
книги / Электронно-лучевая обработка в сварке
..pdf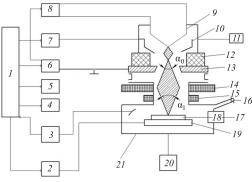
Рис. 1.2. Схема современного процесса электронно-лучевой обработки материалов: 1 – компьютер; 2 – узел перемещения объекта; 3 – устройство контроля; 4 – блок отклонения луча; 5 – блок фокусировки; 6 – высоковольтный выпрямитель; 7, 8 – блок питания модулятора 10
и |
катода 9; 10, 20 – системы откачки пушки и рабочей камеры; |
|
12 |
– изолятор; 13 – анод; 14 – фокусирующая линза; 15 – катушка |
|
отклонения; 16 – система контроля; 17 |
– объект; 18 – вакуумный шлюз; |
|
19 |
– механизм перемещения; 21 – |
вакуумная камера; α0 – угол |
|
расходимости и α1 – угол сходимости электронного луча |
В зависимости от ускоряющего напряжения, как правило, меняется и материал катода. При низких и промежуточных ускоряющих напряженях применяются катоды из гексаборида лантана с косвенным подогревом. В пушках с высоким ускоряющим напряжением используются прямонакальные металлические катоды, которые чаще всего выполняются в виде плоских спиралей из вольфрамовой проволоки или в виде полосок из тантала толщиной
0,1...0,2 мм и шириной 0,8...1 мм.
1.3. Установки для электронно-лучевой обработки материалов
Основными областями промышленного применения электрон- но-лучевого оборудования являются: сварка, плавка, испарение, размерная и термическая обработка материалов. Широкое исполь-
11
зование в промышленности перечисленных процессов привело к созданию большого числа электронно-лучевых технологических установок.
Электронно-лучевые технологические установки состоят из двух основных комплексов – энергетического и электромеханического. К энергетическому комплексу относится аппаратура, предназначенная для формирования пучка электронов с заданными параметрами, управления его мощностью и положением в пространстве. Электромеханический комплекс установки предназначен для герметизации и вакуумирования рабочего объема, выполнения всех установочных, транспортных и рабочих перемещений обрабатываемого изделия и электронной пушки [13].
Вакуумные камеры для электронно-лучевой обработки являются одним из наиболее важных узлов установки для электроннолучевой обработки. От их формы, конструкции, жесткости и габаритов зависят габариты и качество обрабатываемых за одну откачку изделий, удобство их загрузки и выгрузки, возможность пристыковки дополнительных объемов в нужном направлении и др.
По степени специализации различают два типа камер – универсальные и специализированные.
Универсальные камеры предназначены для обработки изделий любой формы и габаритов в пределах габаритов камеры. Такие камеры используются в единичном и мелкосерийном производстве и выпускаются в соответствии с принятыми параметрическими рядами. Это дает возможность выбрать камеры наиболее подходящих размеров применительно к конкретным изделиям.
Специализированные камеры неразрывно связаны с конструкцией и габаритами конкретного изделия или группы изделий. Часто специализированные камеры выполняют по форме обрабатываемого изделия.
Откачные системы служат для создания и поддержания в процессе работы высокого вакуума в ускоряющем промежутке электронной пушки и в вакуумной камере. Типовая схема откачной системы техно- логическойэлектронно-лучевойустановки приведена нарис. 1.3.
12
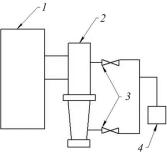
Рис. 1.3. Схема откачной системы установки для электронно-лучевой обработки: 1 – вакуумная камера; 2 – пароструйный высоковакуумный насос; 3 – вакуумные клапаны; 4 – форвакуумный механический насос
Откачная система состоит из механического насоса предварительного разряжения (форвакуумного насоса) и диффузионного паромасляного насоса, снабженного вакуумным затвором.
Предварительная откачка камеры выполняется форвакуумным насосом, а затем открывают затвор диффузионного насоса, и происходит откачка камеры до рабочих значений вакуума. Для повышения пропускной способности вакуум-проводов стремятся к их минимальной длине и возможно большему диаметру. Перегибы ваку- ум-проводов выполняют плавными с большими радиусами закруглений.
Манипуляторы предназначены для рабочих, установочных
итранспортных перемещений обрабатываемого изделия и электронной пушки. Они делятся на две основные группы – манипуляторы изделия и манипуляторы пушки. Первые являются непременным элементом практически любой установки для электроннолучевой обработки, а вторые используют в тех случаях, когда электронная пушка перемещается внутри вакуумной камеры.
Универсальные камеры предназначены для обработки изделий любой формы и габаритов в пределах габаритов камеры. Такие камеры используются в единичном и мелкосерийном производстве
ивыпускаются в соответствии с принятыми параметрическими ря-
13
дами. Это дает возможность выбрать камеры наиболее подходящих размеров применительно к конкретным изделиям.
По конструктивному исполнению манипуляторы подразделяются на универсальные (с большим количеством степеней свободы) и специализированные (для обработки конкретных изделий). Применение более сложных универсальных манипуляторов целесообразно при единичном и мелкосерийном производстве с частой сменой типа обрабатываемых изделий. Упрощенные сменные манипуляторы обычно приспосабливаются к конструкции конкретного изделия или группы однотипных изделий.
Универсальные манипуляторы изделия чаще всего выполняется в виде тележек, вращателей, двухкоординатных столов и т.п. Манипуляторы электронной пушки выполняются в виде шарнирнорычажных устройств, в виде направляющей траверсы, по которой перемещается каретка с шарнирно закрепленной на консоли пушкой, в виде двух- и трехкоординатных механизмов прямолинейного перемещения, а также в виде различного типа самоходных портальных механизмов.
Системы наблюдения, используемые при электронно-лучевой обработке, в большинстве случаев нуждаются в защите их от запыления парами обрабатываемых материалов.
В качестве защитных устройств применяются поворотные прозрачные экраны и прозрачные перемещаемые защитные пленки. В случаях особо интенсивных паровых потоков применяют стробоскопические устройства.
Смотровое окно, кроме прочного иллюминаторного стекла, содержит рентгеновское стекло, необходимое для защиты обслуживающего персонала от рентгеновского излучения из области взаимодействия электронного пучка с металлом.
Оптические устройства, увеличивающие объект наблюдения в 5...50 раз, могут быть независимыми и встроенными в конструкцию смотрового окна или электронной пушки.
Телевизионные системы дают возможность передавать изображение на большие расстояния и устанавливать передающую те-
14
левизионную камеру в непосредственной близости от электронной пушки.
Вспомогательные устройства и механизмы предназначены для выкатывания манипуляторов из вакуумной камеры (выдвижные платформы), для сборки изделий и других целей.
Электропривод в установках для электронно-лучевой обработки управляется как в ручном дистанционном режиме для простых систем, так и в автоматическом режиме для более сложных систем.
Управляющие функции могут выполняться с помощью компьютерных систем или средствами локальной автоматики. Наибольшее распространение в управлении электроприводами получили средства локальной автоматики, при этом локальная автоматика может быть выполнена как на релейно-контактной элементной базе, так и на базе интегральных микросхем или программируемых логических контроллеров.
Механизмы перемещения обрабатываемого изделия и электронной пушки долины работать или в режиме позиционирования, когда необходима высокая точность отработки и высокая точность позиционирования, или в режиме технологического перемещения, когда необходимы высокая стабильность скорости перемещения, высока динамичность и плавное регулирование скорости перемещения. Эти механизмы в основном располагаются внутри технологических вакуумных камер, в ограниченных объемах и работают в условиях тяжелых механических и тепловых нагрузок.
15
2. ТЕХНОЛОГИЯ ЭЛЕКТРОННО-ЛУЧЕВОЙ ОБРАБОТКИ КОНСТРУКЦИОННЫХ МАТЕРИАЛОВ
При осуществлении всех электронно-лучевых процессов электронный пучок используют в качестве энергоносителя, который
всоответствующем виде воздействует на обрабатываемый материал. Пучок генерируется в электронной пушке и через выходное отверстие пушки выводится в технологическую вакуумную камеру. В ней размещены или в нее вводятся объекты электронно-лучевого процесса – заготовки или материалы. Например, при плавке переплавляемый металл подают под пучок, а расплавленный стекает
втигель или кристаллизатор.
При напылении в рабочей камере, наряду с устройствами для подачи испаряемого материала, устанавливают приспособления для крепления и перемещения изделия, на поверхность которого производится напыление.
При встрече электронного пучка с веществом кинетическая энергия электронов пучка, взаимодействующих с атомами вещества, в результате ряда элементарных процессов превращается в другие формы энергии. При сварке, плавке, испарении и термической обработке используется возникающая при этом тепловая энергия. При нетермической обработке и других процессах химической электронно-лучевой технологии столкновения электронов пучка с атомами и молекулами возбуждают и ионизируют последние, вызывая химические реакции между ними. Эти эффекты воздействия электронного пучка на вещество и определяют области электроннолучевой технологии [2, 11, 13].
2.1. Испарение материалов
Испарение (точнее, испарительное осаждение) в вакууме является важным способом получения тонких пленок. Обширные исследования физических и прикладных свойств таких пленок и успехи
16
технологических разработок в этой области привели ко все возрастающему размаху их применения. Этому в немалой степени способствовало применение электронно-лучевого способа испарения материала в технике вакуумного нанесения покрытий.
Использование электронных пучков в процессах, связанных с испарением материалов, обусловлено особенностями распределения потоков энергии при нагреве этого материала. Если при других способах нагрева энергия подводится к испаряемой поверхности через стенку тигля и через испаряемый материал, то при электрон- но-лучевом испарении эта поверхность непосредственно нагревается бомбардирующими ее электронами. Такой способ подвода энергии дает электронно-лучевому испарению ряд преимуществ по сравнению с традиционными.
При прямом нагреве температура испаряемой поверхности наиболее высокая во всем устройстве. Поэтому при прямом нагреве возможно испарять материалы из водоохлаждаемых тиглей, применение которых иявляется характернымдляэлектронно-лучевого испарения.
Водоохлаждаемый тигель необходим при испарении химически высокоактивных, а особенно тугоплавких материалов. Элек- тронно-лучевое испарение материалов из охлаждаемых тиглей позволяет получать покрытия высокой чистоты, потому что почти полностью исключается реакция испаряемого материала с материалом тигля, а материал тигля и продукты реакций практически не испаряются. Другой вариант применения прямого нагрева, дающий возможность получать покрытия высокой чистоты, – бестигельное испарение.
Снизить тепловые потери тигля и тем самым повысить скорость испарения при хорошей степени использования энергии можно, применяя теплоизолирующие тигельные вставки.
Другим стимулом внедрения электронно-лучевого испарения является возможность, управляя электронным пучком во времени и пространстве, управлять тем самым и потоком энергии в испаряемое вещество и воздействовать на скорость испарения и распределение плотности потока пара.
17
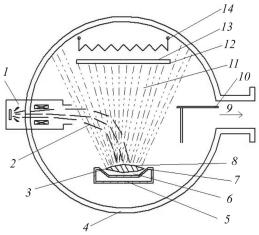
Общая характеристика процесса. Испарительное осаждение – это процесс вакуумного нанесения покрытий, при котором между испарителем и подложкой создается направленный поток пара. Поскольку генерация электронных пучков и их транспортировка также должны производиться в вакууме, применение электронных пучков для испарения материалов, вообще говоря, возможно без какихлибо дополнительных затрат на вакуумные откачные устройства. Принцип электронно-лучевого испарения пояснен на рис. 2.1.
Рис. 2.1. Принцип электронно-лучевого испарения материалов: 1 – электронная
пушка; 2 – электронный пучок; 3 |
– поверхность, бомбардируемая пучком; |
||||||
4 |
– |
кожух технологической |
камеры; 5 – водоохлаждаемый тигель; |
||||
6 |
– |
испаряемый материал; |
7 |
– |
расплавленная |
часть |
материала; |
8 |
– поверхность испарения; 9 |
– |
откачка вакуума; |
10 – |
диафрагма |
||
испарителя; 11 – поток паров; |
12 – напыляемый слой; 13 – подложка; |
||||||
|
|
14 – подогреватель подложки |
|
|
В основных чертах установка для электронно-лучевого испарения состоит из технологической камеры с системой откачки, тигля с испарямым материалом, электронной пушки, заслонки для пара и подложки с приспособлениями для ее крепления, а иногда – нагрева. В противоположность традиционным способам нагрева здесь
18
испаряемый материал нагревается вследствие прямой бомбардировки его поверхности электронным пучком. При этом существенная доля кинетической энергии электронов пучка превращается в тепло и поверхность нагревается до такой температуры, что становится источником пара. В этом потоке пара располагают подложку, на которую конденсируется часть пара, т.е. производится напыление. Испарительное устройство дополняют средствами измерения и контроля, которые особенно важны для управления параметрами пучка в процессе напыления.
Для того чтобы электронный пучок и поток пара распространялись в технологической камере беспрепятственно, давление в ней должно поддерживаться достаточно малым.
Это условие выполняется, если плотность частиц газа настолько мала, что столкновения частиц пара и электронов пучка с частицами остаточного газа относительно редки. В области, примыкающей к испарителю, вследствие высокой плотности пара его частицы взаимодействуют с электронами пучка. При этом как частицы пара, так и электроны изменяют направление движения. Кроме того, электроны теряют энергию, возбуждая и ионизируя пар.
Средняя длина свободного пробега частиц газа между двумя столкновениями при давлении 10–2 Па составляет около 500 мм. Для многих веществ приблизительно такова же средняя длина свободного пробега частиц пара в газе. Если при названных параметрах подложка удалена от испарителя на расстояние, например, 100 мм, то более чем 80 % частиц пара достигают подложки без столкновений с частицами газа. Следовательно, при данных условиях влияние газа на поток пара можно не учитывать.
Средняя длина свободного пробега электронов в газе примерно в 10 раз больше средней длины свободного пробега частиц газа между их столкновениями друг с другом. В большинстве устройств для испарения длина пути электронов такова, что уже при давлении газа 10–1 Па обеспечиваются достаточно малое рассеяние электронов в газе и достаточно малые потери их энергии на столкновения с частицами остаточного газа.
19
Испарение различных материалов, нагреваемых в высоком вакууме, происходит со скоростью (массой вещества, испаряющегося с единицы поверхности за единицу времени), определяемой по уравнению Ленгмюра:
V |
= 4,4 10−4 αP |
|
M 1/2 |
, |
|
l |
S |
T |
|
|
|
|
|
|
|
|
где Vl – скорость испарения; α – коэффициент испарения (для идеального испарения α = 1); PS – упругость пара при температуре Т; M – массовое число испаряемого вещества.
Вышеприведенное уравнение справедливо в предположении, что ни одна из испаряющихся частиц не возвращается на испаряемую поверхность сквозь газ или облако пара над испаряемым материалом. При невыполнении этого условия скорость испарения меньше, чем рассчитываемая по уравнению Ленгмюра, т.е.
V = k Vl ,
где k – коэффициент передачи, который в зависимости от скорости испарения и давления газа может принимать значения от 0 до 1.
Уже при давлении газа 1 Па его влияние на скорость испарения становится существенным. Упругость пара зависит от температуры в первом приближении следующим образом:
P = k |
exp |
|
− k2 |
|
, |
|
S |
1 |
|
|
T |
|
|
|
|
|
|
|
|
где коэффициенты k1 и k2 зависят от материала. Например, у алюминия при повышении температуры приблизительно от 1100 до 1200 °С упругость пара возрастает от 1 до 10 Па.
В соответствии с зависимостью упругости пара от температуры скорость испарения возрастает с температурой поверхности приблизительно экспоненциально.
При техническом решении задач вакуумного нанесения покрытий требуются скорости испарения в пределах 10–5…10–2 г·см–2·с–1.
20