
книги / Экспериментальные исследования закритического деформирования и разрушения конструкционных материалов
..pdf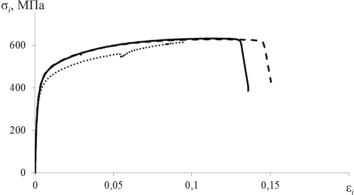
разца в рабочей части (пунктирная линия на рис. 2.24). Полученные данные способствуют развитию модельных представлений о поведении материалов на закритической стадии деформирования, которые необходимы для развития методов оценки безопасности конструкций и прогнозирования процессов их разрушения.
Рис. 2.24. Опытные зависимости изменения интенсивности напряжений от интенсивности деформаций при пропорциональном (сплошная) и сложном нагружении в соответствии с рис. 2.22, а (штриховая) и 2.22, б (пунктирная)
2.4.Микроструктурные изменения стали 40Х при закритическом деформировании
Закритическая стадия деформирования непосредственно предшествует моменту разрушения и характеризуется процессами накопления повреждений и формированием условий разрушения. С точки зрения понимания физических процессов, сопровождающих закритическое поведение сталей, актуальным является вопрос изучения микроструктуры металлов и поверхностей излома образцов. На кафедре металловедения, термической и лазерной обработки металлов ПНИПУ были проведены микроструктурные исследования образцов конструкционной легированной стали 40Х после формирования шейки на стадии разупрочнения и после-
41
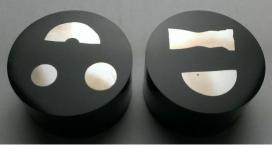
дующей остановки процесса растяжения и разгрузки. Для этого были подготовлены микрошлифы различных частей рабочей части (рис. 2.25), изготовленные путем запрессовки образцов исследуемой стали на автоматическом монтажном прессе Metkon ECOPRESS 100 с дальнейшим шлифованием на шлифовальнополировальном станке Metkon FORCIPOL. Образцы подвергались травлению 4%-м раствором азотной кислоты в спирте.
Рис. 2.25. Микрошлифы для микроструктурных исследований, вырезанные из разных частей образца с шейкой
Изображения микроструктуры в зоне шейки, периферийной зоне рабочей части образца, а также в захватной части образца (исходное недеформированное состояние) получены на световом инвертированном микроскопе Olympus GX 51 при увеличении 500 и 1000 крат. Обработку изображений проводили с использованием программного обеспечения Olympus Stream Motion.
Исходная микроструктура рассмотренной стали 40Х состоит из областей перлита и ферритной сетки. Ферритная сетка сформировалась по границам бывших аустенитных зерен в процессе охлаждения. Средний размер ячейки ферритной сетки, по которой можно оценить размер аустенитного зерна, составляет (54 ± 3) мкм. Микроструктура стали в периферийной части образца (не входящая в зону формирования шейки) представлена на рис. 2.26, а. Микроструктура также состоит из ферритной сетки и перлитных областей. Средний размер ячейки ферритной сетки совпадает с
42
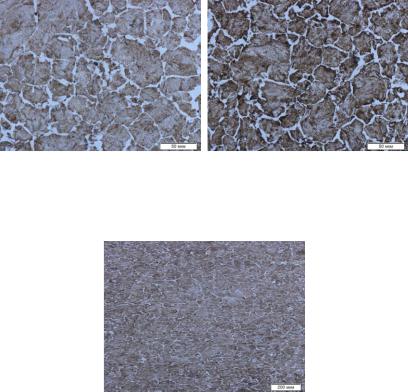
исходным состоянием материала и составляет (54 ± 3) мкм. Деформация в периферийной части образца происходит преимущественно за счет течения ферритной сетки по границам перлитных областей. Микроструктура стали в поперечном направлении, сформированная в шейке образца, подвергнутого закритическому деформированию, представлена на рис. 2.26, б. Микроструктура по-прежнему состоит из ферритной сетки и перлитных областей. Средний размер ячейки ферритной сетки в процессе деформации уменьшается до (44 ± 3) мкм.
а |
б |
Рис. 2.26. Микроструктура стали 40Х в поперечном направлении относительно направления прокатки в периферийной части образца (а) и в зоне формирования шейки (б)
Рис. 2.27. Микроструктура стали 40Х в продольном направлении относительно направления прокатки в области шейки
43
Изображение микроструктуры стали 40Х в продольном направлении относительно направления прокатки приведено на рис. 2.27. В процессе развитого закритического деформирования при испытаниях на одноосное растяжение образца в области формирования шейки ферритная сетка вытягивается в направлении деформации, что приводит к уменьшению поперечного размера ячеек. На микрошлифе, полученном в продольном направлении, наблюдаются темные области с четкими границами, которые могут соответствовать формированию и развитию дефектов. Исследование эволюции систем дефектов, формирующихся на закритической стадии деформирования, требует дальнейшего развития, в том числе с применением других физических методов анализа микроструктуры.
44
3.ЭКСПЕРИМЕНТАЛЬНОЕ ИЗУЧЕНИЕ ОСОБЕННОСТЕЙ РЕАЛИЗАЦИИ
ЗАКРИТИЧЕСКОЙ СТАДИИ ДЕФОРМИРОВАНИЯ В КОМПОЗИЦИОННЫХ МАТЕРИАЛАХ
3.1. Методические особенности проведения экспериментальных исследований деформирования
и разрушения полимерных композиционных материалов
Из анализа литературы следует, что закритической стадии деформирования полимерных композиционных материалов различных классов уделяется недостаточное внимание, ниспадающую ветвь диаграммы деформирования не рассматривают как источник важной информации о поведении материала, а зачастую отбрасывают при представлении экспериментальных данных и, как следствие, не учитывают при проектировании и оценке безопасности конструкций. Тем не менее информация о наличии и условиях реализации закритической стадии деформирования полимерных композитов представляется необходимой для уточненной оценки запаса несущей способности и прогнозирования живучести композитных силовых элементов и может быть использована при проектировании и оценке безопасности конструкций [23–26].
Проанализированы диаграммы деформирования для типовых полимерных композитов с различными направлениями армирования, полученные при распространенных видах статических испытаний (растяжение, изгиб, межслоевой сдвиг). Установлены соответствия видов нагружения типам ниспадающих участков диаграмм деформирования. Среди типов ниспадающих участков диаграмм полимерных композитов можно выделить четыре основных: 1) ниспадающая ветвь диаграммы реализуется в виде незначительного участка разупрочнения с последующем динамическим срывом; 2) полная ступенчатая ниспадающая ветвь с равновесными площадками перераспределения нагрузки;
45
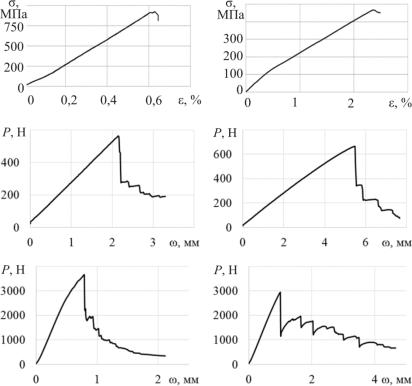
3) ниспадающая ветвь диаграммы начинается с динамического срыва нагрузки на величину от 10 до 50 % от максимальной нагрузки с последующим участком равновесного разрушения; 4) комбинированный, включающий в себя основные типы.
а |
б |
в |
г |
д |
е |
Рис. 3.1. Примеры типовых диаграмм деформирования серийных стекло- (б, г, е) и углепластиков (а, в, д) при испытаниях на растяжение (а, б); трехточечный изгиб (в, г) и межслоевой сдвиг (д, е)
Так, например, при испытаниях на растяжение (рис. 3.1, а, б) диаграммы деформирования образцов на основе стеклоткани Т-10-14 и углеродного препрега ПУ-4э имеют незначительный
46
участок ниспадающей ветви с последующим динамическим срывом, что соответствует первому типу, а при испытаниях на изгиб наблюдается диаграмма с полной ниспадающей ветвью, что соответствует второму типу.
Степень реализации и характер закритической стадии деформирования зависят от реализации различных механизмов разрушения полимерных композитов. Для идентификации механизмов разрушения при исследованиях используются дополнительные измерительные системы регистрации сигналов акустической эмиссии, инфракрасной термографии и анализа и регистрации полей деформаций [31–33].
На основе анализа методических особенностей проведения экспериментальных исследований полимерных композиционных материалов [35–58] разработаны методики проведения исследований закономерностей закритического деформирования и разрушения. Разработанные методики для исследования закритической стадии деформирования предусматривают выполнение условий устойчивости процессов деформирования и структурного разрушения полимерных композитов за счет обеспечения достаточной жесткости нагружающих систем, в том числе с применением сложной оснастки для различных видов испытаний. Несмотря на то, что современные испытательные системы обеспечивают высокие жесткостные характеристики, в процессе нагружения на любой испытательной машине деформация образца сопровождается упругой деформацией частей машины, включая раму, тяги, муфты, захватные приспособления, силоизмерительное устройство и т.п. Чем больше эта деформация, тем податливее нагружающая система, под которой понимается совокупность всех тел, деформирующихся в результате передачи нагрузки на образец. Важность понятия «нагружающая система» с точки зрения исследования процессов закритического деформирования отмечена ранее в работах [26, 28, 29, 59, 60].
Полимерные композиционные материалы, как правило, создаются вместе с конструкцией, которые ввиду широкого разно-
47
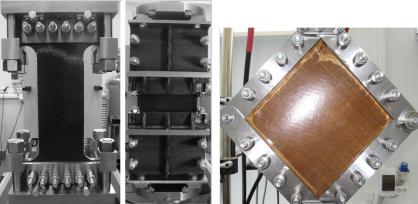
образия материалов и требующихся эксплуатационных характеристик могут иметь различную структуру, в том числе сложную составную крупноячеистую структуру. В таких случаях необходимо использовать дополнительную оснастку для проведения испытаний и определения механических характеристик и особенностей поведения композитов [32, 61, 62].
Например, при испытаниях крупногабаритных образцов – панелей с заполнителем применяются различные дополнительные элементы крепления (оснастка), которые оказывают существенное влияние на податливость всей нагружающей цепи (рис. 3.2). В данном случае коэффициент жесткости всей нагружающей системы будет существенно снижен вследствие податливости элементов захватных приспособлений и крепежных элементов, а также возможного проскальзывания в узлах и выборки технологических зазоров, что приведет к дополнительным перемещениям, регистрируемым встроенным датчиком испытательной установки [63].
а |
б |
в |
Рис. 3.2. Фото дополнительных элементов креплений (оснастки) для испытаний крупноячеистых панелей
сзаполнителем на основе полимерных композиционных материалов на растяжение (а); сжатие (б); сдвиг (в)
48
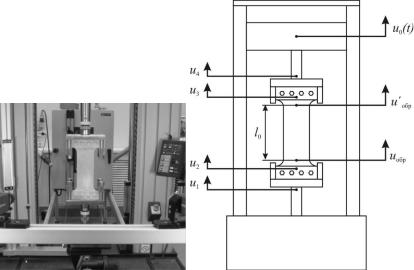
На рис. 3.3 представлена схема определения податливости всей нагружающей цепи, в том числе и элементов оснастки для испытаний панелей с заполнителем, с использованием бесконтактной цифровой видеосистемы анализа полей перемещений и деформаций.
а |
б |
Рис. 3.3. Испытательная машина с оптической системой регистрации полей перемещений на поверхности образца и захватного приспособления (а) и схема регистрации удлинения рабочей зоны образца и элементов нагружающей системы (б)
Встроенные датчики перемещений испытательной машины позволяют контролировать при кинематическом нагружении удлинение всей нагружающей цепи u0(t), включая удлинение образца u(t), и перемещения, обусловленные упругой деформацией нагруженных частей испытательной машины. Следовательно, удлинение образца рассчитывается как
49
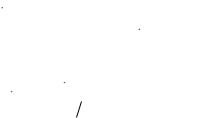
u(t) u |
(t) S(t) |
1 |
, |
(3.1) |
|
||||
0 |
|
Rн.с |
|
|
|
|
|
|
где S(t) – прикладываемая нагрузка, Rн.с – жесткость нагружающей системы.
При проведении испытаний полунатурных образцов из крупноячеистого композиционного материала использованы специальные захватные приспособления, а при определении податливости всей нагружающей системы следует учитывать, как податливость испытательной машины Rм, включая нагружающую раму, тяги и встроенный силоизмерительный датчик, так и податливость захватного приспособления Rз.п:
1 |
|
1 |
|
1 |
. |
(3.2) |
|
|
|
||||
Rн.с |
|
Rм |
Rз.п |
|
Следует отметить, что действительная скорость удлинения рабочей зоны образца u также отличается от номинально заданной скорости кинематического нагружения u0 и может быть определена по формуле
u |
|
u0 |
|
, |
(3.3) |
1 H |
|
R |
|||
|
|
обр |
н.с |
|
|
где Hобр – жесткость рабочей зоны образца, которая определяет-
ся модулем упругости материала Е, площадью поперечного сечения рабочей зоны образца F и длиной рабочей зоны образца l0 ,
Hобр EFl0.
Таким образом, в ходе испытания при помощи цифровой видеосистемы анализа полей перемещений и деформаций, принцип работы которой основан на методе корреляций цифровых изображений, были определены характеристики жесткости нагружающей системы, включая оснастку для испытаний
50