
- •СОДЕРЖАНИЕ
- •Системы вентиляции промышленных зданий в сравнении с системами общественных зданий имеют следующие отличительные особенности:
- •1. Большие расходы воздуха;
- •2. Большие скорости движения воздуха в воздуховодах;
- •3. Большие площади поперечных сечений воздуховодов;
- •4. Применяются в основном воздуховоды круглого сечения;
- •7. Проектирование и монтаж систем промышленной вентиляция отличается специфическими требованиями к их конструированию в зависимости от технологических особенностей производственных процессов.
- •8. Высокая концентрация вредных компонентов в удаляемом воздухе требует либо его очистки в специальном оборудовании перед выбросом в атмосферу, либо организации “факельного выброса” для снижения концентрации вредностей в приземном слое атмосферы.
- •Расчёт и подбор устройств для очистки вытяжного воздуха производится по специальным методикам, приведённых в нормативно-справочной документации, для соответствующих видов производств.
- •9. Местные системы вентиляции и кондиционирования воздуха компонуются в системы по технологическим линиям производства, по одновременности действия оборудования, по видам вредных выделений и по оптимальным расходам воздуха.
- •2. ВРЕДНЫЕ ВЫДЕЛЕНИЯ НА ПРОМЫШЛЕННЫХ ПРЕДПРИЯТИЯХ
- •Избыточная теплота.
- •Источниками теплоты в промышленных производствах могут быть:
- •2. сушильные установки; 5. источники искусств. освещения;
- •3. теплота нагретой продукции; 6. эл.двигатели и др.
- •Количество выделяющейся теплоты определяется по результатам составления теплового баланса в каждом из производств по соответствующей методике.
- •Избыточная влага.
- •Источником влаговыделений могут быть:
- •1. ванны и аппараты с горячей водой;
- •2. сушильные установки;
- •3. смоченные поверхности;
- •4. обрабатываемая продукция
- •5. установки, использующие технологический пар и др.
- •5. красильно-отделочные предприятия легкой промышленности;
- •6. предприятия пищевой промышленности;
- •7. коммунальные предприятия и др.
- •Определение количества влаговыделений проводят в зависимости от источника и вида выделяющейся влаги.
- •Вредные газы и пары.
- •Многие промышленные производства сопровождаются выделением вредных (часто ядовитых) газов и паров.
- •Ядами называют вещества, которые попадая в организм человека даже в незначительных количествах приводят к отравлениям и заболеваниям.
- •x2…xn компонентов смеси вредных газов, м3/ч.
- •Так, например, поступают при одновременном выделении паров растворителей совместно с окислами азота.
- •Расчет количества выделяющихся паров и газов в большинстве случаев проводят по эмпирическим зависимостям, определенным для каждого вида вредностей.
- •Среди наиболее характерных и вредных газов и паров следует отметить:
- •Кроме непосредственного влияния на организм человека пары и газы взрывоопасны при определенном процентном соотношении в смеси с воздухом или кислородом.
- •Классификация вытяжных зонтов
- •Зонты-козырьки над загрузочными отверстиями электрических печей
- •9.6. Пылевые вентиляторы для систем аспирации и пневмотранспорта
7
2. ВРЕДНЫЕ ВЫДЕЛЕНИЯ НА ПРОМЫШЛЕННЫХ ПРЕДПРИЯТИЯХ
Избыточная теплота.
Источниками теплоты в промышленных производствах могут быть:
1. промышленные печи; |
4. солнечная радиация; |
2.сушильные установки; 5. источники искусств. освещения;
3.теплота нагретой продукции; 6. эл.двигатели и др.
Наибольшим количеством тепловыделений отличаются предприятия: 1. металлургической промышленности; 2. машиностроительные (кузнечные, литейные, термические и др. цеха);
3. энергетической промышленности (котельные и машинные залы); 4. стекольной промышленности и др.
Количество выделяющейся теплоты определяется по результатам составления теплового баланса в каждом из производств по соответствующей методике.
Избыточная влага.
Источником влаговыделений могут быть:
1.ванны и аппараты с горячей водой;
2.сушильные установки;
3.смоченные поверхности;
4.обрабатываемая продукция
5.установки, использующие технологический пар и др.
С выделением избыточной влаги связаны следующие производства: 1. гальванические и травильные цеха машиностроительных заводов; 2. разливочные цеха металлургических предприятий; 3. машинные залы ТЭЦ; 4. бумажно-целлюлозные предприятия;
5. красильно-отделочные предприятия легкой промышленности;
6. предприятия пищевой промышленности;
7. коммунальные предприятия и др.
8
Свободно поступающая в воздух влага может приводить к образованию тумана и выпадению конденсата на поверхностях производственного помещения, что для большинства помещений не соответствует требованиям норм по обеспечению санитарно-гигиенических и технологических требований к микроклимату.
Определение количества влаговыделений проводят в зависимости от источника и вида выделяющейся влаги.
Вредные газы и пары.
Многие промышленные производства сопровождаются выделением вредных (часто ядовитых) газов и паров.
Ядами называют вещества, которые попадая в организм человека даже в незначительных количествах приводят к отравлениям и заболеваниям.
При одновременном выделении нескольких видов газов и паров однонаправленного (по степени воздействия на человека) действия общий объем необходимого вентиляционного воздуха определяют суммированием объемов воздуха, необходимых для разбавления каждого вредного компонента.
Lв = Lx1 + Lx2 +…+ Lxn, (2.1)
где Lв – общий объем необходимого вентиляционного воздуха, м3/ч; Lx1, Lx2, Lxn – объемы воздуха, необходимые для разбавления x1,
x2…xn компонентов смеси вредных газов, м3/ч.
Так, например, поступают при одновременном выделении паров растворителей совместно с окислами азота.
При одновременном выделении вредностей не обладающих однонаправленным действием за необходимый объем воздуха принимают большее значение из определенных по каждому компоненту. Так, при расчете необходимого воздухообмена при одновременном выделении теплоты и влаги значение Lв принимают по большему из LQ и Lw, где LQ, м3/ч – количество воздуха, необходимое для ассимиляции теплоизбытков; Lw – то же, для влагоизбытков.
9
Расчет количества выделяющихся паров и газов в большинстве случаев проводят по эмпирическим зависимостям, определенным для каждого вида вредностей.
Среди наиболее характерных и вредных газов и паров следует отметить:
1.Окись углерода (СО) – угарный газ. Вызывает удушье и наиболее часто приводит к отравлениям с тяжелыми последствиями. Присутствует в выхлопных газах автомобилей, в продуктах сгорания топливосжигающих установок, металлургическом производстве и др.
2.Сернистый газ (SO2) – диоксид серы. Выделяется при производстве серной кислоты, целлюлозы, при сжигании твердого топлива содержащего серу
идр. Вызывает раздражение дыхательных путей в организме человека.
3.Азотная кислота и окислы азота. Азотная кислота (HNO3) и ее производные применяются в химической, текстильной промышленности, машиностроении (гальванические цеха), производстве удобрений и др. Определенные концентрации могут вызывать отек легких. Производные азотной кислоты встречаются также в продуктах горения угля и нефтепродуктов.
4.Растворители – группа веществ, применяющихся в промышленности для обезжиривания продукции, приготовления лаков, красок, растворения органических веществ. Летучесть паров растворителей способствует их проникновению в организм человека и создает опасность отравления.
Кроме непосредственного влияния на организм человека пары и газы взрывоопасны при определенном процентном соотношении в смеси с воздухом или кислородом.
Взрыв — физический или/и химический быстропротекающий процесс с выделением значительной энергии в небольшом объёме (по сравнению с количеством выделяющейся энергии), приводящий к ударным, вибрационным
итепловым воздействиям на окружающую среду и высокоскоростному расширению газов.
10
Горе́ние — сложный физико-химический процесс превращения компонентов горючей смеси в продукты сгорания с выделением теплового излучения, света и лучистой энергии. Иногда горение определяют как экзотермическое окисление.
Минимальное процентное соотношение газов или паров с воздухом, при котором наступает условие взрыва, называется нижним пределом взрываемости (НПВ).
Максимальное процентное соотношение газов или паров в смеси с воздухом, при котором существует условие взрыва, называется верхним пределом взрываемости (ВПВ). Газ или пар считается взрывоопасным, если его относительная концентрация находится между нижним и верхним пределами взрываемости.
С точки зрения взрывобезопасности безопасная концентрация газов и паров в воздухе производственных помещений не должна превышать 30 % от НПВ.
Значения пределов взрываемости для наиболее распространенных газов и паров, образующихся на промышленных предприятиях приведены в табл. 2.1
Таблица 2.1
№ |
Наименование вещества |
НПВ, % |
|
ВПВ, % |
п/п |
|
|||
|
|
|
|
|
1. |
Угарный газ СО |
16,1 |
|
73,4 |
|
|
|
|
|
2. |
Этиловый спирт (этанол) С2Н5ОН |
4,0 |
|
13,6 |
3. |
Аммиак NH3 |
16,5 |
|
26,8 |
4. |
Ацетон СН3СОСН3 |
3,0 |
|
9,0 |
5. |
Бензин CnHm |
2,5 |
|
4,8 |
6. |
Водород Н2 |
4,0 |
|
75,0 |
7. |
Метан СН4 |
6,0 |
|
13,9 |
|
Для определения пределов взрываемости Xсм |
паровоздушной смеси |
нескольких компонентов применяют закон Ле Шателье:
Хсм = |
|
|
|
100% |
|
|
, |
||
Р |
+ |
Р |
+...+ |
Р |
|||||
|
|
1 |
2 |
n |
|
|
|||
Х1 |
Х2 |
Хn |
|||||||
|
|
|
|
где P1, P2,…, Pn – относительные (процентные) концентрации компонентов в смеси;
X1, X2,…, Xn – пределы взрываемости компонентов смеси.
11
(2.2)
Пыль.
Под термином пыль понимают материальную систему, состоящую из мельчайших частичек твердого вещества, рассеянных в газообразной среде. Такие системы называют дисперсными. Дисперсные системы состоят из дисперсной фазы (мельчайшие твердые частицы) и дисперсионной среды (газ, воздух). Когда частицы пыли находятся во взвешенном состоянии в воздухе, их называют аэрозолями. Когда масса газовой составляющей мала (осаждение, скопление пыли), смесь называют аэрогелем.
Источником пыли являются технологические процессы, связанные - с дроблением, шлифовкой, механической очисткой поверхностей
деталей, обработкой древесины и др. При некоторых способах окраски выделяется “красочная пыль” (аэрозоль).
Постоянным выделением пыли сопровождаются производства на следующих предприятиях:
1.текстильной промышленности;
2.деревообрабатывающей промышленности;
3.горнорудной промышленности;
4.зерноперерабатывающей промышленности;
5.металлообрабатывающей промышленности.
По действию на организм человека различают:
- ядовитую пыль (напр. свинцовая, ртутная), которая вызывает отравления с тяжелыми последствиям;
12
- неядовитую (древесная, песчаная, абразивная), которая не вызывает острых отравлений, но при длительном вдыхании может приводит к различным заболеваниям легких.
Пыль от веществ легко сгорающих в воздухе (уголь, мука, сахар, табак и др.) взрывоопасна. Это является следствием очень развитой суммарной поверхности размельченного вещества, что приводит к многократному ускорению процессов обмена молекулами между дисперсной средой и фазой. Из-за возросшей поверхности контакта во много раз увеличивается электроемкость частиц, что в результате, при определенной концентрации пыли в воздухе или ином газе может привести к взрыву.
Запыленность воздуха обычно оценивают в мг/м3.
2.1.Очистка воздуха от пыли
Вцелях защиты атмосферного воздуха от вент выбросов вытяжной воздух от оборудования, выделяющего пыль предварительно очищают. В целях сокращения энергозатрат на подогрев приточного воздуха в системах вентиляции часто используют рециркуляцию внутреннего воздуха. В этом случае также необходима тщательная очистка отработанного воздуха от пыли.
Взависимости от принципа действия все пылеулавливающие устройства могут быть разделены на следующие основные группы:
1. Пылеосадочные камеры.
Принцип действия основан на осаждении пыли под действием силы тяжести.
2. Циклоны (инерционные пылеуловители).
Принцип действия основан на использовании сил инерции при изменении направления движения потока запыленного воздуха. Применяют как одиночные, так и “батарейные”.
3. Тканевые, сетчатые, волокнистые фильтры.
Загрязненный воздух в этих устройствах проходит по каналам с изменением направления движения через слой фильтрующего материала
13
(ткань, бумага, металлические сетки, предварительно обработанные маслом и т.п.). Отделение пыли в фильтрах происходит за счет инерционных сил, гравитационных сил диффузионного осаждения.
4. Электрофильтры.
Основным элементом электрофильтров являются электроды с высоким напряжением, сообщающие пылевидным частицам положительный заряд, осадительные электроды, на поверхности которых оседают заряженные частицы и бункеры-пылесборники.
Независимо от принципа действия пылеуловители бывают “сухими” и “мокрыми”. Смачивание фильтрующей поверхности применяют для увеличения эффективности очистки. С этой целью применяются вода (мокрые циклоны) или масло (масляные ячейковые и сетчатые фильтры).
Также для повышения эффективности применяют комбинированную очистку, т.е. устанавливают последовательно различные по принципу действия фильтры.
Большинство фильтров характеризуется следующими основными показателями:
1.степень очистки (к.п.д.), %;
2.производительность (пропускная способность), м3/ч;
3.гидравлическое сопротивление, Па;
4.энергозатраты, кВт-ч/м3;
5.стоимость процесса очистки м3 (или 1000 м3) воздуха.
Для тканевых фильтров дополнительно обычно указывают их предельную пылеемкость – количество осажденной пыли, повышающей сопротивление проходу воздуху до определенных значений.
Степенью очистки называют отношение массы пыли, улавливаемой очищающим устройством, к первоначальной массе пыли, выраженное в процентах. Степень очистки можно также выразить через разность начальной
С1 , мг/м3, и конечной С2 концентраций пыли |
|
η = (С1 – С2 / С1) 100 % . |
(2.3) |
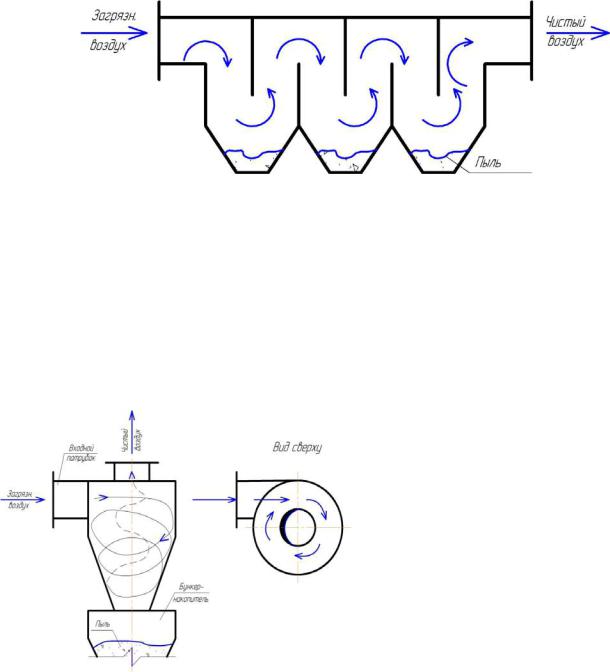
14
Рис. 2.1 Принципиальная схема пылеосадочной камеры
Достоинством пылеосадочных камер является простота эксплуатации, надежность и продолжительный срок эксплуатации. Применяются чаще в комплексе с другими фильтрами как первая ступень (грубой) очистки от крупных фракций пыли.
Циклоны применяются для
очистки вытяжного воздуха с высоким начальным пылесодержанием или содержанием взвешенных крупнодисперсных частиц, например, для очистки воздуха, удаляемого от деревообрабатывающих станков.
Рис. 2.2 Принципиальная схема циклона
Достоинством циклонов является простота устройства и эксплуатации, надежность работы, высокая степень очистки.
Опыт эксплуатации и испытаний различных типов циклонов показал, что для обеспечения эффективной очистки воздуха от взвешенных частиц пыли его скорость перед входным патрубком должна быть в пределах vвх = 10…25 м/с. Минимальное значение обусловлено удержанием частиц пыли во взвешенном
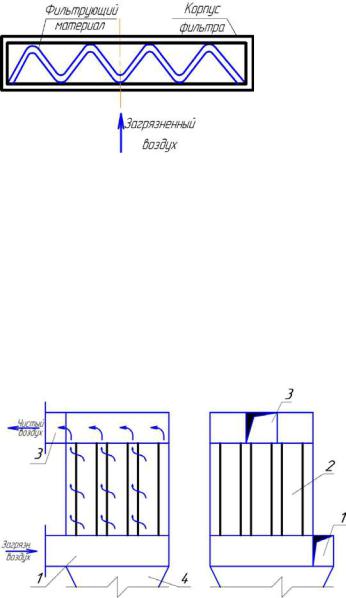
15
состоянии. Максимальное – из-за резкого возрастания гидравлического сопротивления проходу воздуха (пропорционально квадрату скорости) при незначительном повышении степени очистки.
В тканевых фильтрах
основным способом является инерционное осаждение частиц пыли в волокнах ткани. Фильтрующий материал сшивают
Рис. 2.3 Схема тканевого фильтра в виде мешков, рукавов или натягивается на каркас.
Для увеличения площади контакта фильтрующую поверхность выполняют зигзагообразно.
Одними из наиболее распространенных являются рукавные тканевые фильтры с устройством автоматического встряхивания для периодической очистки фильтрующего материала.
1 – входной патрубок;
2 – фильтрующий материал (рукав);
3 – выходной патрубок; 4 – бункернакопитель.
Рис. 2.4 Схема рукавного фильтра Достоинством тканевых фильтров является высокая (до 99 %) степень
очистки.
Недостатком – не все виды фильтрующего материала позволяют очищать воздух с повышенной влажностью или с температурой, при которой возможна конденсация водяных паров. Это приводит к заполнению пор фильтра и резкому снижению фильтрующей способности.
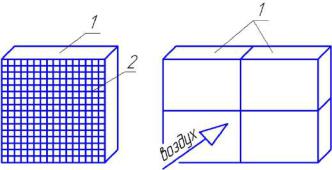
16
1 – ячейка фильтра;
2 – фильтрующий элемент.
Рис. 2.5 Схема масляного фильтра
В качестве фильтрующего заполнителя в масляных фильтрах применяют металлические сетки, стеклянное волокно или тонкостенные металлические кольца покрытые тонким слоем масла. Применяются масляные фильтры для тонкой очистки воздуха (степень очистки до 99 %). Как правило, фильтр набирается из отдельных ячеек, комплектующихся в зависимости от производительности и размеров в общий каркас в горизонтальной или вертикальной плоскости.
2.2. Очистка воздуха от вредных газов и паров
Состав промышленных вентиляционных выбросов отличается большим многообразием видов газообразных веществ и их свойств. Это связано с широкой номенклатурой используемого технологического оборудования, сырья и физико-химических процессов, проводимых при изготовлении продукции.
Вытяжной воздух термических цехов, оборудованных нагревательными печами на жидком и газообразном топливе, содержит пары аммиака, цианистого водорода HCN и других вредных веществ. Гальванические цеха и цехи механической обработки металлов используют при травлении поверхности металла растворы кислот - серной H2S04, соляной НС1, азотной HNO3 и плавиковой HF.
Вентвыбросы производств неметаллических изделий из стеклопластика, пластмасс, полимеров и лакокрасочных цехов также значительно загрязняют
17
окружающую среду. В атмосферу с выбрасываемым воздухом поступают пары растворителей, красок, SO2, СО, пары бензина, толуола, ксилола, изопропилового спирта и др.
Сырьем для предприятий химической промышленности служат нефть, природный газ, попутные газы, которые образуются, например, при коксовании углей на металлургических предприятиях, разнообразные химические вещества и соединения. К основным выбросам относятся С02, окислы азота NOx, сернистый ангидрид SO2, аммиак NH3 , сероводород H2S и сероуглерод CS2, хлористые, фтористые соединения и др.
Выбросы нефтеперерабатывающей и нефтехимической про-
мышленности содержат большое количество углеводородов и сероводорода. Заводы синтетического каучука выбрасывают в атмосферу стирол C8H8, толуол С6Н5СН3, ацетон (СH3)2СО и др. очень высокотоксичные вещества.
Выбросы могут быть нагреты до высоких температур, в них могут присутствовать аэрозольные частицы - пыль, сажа. Поступая в атмосферный воздух, газообразные вещества взаимодействуют друг с другом и могут превращаться в другие соединения, иногда даже более вредные для организма, чем исходные. Интенсивность выбросов по времени не всегда постоянна, изменяется концентрация в них различных вредных веществ и т. д. Зачастую загрязнения многокомпонентны и их необходимо подвергать различным методам обезвреживания.
Поэтому задача проектирования очистки воздуха от газовых загрязнений требует специальных знаний различных дисциплин, в первую очередь, химической технологии. Необходимо знать свойства реагирующих веществ и основные методы улавливания газовых загрязнений, учитывать особенности режимов работы существующего очистного оборудования и техникоэкономические показатели разных вариантов очистки.
Абсорбция газовых примесей
Некоторые жидкости при контакте с многокомпонентной газовой средой способны избирательно извлекать из нее отдельные ингредиенты и поглощать
18
их - сорбировать. Это свойство жидкостей используется при абсорбции* газовых примесей из вентвыбросов.
Вентиляционный воздух и примеси, которые находятся в газовой фазе и при абсорбции не переходят в жидкую фазу, называют газом-носителем. Жидкость, в которой происходит растворение абсорбируемых компонентов, называют абсорбентом (поглотителем или растворителем), а газ, переходящий в абсорбент, т.е. поглощаемый компонент - абсорбтивом.
Физическая сущность процесса абсорбции объясняется так называемой пленочной теорией, согласно которой при соприкосновении жидких и газообразных веществ на границе раздела фаз «газ-жидкость» образуется жидкостная и газовая пленки. Растворимый в жидкости компонент газовоздушной смеси проникает путем диффузии сначала через газовую пленку, а затем, сквозь жидкостную пленку, и поступает во внутренние слои абсорбента.
Для диффузии необходимо, чтобы концентрация растворяемого компонента в газовоздушной смеси превосходила его концентрацию в жидкости. Чем менее насыщена жидкость (раствор), тем больше она поглощает газа.
Процесс, завершающийся растворением абсорбтива в поглотителе, называют физической абсорбцией. При физической абсорбции происходит физическое растворение абсорбируемого компонента в растворителе, при этом молекулы абсорбента и молекулы абсорбтива не вступают между собой в химическое взаимодействие.
Иногда растворяющийся газ вступает в химическую реакцию непосредственно с самим растворителем, образуя новые химические соединения в жидкой фазе. Процесс, сопровождающийся химической реакцией между поглощаемым компонентом и абсорбентом, называют химической абсорбцией (хемосорбцией).
Интенсивность перехода загрязнителя из газовой фазы в жидкую (растворимость газа) зависит от температуры и давления компонентов, а также
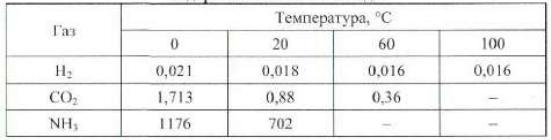
19
от способа организации контакта фаз. Влияние давления достаточно хорошо выражается законом Генри: при постоянной температуре растворимость газа в растворителе прямо пропорциональна давлению этого газа над раствором.
Как правило, растворение газов в жидкости происходит с выделением тепла и с уменьшением объема, поэтому в соответствии с принципом Ле-
Шателье, при повышении температуры их растворимость снижается. Эту зависимость иллюстрирует табл. 2.2, где приведены данные по содержанию (в нормальных литрах) некоторых газов в 1 л воды при стандартном давлении 101 300 Па:
Таблица 2.2
Содержание газов в 1 л воды
Внекоторых случаях, когда растворение сопровождается не выделением,
апоглощением тепла, возрастание температуры приводит к увеличению растворимости газа.
Вкачестве абсорбента может использоваться любая жидкость, которая растворяет извлекаемый компонент. Это может быть вода, растворы аммиака, едких и карбонатных щелочей, солей марганца, этаноламины, суспензии гидрооксида кальция, оксидов марганца и магния, сульфат магния и другие вещества. Главное, чтобы растворитель отвечал ряду требований, среди которых: необходимая поглотительная способность (абсорбционная ёмкость), высокая селективность (избирательность) по отношению к поглощаемому компоненту, невысокая летучесть во избежание загрязнения очищаемого газа парами абсорбента, небольшая вязкость, способность к регенерации. Поглотитель должен быть термо- и химически устойчивым, не проявлять коррозионную активность, быть доступным и недорогим.
20
При физической абсорбции в качестве абсорбента обычно используют воду. Вода - самый дешевый и доступный абсорбент, обладающий высокой эффективностью при удалении кислых растворимых газов, таких как SiF4, паров НСl, HF.
Газы с меньшей растворимостью, например S02, Сl2 легче абсорбируются не чистой водой, а щелочными растворами, в частности, разбавленным NaOH. Для поглощения газов, плохо растворимых в воде, применяют малолетучие органические растворители на основе углеводородов.
Абсорбенты, работающие при отрицательных температурах, принято называть хладоносителями, а процесс абсорбции, протекающий в таких условиях - контактной конденсацией.
Для повторного использования абсорбент подвергают регенерации, проводя процесс, обратный абсорбции - десорбцию (дегазацию, выпаривание). Так, если изменить условия, например, понизить давление над жидкостью или снизить температуру, то происходит выделение газа из жидкости. Сочетая абсорбцию с десорбцией можно многократно и почти без потерь использовать жидкий поглотитель в замкнутом цикле «абсорбция - десорбция - абсорбция», вновь подавая освобожденный поглотитель на стадию абсорбции, снова регенерировать и возвращать его в процесс.
Этот механизм также позволяет выделять из абсорбента поглощенный компонент в чистом виде и использовать в виде сырья д ля других процессов или целевого товарного продукта. Если извлекаемый компонент не представляет ценности или процесс регенерации связан с большими трудностями, то поглотитель используют однократно и после соответствующей обработки сливают в канализацию.
Помимо регенерации абсорбента с помощью десорбции абсорбированные загрязнения удаляют путём осаждения и отстаивания, химического разрушения в результате нейтрализации, окисления, восстановления или
гидролиза, а также экстракцией и другими методами.
Основным оборудованием для проведения физической и химической
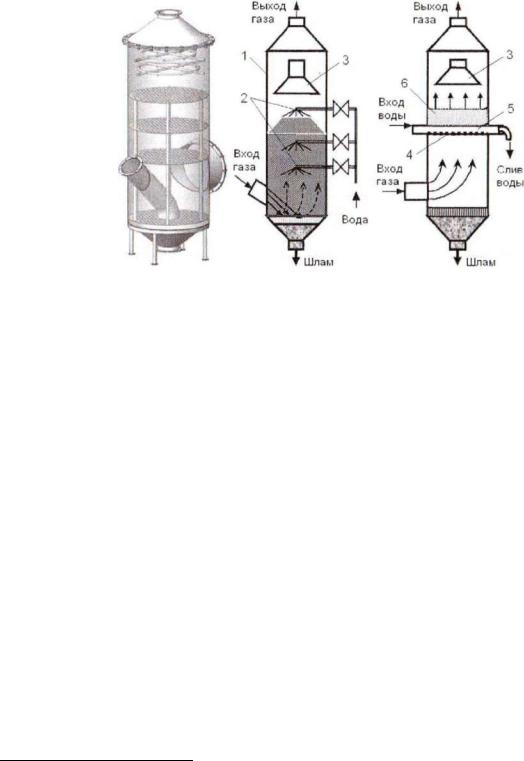
21
абсорбции служат полые распылительные и посадочные башни (рис. 2.6),
пенные аппараты и скрубберы1, различающиеся способом организации контакта фаз (капли или пена). Для более полного извлечения компонента из газовой смеси в них используется принцип противотока с непрерывной подачей в абсорбер свежего раствора.
Рис. 2.6 Распылительные и насалочные башни:
1 - корпус; 2 - форсунки; 3 - каплеотделитель; 4 - опорная решетка; 5 - ороситель; 6 - пористая насадка
Широко применяются скрубберы с подвижной насадкой, к достоинствам которых относятся высокая эффективность разделения при умеренном гидравлическом сопротивлении из-за высоко развитой поверхности контакта в виде тонкой пленки жидкости на элементах насадки, а также большая пропускная способность по газу. На рис. 2.7 показана принципиальная схема такого скруббера. В верхней части аппарата установлен ороситель 1, а под ним размещены верхняя 2 и нижняя опорная 5 ограничительные решетки, между которыми находится подвижная насадка. К опорной решетке меньшим основанием прикреплен расширяющийся усеченный кольцевой элемент 4, делящий пространство опорной решетки на кольцевую 3 и центральную 6 зоны.
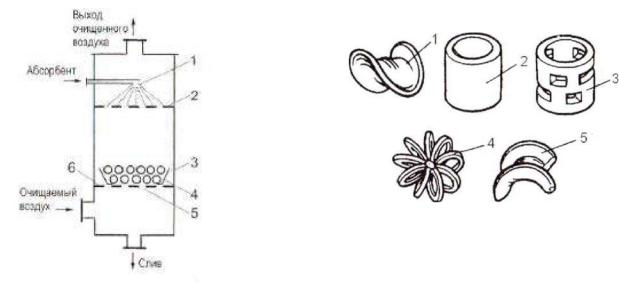
22
|
Рис. 2.8. Стандартные элементы |
|
насадки |
Рис. 2.7 Схема скруббера с подвижной |
1 - седло Берля; 2 - кольцо Рашига; |
3 - кольцо Паля; 4 - розетка Теллера; |
|
насадкой |
5 - седло «Инталокс» |
Обрабатываемый газ подается в аппарат под опорную решетку и делится на два потока; центральный и кольцевой. При прохождении кольцевой зоны поток газа разгоняется. Он воздействует на с прижатые к стенке элементы подвижной насадки и перемещает их от стенки в центральный поток, в результате чего насадка постоянно «пульсирует» в центральном и прилегающем к стенке аппарата потоках, обновляя поверхность взаимодействия фаз. Если выпадает осадок, то подвижная насадка «соскребает» его со стенок корпуса аппарата или опорной решетки.
В качестве посадочных тел используют полые, сплошные и перфорированные шары, а также кольца с перфорированными стенками, полукольца, кубики, скрещенные сплошные и перфорированные диски (рис. 2.8). Материалы для изготовления насадки (керамика, фарфор, уголь, пластмассы, металлы) выбираются из соображений антикоррозионной устойчивости к очищаемому газу и поглотителю.
Широкое распространение получили башенные абсорберы (рис. 2.10),где вместо одного слоя насадки установлено несколько ярусов колпачковых тарелок 1. Каждая тарелка снабжена патрубками 2, которые накрывают колпачками 3 с зубчатыми краями, и оборудуют переливными трубками 4.
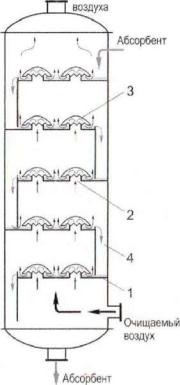
23
Абсорбент в этих аппаратах стекает от тарелки к тарелке по переливным трубкам. Очищаемый газ движется снизу вверх в направлении, указанном стрелками, барботируя через слой жидкости. При прохождении между зубцами колпачков газ разбивается на множество струек и пузырьков, в результате чего образуется большая поверхность соприкосновения взаимодействующих веществ. выход
Рис. 2.10 Схема колпачково-тарельчатого абсорбера
1 - тарелки; 2 - патрубки для прохода газа; 3 - колпачки с зубчатыми краями; 4 - переливные трубки
Адсорбция газовых примесей
Существуют особые твердые материалы, которые, как и абсорбирующие жидкости, способны избирательно поглощать газообразные компоненты из газовых смесей. Эта способность вызвана тем, что после специальной обработки (например, дегазации вакуумированием) или активации (пропитки) их поверхностные атомы или молекулы находятся под воздействием неуравновешенных сил притяжения, направленных внутрь твердого тела.
В результате присутствующие в газовой смеси молекулы загрязнителя
24
собираются на поверхности, в порах или капиллярах твердого материалапоглотителя.
Процесс поглощения газов поверхностью активированного твердого тела называется адсорбцией, а твердое тело, поглощающее газ или пар - адсорбентом. Газ или пар, удерживаемый поверхностью твердого тела, называют адсорбируемым веществом или адсорбатом. Переход молекул загрязняющих веществ из газа-носителя на поверхностный слой адсорбента происходит, если силы притяжения адсорбента больше сил притяжения действующих на адсорбтив со стороны молекул газа-носителя.
Природа сил, вызывающих межмолекулярное притяжение, может быть различной. При физической адсорбции концентрирование молекул поглощаемого вещества на поверхности адсорбента происходит под действием сил Ван-дер-Ваалъса - слабых электромагнитных взаимодействий, которые проявляются на расстояниях меньше атомных l ≈10-8 см (например, между полярной и неполярной молекулами и др.).
При химической адсорбции молекулы адсорбента и газовой примеси химически взаимодействуют за счет ненасыщенных валентных связей поверхностного слоя твердого материала, т.е. вступают в химическую реакцию. При этом возможны очень большие скорости поглощения и полное извлечение компонентов, выделение которых другим способом было бы невозможно из-за их малой концентрации в смеси.
Процесс физической адсорбции может быть обратимым с чередованием стадий адсорбции и десорбции - выделения поглощенного компонента из адсорбента. Регенерацию адсорбента проводят нагреванием, например выжиганием органических веществ, пропусканием острого или перегретого пара, воздуха, инертного газа (азота). Иногда адсорбент, потерявший активность из-за экранирования пылью или смолой, полностью заменяют. При хемосорбции регенерация практически неосуществима.
При контакте адсорбента с газовой смесью первоначально поглощаются все ее компоненты, но после насыщения поверхности адсорбента в нее
25
внедряются преимущественно молекулы с большей адсорбируемостью, вытесняя другие молекулы. На этом основан выбор пары «адсорбент - адсорбат». Процесс адсорбции прекращается после заполнения активной поверхности адсорбента молекулами адсорбата, т.е. по достижении равновесия системы или полного насыщения адсорбента в заданных условиях.
Адсорбируемость (количество газа, адсорбируемого единицей массы сорбента в равновесном состоянии) зависит от температуры и давления в парогазовой фазе. С повышением температуры при прочих равных условиях равновесная концентрация уменьшается, с ростом давления - увеличивается. Равновесная концентрация тем выше, чем больше молекулярный вес поглощаемого газа.
Промышленные адсорбенты изготавливают из твердых пористых материалов и используют в дробленном, гранулированном или порошкообразном виде. С целью снизить энергетические и материальные затраты на адсорбционную очистку при выборе адсорбента учитывают ряд требований.
Адсорбенты должны иметь невысокую стоимость и изготавливаться из доступных материалов. Они должны обладать высокой пористостью и иметь развитую удельную поверхность. От этих характеристик зависит сорбционная емкость, т.е. возможность поглощать большое количество адсорбтива при его малой концентрации в газовой среде.
Адсорбент должен иметь высокую селективность (избирательность) в отношении адсорбируемого компонента. Для снижения затрат на регенерацию удерживающая способность адсорбента не должна быть слишком высокой. При этом он должен обладать достаточной механической прочностью, чтобы выдерживать несколько сотен и тысяч циклов «адсорбция-десорбция».
Адсорбент для процесса физической адсорбции должен быть химически инертным по отношению к компонентам очищаемого воздуха, а для химической сорбции - вступать с молекулами загрязнителей в химическую реакцию.
26
Из практически используемых адсорбирующих веществ ведущее место принадлежит различным видам активированных углей (древесный, костяной и др.), удельная поверхность которых может превышать 500 м2/г. Хорошими адсорбентами являются гель кремниевой кислоты (силикагель АlO2×nH2O), глинозем, каолин, некоторые алюмосиликаты (алюмогели Аl2O3×nH2O), цеолиты (алюмосиликаты). Эти вещества отличаются друг от друга своими адсорбционными свойствами, размерами пор и гранул, плотностью и др.
Активированный уголь удовлетворяет большинству требований и взаимодействует с большинством газообразных веществ, в связи с чем широко применяется. Основным его недостатком является химическая нестойкость к кислороду, особенно при повышенных температурах. В последнее время появился новый тип углеродных адсорбентов - активированные углеродные волокна, применяемые в виде тканей, лент, нетканого материала, войлока и т.п. Благодаря высокой химической, термической и радиационной стойкости они обладают лучшим сочетанием адсорбционных и фильтрующих свойств, высокой адсорбционной активностью и удобством аппаратурного оформления.
Остальные адсорбенты более селективны к улавливанию определенных загрязнителей. Так, оксиды алюминия (алюмогели) и известняк используются для улавливания фтора и фтористого водорода, полярных органических веществ, силикат кальция - для улавливания паров жирных кислот, силикагель - для полярных органических веществ, сухих газовых смесей.
Пример аппаратурного оформления хемосорбционного процесса очистки отходящих газов от фторида водорода HF показан на рис. 2.11. Результатом адсорбции в таком аппарате при температуре более 350°С является образование на поверхности кусков известняка фторида кальция в виде рыхлой оболочки.
Далее насыщенный поглотитель подвергают грохочению на сите. Бедный надрешетный продукт грохочения 20…40 % CaF2 вновь используют для извлечения из воздуха HF, а богатый подрешетный продукт 80…95 % CaF2 - является товарным флюоритом.
Для процессов хемосорбции часто используется импрегнирование
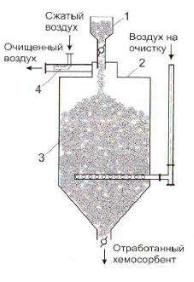
27
(пропитка) некоторых сорбентов. Пропитывающие вещества могут вступать в реакции с определенными загрязнителями или катализировать (ускорять) реакции, ведущие к их обезвреживанию - распаду, окислению и т.д. Так, активированные угли часто предварительно модифицируют путем их обработки серной кислотой, хлоридами железа и ртути, серой, сульфидами металлов и т.п.
Рис. 2.11. Схема установки для хемосорбционной очистки HF известняком
1 - бункер подачи кусков известняка 6…40 мм; 2 - корпус контактного аппарата; 3 - газораспределительное устройство;
4 -пневматический эжектор
При взаимодействии активированного угля, обработанного тяжелыми галогенами (бромом, йодом), с метаном или этаном, образуются тяжелые галогензамещенные углеводороды, которые затем легко адсорбируются.
Алюмосиликаты, пропитанные оксидами железа, при температуре разложения галогенорганических соединений способствуют реакции хлора с оксидом металла. Образовавшиеся парообразные хлориды металлов могут быть в дальнейшем легко сконденсированы, так как имеют низкую упругость насыщенных паров.
Примером использования имггрегнированного активированного угля может служить способ санитарной очистки вентиляционных выбросов от паров ртути (рис. 2.12). Адсорбент для подачи в адсорбер готовят в реакторе 3,
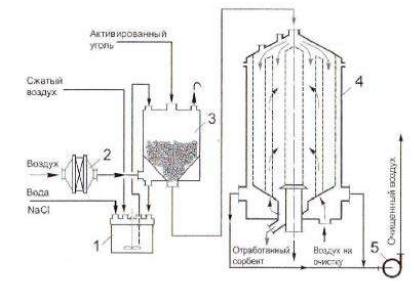
28
где активированный уголь обрабатывается водным раствором хлорида натрия из смесительной емкости 1.
Рис. 2.12. Схема адсорбционной установки демеркуризации вентиляционных выбросов
1 - смеситель; 2 - воздухонагреватель; 3 - реактор; 4 - адсорбер; 5 – вентилятор
Подлежащие очистке вентвыбросы фильтруют через слои гранулированного угля, где в результате взаимодействия с хлоридом натрия пары ртути связываются и удерживаются адсорбентом. По насыщении ртутью поглотитель выгружают из адсорбера и содержащуюся в нем ртуть рекуперируют пирометаллургическим методом. Очищенный воздух через вентилятор 5 отводится в атмосферу.
Теоретически, адсорбция может быть применена для извлечения любых загрязнителей из газового потока. На практике область ее применения ограничена рядом эксплуатационных, технических и экономических условий. Так, по требованиям пожаро- и взрывобезопасности нельзя подвергать адсорбционной обработке газы с содержанием взрывоопасных компонентов более 2/3 от НКПР.
Аппараты для адсорбции обычно громоздки, что определяется малыми (до 0,5 м/с) скоростями потока через слой адсорбента, поскольку при более высоких скоростях резко возрастает истирание и унос адсорбента. Так, при
29
скоростях потока 1…1,5 м/с потери адсорбента за счет уноса могут доходить до 5 % в сутки.
3. МЕСТНАЯ ВЫТЯЖНАЯ ВЕНТИЛЯЦИЯ
Для борьбы с выделяющимися в воздух производственных помещений парами и газами вредных веществ, а также пылью наиболее эффективно применение локализующей вытяжной вентиляции, т. е. удаление вредных выделений от мест их образования.
Удаление загрязненного воздуха от мест его сосредоточения легко осуществить при устройстве укрытий у агрегатов, являющихся источниками вредных выделений. Вытяжка из-под укрытий может быть как естественной, так и механической. Устройство локализующей, или местной, вытяжной вентиляции рекомендуется как один из наиболее экономичных и эффективных методов борьбы с вредными выделениями.
Чистый приточный воздух в этих случаях следует подавать в отдалении от источников вредных выделений, т. е. приточный воздух должен всегда подаваться в «чистую зону» вдали от мест образования вредных выделений.
3.1.Местные отсосы.
Местный отсос представляет собой устройство для локализации вредных выделений у места их образования и удаления загрязненного воздуха за пределы помещения с концентрациями, более высокими, чем при общеобменной вентиляции. Это позволяет сокращать воздухообмен и тем самым снижать расходы на обработку воздуха.
Санитарно-гигиеническое значение местных отсосов заключается в том, что они не допускают проникания вредных выделений в зону дыхания работающих.
Кроме санитарно-гигиенических требований, к местным отсосам предъявляют следующие технологические требования:
а) место образования вредных выделений должно быть укрыто настолько, насколько это позволяет технологический процесс, а открытый (рабочий) проем
30
должен иметь минимально возможные размеры; б) местный отсос не должен мешать нормальной работе или снижать
производительность труда; в) вредные выделения должны удаляться от места их образования в
направлении их естественного движения — горячие газы и пары вверх, холодные тяжелые газы и пыль вниз;
г) конструкция местного отсоса должна быть простой, иметь малое гидравлическое сопротивление, легко сниматься и устанавливаться на место при чистке и ремонте оборудования.
Конструктивно местные отсосы оформляют в виде разнообразных укрытий источников вредных выделений. Условно их можно разделить на три группы: полуоткрытые, открытые и полностью закрытые.
Полуоткрытый отсос представляет собой укрытие, внутри которого находится источник вредных выделений. Укрытие имеет открытый проем или отверстие. Примерами такого укрытия являются вытяжные шкафы, вентилируемые камеры или кабины (для пульверизационной окраски, дробеструйной очистки и т. п.), витринные отсосы и фасонные укрытия у вращающихся режущих инструментов.
К местным отсосам открытого типа относятся укрытия, находящиеся за пределами источника вредных выделений — над ним или сбоку от него. Примерами таких укрытий являются вытяжные зонты, боковые, бортовые и кольцевые отсосы.
Полностью закрытые отсосы являются составной частью кожуха машины или аппарата (элеватора, мельницы, бегуна, дробилки, барабана для очистки литья и т. п.), который имеет небольшие отверстия, щели или неплотности для поступления через них воздуха из помещения.
Укрытие следует располагать по направлению распространения струи вредных выделений, используя для их захвата их собственную кинетическую энергию. В этом случае расход удаляемого воздуха будет минимальным. При проектировании местных отсосов выбор формы укрытия, его расположения
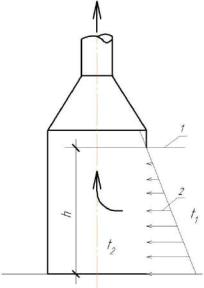
31
относительно источника вредных выделений и объема отсоса зависит от характера технологического процесса.
В настоящее время некоторые виды технологического оборудования выпускаются со встроенными местными отсосами. Таковы, например, окрасочные и сушильные камеры, деревообрабатывающие, шлифовальные и полировальные станки.
3.1.1. Вытяжные шкафы
Вытяжные шкафы представляют собой укрытия с рабочим проемом для наблюдения за т ехнологическим процессом и для его проведения при различного рода лабораторных работах и исследованиях, сопровождающихся образованием значительных количеств тепла, газов и других вредных выделений. Образующиеся внутри шкафа вредные выделения удаляются из него вместе с воздухом за пределы помещения естественным или механическим путем, а на их место из помещения через рабочий проем подтекает воздух, который служит как бы завесой, препятствующей прониканию вредных выделений из шкафа в помещение. Для предотвращения выбивания вредных выделений из шкафа уровень нулевых давлений (нейтральная линия) в нем должен располагаться не ниже верхней кромки проема.
Рис. 3.1 Схема вытяжного шкафа с естественной вытяжкой
1— уровень нулевых давлений;
2— эпюра распределения давлений в рабочем отверстии шкафа;
t1 — температура воздуха в помещении;
t2 — температура газов внутри вытяжного шкафа
Определим объемный расход воздуха, удаляемого из шкафа с естественной вытяжкой (рис. 3.1) при наличии в нем теплового источника.

32
Для удаления из шкафа избытков тепла или других вредных выделений естественным путем необходимо наличие подъемной силы, возникающей в том случае, когда температура воздуха в шкафу превышает температуру воздуха в помещении. Кроме того, удаляемый воздух должен иметь достаточный запас энергии для преодоления аэродинамического сопротивления на пути от входа в шкаф до места выброса в атмосферу.
Объемный расход удаляемого из шкафа воздуха L, м3/ч, может быть определен по формуле
L =120 3 |
h Q Апр2 |
, |
(3.1) |
где h – высота рабочего проема, м;
Q – явная теплота, выделяющаяся в результате реакции, Вт; Апр – площадь рабочего проема, м2.
Необходимую высоту вытяжной трубы гравитационных вытяжных
шкафов Н, м, можно опр еделить, задавшись диаметром трубы d. |
Тогда |
располагаемая разность давлений |
|
Рр = Н · (γ1 – γ2), |
(3.2 ) |
где Н – вертикальное расстояние от цента рабочего проема до среза вытяжной
шахты, м; |
|
|
|
|
|
|
|
|
|
γ1, γ2 – удельные веса воздуха в районе шкафа и внутри шкафа, Н/м3, |
|
||||||||
γ |
= |
3463 |
|
|
|
(3.3) |
|||
273 +t |
|
||||||||
|
|
|
|
|
|||||
Потери давления при движении воздуха от центра рабочего проема до |
|||||||||
среза вытяжной шахты определяется методом динамических давлений: |
|
||||||||
∆Р =ξ |
|
Р =ξ |
|
|
υ2 ρ |
2 |
(3.4) |
||
|
п |
д |
|
п |
|
2 |
|
Потери энергии определяются как доля от динамического давления:
ξп = Σξ +λтр |
H |
|
d , |
(3.5) |
где ξп – приведенный коэффициент местного сопротивления, который определяется по выражению (3.5), зависит от коэффициентов
33
местного сопротивления на тракте от входа в шкаф до среза шахты и линейных потерь по высоте шахты;
υ – скорость в вытяжной шахте, м/с; ρ2 – плотность воздуха в шкафу, кг/м3.
Приравняв выражения (3.2) и (3.4), определяем высоту вытяжной шахты, при которой будет обеспечиваться расход Lух.
Н (γ1 −γ2 )= Σξ +λтр Hd Рд ,
Н = |
Σξ Рд |
|
, |
(3.6) |
|||
∆γ − |
λтр |
Р |
|||||
|
|
|
|||||
|
|
|
|
||||
|
|
d |
д |
|
|
||
|
|
|
|
|
т.е. высота вытяжной шахты определяется в зависимости от суммы коэффициентов местных сопротивлений, перепада удельных весов, диаметра шахты, шероховатости и аэродинамических характеристик.
Объемный расход воздуха L, м3/ч, отсасываемого вытяжными шкафами при механической вытяжке, определяется из условия отсутствия выбивания загрязненного воздуха из шкафа и с учетом токсичности выделяющихся веществ по формуле
L = υ · F · 3600, |
(3.7) |
где v - средняя скорость всасывания в сечении открытого проема, м/с; F — площадь открытого (рабочего) проема шкафа, м2.
Среднюю скорость всасывания в открытом проеме шкафа рекомендуется принимать по данным табл. 3. 1 и по действующим нормативам.
Площадь открытого (рабочего) проема лабораторного шкафа составляет 40—50% площади проема при полном раскрытии дверок шкафа.
Вытяжка из нижней зоны лабораторных шкафов с комбинированным (нижним и верхним) отсосом составляет 30—50% общей вытяжки из шкафа. Остальное количество воздуха удаляется из верхней зоны

34
Таблица 3.1 Рекомендуемые скорости всасывания воздуха в проемах вытяжны шкафов
№ |
Технологическая операция |
Выделяющиеся вредности |
v ,м/с |
|
п/п |
||||
|
|
|
||
1 |
Плавка и розлив свинца |
Аэрозоль свинца и окислов |
1,5…1,7 |
|
|
(t=400° С) |
|
|
|
2 |
Гальваническое свинцевание |
Фтористый водород |
1,5 |
|
3 |
Пайка свинцом или третником |
Аэрозоль свинца и дым |
0,7…1,6 |
|
4 |
Пайка без свинца |
Аэрозоль металла |
0,4…0,5 |
|
5 |
Работа со свинцом при |
Аэрозоль свинца и окислов |
2…2,5 |
|
|
интенсивном движении в шкафу |
|
|
|
6 |
Работа с ртутью без нагрева |
Пары ртути |
0,8…1,1 |
|
7 |
То же, с нагревом |
То же |
1,1…1,3 |
|
8 |
Работа на лабораторных и |
Газы и пары при допустимой |
|
|
|
полузаводских установках |
концентрации, мг/м3; |
|
|
|
|
до 10 |
0,5 |
|
|
|
от 10 до 1 |
0,7…1 |
|
|
|
ниже 1 |
1,2…1,5 |
|
9 |
Операции с особо вредными |
Радиоактивные вещества, |
2…3 |
|
|
веществами |
теллур, бериллий |
|
|
10 |
Промывка в бензине |
Пары бензина |
0,5…0,6 |
|
11 |
Электролитическое обезжиривание |
Туман щелочей |
0,6…0,8 |
|
12 |
Работав лабораторных шкафах |
Различные пары и газы |
0,3…0,5 |
|
13 |
Гидропескоструйная очистка |
Силикатная пыль |
1…1,5 |
|
|
(при закрытом проеме) |
|
|
Последовательность расчета местных вытяжных систем
свытяжным шкафом
1.Определяют расход воздуха, который необходимо удалить от вытяжного шкафа:
L |
ух |
=120 3 |
h Q А2 |
|
|
||||
|
|
|
|
|
|
пр . |
|
||
2. |
|
|
Рассчитывают температуру |
воздуха |
|||||
шкафу, °С: |
|
|
|
|
|
|
|
|
|
|
t2 |
= t1 |
+ |
3,6 Q |
. |
(3.8) |
|||
|
|
||||||||
|
|
|
|
c L ρ |
2 |
|
|
|
|
|
|
|
|
в |
|
|
|
|
Плотность воздуха в шкафу ρ2 принимается с последующим уточнением. 3. Определяют значения γ1 и γ2 по зависимости и плотность воздуха в
вытяжном шкафу ρ2.
35
4. Находят значение скорости в вытяжной шахте, задавшись диаметром или эквивалентным диаметром, если шахта имеет прямоугольное сечение. Значение скорости должно быть в пределах υ = 1,5÷2,5 м/с.
|
υ = |
|
L |
|
|
|
|
|
|
(3.9) |
|
|
|
|
|
|
|
|
|
||
|
πd |
2 |
|
|
|
|
|
|
||
|
4 |
3600 |
|
|
|
|
|
|||
|
|
|
|
|
|
|
|
|
||
5. |
Определяют динамическое давление |
Рд =υ2 |
ρ2 . |
|||||||
|
|
|
|
|
|
|
2 |
|
||
6. |
Рассчитывают перепад удельных весов ∆γ и λтр: |
|||||||||
|
|
|
|
68 |
|
|
k 0,25 |
|
||
|
λтр = 0,11 |
Re |
+ |
|
|
. |
||||
|
|
|
||||||||
|
|
|
|
|
|
d |
|
|||
7. |
Находят высоту Н. |
|
|
|
|
|
|
|
|
|
8. |
Определяют располагаемое давление |
|
Рр. |
|
9.Вычисляют суммарное значение коэффициентов местных сопротивлений Σξ и приведенный коэффициент местного сопротивления ξп .
10.Рассчитывают потери давления ∆Р.
11.Производят сравнительный анализ. При выполнении условия
Рр ≥ ∆Р, |
(3.10) |
проверяют размер вытяжной шахты Н, является ли он приемлемым для монтажа (2 м от уровня верхний точки кровли). Если высота Н соответствует требованиям и выполняется условие (3.10), то такой шкаф оборудуют гравитационной системой. Если условие (3.10) не выполняется или высота не приемлема для монтажа, то в таких случаях шкаф оборудуется механической системой вентиляции.
3.1.2. Бортовые отсосы
Бортовые отсосы. Бортовые отсосы применяют для удаления вредных выделений с поверхности растворов, находящихся в различных ваннах, где происходят процессы металлопокрытия и травления. Различают однобортовые отсосы, когда щель отсоса расположена вдоль одной из длинных сторон ванны,

36
двухбортовые, когда щели расположены у двух про тивоположных сторон, и угловые - при расположении щелей у двух соседних сторон.
Классификация бортовых отсосов
1. По расположению:
а) однобортовые; б) двухбортовые.
Выбор типа бортового отсоса зависит от ширины ванны В (рис, 3.2):
-при ширине ванны В < 600 мм – устанавливается однобортовой отсос;
-при ширине ванны в пределах 600 ≤ В ≤ 1200 мм – устанавливается
двухбортовой отсос.
Рис. 3.2 Схема устройства бортовых отсосов
а— простой; б — опрокинутый
2.По конструктивным особенностям:
а) простые (обычные) бортовые отсосы; б) опрокинутые бортовые отсосы.
Простые бортовые отсосы имеют вертикальную плоскость всасывания, а опрокинутые – горизонтальную плоскость всасывания.
3. По форме:
а) прямоугольные; б) кольцевые; в) угловые.
Как отмечалось выше, вытяжные отверстия прямоугольной и щелевой форм имеют более дальнобойный факел по сравнению с факелами вытяжных
37
отверстий круглой формы. Поэтому всасывающие отверстия бортовых отсосов любых конструкций изготавливаются прямоугольной или щелевой формы.
Обычные бортовые отсосы устанавливаются:
1.Если расстояние от зеркала электролита до центра плоскости всасывания Нр = 80÷150 мм.
2.Если обрабатываемые изделия имеют сложную форму.
3.При наличии у ванны передувки.
При прочих равных условиях предпочтение всегда отдают опрокинутым бортовым отсосам, так как вся плоскость всасывания бортового отсоса лежит в зоне паров электролита и криволинейное движение воздуха, подтекающего к плоскости всасывания, оказывает придавливающий эффект на траекторию движения паров электролита.
Опрокинутый бортовой отсос устанавливают у ванн, у которых Нр = 150÷300 мм.
Основным недостатком опрокинутых бортовых отсосов является перекрытие части площади поверхности зеркала электролита.
Бортовые отсосы всегда устанавливаются с длинной стороны ванны.
Если ванна имеет длину более 1200 мм, то у таких ванн устанавливают секционные бортовые отсосы, т.к. максимальная длина бортового отсоса l1 =
1200 мм.
Если ванна имеет длину не более 1200 мм, то допускается устанавливается один бортовой отсос и в этом случае коллектор может быть исключен из конструкции, а бортовой отсос через переход присоединяется к ответвлению.
Расчёт количества воздуха, удаляемого бортовыми отсосами
Расчет заключается в определении необходимого расхода удаляемого от отсоса воздуха.
В настоящее время наибольшее распространение получили две методики расчета производительности по удалению воздуха бортовыми отсосами:

38
1. Метод расчета профессора Баранова М.М.
Расчет производительности бортовых отсосов выполняют на основе графической методики, разработанной в результате экспериментального изучения действии бортовых отсосов. Пример расчета приведен в учебнике «Отопление и вентиляция», часть 2, Вентиляция, под редакцией В.Н.Богословского.
Методика предназначена для расчета обычных и опрокинутых, одно- и двухбортовых отсосов.
Объемный расход воздуха, удаляемого местным отсосом, м3/ч, определяют по формуле
L = |
(3.11) |
где Lуд – удельный расход воздуха на 1 м длины ванны, м3/(ч·м); Зависит от токсичности вредных выделений и определяется по экспериментальным графикам в зависимости от высоты спектра вредных выделений h, ширины ванны В и типа отсоса.
Под спектром вредных выделений понимают насыщенный испарениями слой воздуха над поверхностью зеркала ванны. Высота спектра вредностей – расстояние по вертикали от верха борта ванны до самой высокой точки спектра.
температура раствора, оС;
температура воздуха рабочей зоны, оС;
При значениях близких к
(“холодные ванны”) избыточная температура раствора t =
принимается не ниже 10 оС.
l – длина ванны, м;
- поправочный коэффициент на глубину уровня раствора ванне (определяется по справочнику);
– поправочный коэффициент на скорость движения воздуха в рабочей зоне (определяется по графикам).
2. По нормам проектирования АЗ-782
(АЗ-782 ГПИ Проектпромвентиляция. Руководство по проектированию отопления и вентиляции предприятий машиностроительной промышленности. Гальванические и травильные цеха.)
39
Этот метод представляет собой расчет производительности бортовых отсосов от эталонной (“нормализованной”) ванны с учетом дополнительных коэффициентов, учитывающих особенности проведения технологического процесса.
Расход удаляемого воздуха определяют по формуле
L =Lo k∆t kт k1 k2 k3 k4 , |
|
|
|
(3.12) |
||||||
где Lo – количество удаляемого воздуха, |
м3/ч, для обычных и |
|||||||||
опрокинутых отсосов без передувки рассчитывается по формуле |
||||||||||
|
|
Вр l |
|
|
1/3 |
|
|
l , |
(3.13) |
|
L |
=1400 0,53 |
+Н |
р |
|
В |
р |
||||
|
||||||||||
o |
|
Вр +l |
|
|
|
|
|
|||
|
|
|
|
|
|
|
|
|
||
Вр – расчетная ширина ванны, м; |
|
|
|
|
|
|
|
|||
l – длина ванны, м; |
|
|
|
|
|
|
|
|
|
|
Hр – расстояние от щели всасывания до уровня электролита в ванне, м; |
||||||||||
k t – поправочный |
коэффициент на температуру |
раствора, |
||||||||
определяется в зависимости от |
t = tр – tр.з.; |
|
kт – коэффициент, учитывающий токсичность раствора и летучесть вредных выделений; принимается по таблице АЗ-782.
Для отсосов с передувкой kт = 1;
k1 – коэффициент, учитывающий конструкцию отсоса: для однобортового отсоса k1 = 1,8; двухбортового k1 = 1;
k2 – коэффициент, учитывающий наличие воздушного перемешивания, k2 = 1 – для ванн без воздушного перемешивания, k2 = 1,2 для ванн с воздушным перемешиванием; Для снижения интенсивности испарения некоторых компонентов,
имеющих значительную летучесть, зеркало электролита укрывают пеной, поплавками или шариками.
k3, k4 – коэффициенты, учитывающие укрытие зеркала электролита по плавками или пеной, при отсутствии какого-либо вида укрытия соответствующий коэффициент принимается равным 1.
Нормализованной |
называется |
отдельно |
стоящая |
стандартно |
установленная ванна, у которой Нр = 150 мм и все коэффициенты, |
входящие |
|||
в уравнение (3.12), равны 1. |
|
|
|
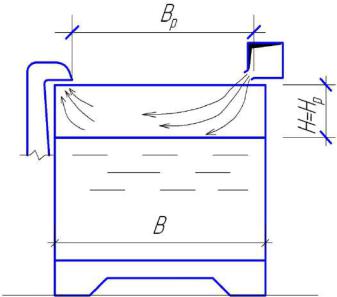
40
Для повышения эффективности локализации выделяющихся вредностей (особенно для ванн шириной В более 1000 мм) применяют однобортовые и двухбортовые отсосы с передувкой (рис. 3.3).
Передувка – воздуховод равномерной раздачи воздуха с переменным сечением (или иной воздуховод с щелевым выпуском), обеспечивающий шиберующий эффект и укрытие зеркала электролита плоской струей приточного воздуха. Приточный воздуховод-передувку располагают на противоположном от отсоса борту ванны. Подобные отсосы (с передувкой) еще называют активированными.
Активированные отсосы позволяют сократить расход воздуха, удаляемого отсосом за счет того, что поток отбираемого воздуха “подгоняется” к всасывающей щели приточной струей.
Расход удаляемого воздуха должен соответствовать сумме расходов подаваемого передувкой воздуха и воздуха, вовлекаемого по пути движения к отсосу. При меньшем расходе возможно “выбивание” загрязненного воздуха в рабочую зону.
Подача воздуха из передувки должна осуществляться как можно ближе к поверхности раствора для обеспечения эффекта “налипания” струи. В этом случае струя становится более дальнобойной. Что позволит уменьшить расход подаваемого воздуха.
Рис. 3.3 Схема бортового отсоса с передувкой
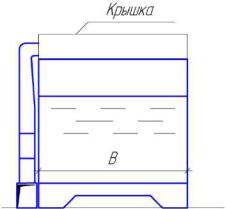
41
Количество воздуха, удаляемого опрокинутыми бортовыми отсосами от
ванны с передувкой, рассчитывается по зависимости: |
|
||
L =1200 В3/2 |
l . |
(3.14) |
|
о |
р |
|
|
Количество приточного воздуха для передувки определяется по выражению:
Рис. 3.4 Бортовой отсос с крышкой
Lп =60 Вр l k∆t . |
(3.15) |
Для более эффективного |
улавливания |
вредных выделений применяют ванны с крышками, укрывающими зеркало раствора частично или полностью.
Для ванн с крышками, перекрывающими более половины зеркала электролита допускается расчетный расход воздуха, определенный по ф-ле (4) сокращать на 30%, т.е.
L' = 0,7L |
(3.16) |
3.1.3. Вытяжные зонты
Вытяжной зонт – это открытый местный отсос, расположенный над технологическим оборудованием и удаляющий вредные газы и пары с плотностью меньше плотности воздуха.
Зонты обычно располагают над нагретым оборудованием с целью улавливания конвективной струи, содержащей вредные выделения.
Экспериментально установлено, что для эффективного улавливания вредных веществ осевая скорость в проеме зонта должна быть не менее 1 м/с, а профиль скоростей на “срезе” зонта должен быть “плоским”. Такие зонты называют емкими. Установлено, что подобный профиль скоростей имеют зонты с углом раскрытия 60°. Зонты с углом раскрытия α < 60° ещё называют
высокими.
Часто свободное пространство над технологическим оборудованием в цехе ограничено. В таких случаях для размещения зонта над оборудованием его