
книги / Оборудование литейных цехов
..pdf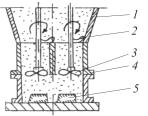
ность плотности в слое увеличивается под ребрами и между ребрами. В конечном счете толщина ребра определяется его прочностью и жесткостью. Шаг решетки выбирается в зависимости от требуемой твердости лада и толщины ребер. С увеличением толщины ребер шаг следует увеличивать.
Решетку во время работы периодически очищают вибрацией от оставшейся смеси. Метод уплотнения решеткой нашел применение только для мелких опок (до 0,7 м2) [35].
3.10.Прессование лопастной головкой
Вформовочных машинах, основанных на лопастном прес-
совании, между бункером 1 и модельным комплектом 5 (рис. 3.15) имеется плита 1 с направляющими цилиндрами по
числу лопастей. Лопасть 3 имеет |
||
винтовую поверхность и жестко |
||
закреплена на валу. При враще- |
||
нии вала уплотняющие |
лопасти |
|
захватывают формовочную смесь |
||
из бункера, |
подают се |
в опоку |
и уплотняют |
равномерно |
до не- |
обходимой плотности. Для того |
Рис. 3.15. Схема прессования |
|
чтобы смесь не зависала в бунке- |
лопастнойголовкой: 1 – бункер; |
|
рах, на валах смонтированы спе- |
2 – лопасть-рыхлитель; 3 – |
|
рабочая лопасть; 4 – плита; |
||
циальные лопасти-рыхлители 2. |
||
5 – модель |
||
В лопастной головке операции |
||
|
засыпки и уплотнения совмещены, благодаря чему отпадает необходимость в наполнительной рамке и дозаторе. Уплотнение смеси происходит практически бесшумно, а степень уплотнения легко регулируется силой тока в электроприводе уплотняющих элементов.
Диаметр лопастей 150–350 мм, а угол их наклона α = 5…10. Число рабочих органов в головке колеблется от 2 до 12 (в зависимости от габаритов опоки). В некоторых конструкциях вал
41
с лопастью по мере уплотнения перемещается в вертикальном направлении. Время уплотнения одной полуформы А = 180 мм составляет 8–10 с. Трение скольжения лопастей по смеси повышает энергоемкость процесса и вызывает быстрое изнашивание лопастей.
Сцелью повышения срока службы уплотняющих лопастей
иснижения энергозатрат применяют конические ролики. Давление прессования в конце уплотнения составляет ≈0,5 МПа. Твердость на контрладе под рабочим органом 90 ед., а на ладе 80–85 ед. В углах формы твердость уменьшается до 70 ед. Действие касательных напряжений при уплотнении приводит к тому, что смесь перемещается в ту часть формы, где по каким-либо причинам оказалась слабоуплотненной.
Лопастное прессование используется для изготовления форм размером от 400×320×100 до 1350×1200×160 мм.
3.11. Силовые приводы прессовых формовочных машин
По конструкции силового привода прессовые формовочные машины подразделяются: на машины с пневматическим, гидравлическим, пневмогидравлическим и электромагнитным приводом. Прессовые силовые приводы могут располагаться как в нижней части машины, так и в верхней. Машины с верхним расположением прессового привода делают реже, чем с нижним. Верхнее расположение привода применяют в случае использования гидросистемы.
Пневматический привод прессовых формовочных машин
Пневматический привод прессовой формовочной машины представляет собой обычный пневмоцилиндр большого диаметра, имеющий малый ход (рис. 3.16) С целью простоты обработки и повышения точности поршни большого диаметра 1 выполняют плавающими, т.е. не имеющими жесткого соединения со штоком или стаканом прессового стола 2. В этом случае не тре-
42
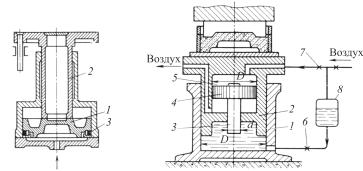
буется строгая соосность цилиндра и направляющих поверхностей для скольжения стакана.
Рис. 3.16. Схема конструкции |
Рис. 3.17. Схема |
пневматического прессового |
пневмогидравлического |
цилиндра большого диаметра: |
усилителя (мультипликатора) |
1 – плавающий поршень; |
|
2 – направляющий стакан |
|
прессовогостола; 3 – резино- |
|
вое саморазжимающееся |
|
уплотнительное кольцо |
|
Пневмогидравлический привод прессовых формовочных машин
Для получения повышенных (1–2 МПа) и высоких (2–4 МПа) давлений прессования используют пневмогидравлические усилители или мультипликаторы (рис. 3.17).
В цилиндр 1 под давлением сжатого воздуха из сети подается масло из бака 8 (кран 6 открыт, а кран 7 закрыт), которое давит на поршень 2 и поднимает его, перемещая при этом вверх стол с модельно-опочной оснасткой и смесью. По достижении поршнем определенной высоты, соответствующей моменту соприкосновения прессовой колодки со смесью в наполнительной рамке и некоторому ее уплотнению, открывается кран 7 и закрывается кран 6. Воздух из сети попадает в полость 5, давит на
43
поршень 4, который, перемещаясь вниз, оказывает через плунжер 3 давление на масло в цилиндре 1. Так как масло практически несжимаемо, то давление на поршень 2 увеличится пропорционально отношению площадей поршня 4 и плунжера 3. Плунжер 3 погрузится в масло на небольшую высоту. Объем масла, вытесненного плунжером при погружении, будет равен дополнительному объему, который получится в результате дальнейшего движения смеси в наполнительной рамке и окончательного ее уплотнения. Таким образом, конечное давление масла
pк (πd 2 / 4)= p0 (πD2 / 4),
или
pк = p0 (D2 / d 2 )= ky p0 , |
(3.3) |
где p0 – начальное давление масла, равное давлению воздуха в магистрали; d – диаметр плунжера; D – диаметр вспомогательного цилиндра; kу – коэффициент усиления, kу = D2/d2.
Усилие прессования
pпр = pк (D12 / 4)= p0ky (πD12 / 4). |
(3.4) |
Пневмогидравлические усилители рациональнее применять при небольших по высоте перемещениях ствола машины.
Гидравлический привод прессовых формовочных машин
С целью уменьшения габаритных размеров машины и повышения плавности хода стола очень часто в прессовых формовочных машинах применяют индивидуальный гидропривод с давлением масла 5–10 МПа.
Гидропривод прессовой формовочной машины состоит из гидронасоса 1, гидроцилиндра 2 и системы маслопроводов 3
(рис. 3.18, а).
44
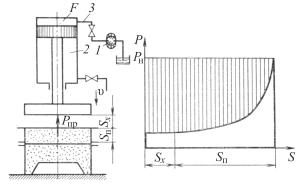
Работа гидропривода прессовых формовочных машин характеризуется переменной нагрузкой в процессе рабочего цикла. После включения гидропривода прессовая плита сначала проходит свободный участок Sx без внешнего сопротивления, а затем производит прессование на глубину Sп. При прохождении участка привод не испытывает большого сопротивления. Только
вконце процесса уплотнения нагрузка резко увеличивается, давление в гидросистеме и мощность, развиваемая приводом, также возрастают. Процесс уплотнения заканчивается, когда давление
всистеме и мощность достигнут номинальных значений. Продолжительность процесса прессования для данного случая
t = s / v = (Sx + Sn )F / (Qнη0 ), |
(3.5) |
где v – скорость движения прессовой колодки; F – площадь поршня; Qн – объемная подача насоса; η0 – объемный КПД, η0 = 0,8…0,9.
аб
Рис. 3.18. Схема гидропривода прессовой формовочной машины (а) и нагрузочный график (б)
Мощность привода N = pнQн, как это видно на схеме (рис. 3.18, б), на большей части пути прессования используют незначительно (заштрихованная область характеризует неиспользованную мощность привода). Для повышения коэффициента использования установленных мощностей применяют схе-
45
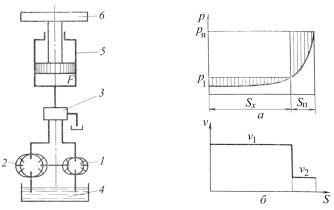
мы с несколькими ступенями изменения скорости. Когда нагрузка мала, скорость рабочего органа увеличивают, а при увеличении нагрузки скорость уменьшают. Таким образом, мощность привода в начале прессования повышается вследствие увеличения скорости прессования. Такое регулирование скорости обеспечивается приводомсдвумя насосамиразнойподачи (рис. 3.19).
У насоса 2 (см. рис. 3.19) большая подача Qн2 и низкий напор p1, а у насоса 1 – малая подача Qнl и высокий напор p2. Сначала в прессовый цилиндр площадью F подают жидкость оба насоса, сообщая высокую скорость v1 (м/с) прессовой плите
(рис. 3.20, б):
v1 = (Qн1 + Qн2 )η01 / F, |
(3.6) |
где η01 – объемный КПД насосов при совместной работе на первом участке прессования; F – площадь прессового поршня.
Рис. 3.19. Схема гидропривода |
Рис. 3.20. Характеристики |
прессовой формовочной машины с |
работы гидропривода прессовой |
двумя насосами: 1 – насос низкой |
формовочной машины с двумя |
производительности; 2 – насос |
насосами: а– степеньиспользования |
высокой производительности; 3 – |
мощности насосов; б – скорость |
система управления; 4 – бак для |
прессовой плиты в зависимости |
масла; 5 – гидроцилиндр; 6 – стол |
от пути перемещения |
формовочной машины или |
|
прессовая плита |
|
46 |
|
С такой скоростью плита пройдет путь Sx (рис. 3.20, а). При достижении напора p, насос 2 (см. рис. 3.19) отключится на слив. Дальнейшее прессование на пути Sn до конечного напора р2 осуществляется только насосом 1 с меньшей скоростью
(рис. 3.20, б):
v2 = (Qн1 / F )η02 , |
(3.7) |
где η2 – объемный КПД насоса 1 на втором участке прессования. При такой работе привода степень использования его повышается (заштрихованная область на рис. 3.20, а составляет небольшую часть площади над кривой нагрузки в отличие от такой же области на рис. 3.18, б). В этом случае продолжитель-
ность процесса прессования также уменьшается:
t2 = |
Sx F |
+ |
SпF |
, |
(3.8) |
(Qн1 + Qн2 )η01 |
Qн1η02 |
||||
Минимальная продолжительность процесса |
достигается |
в том случае, если напор и подача насосов выбраны из условия
x = Q |
/ |
( |
Q |
+ Q |
( |
η / η |
2 ) |
= p / p |
2 |
= 0,1...0,2. |
(3.9) |
н1 |
|
н1 |
н2 ) |
1 |
1 |
|
|
Существуют также насосы, у которых напор и подача регулируются плавно по закону
pнQн = const. |
(3.10) |
При малом напоре насос развивает высокую подачу (начало прессования), а при повышении напора подача насоса, а значит, и скорость прессовой плиты уменьшаются.
Электромагнитный привод прессовых формовочных машин
Плавный прогрессивный рост силы по ходу прессового стола можно также получить с помощью электромагнита (рис. 3.21). Сила прессования непрерывно возрастает с уменьшением зазора
47
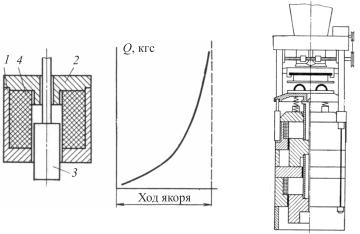
между якорем и статором. На рис. 3.22 приведена схема компоновки построенного по этому принципу опытного прессового формовочного автомата, имеющего два силовых прессующих электромагнита, работающих по схеме тандем.
аб
Рис. 3.21. Электромагнит с плоскими Рис. 3.22. Схема компоновки торцамиякоряистатора(а) иростсилы электромагнитного прессового
по ходу якоря (б): 1 – сердечник; 2 – |
автомата. Размеры опок |
статор; 3 – якорь; 4 – катушка |
500×400×150 мм. Усилие |
|
прессования 40 тс |
3.12. Траверсы
Траверсы прессовых механизмов современных формовочных машин делают четырех типов: 1) поворотные в виде консольной балки; 2) поворотные в виде балки на двух опорах; 3) в виде тележки и 4) неподвижные.
Траверса в виде консольной балки схематически показана на рис. 3.23 в трех вариантах. Для возможности насыпания формовочной смеси в опоку из бункера и для съема заформованной опоки с машины траверса поворачивается около вертикальной колонны. Воспринимая большую силу прессования
48
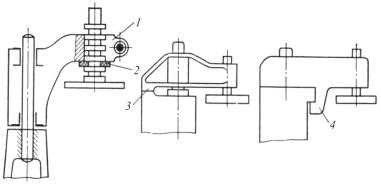
иработая на изгиб по схеме консольной балки, траверса данного типа должна иметь достаточно большой момент сопротивления. Для формовки крупных опок такие траверсы получаются громоздкими, и поэтому обычно их применяют только для небольших машин.
На схемах (см. рис. 3.23, а–в) приложенный к траверсе изгибающий момент от силы прессования гасится моментом сил: а – реакции в подшипниках; б – реакции в дополнительной опоре на хвостовике траверсы; в – реакции, возникающей при зацеплении за выступ станины крюкообразного прилива траверсы.
Схема поворотной траверсы, работающей как балка на двух опорах, приведена на рис. 3.24. Вторая опора представляет собой тягу с головкой, зацепляемой за выступ станины. Траверсы такого типа применяют для прессовых механизмов формовочных машин средних и больших размеров. Эти траверсы, как
итраверсы первого типа, наиболее распространены.
Для осуществления поворота траверсы описанного типа обычно применяют механизм с пневмоцилиндром, схема которого приведена на рис. 3.25, а.
а |
б |
в |
Рис. 3.23. Варианты поворотной траверсы в виде консольной балки: 1 – клемма; 2 – разрезноевкладноекольцо; 3 – хвостовик; 4 – крюкообразный выступ траверсы
49
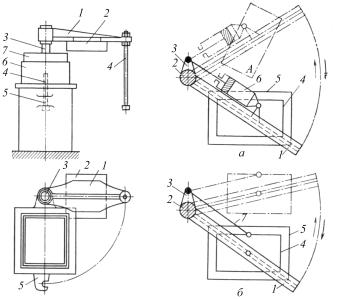
Рис. 3.24. Схема поворотной |
Рис. 3.25. Схемымеханизирован- |
|||||
траверсы в виде балки на двух |
ных |
поворотных |
траверс: |
а – |
||
опорах: 1 – траверса; 2 – прессо- |
с поворотом от пневматического |
|||||
вая колодка; 3 – колонна машины; |
цилиндра; б – с параллельным |
|||||
4 – дополнительная опора (тяга); |
перемещением прессовой колод- |
|||||
5 – выступ станины; 6 – опока; |
ки; |
1 – траверса; |
2 – колонна; |
|||
7 – наполнительная рамка |
3 – кронштейн колонны; |
4 – |
||||
|
прессовая |
колодка; |
5 – |
стол |
||
|
машины; 6 – пневматический |
|||||
|
цилиндр |
поворота |
траверсы; |
|||
|
7 – тяга, поворачивающая прес- |
|||||
|
совую колодку |
относительно |
||||
|
|
|
траверсы |
|
|
При неподвижном креплении прессовой колодки к траверсе последнюю приходится поворачивать в нерабочее положение до тех пор, пока угол А колодки не выйдет за габариты стола машины. Для уменьшения угла поворота траверсы можно прессовую колодку сделать поворачивающейся отно-
50