
книги / Переработка углеводородных газов.-1
.pdfступени устанавливают дожимной компрессор или в точке дросселирования газа помещаютхолодильную машину (5).
Извлечение углеводородов из газа методом НТС в значительной мере определяется составом исходного газа. Для обеспечения нужного уровня извлечения жидких углеводородов необходимо поддерживать высокое давление и низкую температуру, что не всегда удается из-за сильного снижения давления газа в системе. В этом состоит основной недостаток процесса НТС, поэтому схемы НТС заменяют на схемы низкотемпературной конденсации (НТК), отличающиеся более низкими температурами охлаждения газа (–90…–120 °С).
5.2. Извлечение тяжелых углеводородов из газа методом низкотемпературной конденсации
Процесс НТК получал развитие, когда повысился спрос на этан как сырье для нефтехимии. Это потребовало перейти на низкие температуры охлаждения газа. Это в свою очередь потребовало наряду с эффектом дросселирования применять искусственное охлаждение с использованием пропанового (до –70 °С) холода или каскадного холодильного пропан-этанового цикла, с помощью которого стало возможно извлекать из газа 85–87 % этана, 99 % пропана и 100 % всех остальных углеводородов.
Для получения искусственного холода используют обычно компрессорные холодильные машины, хладагентом в которых выступает пропан, этан или фреон, а также турбодетандеры, в которых энергия расширяющегося газа рекуперируется для производства холода. Рассмотрим схему НТК (рис. 5.2).
Согласно схеме предварительно осушенный газ охлаждается
врекуперативных теплообменниках (8) и после отделения от него
всепараторе (2) сконденсированных углеводородов через детандер (3) поступает в колонну (4). В нее же из теплообменника (8)
поступает смесь сконденсированных углеводородов (от С2 и выше), а деэтанизированный газ с верха колонны (4), пройдя тепло-
61
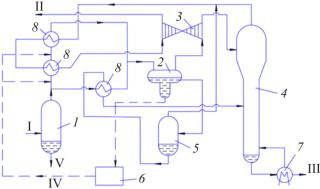
обменник (8), сжимается в турбодетандере (3) и идет к потребителю. ШФЛУ направляется на ректификацию, где отделяется С2 (87–90 %) и остальные углеводороды.
Рис. 5.2. Принципиальная схема процесса низкотемпературной конденсации (НТК): 1, 2 – сепараторы 1-й и 2-й ступеней; 3 – турбодетандер; 4 – ректификационная колонна; 5 – выветриватель конденсата; 6 – блок регенерации ингибитора гидратообразования; 7 – ребойлер; 8 – теплообменники; I и II – исходный и очищенный газ; III – ШФЛУ; IV – ингибитор
гидратообразования; V – конденсатсырогогаза
5.3. Маслоабсорбционное извлечение тяжелых углеводородов из газа
Это один из массовых процессов извлечения из газа тяжелых углеводородов. Сущность его состоит в поглощении тяжелых углеводородов абсорбентом (маслом) с последующей их десорбцией путем отпарки из абсорбента. В качестве абсорбента используют обычно керосиновую или дизельную фракцию нефти со средней молекулярной массой 140–200.
Типичная принципиальная схема масляной абсорбции приведена на рис. 5.3.
Согласно схеме исходный газ охлаждается в охладителях (1, 2), разделяется в сепараторе (3) и поступает в абсорбер (4), где извлекается основная масса тяжелых углеводородов. Насыщенный абсор-
62
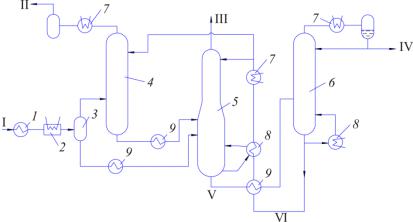
бент через теплообменник (9) поступает в абсорбционно-отпарную колонну (5). В нее же поступает конденсат из сепаратора (3). На верх колонны (5) подается регенерированный абсорбент, снизу через ребойлер (8) подается тепло. В колонне (5) из насыщенного абсорбента с абсорбера (4) отпариваются легкие углеводороды, а свежим абсорбентомпоглощаютсяуглеводородыС3 и выше.
Рис. 5.3. Принципиальная схема отбензинивания газа масляной абсорбцией: 1, 2 – охладители газа; 3 – сепаратор; 4 – абсорбер; 5 – абсорбционноотпорная колонна; 6 – десорбер; 7 – холодильник; 8 – ребойлеры; 9 – теплообменники; I и II – исходный и отбензиненный газы; III – газ деэтанизации; IV – ШФЛУ; V и VI – насыщенный и регенерированный
абсорбент
Полностью насыщенный абсорбент с низа колонны (5) нагревается в теплообменнике (9) и идет в десорбер (6), где от него отгоняется ШФЛУ. Регенерированный абсорбент поступает в аппараты 4 и 5.
В обычном процессе абсорбции, а именно: при температуре в абсорбере 10–30 °С и Р = 4…7 МПа, а в десорбере tниза = 220…230 °С и Р = 0,7…1,5 МПа, удается извлечь 50–70 %
углеводородов С3, до 48 % углеводородов С4 и выше.
63
Совершенствование процесса масляной абсорбции связано с решением задач, среди которых можно выделить следующие:
−для того чтобы повысить эффективность процесса, регенерированный абсорбент (VI) подают в поток газа деэтанизации (III), из которого он извлекает метан и этан, предварительно насыщаясь ими, после этого абсорбент направляется в абсорбер (4) и абсорбци- онно-отпарную колонну (5). Тем самым снижается объем газа деэтанизации иувеличивается выходтоварного газа(II);
−для того чтобы повысить степень извлечения тяжелых углеводородов из газа, надо снизить температуру газа перед входом
вабсорбер и в самом абсорбере.
Это позволяет уже до абсорбера, в сепараторе (3) сконденсировать и отделить большое количество сжиженных углеводородов, снизить нагрузку на абсорбер и углубить извлечение углеводородов С2–С5 в самом абсорбере. В этом случае в абсорбере t = –20…–60 °С, Р = 4…6 МПа, в десорбере Р = 1…2 МПа. Сте-
пень извлечения пропана в этом случае составляет 80–99 %, этана– 20–50 %, более тяжелых углеводородов (С4 ивыше) – 100 %.
5.4. Извлечение тяжелых углеводородов из газа методом адсорбции
Адсорбционный метод применяется для выделения из газа тяжелых углеводородов, когда содержание последних не превышает 50 г/м3.
Сущность метода заключается в способности пористых твердых тел, таких как активированный уголь, силикагель, молекулярные сита (цеолиты), адсорбировать на своей поверхности различные углеводороды.
Количество адсорбированных углеводородов зависит от природы адсорбента, состава газа, поступающего на адсорбцию, температуры и давления.
Так, адсорбционная активность силикагеля по отношению к углеводородам находится в такой последовательности: арены, алкены, нафтены, алканы. В пределах одного класса углеводородов ко-
64
личество вещества, адсорбированное одним и тем же адсорбентом (активированныйуголь), растетсповышениеммолекулярноймассы.
Повышение температуры и понижение давления отрицательно влияют на процесс адсорбции. Обычно адсорбцию проводят при температуре окружающего воздуха и повышенном давлении, а регенерацию продувкой газа или водяным паром при повышенных температурах и атмосферном давлении.
Различают периодические и непрерывные процессы выделения газовых бензинов с помощью адсорбентов. Наиболее распространены схемыпериодическойадсорбции, как наиболеепростые.
Периодический процесс адсорбционного выделения газового бензина состоит из четырех стадий:
1)адсорбция углеводородов на поверхности адсорбента;
2)нагрев адсорбента;
3)десорбцияадсорбированныхуглеводородов горячим газом;
4)охлаждение адсорбента.
Технологическое оформление процесса адсорбционного извлечения тяжелых углеводородов из газа аналогично схеме адсорбционной осушки углеводородных газов.
При адсорбционном отбензинивании газа удается извлечь более 50 % углеводородовС3, 70–85 % бутанаипочти100 % пентана.
Из-за малой производительности установок адсорбционного отбензинивания газа, громоздкости и сложности обслуживания этот метод применяется только тогда, когда из-за низких концентраций тяжелых углеводородов в газе, абсорбция не обеспечивает требуемой глубины их извлечения.
В частности распространение получил процесс короткоцикловой адсорбции, когда одновременно проходит осушка и отбензинивание тощих газов. В этом случае в качестве сорбентов применяют силикагель или боксит. Исследования показали, что при сокращении цикла адсорбции, количество извлекаемых тяжелых углеводородов возрастает.
Адсорбция ведется при температуре окружающего воздуха и при давлении, равном давлению в газопроводе. Регенерация адсор-
65
бента идет нагретым до 290–315 °С отбензиненным и осушенным газом. Температурарегенерациисоставляет не менее 205 °С.
Установка включает два или более адсорберов, которые попеременно работают на стадиях адсорбции и регенерации. Циклы адсорбции и регенерации отрегулированы таким образом, что их продолжительности равны между собой.
5.5. Стабилизация и переработка газовых конденсатов
В общем случае газовыми конденсатами принято считать как смесь «тяжелых» углеводородов (ШФЛУ), выделяемую из газа перед его отправкой в магистральные газопроводы, так и жидкую смесь тяжелых углеводородов, выносимую газом из скважин в капельном виде и отделяемую от газа механически на первых же ступенях сепарации.
Первый конденсат (называемый газовым бензином) содержит смесь углеводородов от С2 до С6 с примесью углеводородов С7 и С8 и обычно перерабатывается на газоперерабатывающих заводах (установки ГФУ) с получением отдельных углеводородов – сырья для нефтехимии.
Газовый конденсат, выносимый газом в виде капельной жидкости из скважины, по своему составу более тяжелый – содержит углеводороды от С2 до С20 и выше. Технология переработки такого конденсата включает процессы стабилизации, обезвоживания и обессоливания, очистки от серы, перегонки и выделения фракции моторных топлив.
Групповой химический и фракционный состав газовых конденсатов различается для разных месторождений. Для того чтобы установить определенный подход к их оценке, введена стандартная классификация (ОСТ 51.56–79). Классификационными признаками служат содержание общей серы, массовая доля ароматических и нормальныхалкановых углеводородов, фракционный состав.
Газовые конденсаты стабилизируются одним из двух методов: ступенчатой дегазацией или ректификацией в стабилизационных колоннах.
66
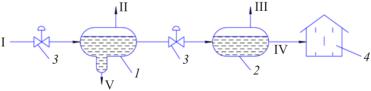
Ступенчатая дегазация – это простейший метод стабилизации (рис. 5.4) состоит в том, что за счет двухили трехступенчатого сброса давления происходит однократное испарение наиболее легких компонентов, которые отделяются в виде конденсата. Согласно схеме конденсат (I) из низкотемпературного сепаратора дросселируется в сепаратор 1, а затем в 2. Из них выводится газ II, III 1-й и 2-й ступеней. Обычно газ 1-й ступени подают эжектором в основной поток газа процесса НТС. Газ 2-й ступени используется как топливо длясобственных нуждпромысла.
Рис. 5.4. Схема двухступенчатой дегазации газового конденсата: 1, 2 – сепараторы; 3 – дроссельные клапаны; 4 – емкость стабильного конденсата; I и IV – нестабильный и стабильный конденсат; II и III – газы дегазации 1-й и 2-й ступеней; V – вода
Такая схема стабилизации характерна для промыслов, где стабильные конденсаты хранятся в атмосферных резервуарах. Для этих схем характерно нечеткое отделение легких углеводородов; часть их остается в конденсате и в последующем может теряться (выветриваться). Для исключения потерь ценных компонентов применяют методызакрытойстабилизации вректификационных колоннах.
Современные стабилизационные установки газового конденсата ректификацией включают две колонны абсорбционно-отпар- ную (АОК) и стабилизационную.
Согласно схеме (рис. 5.5) газовый конденсат из сепаратора установки НТС (I) через дроссель (6) поступает в предварительный сепаратор (1), откуда обе фазы – газовая и жидкая – после нагрева горячим потоком стабильного конденсата поступают в АОК. Давле-
ние в ней 2–2,5 МПа, tверха = 15…20 °С, tниза = 170…180 °С. С верха
67
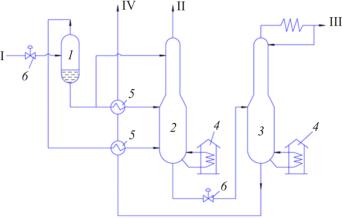
колонны отбирается сухой газ. Деэтанизированный конденсат снизу АОК через дроссель вводится в стабилизационную колонну (3), где от него отделяют ШФЛУ, а снизу стабильный конденсат. Давление вэтойколоннеP = 1…1,5 МПа, tверха = 50…75 °С, tниза = 180…190 °С.
Рис. 5.5. Схема стабилизации газового конденсата ректификацией: 1 – предварительный сепаратор; 2 – АОК; 3 – стабилизационная колонна; 4 – печи; 5 – теплообменники; 6 – дроссели; I и IV – нестабильный
истабильный конденсат; II – газ стабилизации; III – ШФЛУ
Всвою очередь полученный в ходе стабилизации нестабильный газовый бензин или ШФЛУ содержит в своем составе
достаточно много углеводородов С2–С4, а следовательно, имеет высокое давление насыщенных паров и не может быть использован в качестве товарного бензина.
Всвязи с этим такие бензины подвергают дополнительной стабилизации с использованием установок двух типов: с получением сжиженногогаза и сполучениеминдивидуальныхуглеводородов.
Согласно схеме с получением сжиженного газа (рис. 5.6), нестабильный газовый бензин через теплообменник (1) поступает
вколонну (2), которая работает при температуре 40–45 °С и давлении 1–1,5 МПа.
68
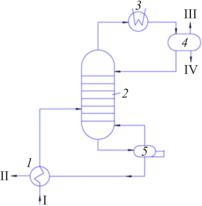
Рис. 5.6. Принципиальная схема установки стабилизации газового бензина сполучениемсжиженногогаза: 1 – теплообменник; 2 – колоннаректификации; 3 – конденсатор-холодильник; 4 – емкость орошения; 5 – ребойлер; I – нестабильный бензин; II – стабильный бензин; III – газ; IV – пропан-бутановая смесь
Сверха колонны (2) уходит газ С1–С4; который после охлаждения в конденсаторе-холодильнике (3) попадает в емкость
орошения (4), с верха которой уходит газ С1–С2, а с низа – смесь С3–С4 (сжиженный газ).
Сниза колонны (2) отбирают стабильный газовый бензин, который, пройдя теплообменник (1), уходит с установки. Тепло поступает в низ колонны (2) за счет нагрева части стабильного бензина в ребойлере (5) и возврата его в колонну (2).
Согласно схеме стабилизации ШФЛУ с получением индивидуальных углеводородов (рис. 5.7) нестабильный газовый бензин после нагрева в теплообменнике (5) поступает в этановую колон-
ну (1), с верха которой выходят углеводороды С1–С2. Остаток идет в пропановую колонну (2), с верха которой отводится про-
пан (С3), остаток идет в бутановую колонну (3), с верха которой получают углеводороды С4, а снизу – стабильный бензин. Углеводороды С4 дополнительно разделяют в колонне (4) на i-C4
(сверху) и n-С4 (снизу).
69
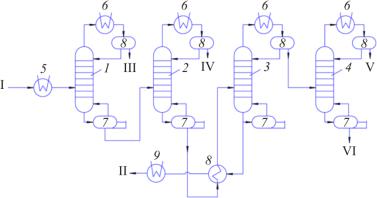
Рис. 5.7. Принципиальная схема установки стабилизации с получением индивидуальных углеводородов: 1, 2, 3, 4 – этановая, пропановая, бутановая, изобутановая колонны; 5 – теплообменник; 6 – холодильникиконденсаторы; 7 – ребойлеры; 8 – емкость орошения; 9 – холодильник; I – нестабильный бензин; II – стабильный бензин; III – углеводороды
С1–С2; IV – углеводороды С3; V – изобутан; VI – н-бутан
Давление в колоннах: 1 – 4 МПа, 2 – 1–1,5 МПа, 3 и 4 –
0,4–0,6 МПа.
5.6. Конструкции аппаратов, используемых в процессах подготовки и переработки углеводородных газов
Фазовые сепараторы – оборудование для разделения фаз защищают расположенное после них оборудование, рассчитанное на переработку однофазных потоков, и улавливают захваченные жидкости, выходящие с различных технологических установок.
Наиболее распространенные типы сепараторов:
−отбойный сепаратор – сепаратор без внутренних контактных устройств, служащих для улучшения разделения;
−скруббер – сепаратор, предназначенный для отделения жидкости от газа с высоким газожидкостным отношением. Скруббер может иметь внутренние устройства, но емкость отсека для уловленной жидкости не велика;
70