
книги / Электронно-лучевая обработка в сварке
..pdf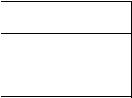
В процессе нагрева поглощающая способность многих металлов не остается постоянной и заметно увеличивается с ростом температуры.
3.3. Основные серийные технологические установки
Первые отечественные технологические установки типа СУ-1
иК-3 были выпущены в 1964 году. В дальнейшем в течение нескольких лет сотни установок эксплуатировались на многих предприятиях, выполняя операции по сверлению отверстий, микросварке, подгонке номиналов резисторов и др. Были разработаны
иосвоены промышленностью более совершенные установки. Большинство установок являются универсальными, имеют широкие технологические возможности.
Внастоящее время с учетом современных достижений в области разработок конструкций различных типов лазеров, накопленного опыта их эксплуатации, технологических задач в различных отраслях производства отечественной промышленностью выпускаются высокопроизводительные лазерные установки типа «Квант», «Кристалл», «Корунд», «Катунь», «Кордамон» и другие. На базе этих установок создан целый рад модификаций для выполнения различных операций. Изготавливаются также небольшими партиями лазерные установки для решения конкретных технологических задач, например в микроэлектронике.
Технические характеристики основных лазерных технологическихустановок, выпускаемых в нашейстране, приведены в табл. 3.2.
|
|
|
|
|
|
|
Таблица 3.2 |
Технические характеристики лазерных установок |
|||||||
|
|
|
|
|
|
|
|
Тип установки |
|
Параметры излучения |
|
Назначение |
|||
λ, мкм |
τ, мс |
Е, Дж |
Р, кВт |
|
f, Гц |
||
Кристалл-6 |
1,06 |
0,2 |
4,0 |
– |
|
20 |
Для сверления и фре- |
|
зерования материалов |
||||||
Кристалл-7 |
1,06 |
0,2 |
5,0 |
– |
|
5 |
Для сверления сквоз- |
|
|
|
|
|
|
|
ных отверстий |
|
|
|
|
|
|
|
41 |
|
|
|
|
|
|
|
Окончание табл. 3.2 |
|
|
|
|
|
|
|
|
Тип установки |
|
Параметры излучения |
|
Назначение |
|||
λ, мкм |
τ, мс |
Е, Дж |
Р, кВт |
|
f, Гц |
||
Квант-9 |
1,06 |
0,5 |
10 |
– |
|
1 |
Для сверления отвер- |
|
|
|
|
|
|
|
стий в алмазах |
Квант-10 |
1,06 |
4,0 |
10 |
– |
|
1 |
Для точечной сварки |
Квант-11 |
1,06 |
0,2 |
0,2 |
– |
|
100 |
Для резки полупро- |
|
водниковых пластин |
||||||
Квант-12 |
1,06 |
2,0 |
3 |
– |
|
20 |
Для шовной сварки |
Квант-15 |
1,06 |
2,0 |
12 |
– |
|
20 |
Для точечной и шов- |
|
|
|
|
|
|
|
ной сварки |
Квант-16 |
1,06 |
5,0 |
30 |
– |
|
1 |
Для поверхностной |
|
закалки |
||||||
|
|
|
|
|
|
|
|
Квант-17 |
1,06 |
1,0 |
4 |
– |
|
10 |
Для сварки двумя |
|
лучами |
||||||
|
|
|
|
|
|
|
|
Квант-18 |
1,06 |
10 |
130 |
– |
|
0,5 |
Для термоупрочнения |
ЛТ-1 |
10,6 |
– |
– |
5 |
|
– |
Для резки и сварки |
Катунь |
10,6 |
– |
– |
0,8 |
|
– |
Для резки и сварки |
Кардамон |
10,6 |
– |
– |
0,8 |
|
– |
Для резки и сварки |
Кристалл-1А |
10,6 |
– |
– |
0,04 |
|
– |
Для резки стекла |
Алмаз-5 |
10,6 |
– |
– |
0,8 |
|
– |
Для резки стали |
42
4.ТЕХНОЛОГИЯ ЛАЗЕРНОЙ ОБРАБОТКИ МЕТАЛЛОВ
ИСПЛАВОВ
4.1. Классификация видов лазерной обработки
Одним из перспективных направлений лазерной технологии является поверхностная обработка металлов и сплавов. Она объединяет целый ряд процессов – закалку, отжиг, легирование и наплавку, ударно-импульсную обработку, амортизацию поверхности.
Значительный рост средних мощностей и частоты следования импульсов твердотельных лазеров, увеличение мощности непрерывных газовых лазеров на СО2 резко повысили интерес и к лазерной сварке и резке.
Классификация основных видов лазерной обработки представлена на рис. 4.1.
4.2. Лазерная поверхностная обработка
Улучшение эксплуатационных свойств металлических материалов при различных видах лазерной поверхностной обработки связано с изменением структурного состояния, фазового и химического составов поверхностных слоев. Используя лазерный пучок как концентрированный источник тепла, можно выполнять различные виды локальной термической обработки, например закалку
иотжиг.
В1976 году сотрудниками американской технологической корпорации был предложен метод лазерной поверхностной закалки из жидкого состояния, названный «лазерное глазурирование». Для
лазерного глазурирования, как правило, используют непрерывное излучение с плотностью мощности 104…107 Вт/см2. При перемещении обрабатываемой поверхности под лучом лазера (или луча по поверхности) тонкие слои материала расплавляются и затем быстро
43
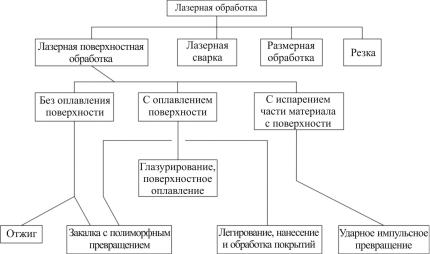
затвердевают за счет передачи тепла низлежащим холодным слоям металла основы. Для чистого никеля, например, расплавленные
слои толщиной 2,5 и 25 мкм охлаждаются со скоростями 5·108 и 5·106 град/с.
Рис. 4.1. Классификационная схема основных видов лазерной обработки
Изменяя мощность и время воздействия лазерного излучения на обрабатываемые участки поверхности материала, можно получить широкий спектр структурных состояний; ультрамикроскопические структуры, перенасыщенные твердые растворы, структуры с повышенной гомогенностью, тонкие дендритные структуры, тонкие эвтектические композиции. При экстремально высоких скоростях охлаждения, наблюдаемых при лазерном глазурировании, на кристаллической основе в ряде случаев могут быть зафиксированы аморфные структуры.
Лазерное оплавление можно также использовать для поверхностностного легирования или обработки покрытий. В последнем случае наблюдается залечивание дефектов (пор и трещин) и улучшается прочность сцепления покрытия с основой вследствие обра-
44
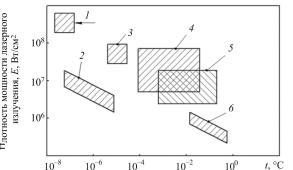
зования жидкой фазы. С помощью лазера можно производить наплавку или напыление различных покрытий аналогично процессам дуговой, плазменной или пламенной наплавки или напыления.
Результаты лазерной поверхностной обработки зависят прежде всего от двух основных параметров – плотности мощности лазерного излучения Е и времени воздействия излучения t. Значения указанных параметров для различных видов лазерной обработки приведены на рис. 4.2.
Рис. 4.2. Режим облучения для различных видов лазерной обработки: 1 – ударная импульсная обработка; 2 – глазурирование и поверхностное оплавление; 3 – сверление; 4 – сварка и резка; 5 – легирование и нанесение покрытий; 6 – закалка с полиморфным превращениями
Лазерная ударная обработка производится импульсами с длительностью 10–8 с и плотностью мощности излучения 106...108 Вт/см2. При воздействии подобных импульсов излучения на поверхность происходит мгновенное взрывообразное испарение части материала
ипереход окружающего поверхность вещества в плазменное состояние. Последующее расширение плазмы сопровождается возникновением ударной волны, которая воздействует на поверхность
ираспространяется вглубь обрабатываемого материала. Следствием распространения волн в кристаллическом веществе является образование различного рода структурных дефектов, что, в свою очередь, приводит к изменению свойств материала.
45
Лазерная закалка принципиально отличается от объемной закалки тем, что она может протекать с оплавлением и без оплавления поверхности. В последнем случае структурно-фазовые превращения происходят в твердом состоянии. Этот вид закалки применяют в основном для сплавов, испытывающих полиморфные превращения. Одним из ее важнейших преимуществ является сохранение микрогеометрии поверхности, благодаря чему отпадает необходимость последующей механической обработки. Такой вариант упрочнения экономически выгоден, позволяет встроить операцию лазерной закалки в общий технологический цикл изготовления детали, не усложняя его, что в большинстве случаев является определяющим фактором пригодности процесса для его внедрения.
Закалку с оплавлением поверхности можно рассматривать как один из видов закалки из жидкого состояния. При этом существенно ухудшается исходная микрогеометрия поверхности, поэтому необходима последующая механическая обработка.
Преимущества лазерной закалки перед традиционными способами закалки (в том числе закалки токами высокой частоты) следующие:
а) возможность упрочнения поверхности любой формы, труднодоступных мест (пазов, отверстий) в изделиях сложной конфигурации;
б) локальность нагрева, малые зоны термического влияния, в связи с чем значительно снижаются или совсем исключаются деформации изделия и обеспечивается прецизионный характер обработки;
в) бесконтактность воздействия излучения, что позволяет упрочнять любые материалы независимо от их физико-химических свойств – стали, чугуны, твердые сплавы, цветные металлы, порошковые материалы и др.;
г) высокая производительность и экономичность; д) отсутствие громоздкого термического оборудования и охла-
ждающих сред (печей, средств охлаждения), что повышает культуру производства и улучшает условия труда;
46
е) возможность проведения термообработки в вакууме, инертных и активных средах.
Для лазерной закалки могут быть использованы лазеры как импульсного, так и непрерывного действия. Наиболее важные факторы, определяющие выбор типа лазера, – глубина упрочнения и производительность процесса. Максимальная глубина упрочнения при закалке импульсными лазерами типа «Квант» и СО2-лазерами мощностью до 5 кВт составляет в случае оплавления поверхности в среднем 0,2–0,25 и 1,5–1,8 мм, а при отсутствии проплавления
0,07–0,15 и 0,8–0,9 мм.
Практика работы с лазерным излучением показала, что лазерная термическая обработка металлов без оплавления поверхности практически невозможна без специальных технологических мер, повышающих поглощающую способность металла. Для получения стабильных результатов лазерной термической обработки на обрабатываемую поверхность перед облучением наносят соответствующие покрытия. Чаще всего для этой цели используют фосфаты марганца или цинка, различные краски, суспензии, сажи, оксиды цветных металлов. Так, например, при термоупрочнении сталей типа 40Х использовались покрытия, содержащие оксиды цинка и хрома, красный железооксидный пигмент с различными связующими. Способы нанесения покрытия различны: пневмораспылителем, окунанием, кистью. Продолжительность сушки при 80 °С составляет 15 мин.
Поглощательная способность металла повышается и при использовании ряда покрытий из диэлектрических материалов, широко применяющихся в машиностроении. Эти покрытия получаются при фосфатировании коллоидного раствора графита, напылении окислов различных металлов, силикатов.
В табл. 4.1 приведены значения критических плотностей энергии, при которых наблюдается поверхностное упрочнение ряда сталей, подвергнутых различным видам предварительной термической обработки. Интервал этих значений зависит от времени воздействия излучения, химического состава и исходного состояния обрабаты-
47
ваемого материала. Этот диапазон ограничен верхним и нижним критическими уровнями плотности энергии. Верхней критической плотностью энергии qs max считается плотность энергии, соответст-
вующая процессу плавления, нижней – плотность энергии qs min , при которой наблюдается процесс отпуска.
Таблица 4.1
Условия получения эффекта гарантированного упрочнения в материалах при импульсном облучении
|
qs min , |
qs max , |
Микротвер- |
Микротвер- |
|
Облучаемый материал |
2 |
2 |
дость исход- |
дость упроч- |
|
Дж/мм |
Дж/мм |
||||
|
ная, МПа |
ненная, МПа |
|||
Сталь 20 |
1,5/1,8 |
3,7/4,3 |
1800 |
7200 |
|
Сталь 45 нормализованная |
2,4/1,7 |
4,6/4,0 |
2000 |
7800 |
|
Сталь 45 закаленная |
1,4/1,7 |
3,6/4,1 |
5500 |
7800 |
|
Сталь У8 |
2,3/1,6 |
4,4/3,8 |
2200 |
10 000 |
|
Сталь У8 закаленная |
1,3/1,6 |
3,5/4,0 |
7000 |
10000 |
|
Сталь У12 |
2,2/1,5 |
3,2/3,6 |
2800 |
11 500 |
|
нормализованная |
|
|
|
|
|
Сталь У12 закаленная |
1,2/1,6 |
3,6/4,0 |
7000 |
12 000 |
|
Сталь 9ХС |
2,2/1,6 |
4,3/3,7 |
2500 |
11 500 |
|
нормализованная |
|
|
|
|
|
Сталь 9ХС закаленная |
1,3/1,6 |
3,5/4,0 |
7000 |
9800 |
|
Сталь ШХ15 |
2,1/1,5 |
4,2/3,6 |
2750 |
10 500 |
|
нормализованная |
|
|
|
|
|
Сталь ШХ15 закаленная |
1,2/1,6 |
3,5/3,9 |
6900 |
10 500 |
|
Сталь ХВГ |
2,0/1,4 |
4,1/3,5 |
– |
– |
|
нормализованная |
|
|
|
|
Лазерный отжиг. Наиболее широко возможности лазерного отжига используют в электронной промышленности. В отличие от обычного печного отжига с помощью лазерного луча можно осуществлять контролируемый по температуре и времени нагрев поверхностных слоев различных материалов на заданную глубину. При этом температура соседних участков металла практически не изменяется.
48
Применение лазерного отжига вследствие локальности и кратковременности нагрева позволяет подавить диффузионные процессы и существенно улучшить характеристики полупроводниковых материалов и структур. Так, с помощью лазерного отжига может быть достигнута более высокая эффективность легирования, в 6...8 раз повышена электрическая активность носителей заряда в полупроводниковых структурах.
Одной из перспективных технологических схем лазерной наплавки является проведение процесса с использованием непосредственной подачи наплавляемого порошка в зону обработки. Указанная схема обладает рядом преимуществ по сравнению с лазерной обработкой металлов с предварительно нанесенными суспензией или пастой: отсутствие нежелательных процессов, связанных со сгоранием или разложением связующих веществ, повышенная технологичность и уменьшение энергоемкости процесса лазерной обработки. Для полного проплавленного слоя предварительно нанесенного материала постепенно наращивают наплавляемый материал в процессе поступления порошка. Например, при проведении лазерной наплавки на сталь хромборникелевого сплава ПГ-ХН80СР2 удельная энергия для получения валика толщиной 1 мм для различных технологических схем составляет 30…60 Дж/мм2 при непрерывной подаче порошка в зону обработки, 16…120 Дж/мм2 при оплавлении порошковых паст и 180…330 Дж/мм2 при оплавлении газотермических напыленных покрытий.
4.3. Лазерная обработка отверстий
Сфокусированное лазерное излучение применяется для обработки отверстий диаметром 0,001...2,5 мм в деталях из различных материалов с толщиной стенки 0,02...12 мм. Целесообразно рассматривать раздельно особенности получения отверстий в двух размерных диапазонах: при чисто лазерной обработке, обеспечивающей формирование отверстий диаметром 0,001...0,8 мм и глубиной до 5 мм, и при обработке с использованием дополнительно
49
с энергией лазерного пучка других видов энергии, обеспечивающей получение отверстий диаметром 0,8...2,5 мм и глубиной до 12 мм.
При разработке процесса лазерной обработки отверстий необходимо:
а) определить значение параметров лазерного излучения – энергии Е, длительности τи , расходимости пучка θ, числа импуль-
сов n;
б) выбрать условия обработки: фокусное расстояние рабочего объектива F, увеличение окуляра наблюдательной системы;
в) выбрать лазерную технологическую установку; г) установить методы настройки технологического режима ла-
зерной установки – энергии импульса (изменением энергии накачки активного элемента Eн; диафрагмированием пучка); длительности импульса (изменением параметров формирующей линии накачки – индуктивности Lн, емкости C, напряжения питания ламп накачки Uн; использованием затворов или комплексом перечисленных приемов);
д) предусмотреть экономическую эффективность процесса по соответствующим методикам, используя одно из следующих выражений для оценки машинного времени, необходимого для получения отверстия заданных параметров; для одноимпульсной обработки детали с K отверстиями – Tман = K τн; для многоимпульсной об-
работки детали с отверстиями – Tман = K n(τн + I f ).
При решении поставленных задач особое внимание следует обратить на многоплановое влияние некоторых методов настройки на параметры технологического режима.
Качество является комплексным критерием технологического процесса и характеризует результаты обработки следующими показателями: точностью диаметральных размеров, степенью соответствия поперечной и продольной формы отверстия заданной, величиной шероховатости и волнистости поверхности отверстия, а также состоянием и свойствами приповерхностного слоя.
50