпульсного уплотнения используется аналогичная воздушно-импульсному уплотнению реологическая модель.
214
Факторы, влияющие на рабочий процесс газоимпульсных формовочных машин
Рабочий процесс газоимпульсных установок (рабочий режим) зависит от следующих факторов:
1)изменение скорости газовоздушной смеси (20–50 м/с)
истепень ее турбулизации;
2)изменение интенсивности источника зажигания.
Чтобы выполнить первое условие, идут двумя путями:
1.В камере сгорания устанавливают вентилятор с различной частотой вращения (от 1000 об/мин до 3000 об/мин), причем чем выше обороты, тем выше градиент давления. Подбирается такая скорость вращения, чтобы режим был оптимальным.
2.В камеру устанавливают звуковой генератор, который при определенной частоте колебаний возбуждает в газовоздушной среде, находящейся в камере сгорания, турбулентность потока. В результате повышения скорости газовой смеси и турбулизации повышается химическая реакция между молекулами
СН4 и O2, т.е. интенсифицируется скорость сгорания смеси. Повысить интенсивность источника зажигания можно так-
же двумя способами:
1.Устанавливают мощный электроимпульсный источник зажигания.
2.Встраивают форкамерное зажигание, например конструкцию (рис. 11.4). Камера сгорания 1 имеет перегородку 2,
вкоторой имеется два и более отверстий 3. После подачи газа
вкамеры последний с помощью вентилятора 4 перемешивается и воспламеняется свечой 5, находящейся в камере А. Поскольку объем камеры А намного меньше объема камеры В, в камере А смесь быстро сгорает и создается повышенное давление. Пламя горения переходит в камеру В, поджигая смесь сразу в нескольких местах.
Врезультате скорость горения и градиент давления dp/dt намного повышаются. Регулируя площадь проходных отверстий
вперегородке, можно регулировать режим работы установки.
215
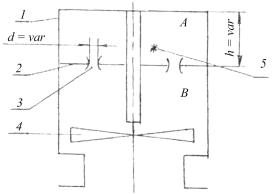
Рис. 11.4. Схема камеры сгорания с форкамерным зажиганием и встроенным вентилятором (А – форкамера; B – основная камера сгорания)
На практике наибольшее применение нашел способ регулирования рабочего процесса путем применения вентилятора с переменным числом оборотов. Хороший результат показал также способ интенсификации рабочего процесса с применением звукового генератора [19].
Требования к смесям и модельно-опочной оснастке при применении газоимпульсной формовки
Учитывая разносторонние технологические требования
кформовочной смеси, рекомендуется применять следующий состав и свойства формовочной смеси для импульсных способов уплотнения [19] (табл. 11.1).
Установлены наиболее оптимальные параметры для импульсных процессов: влажность 3,2 %; начальная плотность 0,75 г/см3; уплотняемость в пределах 40–45 %. Требования импульсных способов к свойствам смеси обуславливают повышенное внимание
ксистемам подготовки, смесеприготовления и транспортирования.
При применении импульсных способов уплотнения не существует ограничений по высоте опоки. Однако чем меньше высота опоки, тем больше должен быть импульс, что не всегда
216
можно достигнуть при той или иной конструкции импульсной установки, в частности, конструкции быстродействующего воздушного клапана. Поэтому практикой не рекомендуется уплотнять опоки менее 200 мм. Исходя из требований к пониженной начальной плотности смеси, высота наполнительной рамки должна быть 2/3 от высоты опоки. При газоимпульсном уплотнении давление смеси на модельную плиту достигает 0,5–0,8 МПа, а на стенки опоки – 0,4–0,6 МПа. Требования к опокам по жесткости и прочности такие же, как и для прессования. Чистота поверхности опок не ниже 5 класса точности, Rz = 2,5.
Таблица 11.1
Рекомендуемый состав и свойства формовочной смеси для импульсных способов уплотнения
Содержание, % |
|
пылевидного материала |
13–14 |
активной глины |
8,5–9,0 |
песка |
1,8–2,3 |
Содержание влаги, % |
3–3,5 |
Предел прочности на сжатие по сырому, σсж, кПа |
190–205 |
Предел прочности на срез, σср, кПа |
40–47 |
Отношение прочности при протяжке (раздавливании) |
0,16–0,18 |
σразд/ σсж по сырому |
|
Газопроницаемость, ед |
95–110 |
Уплотняемость, % (по Фишеру) |
38–45 |
Высокая интенсивность протекания процесса импульсного уплотнения требует в массовом производстве применения модельной оснастки повышенной жесткости по сравнению с традиционным встряхивающе-прессовым способом. При единичном изготовлении форм возможно применение деревянных моделей. Для обеспечения качественной вытяжки формы на болванах рекомендуется устанавливать венты. Места расположения вент и их количество, как правило, определяются опытнымпутем.
Требования к оснастке при ГИФ аналогичны требованиям ВИФ.
217
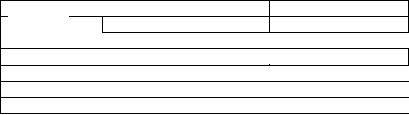
11.2. Рабочий процесс в камере газоимпульсной установки
Наибольшее практическое применение в газоимпульсной формовке нашел процесс сгорания метано-воздушной смеси.
В табл. 11.2 [28] представлены параметры расчета стехиометрического сгорания метано-воздушной смеси.
Таблица 11.2 Состав горючей смеси в молях СH4 + α(2O2 + 7,52N2)
Теплота сгорания, кДж/моль |
814,2 |
|
Дозировка |
об.% |
9,5 |
|
г/м3 |
67,8 |
Давление дозировки, МПа |
0,1105 |
|
Давление продуктов сгорания, МПа |
0,97 |
|
Температура продуктов сгорания, К |
2585 |
|
Содержание СО, об.% |
1,8 |
Стехиометрическое уравнение реакции горения углеводородных газов имеет вид:
|
m |
= nCO2 + |
m |
H2O + Q, |
(11.1) |
|
CnHm + n + |
4 |
O2 |
2 |
|||
|
|
|
|
|
где n и m – соответственно количество атомов углерода и водорода в молекуле углеводорода.
При полном сгорании горючих газов и теоретическом объеме воздуха продукты сгорания содержат СO2, N2, Н2O.
Из табл. 11.2 видно, что давление продуктов сгорания ме- тано-воздушной смеси в камере составляет 0,97 МПа. Эксперименты показывают, что в действительности оно ниже и составляет 0,7–0,75 МПа и только в тех случаях, когда эксперименты проводятся с пустой опокой. Если в опоке имеется формовочная смесь, то максимальное давление достигает лишь величины 0,5– 0,6 МПа. Это объясняется различными тепловыми потерями.
218
11.3. Баланс энергии сгорания газовоздушной смеси
Запишем баланс полной энергии сгорания смеси в рабочей камере газовоздушной установки [12] Qполн:
Qполн = Qупл + Qфор + Qт + Qзап + Qст, |
(11.2) |
где Qупл – энергия, затраченная на работу уплотнения смеси; Qфор – потери энергии на уход в атмосферу и в форму несгоревших газов, на фильтрацию газов, а также потери, отданные теплотой верхнему слою смеси; Qт – потери энергии на конвективный теплообмен и теплообмен через излучение; Qзап – потери энергии на запыленность в камере сгорания; Qст – потери энергии, ушедшей на нагрев стенок камеры.
Полная энергия сгорания газовоздушной смеси определяется выражением [32]
|
pгорVк |
|
p V |
|
|
||
Q = |
|
|
− |
0 к |
, |
(11.3) |
|
γпр −1 |
γ−1 |
||||||
|
|
|
|
где ргор – теоретическое давление продуктов сгорания в замкнутом объеме; Vк – объем камеры сгорания; γпр = 1,3 – показатель адиабаты продуктов сгорания при высоких температурах; γ – показатель адиабаты при нормальных условиях (γ = 1,4); р0 – атмосферное давление.
На уплотнение формы затрачивается энергия
Eупл = δ0·Vсм·W, |
(11.4) |
где δ0, Vсм – начальная плотность и объем формовочной смеси, подлежащей уплотнению в данной оснастке; W – удельный энерговклад в уплотнение смеси.
Установлено, что до 65 % энергии, запасенной в горючей газовой смеси, теряется на охлаждение газа в верхнем слое формы и уход в форму несгоревшего газа (Qфор).
Конвективный теплообмен газа со стенками камеры и дефлектора не успевает привести к большим потерям энергии на
219
стадии уплотнения формы, но в целом этот канал расхода играет важную роль в общем энергобалансе. Известно, что при стехиометрическом сгорании метана в воздухе образуется 19 % Н2O и 9,5 % СO2. Известно также, что трехатомные молекулы достаточно легко возбуждаются уже при температурах порядка 2000 °С. В этом случае тепловое излучение возбужденных молекул достигает стен камеры и дефлектора и поглощается ими. Потеря теплоты на теплообмен излучением в три раза превышает потери теплоты на конвективный. Однако установлено [32], что уже при незначительном уменьшении температуры сгорания излучательный теплообмен со стенками установки существенно замедляется (~Т4). Суммарный расход энергии на конвективный излучательный теплообмен со стенками составляет ~ 3 % (на стадии уплотнения формы).
Во время смешения вентилятором горючего газа с воздухом с поверхности неуплотненной формы сдуваются и увлекаются внутрь камеры сгорания частицы кварцевой пыли и глины, которые и поглощают значительное количество энергии. Эти потери энергии достигают в отдельных случаях до 40 %.
Кроме больших потерь энергии, запыленность потока приводит к нестабильности зажигания газовоздушной смеси, так как частицы пыли отбирают тепло от очагов зажигания и горение в определенное время может прекратиться. Смачивание верхнего слоя формы перед уплотнением и установка разделительной сетки между камерой сгорания и модельной оснасткой являются существенной мерой по предотвращению запыленности внутри камеры и повышению ее эффективности. Что касается нагрева конструкций формовочной установки, то можно заметить лишь следующее: при нормально работающих режимах температура стенок камеры не превышает 50–55 °С, а стенок
дефлектора 70–80 °С, что не оказывает заметного |
влияния |
на стабильность работы установки и отрицательного |
влияния |
на окружающую среду. |
|
220 |
|