
книги / Экспертиза качества и разрушений
..pdfабсолютных значений нормальных и |
касательных |
напряжений, |
а следовательно, напряженное состояние |
и характер |
разрушения |
материала. Так, например, при одноосном растяжении образца τmax = σI/2, т.е. касательные напряжения в 2 раза меньше, чем нормальные. При кручении, когда τmax = σI, касательные и номальные напряжения равны. Поэтому один и тот же материал при растяжении может разрушаться хрупко, а при кручении − вязко.
Для количественной оценки напряженного состояния материала
вводят понятие коэффициента жесткости состояния |
|
α = τmax/σI. |
(4.14) |
Из этой формулы видно: чем меньше коэффициент α, тем жестче напряженное состояние и, следовательно, больше опасность хрупкого разрушения.
Созданию более жесткого напряженного состояния материала,
аследовательно, его охрупчиванию способствуют:
–увеличение толщины образца или детали;
–увеличение скорости нагружения;
–наличие в образце или детали концентраторов напряжения или дефектов в виде трещин.
Чувствительность материала к охрупчиванию при наличии концентраторов напряжений с повышением прочности металлических материалов увеличивается.
Развитие тепловой хрупкости выявлено в сталях разного состава и термообработки. Прирост критической температуры хрупкости существенным образом зависит от длительности и температуры эксплуатации конструкции (рис. 4.27, 4.28). Наибольший прирост охрупчивания происходит за первые 1000 ч выдержки в диапазоне температур охрупчивания.
Тепловое охрупчивание приводит к межзеренному разрушению
(рис. 4.29).
Механизм развития тепловой хрупкости включает две стадии:
–структурные изменения в стали.
–сегрегационное обогащение примесями границ структурных элементов и раздела фаз.
В свою очередь стадия I включает следующие процессы:
–повышение плотности распределения частиц дисперсной фазы по границам структурных элементов;
171
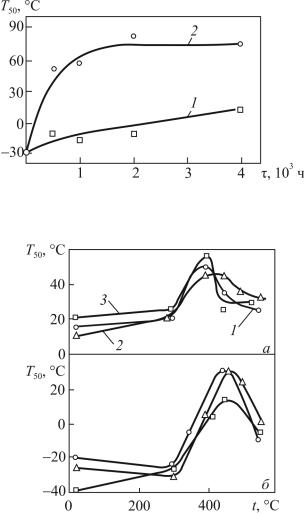
–укрупнение по границам элементов структуры частиц дисперсной
фазы;
–перестроение дислокационной структуры в сторону укрупнения субзерен, по границам субзерен, имеющих повышенную плотность распределения частиц карбидов;
–перераспределение химических элементов, образующих карбиды
всторону увеличения содержания в них более сильных карбидообразующих элементов.
Рис. 4.27. Изменение уровня критической температурыхрупкости в зависимости отдлительностивыдержки стали 10ХСНДпри 340 °С(1) и460 °С(2)
Рис. 4.28. Зависимость критической температуры хрупкости Т50 стали 10ХСНД сферритно-перлитной (а) и сорбитной (б) структурой от температуры выдержки длительностью 1000 ч. Температура аустенитизации 920 (1),1050 (2) и1175 °С(3)
172
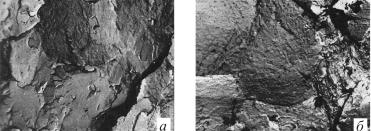
Рис. 4.29. Электронные фрактограммы хрупких изломов в состоянии тепловой хрупкости (а) и в состоянии обратимой отпускной хрупкости (б) термоулучшенной стали 10ХСНД. ×4000
Типичная картина влияния типа структуры на склонность к тепловой хрупкости стали 10ХСНД приведена на рис. 4.28. Сталь 10ХСНД с исходной структурой сорбита отпуска в большей степени подвержена охрупчиванию, чем та же сталь с ферритно-перлитной структурой.
Максимум теплового охрупчивания сталей проявляется в диапазоне 400−450 оС. Наибольшей склонностью к тепловой хрупкости обладают кремниймарганцовистые стали, а наименьшей − стали с молибденом.
Повышение в стали содержания фосфора приводит к увеличению степени теплового охрупчивания.
Интенсивный прирост критической температуры хрупкости выявляется при содержании фосфора более 0,02 %. Отличительной особенностью теплового охрупчивания является отсутствие его связи, выявляемой при испытании гладких стандартных образцов.
Наиболее частые случаи водородного охрупчивания в процессе эксплуатации вследствие наводораживания.
Особый интерес к этому явлению возник в июне 1965 г., когда сотрудники NASA наблюдали преждевременное разрушение емкости для хранения газообразного водорода, рассчитанной на давление 35 МПа. Разрушение призошло при давлении 27,4 МПа. В упрощенном виде водородное охрупчивание включает следующие стадии проникновения водорода в металл (еслиэто неводородосодержащая среда):
–массоперенос водорода от его источника к месту его проникновения на поверхности металла;
–адсорбция водорода на поверхности металла;
–переход водорода с поверхности металла в его внутренние области;
–диффузию водорода по телу металлического объекта.
173
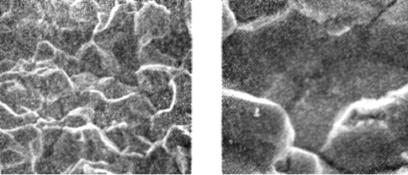
Кинетика и скорость водородного охрупчивания металлов зависит от многих факторов:
–типа кристаллической решетки;
–химического состава, в том числе от содержания вредных примесей;
–микроструктуры;
–напряженного состояния;
–температуры;
–давления водорода в жидкой среде;
–скорости и характера нагружения.
Охрупчивание может возникнуть и как непосредственный результат выдержки в водородосодержащей среде.
Наружный водород может быть молекулярным, атомарным или входить в состав молекул сероводорода, воды, метанола и др. Водород во внутренних объема металла большей частью представляет протоны. В таком виде он может взаимодействовать с другими протонами, атомами металла, с дислокациями.
Охрупчивание, вызванное присутствием водорода, приводит к межзеренному разрушению (рис. 4.30). Этот вид разрушения проявляется при низких скоростях деформации. Повышение скорости деформации существенно снижает эффект охрупчивания. Изменение скорости нагружения в исходном состоянии на пластичность образцов не влияет.
а |
б |
Рис. 4.30. Межзеренное разрушение, обусловленное водородным охрупчиванием: а − ×1000; б − ×2600
174
К примеру, длительная выдержка (1000 ч) стали 15Х2МФА в среде водорода при Р = 17…50 МПа приводит к снижению значений ударной вязкости KСV и доли волокна в изломе на 10–30 %. При этом в изломе ударных образцов возрастает доля межзеренного разрушения, указывающего на значительное снижение уровня когезивной прочности границ зерен.
Одновременно наблюдается существенное возрастание работы распространения вязкой трещины. Присутствие водорода вызывает развитие водородной коррозии. В мартенситных или дисперсионнотвердеющих сталях, обладающих высоким пределом текучести, наличие даже следов водорода оказывается достаточным, чтобы вызвать охрупчивание при комнатной температуре
Под радиационным охрупчиванием понимают эффект смещения температуры вязко-хрупкого перехода под воздействием быстрых нейтронов, характеризуемым нейтронным спектром и нейтронным потоком (рис. 4.31). Спектр определяет набор дискретных уровней энергии
нейтронов. Нейтронный поток характеризует |
интенсивность радиации |
и выражается числом нейтронов (обычно |
с энергией >0,1 МэВ), |
пересекающих площадь 1 см2 за 1 с [нейтрон/см2]. Нейтронный поток, суммированный во времени (нейтрон/см2), или флюенс нейтронов, − мера накопления радиационного воздействия.
Под действием потока нейтронов в конструкционных сталях происходят значительные структурные изменения. В образцах стали 10ХМФТ, вырезанных из реактора ВВЭР-440, образуются радиационные дефекты − дислокационные петли, дискообразные и округлые выделения. Дискообразные выделения в этой стали являются карбидами ванадия, имеющими толщину 1–2 нм и средний диаметр ≥10 нм. Их число по сравнению с исходным состоянием может возрасти на два порядка.
Во внутренних объемах зерен появляются округлые предвыделения размером 2–3 нм, обогащенные атомами меди.
Радиационное охрупчивание приводит к повышению предела текучести и, в меньшей степени, временного сопротивления, снижению поперечного сужения и ударной вязкости на верхнем плато.
Охрупчивание нелинейно возрастает с накоплением дозы облучения. Наиболее интенсивно охрупчивание стали происходит в начальный период облучения.
175
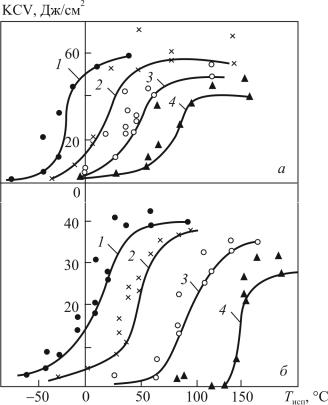
Степень радиационного охрупчивания конструкционных материалов с ОЦК-решеткой заметным образом зависит от его химического состава. В наибольшей степени склонность к радиационному охрупчиванию возрастает при легировании углеродистой стали медью. Снижение в стали концентрации примесных элементов P, S, As, Sn, Sb способно значительно повысить стойкость против радиационного охрупчивания. В целом сдвиг температуры вязко-хрупкого перехода после облучения вызван действием трех механизмов охрупчивания: упрочнение матрицы, образование зернограничных и внутризеренных сегрегаций.
Рис. 4.31. Температурные зависимости ударной вязкости для сталей Ст.3 (а) и 15ХСНД (б): 1 − исходное состояние материала;
2, 3, 4 − после облучения при 70 °С до флюенса нейтронов (2–3)×1022, (4–6)×1022 и (1,7–1,9)×1023 м–2 соответственно
Явление науглероживания заключается в насыщении поверхностых слоев металла углеродом, вызывающим изменение химического состава и механических свойств (рис. 4.32).
176
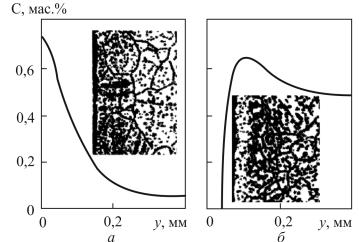
Рис. 4.32. Характерное распределение углерода по сечению деталей после выдержки в науглероживающей среде
Условия эксплуатации в нефтехимической промышленности труб, печных змеевиков часто приводят к науглероживанию их внутренней поверхности. Формирование на поверхности труб науглероженного слоя, обладающего ограниченной пластичностью и склонностью к растрескиваию, существенно ограничивает срок службы змеевиков трубчатых печей. Наиболее часто для изготовления таких изделий применяются жаропрочые стали 15Х5М, 10Х2М1, 45Х18Н25С5 и др. Они эксплуатируются взмеевиках трубчатых печей до температуры 1000 °С.
Трещины образуются из-за перегрузки хрупкого науглероженного слоя при совместном деформировании с пластичной матрицей стали. Разрушение трубы происходит при температурах ниже 450 °С, когда проросшая через толщину науглероженного слоя трещина не «завязнет» в металле трубы.
Допустимая толщина науглероженного слоя может быть рассчи-ана из условия обеспечения прочности стенки как слоистого композита, в котором вклад каждого слоя в прочность зависит от объемной доли слоя. В зависимости от условий эксплуатации распределение углерода по сечению элемента конструкции может быть разным. Для толстостенных элементов, работающих в среде с высокой активностью углерода конструкций, характерно поверхностное науглероживание с классическим диффузионным профилем (см. рис. 4.32, а). В тонкостеных деталях, длительно подвергающихся науглероживанию в окисли- ельно-востановительной среде с низкой активностью углерода,
177
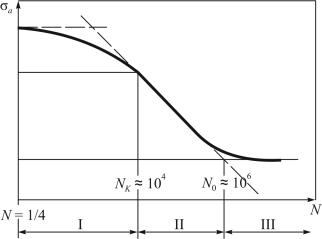
наблюдается иная ситуация. Вследствие ухода карбидообразующих элементов в оксидную пленку у поверхности возникает обедненная зона и обратный «профиль» (см. рис. 4.32, б). В последнем случае распределение углерода близко к равномерному.
По трещинообразованию наиболее опасен первый случай науглеоживания. Присутствие в поверхностном слое карбидов, к тому же преимущественно по границам зерен перлита, обусловливает его повышенную хрупкость. Трещинообразование в стали при комнатной температуре происходит в условиях растяжения на несколько проценов. При комнатной температуре глубина трещины практически совпаает с толщиной науглероженного слоя.
4.4. Усталостное разрушение
Усталостное разрушение происходит при повторно-циклическом нагружении в результате накопления необратимых повреждений. При этом виде разрушения на поверхности тела вначале появляются микротрещины, одна из которых в результате многократного приложения нагрузки прорастает в макротрещину с последующим полным разрушением образца или детали машин.
Первооткрывателем явления стал Вильгельм Альберт, но термин «усталость» был введен в 1839 г. французским ученым Ж.-В. Понселе, который обнаружил снижение прочности стальных конструкций при воздействии циклических напряжений.
Рис. 4.33. Полная кривая усталости: I, II и III − области усталости
178
Однако наибольший вклад в научную основу проектирования металлических конструкций, подвергаемых повторным напряжениям, внес немецкий инженер Август Велер своими классическими опытами с железом и сталью в условиях повторного растяжения-сжатия и изгиба, результаты которых были опубликованы в середине XIX в.
Л. Шпангерберг в 1874 г. впервые графически изобразил результаты исследований, опубликованных А. Велером в виде таблиц. С тех пор графическое представление полученной зависимости − диаграмму усталости − между амплитудами напряжения цикла σа и числом циклов нагружения до разрушения N называют диаграммой Велера (рис. 4.33).
4.4.1. Диаграмма усталости
Переменные напряжения характеризуются максимальными σmax, минимальными напряжениями σmin, амплитудой напряжения σа = (σmax + + σmin)/2, коэффициентом ассиметрии цикла R = σmin/σmax.
Пределом выносливости σw (σR) называется наибольшее по абсолютному значению напряжение σmax по достижению условного предельного числа циклов нагружения, являющегося базовым при таких испытаниях. У конструкционных сталей он достигает 107, а у сплавов цветных металлов – 108 циклов. Критерием разрушения является появление усталостной трещины или разрушение образца. Предел выносливости при симметричном цикле обозначают σ–1.
Процесс усталостного разрушения определяется уровнем приложенных переменных напряжений, а также разными условиями, интенсифицирующими действие приложенных напряжений. К таким факторам относится и влияние коррозионной среды, трение, износ и другие.
В целом выделяют:
–чистую усталость, обусловленную только влиянием переменных механических напряжений;
–усложненную усталость, возникающую при совместном влиянии переменных механических нагрузок, внешней среды и дополнительных процессов, протекающих в металле.
В условиях чисто переменного механического нагружения сопротивление металла разрушению существенным образом зависит от уровня приложенных напряжений, для отображения связи которого с числом циклов нагружения используют полную кривую усталости (рис. 4.34).
179

Рис. 4.34. Схематическое изображение полной кривой усталости : σвр , σнр − напряжение верхнего и нижнего разрыва; σк − критическое напряжение; σR − предел выносливости (усталости); σцт − циклический предел текучести; σцуп − циклический предел упругости; Nк − критическое число циклов; NR − минимальное критическое число циклов, необходимое для разрушения
На кривой можно выделить ряд характерных участков и перегибов. Вся кривая в первую очередь разделяется на две основные области: мало- и многоцикловой усталости. Границей между ними является напряжение, равное динамическому пределу текучести, т.е. определенному при скорости нагружения циклических испытаний. Область малоцикловой усталости охватывает диапазон напряжений σв > σрн, где σрн − где напряжения нижнего разрыва на кривой усталости, в пределах которой с первых циклов нагружения подводимая энергия расходуется на зарождение микротрещин. В самой малоцикловойобласти выделяют три участка.
На участках I и II разрушение носит квазистатический характер с образованием шейки в месте разрыва. В процессе циклов нагружения происходит накопление пластической деформации.
180