
8875
.pdf– Жаропрочные стали для производства арматуры, производства электроэнергии: соединительные элементы.
При этом высококачественные конструкционные стали имеют более десятка различных подгрупп, классификация по которым осуществляется на основе их физико-химических свойств и области применения. Кроме этого,
существуют стали, предназначенные исключительно для холодной штамповки или же обладающие свойствами улучшения прочностных характеристик при термической обработке.
Тем не менее, изделия, изготовленные из высококачественной конструкционной стали, не рассчитаны на повышенные нагрузки. Для этих целей применяются различные виды особовысококачественной конструкционной стали, которые обладают уникальными характеристиками.
Особовысококачественные конструкционные стали В особовысококачественных сталях содержание углерода и легирующих
такое же, как и в соответствующих марках высококачественных сталей.
Содержание серы и фосфора наименьшее – до 0,015 и 0,025% соответственно.
Особо высококачественные стали обозначаются через тире буквой Ш
(электрошлакового переплава) в конце марки. Например, 30ХГС-Ш.
Легированные высококачественные стали выплавляют в электропечах.
Особовысококачественные стали (например, шарикоподшипниковые типа ШХ,
с содержанием и Р не менее 0,015%) после выплавки в электропечах подвергают обработке синтетическими шлаками и другим методам очистки.
К наиболее распространенной группе особовысококачественных конструкционный сталей относятся так называемые мартенсито-стареющие сплавы, обладающие повышенным пределом выносливости. Стали особо
высокой прочности и вязкости (мартенситно-стареющие) по химическому составу являются безуглеродистыми (менее 0,03% С) и высоколегированными
(Ni, Co, Мо, Cr, Ti, Be и др.). Эти стали характеризуются следующими
91
потребительскими свойствами: в=1800...3000 МПа; |
>10%, >40%; |
КСU=0,3...2,5кДж/м2.
Технологические свойства мартенситно-стареющих сталей – повышенные:
хорошие свариваемость, обрабатываемость резанием и пластичность в закаленном состоянии; незначительная деформация деталей при отпуске,
выполняемом после резания и создающем необходимые высокие механические свойства. Мартенситно-стареющим сталям можно придать стойкость против коррозии и теплостойкость. Так, при дополнительном легировании хромом
(12%) эти стали становятся стойкими против коррозии даже в сильно агрессивных средах (морской воде, кислотах и др.).
Мартенситно-стареющие стали – особовысококачественные и из-за высокой стоимости применяются для деталей наиболее ответственного назначения: Н18К9М5 – Ш – шестерни, валы, корпуса ракет; Н10Х12Д2Т – Ш – детали химической аппаратуры, пружины; Н4Х12К15М4Т – Ш - штампы горячего деформирования, детали теплоэнергетических установок и др.
Основная их область применения заключается в изготовлении высоконагруженных деталей, а также тросов и крепежей.
К числу особовысококачественных видов также относятся шарикоподшипниковые конструкционные стали и специальные сплавы,
обладающие повышенной износостойкостью, жаростойкостью и пониженной чувствительностью к коррозии.
Кроме этого, для работы в агрессивной среде нередко применяются двухслойные стали, в состав которых входит никель и хром.
Следует также отметить, что к особовысококачественным видам относятся криогенные виды конструкционной стали, которые не утрачивают своих прочностных характеристик при низких температурах, поэтому могут использоваться в условиях вечной мерзлоты, а также для изготовления особо прочных емкостей, применяемых при транспортировке сжиженных газов.
92
1.4. Цветные металлы и сплавы на их основе
Цветными металлами принято считать металлы, не входящие в группу черных металлов, т.е. не имеющих железо-углеродистую основу. Цветных металлов в природе значительно меньше, процесс получения их из руды значительно трудозатратен, поэтому стоимость их значительно выше чем черных металлов. Однако многие цветные металлы обладают уникальными свойствами, и несмотря на дороговизну нашли применение в строительстве.
Наиболее применяемые медь, алюминий, титан и сплавы на их основе.
Медь – металл розовато-красного цвета с плотностью 8,95 г/см3 и
температурой плавления 1083 ºС. Медь кристаллизуется в ГЦК решетке и не имеет полиморфных превращений. На воздухе при наличии влаги и углекислого газа медь медленно окисляется, покрываясь пленкой так называемой патины зеленого цвета, которая является щелочным карбонатом меди (СuОН)2СO3 . Эта пленка в определенной мере защищает медь от дальнейшей коррозии. Чистая медь обладает высокой электропроводностью
(второе место после серебра), пластичностью, коррозионной стойкостью в пресной и морской воде, а также в ряде химических сред. Механические свойства меди в литом состоянии: σв = 160 МПа, δ = 25 %; в горяче деформированном: σв = 250 МПа, δ = 50 %.
Вредными примесями, снижающими механические и технологические свойства в меди являются висмут, свинец и сера. Эти примеси в меди почти не растворимы, дают легкоплавкие эвтектики и вызывают красноломкость.
Опасными являются газообразные примеси – кислород, водород. Так, медь,
содержащая кислород (в виде Cu2O), при нагреве в среде водорода поглощает его и при дальнейшей диффузии в глубь металла протекает реакция Cu2O + + H2 = 2Cu + H2O. Пары воды создают высокое давление внутри несплошностей металла, при этом возможны разрывы и трещины. Это явление получило название «водородная болезнь» меди. Медь хорошо деформируется,
сваривается и паяется. Ее недостатком является сравнительно плохая
93
обрабатываемость резанием. Соединение деталей из меди и ее сплавов часто выполняют посредством твердой и мягкой пайки. Твердые припои изготавливают на основе меди и цинка с добавкой серебра; температура их плавления составляет 600…1000 ºС. Мягкие припои изготавливают из сплавов олова со свинцом; температура их плавления 200…300 ºС.
Сплавы меди устойчивы к коррозии, обладают хорошими антифрикционными, технологическими и механическими свойствами и широко используются в качестве конструкционных материалов. По технологическим характеристикам различают деформируемые и литейные медные сплавы, по химическому составу их делят на латуни и бронзы. Латуни – сплавы меди с цинком, а бронзы – сплавы меди с другими элементами. Медные сплавы обозначают начальной буквой сплава Л – латунь или Бр – бронза, после чего следуют первые буквы основных элементов, образующих сплав: О – олово, Ц – цинк, Мц – марганец, А – алюминий, Ж – железо, Ф – фосфор, Б – бериллий, X
– хром, Н – никель и т. д., а после них цифры, указывающие содержание легирующих элементов в процентах. В деформируемых латунях не указывается содержание цинка, а в деформируемых бронзах – содержание меди: их концентрации определяются по разности. Например, ЛЖМц-59-1-1 – латунь,
содержащая (%): 59 Сu, 1 Fe, 1 Мn и остальное – цинк; или БрОФ6,5-0,15 –
бронза: 6,5 Sn, 0,15 Р, остальное – медь. Порядок цифр в обозначениях марок деформируемых и литейных сплавов различен. В марках деформируемых латуней и бронз цифры, отделенные друг от друга дефисом, ставятся в конце обозначения и расположены в той же последовательности, что и буквы,
например ЛА60-1-1 или БрОЦ4-3. В литейных латунях и бронзах содержание всех компонентов сплавов в процентах, в том числе, содержание цинка приведены сразу же после обозначающих их букв. Содержание меди в литейных сплавах определяется по разности от 100 %. Например, ЛЦ16К4 –
литейная латунь, содержащая 16 % Zn, 4 % Si, остальное медь; Бр05Ц5С5 –
литейная бронза, содержащая 5 % Sn, 5 % Zn, 5 % Pb, остальное – медь.
94
Алюминий относится к легким металлам (его плотность 2,7 г/см3) с
температурой плавления 660 ºС, имеет ГЦК решетку с периодом а = 0,4041нм.
Обладает высокой тепло- и электропроводностью, высокой пластичностью и малой прочностью. Полиморфных превращений не имеет. Несмотря на большое сродство к кислороду, устойчив благодаря образованию плотной защитной пленки Al2O3. Прокатанный и отожженный алюминий высокой чистоты имеет σв = 600; σ02 = 200 МПа; HB 25; ψ = 85 % и δ = 40 %. Алюминий высокой чистоты маркируется А99 (99,999 % Al), А8, А7, А6, А5, А0 (содержание алюминия от 99,85 до 99 %). Алюминий, применяемый для лабораторных целей, содержит 99,99 % А1, для технических целей – 99,50 %
А1. Классификация технических алюминиевых сплавов:
– деформируемые, предназначенные для получения поковок, штамповок,
проката, труб;
–литейные сплавы;
–сплавы, получаемые методом порошковой металлургии (спеченные алюминиевые порошки (САП) и сплавы (САС)).
Основными легирующими элементами в деформируемых алюминиевых сплавах являются Сu, Zn, Mg, Мn. В условиях равновесия сплавы представляют собой равновесный твердый раствор с выделениями интерметаллидных фаз типа СuА12 (θ-фаза), Al2CuMg (S-фаза), Al6CuMg4, (Т-фаза) и др.
Постоянными примесями в алюминии являются железо и кремний. Обе примеси практически нерастворимы в алюминии. При одновременном их содержании появляется новая фаза тройного химического соединения Al–Fe–Si.
Это соединение выделяется по границам зерен и снижает пластичность алюминия. Предельное содержание примесей Fe и Si в деформируемых алюминиевых сплавах должно составлять не более 0,5 %.
Состав и свойства некоторых алюминиевых сплавов приведены в таблице
1.5.
95
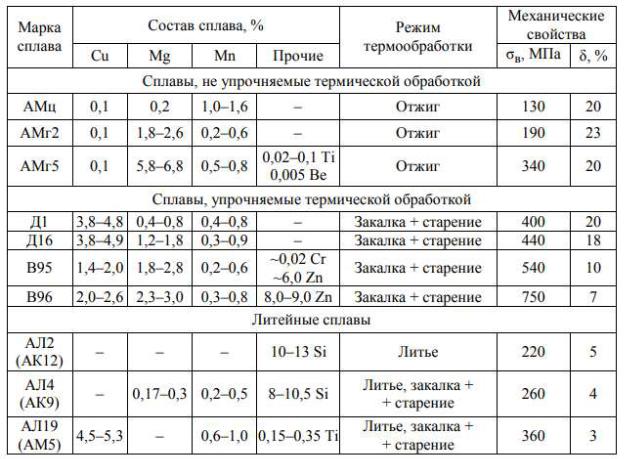
Таблица 1.5.
Состав и свойства алюминиевых сплавов
Деформируемые сплавы, не упрочняемые термообработкой, имеют сравнительно низкую прочность, но более высокую пластичность и коррозионную стойкость. Их применяют в отожженном состоянии или упрочняют с помощью холодной пластической деформации. К таким сплавам относятся сплавы типа АМц (система Аl–Мn) и типа АМг (система Al–Mg). Эти сплавы хорошо обрабатываются давлением и свариваются. Используются в изделиях, получаемых глубокой вытяжкой из листового материла. Благодаря меньшей плотности и достаточной прочности чаще применяют алюминиево-
магниевые сплавы.
Деформируемые сплавы, упрочняемые термообработкой. Примером деформируемых термоупрочняемых алюминиевых сплавов являются сплавы алюминия с медью.
96
Наиболее распространенными упрочняемыми деформируемыми алюминиевыми сплавами являются дуралюмины (Al–Cu–Mg). Достоинством дуралюминов является высокая удельная прочность, благодаря чему они относятся к числу широко применяемых в самолетостроении материалов для изготовления лопастей воздушных винтов, шпангоутов, тяг управления и др.
Дуралюмины имеют пониженную коррозионную стойкость. Для повышения коррозионной стойкости листы дуралюмина плакируют, т. е. покрывают слоем чистого алюминия и выполняют совместную прокатку листов. Алюминий,
толщина слоя которого составляет 2–5 %, сваривается с основным металлом и защищает его от коррозии. Для повышения коррозионной стойкости деталей из дуралюминов их также подвергают анодной поляризации в 10 %-м растворе серной кислоты. Выделяющийся кислород способствует образованию на поверхности дуралюминовой детали оксидной пленки, предохраняющей деталь от окисления.
Литейные алюминиевые сплавы. Литейные сплавы должны обладать высокой жидкотекучестью, малой склонностью к образованию горячих трещин и пористости. Для обеспечения высокого уровня литейных свойств необходим минимальный эффективный интервал кристаллизации. Наиболее высокие литейные свойства имеют сплавы с эвтектической структурой. Такими сплавами являются сплавы алюминия с высоким содержанием кремния (более 5 %), называемые силуминами.
Наиболее широкое распространение получил силумин марки АК12 (АЛ2),
содержащий 10–13 % кремния. При более высоких требованиях к прочностным свойствам применяют доэвтектические силумины с 4–10 % Si и добавками небольших количеств Zn, Сu, Mg, Мn. Кроме силуминов получены литейные сплавы, легированные медью и магнием. Они имеют несколько худшие литейные свойства, но более высокие механические характеристики, в том числе, при повышении температуры. Эти сплавы могут подвергаться термической обработке.
97
Жаропрочные алюминиевые сплавы. Жаропрочные сплавы получают легированием алюминия медью, магнием, никелем, железом, титаном. Для получения нужных свойств их подвергают закалке (перевод избыточных фаз в твердый раствор) и затем искусственному старению (стабилизация структурного состояния). Чем сложнее состав сплава и состав выделяющихся фаз, тем медленнее происходит разупрочнение сплава при высоких температурах. Поэтому жаропрочные сплавы обычно имеют сложный химический состав и содержат специальные присадки железа и никеля для замедления диффузионных процессов, приводящих к разупрочнению.
Например, сплав АК2 (К – «ковкий») помимо 3,5–4,5 % Cu, 0,4–0,7 % Mg
содержит 1,8–2,3 % Ni, 0,5–1,0 % Fe.
Для обозначения алюминиевых сплавов принята смешанная буквенная и буквенно-цифровая маркировка. В отличие от маркировки сталей и медных сплавов она несколько бессистемна. В сплавах АМц буквы Мц обозначают марганец, сплавы системы Al–Mg обозначают АМг. Буква Д обозначает сплавы типа дуралюминий. Буквы АД в начале марки означают технический алюминий, буквы АК – алюминиевый ковочный сплав. Буква В в начале марки означает высокопрочный алюминиевый сплав. Состояние полуфабрикатов из деформируемых сплавов обозначается буквенно-цифровой маркировкой: М – мягкий, отожженный; Т – закаленный и естественно состаренный; Т1 –
закаленный и искусственно состаренный; Н – нагартованный; П – полунагартованный; HI – усиленно нагартованный (нагартовка листов примерно на 20 %); ТН — закаленный, естественно состаренный,
нагартованный; Т1Н – закаленный, нагартованный и искусственно состаренный; Т1Н1 – закаленный, нагартованный на 15–20 % и искусственно состаренный. Условные обозначения видов термообработки литейных сплавов:
Т1 – старение; Т2 – отжиг; Т3 – закалка; Т4 – закалка и естественное старение;
Т5 – закалка и неполное искусственное старение; Т6 – закалка и полное искусственное старение до максимальной твердости; Т7 – закалка и стабилизирующий отпуск; Т8 – закалка и смягчающий отпуск. На способ литья
98
указывают буквы: З – в землю; О – в оболочковые формы; В – по выплавляемым моделям; К – в кокиль; Д – под давлением. Буква М обозначает,
что сплав при литье подвергается модифицированию.
Титан – металл серебристо-белого цвета. Относится к тугоплавким металлам: температура его плавленая равна 1668 ± 4 ºС в зависимости от степени его чистоты.
Титан имеет две полиморфные модификации: до 882 ºC существует α-Ti,
кристаллизующийся в ГПУ-решетке с параметрами a = 2,95 Å и c = 4,68 Å, а
выше 882 ºС – β-Ti , имеющий ОЦК-решетку, a = 3,28 Å. Плотность α-Ti
составляет 4,565 г/см3, а β-Ti – 4,320 г/см3. Вредными примесями в титане являются: азот, углерод, кислород и водород. Они дают твердые растворы внедрения и хрупкие оксиды, карбиды, нитриды и гидриды. Эти примеси понижают пластичность и свариваемость, повышают прочность и твердость,
ухудшают сопротивление коррозии. При введении всего лишь 0,03 % Н, 0,2 % N или 0,7 % О титан полностью теряет способность к пластическому деформированию и хрупко разрушается. Технически чистый титан марки ВТ1-1
содержит не более, % (мас): 0,30 Fe; 0,12 Si; 0,08 С; 0,15 О; 0,05 N; 0,012 Н. По прочности и пластичности ВТ1-1 не уступает ряду углеродистых и хромоникелевых коррозионностойких сталей: σв = 450…600 МПа; σ02 = 380…500 МПа; δ > 25 %; ψ > 50 %. Чистый титан с малым содержанием водорода (менее 0,002 %) не обладает хладноломкостью при прочности σв = 1300 МПа и сохраняет высокую пластичность даже при температуре жидкого гелия (δ = 15–20 %). По удельной прочности в интервале температур 300…600 ºС сплавы титана не имеют себе равных; при температуре ниже 300 ºС они уступают алюминиевым сплавам, а выше 600 ºС – сплавам на основе железа и никеля. Титан имеет низкий модуль нормальной упругости (Е = 112 ГПа),
почти в 2 раза меньший, чем у железа и никеля, что затрудняет изготовление жестких конструкций. Для повышения жесткости приходится увеличивать толщину деталей и их массу. Титан пластичен и легко обрабатывается давлением при комнатной и повышенной температурах. Недостатком титана
99
является плохая обрабатываемость резанием. Титан относится к числу химически активных металлов, но обладает высокой коррозионной стойкостью за счет образования на его поверхности стойкой оксидной пленки ТiO2, прочно связанной с основным металлом, и исключающей его непосредственный контакт с внешней средой. Толщина оксидной пленки, образующейся на титане после пребывания на воздухе, обычно достигает 5…6 нм. Благодаря оксидной пленке, титан и его сплавы не корродируют в атмосфере, пресной и морской воде, устойчивы против кавитационной коррозии и коррозии под напряжением,
а также в кислотах органического происхождения.
Благодаря высокой коррозионной стойкости титан и его сплавы практически идеально подходят для строительства морских сооружений.
1.5.Контрольные вопросы
1.Какими свойствами характеризуются металлы?
2.Чем металлы отличаются от неметаллов?
3.Что такое кристаллическая решетка? Основные типы кристаллических решеток.
4.Что такое точечные, линейные, поверхностные дефекты?
5.Какое влияние оказывают дефекты кристаллического строения на свойства металлов?
6.Что называется кристаллизацией?
7.От чего зависит размер зерна?
8.Почему величина кристаллов зависит от степени переохлаждения?
9.Что такое дендрит?
10.Какие свойства металлов относят к технологическим?
11.Что относится к качественным характеристикам металлов и сплавов?
12.На какие группы делят все металлы и образованные из них сплавы?
13.Что подразумевается под определением «чистый металл»?
14.Какой вид разрушения (хрупкое или вязкое) наиболее опасен?
100