
книги / Экспертиза качества и разрушений
..pdf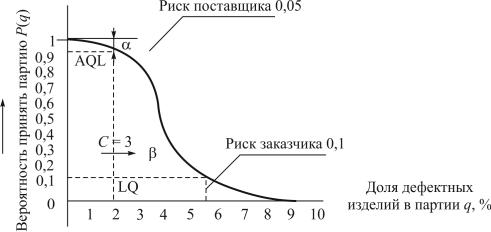
Рис. 2.5. Оперативная характеристика
2.11. Принципы применения стандартов на статистический приемочный контроль по альтернативному признаку
Рассмотрим порядок применения стандарта ГОСТ 18242–72 «Качество продукции. Статистический приемочный контроль по альтернативному признаку. Одноступенчатые и двухступенчатые корректируемые планы контроля».
Аналогом этого стандарта является международный стандарт ISO 2859. Указанный стандарт может применяться для контроля всех видов продукции производственно-технического назначения и товаров народного потребления штучной продукции, поступающих на контроль в виде единичных партий или последовательности работ.
Для выбора плана выборочного контроля необходимо установить следующие показатели:
–объем партии;
–виды дефектов;
–уровень контроля;
–приемочный уровень дефектности AQL;
–тип плана выборочного контроля;
–вид контроля.
Кратко рассмотрим приведенные выше показатели.
Объем контролируемой партии должен, как правило, указываться в нормативно-технической документации на продукцию как одним чис-
51
лом, так и предельными значениями или в виде одиночных партий либо последовательности партий.
Виды дефектов. Ранее отмечалось, что статистический приемочный контроль может осуществляться с разделением дефектов на критические, значительные и малозначительные.
Параметры или свойства единиц продукции, нарушение которых приводит к критическим дефектам (например, авиационная продукция), следует подвергать сплошному контролю или испытаниям. В случаях, где единственно возможным методом контроля критических дефектов является разрушающий контроль (например, цельносварные изделия ракетной техники), можно проводить выборочный контроль. В этом случае приемочное число Aс = 0, а браковочное число Rс = 1.
Объем выборки определяется по формуле
n = k/p, |
(2.9) |
где k – коэффициент, зависящий от риска появления одной дефектной единицы продукции в выборке; p – максимально допустимый процент дефектных единиц продукции в партии.
Значения коэффициентов k приведены в табл. 2.1.
Таблица 2 . 1
Значения коэффициентов k
от риска проявления дефектной единицы
Риск появления одной дефектной |
Коэффициент k |
единицы продукции в выборке |
|
1 в 10 |
230,26 |
1 в 100 |
460,52 |
1 в 1000 |
690,78 |
1 в 10000 |
921,04 |
1 в 100000 |
1151,30 |
Рассмотрим пример. На контроль предъявлена партия в 10 000 единиц продукции. Контроль разрушающий. Максимально допустимый процент единиц продукции с критическим дефектом p составляет 2 %. Риск появления дефектных единиц продукции – одна дефектная единица в партии. Требуется определить план выборочного контроля.
Объем выборки определяем по формуле n = k/p = k/2.
Пользуясь данными табл. 2.1, находим k = 921,04. Тогда n = 460,52. Округляя, получим n = 461.
52
Таким образом, план выборочного приемочного контроля имеет следующие параметры: n = 461; Ac = 0; Rc = 1 или (461; 0; 1). Очевидно, что если в выборке из n = 461 не обнаружится ни одной дефектной единицы продукции, то партия принимается. Если будет обнаружена хотя бы одна дефектная единица, то партия бракуется.
Продукция со значительными и малозначительными дефектами может проверяться сплошным или выборочным контролем. При выборочном контроле каждой группе дефектов должен быть назначен свой приемочный уровень дефектности в соответствии с табл. 2.2.
|
Таблица 2 . 2 |
Приемочный уровень дефектности |
|
|
|
Класс дефекта |
Приемочный уровень дефектности, % |
Значительный |
0,4 |
Малозначительный |
1,5 |
Вэтом случае имеются два плана выборочного контроля, соответствующие этим приемочным уровням дефектности. Если партия не удовлетворяет хотя бы одному плану или обоим вместе, она будет забракована.
Уровни контроля. Стандарт ГОСТ 18242–72 содержит семь уровней контроля: I, II, III (общие); S-1; S-2; S-3; S-4 (специальные). Основным для применения является уровень контроля II. Специальные уровни контроля используются тогда, когда объем выборки невелик. Уровень контроля устанавливается соответственно нормативно-техничес- кой документации на конкретный вид продукции.
Приемочный уровень дефектности AQL является основным пунктом стандарта. Предполагается, что между поставщиком и потребителем имеется договоренность, согласно которой потребитель рассматривает AQL как соответствующий его требованиям, а поставщик должен предъявлять на контроль партии продукции с фактическим уровнем дефектности не больше приемочного.
Втаблицах стандарта приведены AQL от 0,1 до 10 % для доли дефектности и от 10 до 1000 дефектов для числа дефектов на 100 единиц продукции.
Типы планов выборочного контроля. В стандарте содержатся сле-
дующие типы планов выборочного контроля: одноступенчатые, двухступенчатые, многоступенчатые и последовательные. На рис. 2.6 приве-
53
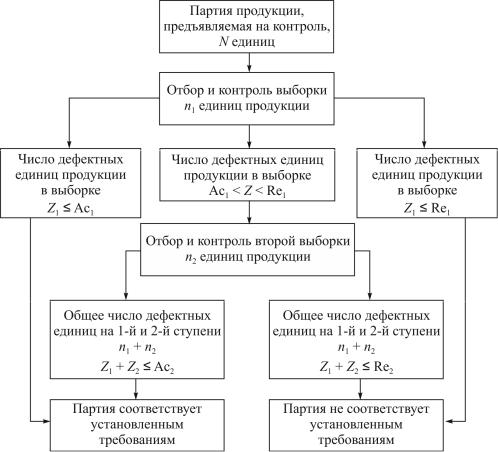
дена схема двухступенчатого плана контроля. В случае контроля одиночных партий продукции выбор плана контроля целесообразно осуществлять на основе анализа оперативной характеристики с учетом браковочного уровня дефектности.
Рис. 2.6. Схема двухступенчатого плана выборочного контроля
2.12. Статистический приемочный контроль по количественному признаку
Считается, что статистический приемочный контроль по количественному признаку при одном и том же объеме выборки представляет больше информации, чем приемочный контроль по альтернативному признаку. Однако это не означает, что последний хуже. Приемочный контроль по количественному признаку имеет свои недостатки: наличие дополнительных ограничений, сужающих область применения. Разра-
54
ботка планов может потребовать больших затрат труда, и для контроля часто требуется более сложное оборудование.
Если осуществлять разрушающий контроль, то планы контроля по количественному признаку окажутся экономичнее планов по альтернативному признаку. При контроле по количественному признаку качество партии продукции оценивается среднеарифметическим и среднеквадратическим отклонениями контролируемого параметра, а также зависящим от них уровнем дефектности.
Эти показатели качества включаются в планы контроля. Статистический приемочный контроль по количественному при-
знаку представлен ГОСТ 20736–75. Стандарт учитывает требования международного стандарта ISO 3951. Данный стандарт может быть использован для контроля всех видов штучной продукции, поступающей на контроль в виде одиночных партий при нормальном законе распределения одного или двух контролируемых параметров.
Контроль по количественному признаку заключается в том, что у единиц продукции измеряют численное значение контролируемого параметра, затем вычисляют выборочное среднеарифметическое значение X и оценивают его отклонение γ от значения верхней Тв или нижней Тн границ допуска. Для выбора плана выборочного контроля необходимо установить следующие показатели:
–объем партии продукции;
–уровень контроля;
–приемочный уровень контроля AQL;
–вид контроля;
–среднеквадратическое отклонение или метод его оценки;
–способ контроля.
Кратко рассмотрим эти показатели.
Объем партии устанавливается нормативно-технической документацией, а также стандартом.
Уровень контроля. Стандарт устанавливает пять уровней контроля: I, II, III (общие уровни), S-3, S-4 (специальные уровни). Основным является II уровень, с него начинают контроль.
Приемочный уровень дефектности является центральным пунктом стандарта. В таблицах стандарта содержится 14 значений AQL в диапа-
зоне от 0,04 до 15,0.
Виды контроля. Их установлено три: нормальный, усиленный и ослабленный контроль.
55
Нормальный контроль является основным видом контроля и применяется во всех случаях, если в нормативно-технической документации неоговорено применение другого вида контроля. Нормальный контроль ведется до тех пор, пока поставщик предъявляет на контроль партии продукции, соответствующие установленному значению приемочного уровня дефектности. Если эти условия нарушаются, то переходят к усиленномуконтролю.
Среднеквадратическое отклонение и метод его оценки. При контроле по количественному признаку в ряде случаев среднеквадратическое отклонение σ контролируемого параметра заранее бывает известно (например, технологический процесс стабилен) либо неизвестно. В первом случае используется σ – план выборочного контроля. Этот метод предусматривает наименьший объем выборки по сравнению с другими методами и требует меньше вычислений. Если σ неизвестно, стандарт предусматривает два метода его оценки:
•по выборочному среднеквадратическому отклонению S (S-план),
•по размаху R (R-план).
S-план (или S-метод) предпочтительнее, так как требует меньшего объема выборки, чем R-план. При использовании R-метода следует иметь в виду, что чем больше объем выборки, тем меньше информации дает ее размах о значении среднеквадратического отклонения σ. При объеме выборки больше восьми единиц продукции оценивать σ по размаху не рекомендуется. В этих случаях стандарт предусматривает применение среднего размаха R. Для определения R выборку делят на несколько подгрупп по пяти результатам измерений вкаждой подгруппе. Определяют
R = X max |
− Xmin |
; |
|
= ΣRi . |
(2.10) |
R |
|||||
|
|
|
|
n |
|
Способ контроля. Стандартом предусмотрены три способа выбора плана выборочного контроля.
Первый способ заключается в том, что вычисленное отклонение γ сравнивается со значением контрольного норматива K (KS, KR, Kσ), который находится из таблиц стандарта. Если γ > K – партию принимают. Если γ < K или хотя бы одна из величинγ отрицательна, то партию бракуют.
Второй способ заключается в том, что по вычисленному отклонению γ и объему выборки с помощью таблиц стандарта находят оценочное значение входного уровня дефектности P. Величину Р сравнивают
56
с допускаемым уровнем дефектности М (MS, MR, Mσ), значения которого находят из таблиц стандарта. Если Р < М – партию принимают. Если Р > М или хотя бы одна из величин Р отрицательна, то партию бракуют.
Графический способ заключается в том, что по значениям границы контролируемого параметра, среднеарифметического значения X
исреднеквадратического отклонения σ определяют точки значений σ/(Тв – Тн) и (X – Тн)/(Тв – Тн), которые затем наносят на номограмму,
ипо расположению этих точек принимают решение.
Общий подход к текущему контролю качества достаточно прост. В процессе производства проводятся выборки изделий заданного объема. После этого на специально разлинованной бумаге строятся диаграммы изменчивости выборочных значений плановых спецификаций
вэтих выборках и рассматривается степень их близости к заданным значениям. Если диаграммы обнаруживают наличие тренда выборочных значений или оказывается, что выборочные значения находятся вне заданных пределов, то считается, что процесс вышел из-под контроля, и предпринимаются необходимые действия для того, чтобы найти причину его разладки. Иногда такие специально разлинованные бумаги называют контрольными картами Шуэрта (по имени W.A. Shewhart, который общепризнанно считается первым применившим на практике описываемые здесь методы анализа).
Интерпретация контрольных карт. В компьютерном варианте контрольных карт наиболее часто встречается ситуация, когда на экране находятся две карты (и две гистограммы), одна из них называется Х-картой, а другая – R-картой.
Вобеих контрольных картах по горизонтальной оси откладываются номера соответствующих выборок; по вертикальной оси в случае X-карты отложены выборочные средние исследуемых характеристик, а в случае R-карты – размахи соответствующих выборок (рис. 2.7). Пусть, например, производятся контрольные измерения диаметра поршневых колец, изготавливаемых на вашем предприятии. Тогда центральная линия на X-карте будет соответствовать размеру, используемому в качестве стандарта (например, установленному диаметру кольца
вмиллиметрах), в то время как центральная линия R-карты будет соответствовать приемлемому (т.е. находящемуся в пределах плановой спецификации) размаху диаметра поршневого кольца в выборках; таким образом, последняя контрольная карта представляет собой карту изменчивости процесса (чем больше изменчивость, тем больше диапазон от-
57
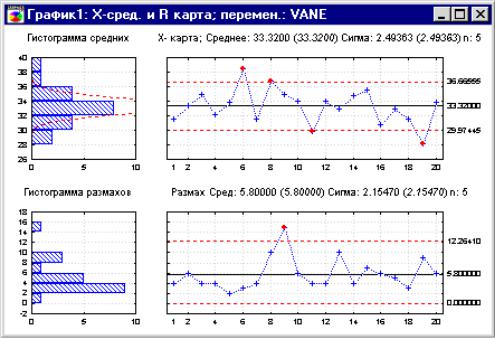
клонения от стандарта). Кроме центральной линии, на карте обычно присутствуют две дополнительные горизонтальные прямые, обозначающие верхний и нижний контрольные пределы (ВКП и НКП соответственно). Принципы определения этих линий рассматриваются ниже. Обычно нанесенные на карты отдельные точки соответствуют выборочным значениям и соединяются прямыми линиями. Если результирующая кривая на графике выходит за верхний или нижний контрольный предел или ее конфигурация выражает определенную тенденцию поведения для следующих друг за другом выборок, то это рассматривается как указание на существование проблем с качеством.
Рис. 2.7. X- и R-карты
Установка контрольных пределов. Несмотря на то, что можно дос-
таточно произвольно определить момент разладки производственного процесса (например, при выходе соответствующих значений за границы верхних и нижних контрольных пределов), обычной практикой является применение статистических методов для определения этого момента.
Пример. Предположим, вы контролируете среднее значение некоторой величины – например, диаметра поршневых колец. Пусть среднее значение диаметров и дисперсия в процессе производства не меняются. Тогда
58

выборочные средние, полученные для последовательных выборок, будут распределены нормально относительно истинного среднего. Более того, не вдаваясь в тонкости, связанные с выводом формул, можно заключить (согласно центральной предельной теореме и сделанному предположению о нормальности выборочных средних размеров колец), что стандартное отклонение распределения выборочных средних будет равно сигме (стандартному отклонению отдельных наблюдений или измерений диаметра отдельных колец), деленному на квадратный корень из n (n – размер выборки). Следовательно, примерно 95 % значений выборочных средних по-
падут в интервал µ ± 1,96σ n . На практике обычно заменяют 1,96 на 3 (при этом в интервал попадают приблизительно 99 % выборочных средних) и определяют верхний и нижний контрольные пределы как ±3σ соответственно.
Наиболее часто используемые типы контрольных карт. Класси-
фикация типов контрольных карт часто осуществляется согласно типам величин, которые выбраны для отслеживания характеристик качества. Так, различают контрольные карты для непрерывных переменных
иконтрольные карты по альтернативному признаку. В частности, для контроля по непрерывному признаку обычно строятся следующие контрольные карты:
X-карта. На эту контрольную карту наносятся значения выборочных средних для того, чтобы контролировать отклонение от среднего значения непрерывной переменной (например, диаметров поршневых колец, прочности материала и т.д.).
R-карта. Для контроля за степенью изменчивости непрерывной величины в контрольной карте этого типа строятся значения размахов выборок.
S-карта. Для контроля за степенью изменчивости непрерывной переменной в контрольной карте данного типа рассматриваются значения выборочных стандартных отклонений.
S**2-карта. В контрольной карте данного типа для контроля изменчивости строится график выборочных дисперсий.
Для контроля качества продукции по альтернативному признаку обычно применяются следующие типы контрольных карт:
C-карта. В таких контрольных картах строится график числа дефектов (в партии, в день, на один станок, в расчете на 100 футов трубы
ит.п.). При использовании карты этого типа делается предположение,
59
что дефекты контролируемой характеристики продукции встречаются сравнительно редко, при этом контрольные пределы для данного типа карт рассчитываются на основе свойств распределения Пуассона (распределения редких событий).
2.13. Вопросы организации контроля и обеспечение качества выпускаемой продукции в условиях массового производства
Техническим контролем называется проверка соответствия процессов, от которых зависит качество продукции, и их результатов установленным технически требованиями. Исходя из изложенного объектами контроля в действующем производстве являются исходные материалы, технологические процессы, полуфабрикаты, а также готовая продукция. Задача технического контроля в условиях машиностроительных предприятий связана с гарантированным выпуском качественной продукции. Рациональное качество контроля должно обеспечить:
–его профилактичность;
–достаточную точность контроля, которая достигается соответствующим выбором методов и средств анализа;
–объективность и надежность контроля.
Техника статистического контроля многообразна. Она включает планы выборочных проб, применение вероятностной бумаги и специальных контрольных карт самого разнообразного объема и назначения. Другой технической задачей контроля качества является анализ дефектов и причин брака. Решение этой задачи преследует три цели:
–выявление брака по вине поставщика;
–выявление брака в собственном производстве;
–анализ рекламаций.
Многолетняя практика заводов показывает, что необходимость в специальных исследованиях возникает в редких случаях, когда экономически целесообразно применение сложной современной техники.
60