
книги / Оборудование литейных цехов
..pdf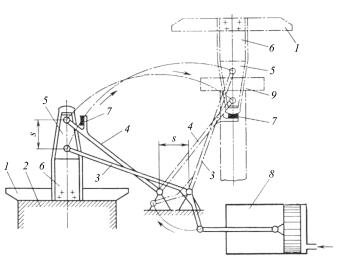
схема механизма поворота плиты (имеющей неподвижные по высоте опоры) с помощью качающегося пневмоцилиндра и системы рычагов, а на рис. 4.33, б в двух положениях (нижнем и верхнем) показан механизм цепного поворота для плиты, перемещающейся по вертикали во время поворота.
Перекидные столы являются характерными узлами для встряхивающих машин крупного размера. Типичным для целого семейства таких машин (для опок крупных размеров) является рычажный механизм поворота перекидного стола (рис. 4.34).
а |
б |
Рис. 4.34. Схема рычажного поворотного механизма перекидного стола: а – положение перед поворотом; б – положение после поворота; 1 – перекидной стол; 2 – встряхивающий стол; 3 – ведущий рычаг поворотного механизма; 4 – направляющий рычаг; 5 – призма; 6 – боковина перекидного стола; 7 – упор; 8 – пневмогидравлический цилиндр поворотного механизма; 9 – приемный стол вытяжного
механизма
Поворотный механизм состоит из двух пар рычагов 3 и 4, по паре на каждой стороне машины. Расстояния s между неподвижными точками вращения каждой пары рычагов и между их
131
подвижными шарнирами на других их концах одинаковы. Поэтому при повороте ведущего рычага 3 от кривошипного механизма с помощью пневмогидравлического цилиндра поворота 8 перекидной стол по пути своего переноса в показанное штриховыми линиями положение поворачивается на 180° вокруг горизонтальной оси. Находящаяся на перекидном столе набитая полуформа становится теперь в положение б для вытяжки модели, которая и осуществляется с помощью вытяжного механизма 9. При встряхивании же (в положении а) перекидного стола (вместе с находящейся на нем модельной плитой и опокой) рычаги 3 и 4 остаются неподвижными, так как призма 5, с которой сочленены их концы, допускает подъем перекидного стола при встряхивании, а сама остается неподвижной. Чтобы эта призма не вышла из своего гнезда, в боковине перекидного стола в положении б имеются упоры 7, по одному на каждом направляющем рычаге 4. Эти упоры и поддерживают перекидной стол на цилиндрических поверхностях его боковин, или щек, как показано штриховыми линиями на рис. 4.34.
Приемные столы встряхивающих формовочных и стержневых машин с поворотной плитой и с перекидным столом снабжают так называемыми нивелирующими механизмами. Назначение нивелирующего механизма – обеспечить вытяжку модели из формы при неправильной тыловой поверхности опоки или неровном подопочном щитке. Если такую опоку (рис. 4.35, а) опускать на жесткий приемный стол, то она повернется около своего выступающего ребра А; произойдет перекос формы относительно модели и обрыв формы или образование трещин. Поэтому приемный стол снабжают приспособлением в виде двух (или более) брусков, опирающихся на пружины или другие податливые опоры. При соприкосновении опоки с брусками они «приспосабливаются» к неправильной тыловой поверхности опок и прилегают к ней. Далее с помощью особого устройства приемные бруски жестко фиксируются в этом положении, и опока при вытяжке модели уже остается неподвижной относи-
132
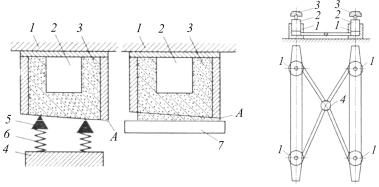
тельно приемного стола. Несмотря на неправильную тыловую поверхность опоки или неровный подопочный щиток, на который онапринимается, перекоса формы относительно модели не будет.
Нивелирующие механизмы необходимы в машинах с поворотной плитой или с перекидным столом, не имеющих подпрессовки формы после встряхивания. В случае же подпрессовки подопочный щиток, которым на таких машинах доуплотняется форма после встряхивания, упрется в выступающее ребро А опоки (рис. 4.35, б) и дальше не пойдет. Нижняя плоскость щитка остается горизонтальной, и форма может быть принята на жесткий приемный стол без нивелирующего механизма.
а |
б |
|
|
|
|
|
|
Рис. 4.35. Принцип вытяжки модели на |
Рис. 4.36. Схема ниве- |
||||||
машине с поворотной плитой при |
лирующего |
механизма |
|||||
неправильной тыловой поверхности опоки: |
с |
четырьмя |
гидравли- |
||||
а – без подпрессовки; б – с подпрессовкой; |
ческими |
цилиндрами: |
|||||
1 – поворотная плита; |
2 – модель; |
1 |
|
– гидравлические |
|||
3 – опока; 4 – приемный стол; 5 – бруски |
цилиндры; 2 – поршни; |
||||||
нивелирующего механизма; 6 – пружины |
3 |
– |
приемные |
брусья; |
|||
брусков; 7 – подопочный (подпрессовочный) |
4 |
– |
кран |
для |
отсечки |
||
щиток |
|
сообщения |
|
гидроцилин |
|||
|
|
|
дров между собой |
Нивелирующие механизмы делают разнообразных конструкций: с податливыми опорами приемных брусьев на пружинах и подпружиненных рычагах с фиксацией их запорными ру-
133
коятками, пневмоцилиндрами, клиньями и пр. На рис. 4.36 показан нивелирующий механизм с четырьмя вертикальными гидроцилиндрами, на поршни которых опираются два приемных бруса. Масляные пространства всех четырех цилиндров сообщаются между собой, поэтому приемные брусья свободно подаются под принимаемой формой и устанавливаются, приспосабливаясь к ее тыловой поверхности. Затем цилиндры разъединяются между собой и, будучи изолированными, жестко фиксируют брусья в принятом ими положении.
Вопросы для повторения
1.Классификация встряхивающих формовочных машин.
2.Преимущества и недостатки процесса уплотнения встряхиванием и встряхивающих формовочных машин.
3.Механизм процесса уплотнения встряхиванием.
4.Уравнение движения стола. Влияние жесткости упругих прокладок на силу удара и ускорение стола.
5.Параметры удара: скорость падения стола, высота встряхивания и частота ударов, их среднее численное значение.
6. Отличие встряхивающего механизма с амортизацией
ибез амортизации удара.
7.В каком случае мощность встряхивающего механизма выше (в случае амортизации или без нее) при одинаковом размере опок?
8.Способы амортизации ударов во встряхивающих формовочных машинах.
9.Роль воздухоподводящей системы встряхивающего механизма, эффективность его работы.
10.Что такое коэффициент расхода воздухоподводящей системы встряхивающего механизма, его численное значение?
11.Способы воздухораспределения во встряхивающих формовочных машинах.
12.Зачем применяют во встряхивающих машинах нивелирующие механизмы?
134
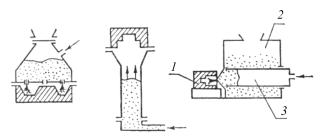
13.Влияние величины безударной нагрузки на эффективность работы встряхивающего механизма.
14.Принцип расчета диаметра цилиндра встряхивающего механизма.
15.Необходимое число ударов во встряхивающих формовочных машинах.
16.Рабочие процессы при встряхивании.
17.Определение индикаторного расхода воздуха.
18.Определение сечениявпускных и выхлопных отверстий.
19.Способы автоматического регулирования уплотнения при встряхивании.
5.ПЕСКОДУВНЫЕ ФОРМОВОЧНЫЕ ЛИТЕЙНЫЕ МАШИНЫ
5.1. Классификация пескодувных формовочных литейных машин
Пескодувные машины можно классифицировать по следующим признакам: а) принципу работы; б) направлению дутья; в) назначению.
а |
б |
в |
Рис. 5.1. Пескодувные машины с различным направлением дутья
По принципу работы пескодувные машины подразделяются на собственно пескодувные и пескострельные.
135
По направлению дутья различают машины с верхним (рис. 5.1, а), нижним (рис. 5.1, б) и боковым (рис. 5.1, в) дутьем.
Машины с верхним дутьем получили наибольшее распространение, так как конструктивно наиболее просты и легко вписываются в автоматические линии.
Машины с нижним дутьем встречаются значительно реже. Они применяются главным образом для изготовления оболочковых форм и стержней из песчано-смоляных смесей в нагретых ящиках. В этом случае после снятия давления смесь, не успевшая затвердеть внутри ящика, падает вниз в резервуар машины.
Машины с боковым дутьем также встречаются редко. Отличительная особенность их та, что рабочий резервуар 3 периодически заполняется смесью из основного резервуара 2, а затем прижимается к стержневому ящику 1. При вдувании смеси в ящик давление воздуха распространяется не на весь объем смеси в основном резервуаре, а только на небольшую ее часть, заключенную в рабочем резервуаре.
По назначению пескодувные машины подразделяют на стержневые и формовочные.
Стержневые машины выполняются с различным направлением дутья и по принципу работы могут иметь как пескодувный, так и пескострельный механизм уплотнения.
Пескострельные стержневые машины, в свою очередь, можно разделить на две большие группы: машины для изготовления стержней с последующим отверждением их тепловой сушкой на плитах; машины для изготовления стержней с отверждением непосредственно в стержневой оснастке (ящиках).
Во второй группе стержневых машин можно выделить: а) машины для изготовления стержней в нагреваемой оснастке; б) машины для изготовления стержней из холоднотвердеющих смесей; в) машины для изготовления стержней с отверждением их путем продувки углекислым газом.
Благодаря достоинствам (повышенная точность получаемых стержней, значительное сокращение цикла их изготовле-
136
ния, ликвидация необходимости в применении сушильных плит, устранение армирования и др.) машины этой группы получают все большее распространение в условиях крупносерийного и массового производства. На базе этих машин созданы и работают поточные и автоматические линии, позволяющие в большой мере снизить трудоемкость изготовления стержней и повысить их качество.
5.2. Уплотнение формовочных и стержневых смесей пескодувным методом
При уплотнении смеси пескодувным способом сжатый воздух, поступая в резервуар 4 пескодувной машины (рис. 5.2, а), давит на формовочную или стержневую смесь, протекает через ее поры и увлекает за собой отдельные частицы. Вылетая из резервуара через вдувные отверстия 3, частицы смеси заполняют полость опоки или стержневого ящика 2, прижимаясь друг к другу силой воздушного потока. Отработанный воздух выходит из ящика через специальные вентиляционные отверстия 1.
Таким образом, сжатый воздух производит одновременно две операции: а) транспортирование смеси из рабочего резервуара в полость стержневого ящика или опоки; б) уплотнение смеси в объеме указанной оснастки.
Уплотнение смеси надувом происходит как за счет кинетической энергии пневмопесчаной струи, так и за счет перепада давления, возникающего при фильтрации воздуха, проходящего через неподвижный слой смеси в опоке или стержневом ящике.
Так как процесс надува весьма кратковременен, оба фактора, вызывающие уплотнение смеси, действуют практически одновременно, изменяется толькоих соотношение в течение процесса.
При проектировании пескодувных машин важно правильно выбрать тип рабочего резервуара и его размеры, определить оптимальное живое сечение вдувных отверстий и их количество, обеспечить хорошую вентиляцию ящика, способствующую равномерному уплотнению смеси.
137
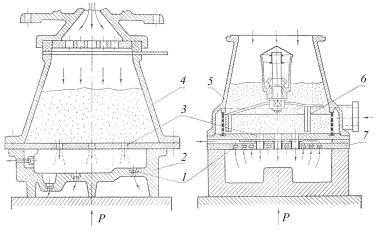
а |
б |
Рис. 5.2. Пескодувные резервуары: а – с нижней вентиляцией; б – с верхней вентиляцией
Воздух из ящика выходит через вентиляционные отверстия – венты, а смесь занимает его полость. Если воздух не будет вытеснен из ящика в определенное время и в данном направлении, то неизбежно образование неуплотненных участков в стержнях и их непригодность как детали для литейной формы.
Рассмотренный нами пескодувный резервуар имеет нижнюю вентиляцию. В резервуарах с верхней вентиляцией (рис. 5.2, б) воздушно-песчаная смесь вдувается в полость ящика через отверстие 3, а отработанный воздух выходит через вентиляционные отверстия1, расположенные в наружном днище7 резервуара5.
При такой системе вентиляции установка вент в модельной оснастке отпадает или же значительно сокращается.
Для разрыхления смеси и направления ее к вдувным отверстиям в резервуаре предусмотрена механическая мешалка 6.
Процесс уплотнения смеси пескострельным методом является разновидностью пескодувного, имеет много общего с ним и в то же время обладает рядом существенных особенностей.
138
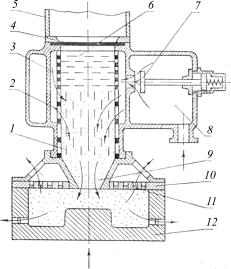
Истечение смеси из резервуара в стержневой ящик при пескострельном методе происходит мгновенно, напоминая выстрел. Это объясняется сужением потока в конической насадке 9 на выходе из резервуара (рис. 5.3) и небольшим уплотнением смеси под действием давления сжатого воздуха с последующим выбросом непрерывно образующихся комков в ящик. Смесь из бункера 5 поступает в резервуар 3 при открытом шибере 4, управляемом пневмоцилиндром. Сжатый воздух через вдувной клапан 7, горизонтальные 6 и вертикальные 1 прорези входит во внутреннюю полость гильзы 2, отделяя от ее стенок смесь.
Рис. 5.3. Пескострельный резервуар
Как и в пескодувном резервуаре с верхней вентиляцией, вдувная плита 10 является универсальной: имеет вентиляционные отверстия 11 для отвода воздуха из полости стержневого ящика 12. Резервуар выполнен в одном блоке с ресивером 8, обеспечивающим мгновенную подачу больших порций воздуха в рабочий резервуар машины.
139
Как показали исследования (ВНИИлитмаш), характер перемещения смеси внутри резервуара зависит главным образом от соотношения суммарных площадей сечения прорезей в верхней и нижней частях гильзы. Оптимальным является такое соотношение, при котором режим истечения характеризуется постоянной плотностью столба смеси.
Процесс формирования стержня условно можно разделить на два этапа.
На первом этапе ящик заполняется смесью из насадка резервуара, причем истечение ее в этот период происходит при небольшом давлении воздуха. Заполнение ящика и предварительное уплотнение смеси в большинстве случаев заканчивается до того, как давление воздухаврезервуаре достигнет максимума.
На втором этапе стержень окончательно уплотняется за счет выдавливания дополнительной порции смеси под действием разности давлений воздуха в резервуаре и ящике. Эта дополнительная порция, выпрессовываясь из насадка, принимает форму кома, уплотняющего смесь, находящуюся в стержневом ящике.
Конструктивные параметры резервуаров пескострельных машин должны обеспечивать неизменную плотность смеси при истечении и благоприятные условия для образования прессующего кома. Пескострельные машины имеют ряд преимуществ перед пескодувными: степень уплотнения в них значительно выше и распределение ее по высоте ящика более равномерно; расход воздуха примерно в 3–5 раз ниже, чем у пескодувных; меньше абразивное действие частиц смеси на стенки ящика; пескострельные головки конструктивно проще по сравнению с пескодувным резервуаром.
Следует также отметить преимущество пескострельных машин при использовании термореактивных быстротвердеющих смесей, формуемость которых ухудшается при длительном контакте с воздухом.
140