
книги / Переработка углеводородных газов.-1
.pdfди- и триэтаноламины, диизопропаноламин, метилдиэтаноламин, МДЭА) или щелочей.
Процессы физической абсорбции основаны на физическом растворении извлекаемых компонентов в абсорбенте, в качестве которых применяются N-метилпирролидон, гликоли (ди- и триэтиленгликоли), трибутилфосфат, сульфолан, метанол и др.
В комбинированных процессах используют смешанные поглотители. Например, в процессе «Сульфинол» используются поглотители сульфолан и диизопропаноламин.
Окислительные процессы основаны на необратимом превращении поглощаемого сорбентом сероводорода в элементарную серу. Сорбент в этом случае содержит катализатор окисления и представляет собой водно-щелочной раствор катализатора – комплексное соединение хлорида железа с динатриевой солью этилендиаминтетрауксусной кислоты (трилон Б), горячий раствор мышьяковистых солей щелочных металлов.
Адсорбционные процессы основаны на селективном физическом поглощении Н2S и CО2 в порах твердых сорбентов, в качестве которых используютактивныеугли или синтетические цеолиты.
Выбор того или иного метода очистки зависит от многих факторов, таких как начальные и конечные концентрации Н2S и CО2, область применения газа (в быту, в качестве топлива в двигателях, при синтезе), доступность того или иного вида поглотителя), однако основным является концентрация Н2S и CО2, а также других сероорганических соединений в газе.
При высоких концентрациях кислых компонентов предпочтение отдается физической абсорбции, основной недостаток которой – низкая избирательность в отношении углеводородов. Хемосорбционные и комбинированные процессы рекомендуются при средних концентрациях Н2S и CО2, а окислительные – при низких концентрациях.
При любом методе очистки большое значение придается свойствам поглотителя. Основные требования, предъявляемые кнему:
– низкое давление насыщенного пара, чтобы потери с очищаемым газом были минимальны;
41
–высокая способность поглощать кислые компоненты в широком интервале их парциальных давлений;
–низкая вязкость дляобеспеченияхорошего контакта с газом;
–малая растворяющая способность по отношению к углеводородам;
–низкая коррозионная активность;
–высокая стойкость к окислению.
4.9. Хемосорбционные процессы очистки
Наиболее широкое применение получили процессы очистки аминами (моно- и диэтаноламины), которые при взаимодействии с Н2S и CО2 образуют химические соединения, распадающиеся при повышении температуры и снижении давления. При этом протекают следующие реакции:
2RNH2 + H2S ↔ (RNH3)2S;
2RNH2 + CO2 + H2O ↔ (RNH3)2CO3.
Рассмотрим технологическую схему очистки углеводородных газов от кислых соединений раствором моноэтаноламина
(МЭА) (рис. 4.6).
Согласно схеме исходный газ в абсорбере 1 контактирует с МЭА во второй ступени – сначала со слабо регенерированным, а затем – с полностью регенерированным потоком. Абсорбент с низа абсорбера 1 поступает в десорбер 3, где отделяется углеводородный газ, а насыщенный кислыми компонентами поглотитель через теплообменники 6 поступает в регенерационную колонну 2, в которой комплексные соединения Н2S и CО2 с амином разлагаются, а выделяющиеся кислые газы выходят сверху колонны 2. С низа колонны 2 регенерированный поглотитель через ребойлер 5 и охладительные аппараты 6 и 7 направляются в абсорбер. Часть абсорбента при этом циркулирует через очиститель 4, где отделяются накапливаемые в растворе неразлагающиеся соединения МЭА с СОS и СS2, которые снижают поглотительную способность абсорбента по отношению к Н2S и CО2.
42
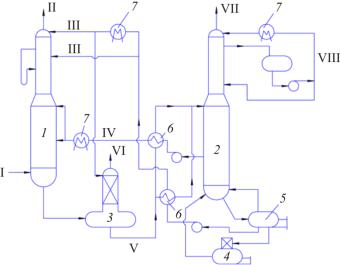
Рис. 4.6. Принципиальная схема очистки газа раствором МЭА: 1 – абсорбер; 2 – десорбер(регенераторМЭА); 3 – промежуточныйдесорбер(выветриватель); 4 – очиститель; 5 – ребойлер; 6 – теплообменники; 7 – холодильники; I, II – исходный и очищенный газы; III, IV, V – регенерированный, слабо регенерированный и насыщенный поглотитель; VI – топливный газ;
VII – смесь кислых газов; VIII – циркуляционное орошение
Технологические параметры процесса:
−для абсорбера: t = 35–40 °C, Р = 3…5 МПа;
−для десорбера: t = 125 °С, Р = 0,3…0,8 МПа.
Следует отметить, что использование МЭА в качестве абсорбента имеет ряд недостатков:
−образованиенеразлагающихся соединений сСОS иСS2 иО2;
−большие потери от испарения (низкая температура испарения);
−низкая селективность к Н2S в присутствии CО2;
−пенообразование в присутствии жидких углеводородов, ингибиторов коррозии, механических примесей.
Очистка газа с использованием диэтаноламина (ДЭА) частично лишена недостатков, присущих процессу МЭА. Техноло-
43
гическая схема аналогична процессу МЭА, только отсутствует очиститель 4. Концентрация ДЭА в зависимости от разновидности процесса составляет от 20–25 до 25–35 % (поглотительная способность более концентрированного раствора выше).
В настоящее время на установках очистки газа от Н2S в качестве хемосорбента получил применение МДЭА (метилдиэтаноламин). Его эффективность максимальна при концентрации 30–50 мас. %. На реальных технологических установках используется концентрация около 70 мас. %, что позволяет существенно снизить циркуляцию раствора.
Достаточно глубокую очистку от Н2S и CО2, а также от СОS, СS2 и меркаптанов также обеспечивает процесс, в котором в качестве поглотителя используются 60–75 % водные растворы дигликольамина (ДГА). Повышенная концентрация позволяет снизить циркуляцию раствора и уменьшить энергозатраты. Раствор ДГА очень мало растворяет углеводороды (меньше, чем МЭА и ДЭА). Его регенерацию проводят обычно под вакуумом (10–20 кПа), так как температурарегенерациине превышает 170 °C.
4.10. Процессы очистки углеводородных газов растворами солей щелочных металлов
Эти процессы основаны на хемосорбционной активности водных растворов карбонатов Na и К по отношению к основным серосодержащим соединениям газа, за исключением меркаптанов. Для повышения эффективности карбонатных растворов в них вводят активаторы.
Основные протекающие при этом реакции:
К2СО3 + Н2S ↔КНСО3 + КНS;
СОS + Н2О↔СО2 + Н2S; К2СО3 + СО2+ Н2О↔ 2КНСО3.
Технологическая схема этого процесса аналогична схеме очистки аминами. Наиболее распространен поташ-процесс, в котором в качестве поглотителя используются 25–35 % раствор
44
К2СО3, очищающий газ от Н2S, СО2, СОS и СS2. Абсорбция протекает при t = 110…115 °С, Р = 2…8 МПа. Регенерация поглотителя протекает при t = 115…120 °С и давлении, близком к атмосферному, или под вакуумом.
Процесс применяют для очистки углеводородных газов с высоким содержанием СО2 и общей концентрацией кислых газов
5–8 % и выше.
К недостаткам процесса можно отнести:
−трудность удаления меркаптанов;
−повышенную коррозию оборудования;
−необходимость иметь низкое соотношение количеств Н2S
иCО2 в газе, поступающем на очистку.
Совершенствование поташ-процесса возможно путем введения активирующих добавок к поглотителю для повышения его поглотительной способности, снижения коррозии ипенообразования.
4.11. Физическая абсорбция
Процессы физической абсорбции основаны на растворении компонента газа в жидкости, определяемом законом Генри (объем поглощаемого компонента пропорционален его парциальному давлению). Количество растворившегося компонента тем больше, чем выше его парциальное давление и коэффициент растворимости, увеличивающийся с понижением температуры.
Разными фирмами разработан целый ряд процессов физической абсорбции с использованием того или иного растворителя в зависимости от параметров очищаемого и очищенного газа (глубина очистки).
Очистка гликолями. Применяется обычно на промыслах, когда газ содержит большое количество Н2S и CО2 и нет необходимости доочищать его до требований стандарта, так как этот газ используется непосредственно на промысле (закачка в пласт для поддержания давления, в качестве топлива). В этом случае происходит не только очистка газа от кислых компонентов, но и его осушка. Кроме того, при повышении давления резко возрастает
45
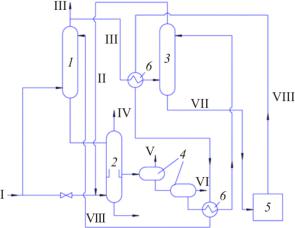
степень удаления Н2S по сравнению с CО2 при использовании в качестве поглотителя ДЭГ (диэтиленгликоль). При этом удаление кислых компонентов из насыщенного абсорбента (основного количества) происходит простой дегазацией без затрат тепла.
Принципиальная схема очистки газа ДЭГ представлена на рис. 4.7. Согласно схеме основной поток газа с t = 40 °С направляется в абсорбер (2) (Р = 7…8 МПа, где он осушается от влаги). Другая часть сырого газа идет в колонну (1) (давление на 0,2–0,3 МПа выше, чем в абсорбере) для глубокой очистки от Н2S абсорбцией регенерированным раствором ДЭГ (VIII), который после насыщения направляется как осушающий агент в абсорбер (2). Осушенный газ с верха абсорбера (2) используется в качестве топлива (IV), а насыщенный ДЭГ через дегазаторы (4) направляется в отдувочную колонну (3) (давление на0,2 МПа выше, чем в абсорбере (2)).
Рис. 4.7. Принципиальная схема очистки и осушки газа раствором ДЭГ: 1 – абсорбер очистки от сероводорода; 2 – абсорбер осушки; 3 – колонна отдувки; 4 – дегазаторы; 5 – блок регенерации ДЭГ; 6 – теплообменник; I, II, III – исходный, отдувочный и очищенный от сероводорода газы; IV – осушенный газ; V – газ дегазации; VI – жидкие углеводороды; VII – раствор ДЭГ, насыщенный сероводородом и водой;
VIII – регенерированный раствор ДЭГ
46
Очищенный от Н2S газ (III) с верха колонны (1) частью выводится как топливо или для технологических нужд, а другая его часть, нагретая до 120 °С, подается в низ колонны (3) для отдувки сероводорода из раствора ДЭГ. Отдувочный газ, содержащий до 7 % сероводорода, направляется в смеси с сырым газом в абсорбер (2). Из дегазаторов (4) выводят десорбированный газ (V) и жидкие углеводороды(VI), поглощенные в абсорбере потокомабсорбента.
Процесс «Пуризол». В качестве абсорбента используется N-метилпирролидон (N-МП) – тяжелый малотоксичный растворитель, смешивающийся с водой в любых соотношениях. В N-МП хорошо растворяются меркаптаны и сероводород, а при высоких парциальных давлениях и углекислый газ. В N-МП может раствориться в 10–12 раз больше Н2S, чем СО2, поэтому процесс можно использовать для селективного извлечения сероводорода.
Схема процесса может быть одно- и двухступенчатой. Первая схема применяется, когда содержание углекислого газа мало. Вторая используется для очистки газа с большим содержанием СО2, при этом на первой ступени удаляется сероводород, а на второй – углекислый раз. Регенерация поглотителя идет при температуре 100–120 °С и давлении, близком к атмосферному.
Поскольку в N-МП одновременно с кислыми компонентами растворяются и углеводороды, то абсорбент до регенерации проходит стадию выветривания (отдува). Отдувочный газ возвращается в поток сырого газа перед абсорбером.
Процесс «Селексол». В качестве абсорбента используется диметиловый эфир полиэтиленгликоля (ДМЭ ПЭГ). Это комплексное вещество, хорошо поглощающее все сернистые соединения, углекислый газ и пары воды. ДМЭ ПЭГ используют в концентрированном виде (содержание воды от 0 до 5 %).
К преимуществам данного абсорбента можно отнести:
−стабильность абсорбционной способности (до 10 лет);
−хорошая биоразлагаемость;
−нетоксичность и малая коррозионная активность;
−небольшая теплота абсорбции;
47
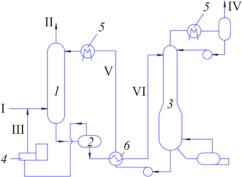
−низкая склонность к вспениванию, высокая гигроскопич-
ность;
−малое давление насыщенных паров.
Согласно схеме (рис. 4.8) насыщенный абсорбент из абсорбера 1 проходит дегазацию в аппарате 2. Отдувочный газ возвращается дожимным компрессором 4 в поток свежего газа. Далее абсорбер поступаетв десорбер 3 дляудалениякислых компонентовIV.
Рис. 4.8. Принципиальная схема очистки и осушки газа в процессе «Селексол»: 1 – абсорбер; 2 – дегазатор; 3 – десорбер; 4 – дожимной компрессор; 5 – холодильники; 6 – теплообменник; I, II, III – см. рис. 4.3; IV – кислые газы; V, VI – регенерированный и насыщенный раствор абсорбента
По поглотительным способностям ДМЭ ПЭГ различные компоненты газа располагаются в ряду:
H2O > CS2 > CH3S > H2S > C5H12 > C4H10 > C3H8 > CO2 > C2H6.
Поэтому этот процесс используется тогда, когда необходима глубокая очистка от сероводорода и других серосодержащих соединенийи нетребуетсяотделения основноймассыуглекислого газа.
Процесс «Сульфинол». В этом процессе используется комплексный поглотитель, состоящий на 60–65 % из сульфолана (физический абсорбент) и на 28–32 % из диизопропаноламина (хемосорбент). Наличие в растворителе одновременно физиче-
48
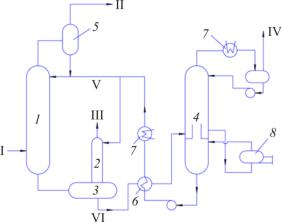
ского и хемосорбента позволяет придать процессу универсальность по составу исходного газа. Поглотительная емкость такого абсорбента существенно выше, чем у МЭА (до 120 м3/м3 против 25–30 м3/м3 для МЭА). Это в свою очередь предопределяет меньшую кратность циркуляции и меньшие габариты аппаратов, ниже (на 30–80 %) энергозатраты на регенерацию сорбента.
Еще одно преимущество данного сорбента состоит в том, что он очищает газ не только от Н2S и CО2, но и от СОS, CS2 и тиолов. Низкое давление насыщенных паров абсорбента способствует снижению его потерь с очищенным газом.
Схема очистки газа с использованием абсорбента сульфоналДИПА приведена на рис. 4.9. Давление в абсорбере Р = 7,1 МПа, в десорбере Р = 0,17 МПа.
Рис. 4.9. Принципиальная схема очистки газа в процессе «Сульфинол»: 1, 2 – абсорбенты; 3 – дегазатор; 4 – десорбер; 5 – сеператор; 6 – теплообменник; 7 – холодильники; 8 – ребойлеры; I и II – исходный и очищенный газ; III – очищенный газ от дегазации; IV – кислые газы; V и VI – регенерированный и насыщенный абсорбент
Позднее был разработан процесс «Сульфинол-СКОТ», с помощью которого решаются 2 задачи:
49
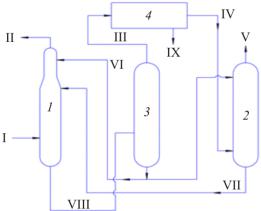
1)из углеводородного газа выделяется концентрат кислых газов, идущих на получение серы (процесс Клауса);
2)улавливается значительное количество оксидов серы из
отходящих дымовых газов процесса Клауса.
Рис. 4.10. Принципиальная схема комбинированного процесса «СульфинолСКОТ»: 1, 2 – абсорбенты; 3 – десорбер; 4 – установка получения серы из сероводорода (процесс Клауса); I и II – исходный и очищенный углеводородный газ; III – кислый газ; IV – отходящий дымовой газ от установки Клауса; V – очищенный от диоксида серы отходящий дымовойгаз; VI – регенерированныйабсорбент; VII иVIII – полунасыщенный
и насыщенный абсорбент; IX – сера
Согласно технологической схеме (рис. 4.10) газ очищается в основном абсорбере 1 блока «Сульфинол», на верх которого подается регенерированный абсорбент VI. Другой поток данного абсорбента поступает в абсорбер 2 блока «СКОТ», где отходящий газ процесса Клауса очищается от диоксида серы. Полученный абсорбент VII из данного абсорбера возвращается в основной абсорбер 1 ниже ввода свежего абсорбента и поглощает другие сернистые компоненты из газа. Колонна регенерации 3 общая для обоих блоков.
50